BMW reinvents its Munich plant with AI, automation and digital logistics to support Neue Klasse production and meet rising demand in a constrained city-centre location
Speaking at the recent Automobil Produktion Kongress in Munich, Dr. Michael Nikolaides, BMW’s SVP of Production Network, Supply Chain Management and Logistics, laid out the company’s roadmap for the digitalisation of production and logistics operations.
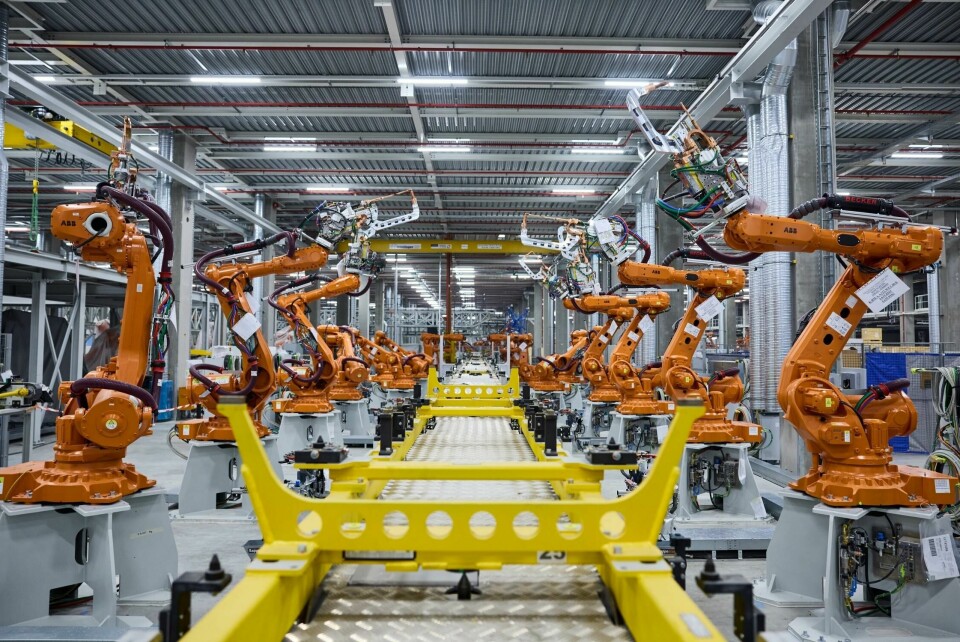
BMW is preparing for a significant turning point with the launch of its all-new vehicle platform, the Neue Klasse. For Nikolaides, this is not just about launching a new electric model – it’s about reinventing BMW’s entire production ecosystem.
“The Neue Klasse is not just a new battery-electric vehicle. It represents a complete transformation of our product portfolio,” he said. “It is reminiscent of the 1960s, when BMW introduced the original Neue Klasse.”
This transformation is notably visible at the Munich plant, which Nikolaides described as a “symbol of performing while transforming.” Despite major construction to accommodate the new platform, the plant continues to deliver 1,000 vehicles per day, on time and in full quality.
”AI helps us steer supply chains dynamically… It allows us to reconfigure supply chains quickly when new regulations emerge – which happens almost daily”
Dr. Michael Nikolaides, BMW
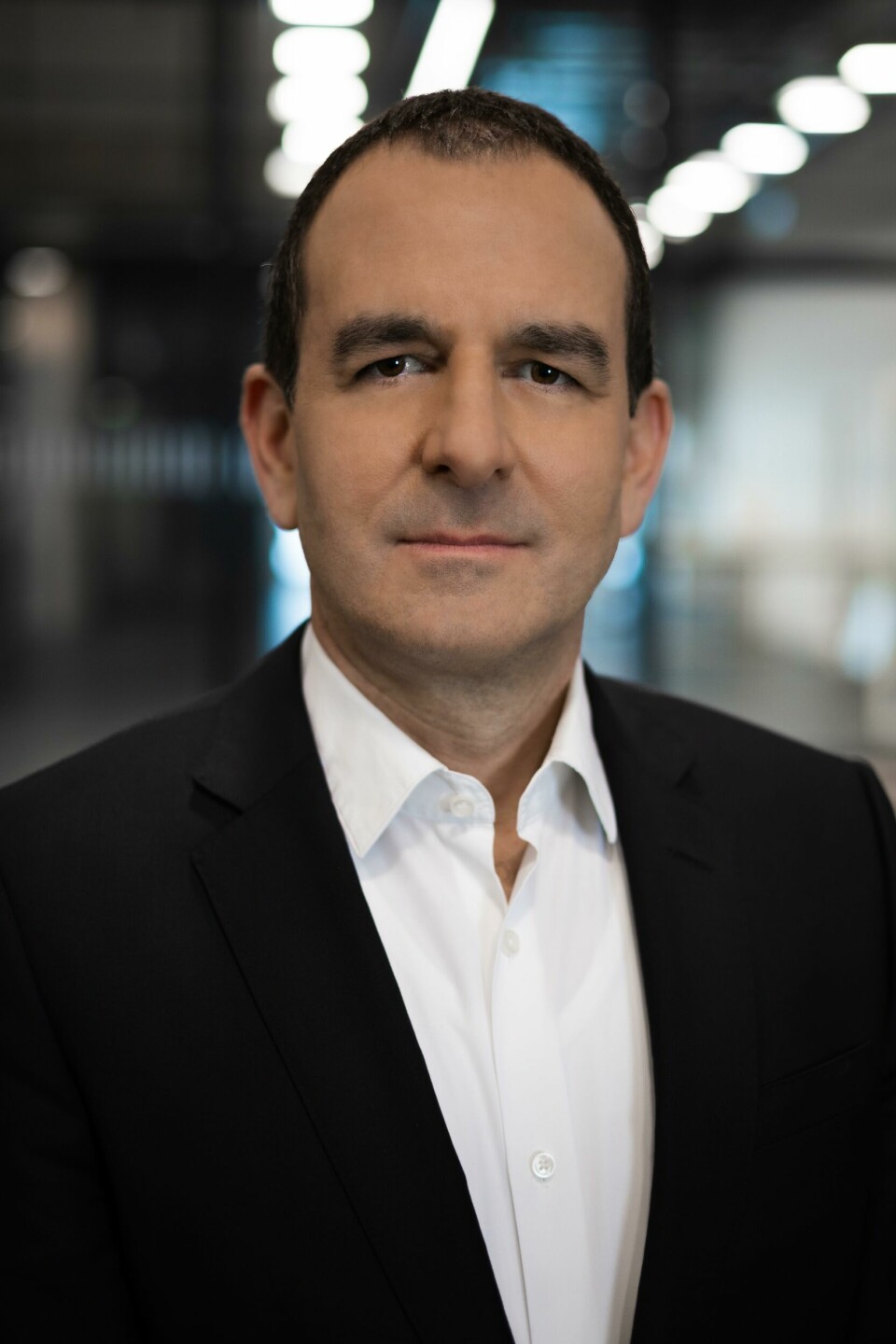
iFactory: Digitalisation at scale
To navigate this important shift, BMW developed the BMW iFactory concept – its unified system for managing production and logistics change. At its heart is digitalisation, which Nikolaides framed through three key pillars: visualisation, artificial intelligence, and automation.
For the visualisation part of the programme, BMW is digitising its entire global production network – 30 plants, over 2.4m vehicles annually – into the Nvidia Omniverse. This enables rapid simulation, efficiency gains, and agile problem-solving:
“It allows us to gain speed, efficiency, and the ability to test everything in the virtual world before implementing it physically. This is a major step forward,” explained Nikolaides.
AI is already embedded across BMW plants. At quality control checkpoints, AI now drives inspections, improving speed and accuracy. But its impact goes far beyond defect detection:
“AI helps us steer supply chains dynamically… It allows us to reconfigure supply chains quickly when new regulations emerge – which happens almost daily.”
Integration was key to making AI work. Nikolaides stressed the importance of harmonising data systems early in the digitalisation journey:
“The first lesson we learned was that we had to bring order and structure to our data… We’ve since integrated all our production data into what we call our internal data lake.”
“A forklift driver may no longer operate the vehicle, but they can move into maintenance or system supervision. Employees are eager to upskill into these new roles”
Dr. Michael Nikolaides, BMW
Automation: Smart transport and human-centric shifts
BMW’s automation strategy doesn’t mean removing humans – it means redefining their roles. Over 600 fully autonomous smart transport robots are in operation, developed in part by BMW’s own company, IdealWorks. These navigate plants independently and are deeply integrated into logistics flows.
Autonomous forklifts and route trains also coordinate through intelligent algorithms, further enhancing supply chain reliability without sidelining the workforce.
On integrating smart automation Nikolaides noted: “A forklift driver may no longer operate the vehicle, but they can move into maintenance or system supervision. Employees are eager to upskill into these new roles.”
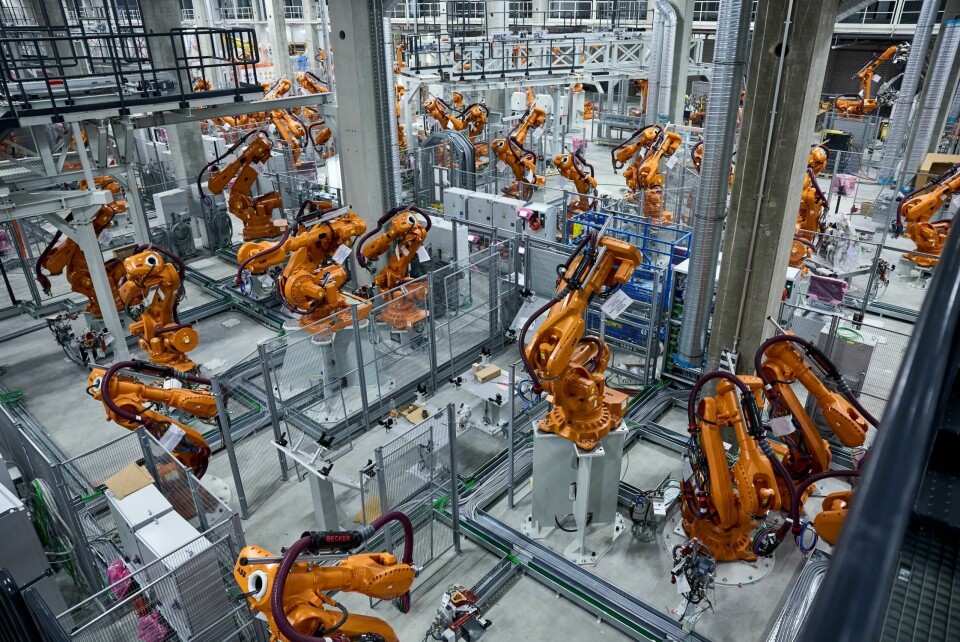
AI offers huge potential to enhance the capabilities of automated systems
AI a gamer changer for robotic applications
While BMW has used robotics since the 1980s, Nikolaides pointed out that what’s new is their convergence with AI. For instance, the Munich body shop has grown from 400 robots in 1982 to over 1,200 today, and that number is expected to surpass 2,000 with the Neue Klasse.
The future may even include humanoid robots. BMW is piloting a cooperative AI-driven humanoid at its Spartanburg plant in the US, inspired partly by industry buzz around Tesla’s Optimus project.
“It’s still early days… But there definitely are scenarios where you would not want humans working, due to safety or fatigue. In those cases, humanoid robots could be a real advantage,” said Nikolaides
Read more BMW stories
- BMW develops next-level digital manufacturing at Landshut and Regensburg plants
- Future-ready: BMW’s digital transformation of its Munich plant and beyond
- BMW plants prepare for a new era with Neue Klasse production
- Embracing agile, digital ecosystems: BMW, Mercedes-Benz & Dräxlmaier
Global volatility and strategic resilience
Despite internal innovation, BMW’s production network also faces external headwinds – geopolitical tensions, trade uncertainties, and regulatory flux. But Nikolaides views these not as roadblocks, but as reasons to build flexibility into every layer of operations:
“We don’t see it as difficult; we see it as challenging. The key is flexibility and speed.”
BMW is streamlining global flows by reducing border crossings, increasing supply chain transparency, and leveraging its international footprint. For example, the company’s largest plant being based at Spartanburg in the US is a strategic asset amid trade realignments.
“We apply the same criteria to all investments: cost-benefit analysis, feasibility, and alignment with our strategy – albeit now with a higher degree of uncertainty. So, we approach this like entrepreneurs.” Dr. Michael Nikolaides, BMW
How BMW is investing in emerging tech
Naturally, much of what Nikolaides described – humanoid robots, AI systems, omniverse simulations – comes with heavy upfront costs. But BMW applies a disciplined lens to all such investments. Pilot projects are evaluated not just on innovation appeal but on real-world applicability and ROI.
Nikolaides said “We apply the same criteria to all investments: cost-benefit analysis, feasibility, and alignment with our strategy – albeit now with a higher degree of uncertainty. So, we approach this like entrepreneurs.”
Looking ahead: AI as a key enabler
Nikolaides returned to AI as the foundational driver of BMW’s future manufacturing model:
“AI has huge potential. In combination with automation and smart transport systems, AI has enormous potential. That’s where I see a lot of future development.”
What distinguishes BMW’s approach is not merely adoption of buzzworthy technologies but the integration of these technologies into a cohesive, human-centred production ecosystem. From smart robots in Munich to intelligent supply chains powered by harmonised data lakes, BMW is positioning itself to lead – not follow –the next industrial revolution.
As Nikolaides summed it up: “There is already a great deal happening, and AI is opening new worlds of possibility. This transformation continues.”