The software-defined assembly line
The manufacturing industry is on the cusp of a revolution, where investment is led by software rather than hardware. That in turn enables a raft of new possibilities in creating the factory of the future, according to experts from Audi, ABB and Cosmo Tech.
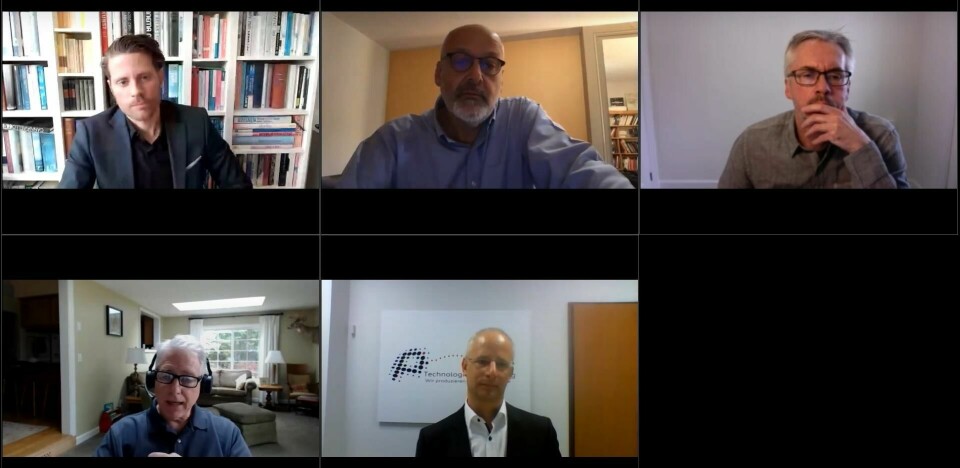
Automotive manufacturing has experienced a number of technological sea changes over the past decades: the move from relay panels to PLCs (programmable logic controller), from ‘dumb’ buttons to HMIs for communicating with machines, and the widespread introduction of robots. Experts at last week’s AMS Livestream agreed that the next revolution will be a change from a hardware-defined production system to one that is software-defined.
“[We will be] thinking of functionalities as software building blocks, instead of buying a piece of hardware that supplies us with a certain functionality,” said Dr Henning Löser, head of Audi’s Production Lab. “We’re now moving down the same route that we did with data centres, and this is going to revolutionise automation.”
He added that there is some reluctance for a change like this, but that it would enable an exponential acceleration in Industry 4.0, because software is much easier to change and maintain than hardware.
Software is a driving force in many of ABB’s solutions, said Patrick Matthews, global powertrain group manager and VP of robotic systems. Thanks to virtual factory planning with the company’s ‘Robot Studio’ application, potential issues can be caught earlier, before any hardware has been produced or installed. Once everything is in place, there are massive amounts of data coming from the equipment, and machine learning can be used with this for ongoing maintenance.
Matthews gave the example that for certain specialised equipment, there were just a handful of experts who could troubleshoot it and had to travel around the world to do so. “What we’ve now done is redeploy those guys, had them look at some algorithms, add some more sensors to the machine, add some more devices onto those machines and connect them,” explained Matthews. “We built algorithms so that the machines will self-adjust, essentially having them do on the fly what our guys were going in to do.”
Data is king
As the pandemic has shown that companies lack visibility of their operations – which parts are failing and which are going to fail first in the future, AI for these data analytics has become more important. Full visibility and predictive algorithms, such as the hybrid AI and digital twins Cosmo Tech develops (see boxout), used to be a nice to have, said Michel Morvan, co-founder and executive chairman.

“What I observe now in our customers – not only in the automotive sector but there in particular – is that people realise that knowing the state of all their systems, having good data, having the possibility to visualise it is a question of life and death.”
The software revolution doesn’t just mean more software, it also entails looking at it in a different way. Particularly when it comes to data collection and analytics, software applications are going to come from different suppliers who are focusing on one particular specialism. According to Matthews, ‘applications’ can be thought of fairly literally, like phone apps that plug into a bigger system.
“You’re going to see a lot of apps be developed that can be put into systems that can look at particular things and analyse them, and give you insight or give you direction based on that data that it’s analysing,” he explained. “I don’t think that there is going to be one huge Cray supercomputer that’s going to analyse everything and tell you exactly what to do. I think it’s going to come in little steps.”
Common platform needed
While such a multitude of apps makes sense, they do need to work together properly. Löser warned that the industry faces a challenge to find a platform to orchestrate all the different pieces of software from different vendors and make sure they are all up to date. For instance, if one piece of equipment starts updating twice a day, that may cause problems when the rest of the system hasn’t adapted yet.
“It’s clear that we need some kind of open platform that everybody can build their bits and pieces on, so that the entire factory can play together smoothly like a well-tuned orchestra.”
Morvan agreed that there will be little steps that need to be united in big leaps, adding that connections to other apps are an important part of developing Cosmo Tech’s software. He also said: “You need something that is customisable, but also is kind of generic so that you can go fast, because you cannot reinvent the wheel every time you have a problem in a plant so that’s exactly this in-between that we have to find.”
An essential component to enabling this customisability for individual plants or applications are common, open standards, Löser predicts, in order that everybody can develop towards these standards, and make it easy to plug all the apps together and to allow for the unique character of the individual plants.
Once a suitable platform is found or developed, there are further benefits in the flexibility it enables. “With the transition to an orchestration platform, all of a sudden, we are not locked into one specific supplier anymore in the plants. Instead, we can open it up and make it easier for new software solutions to find their way into our production systems,” said Löser. What’s more, such a system will allow the software to be updated continually, adding features that no-one can even imagine today.