A future for fuel cells
Hydrogen fuel cell technology is not a new development, and the use of these energy sources has, until recently, been in niche applications. Now, though, fuel cells are beginning to find their way into real automotive use as a means of facilitating the goal of ‘zero emission’ vehicles with supporting investment of significant proportions
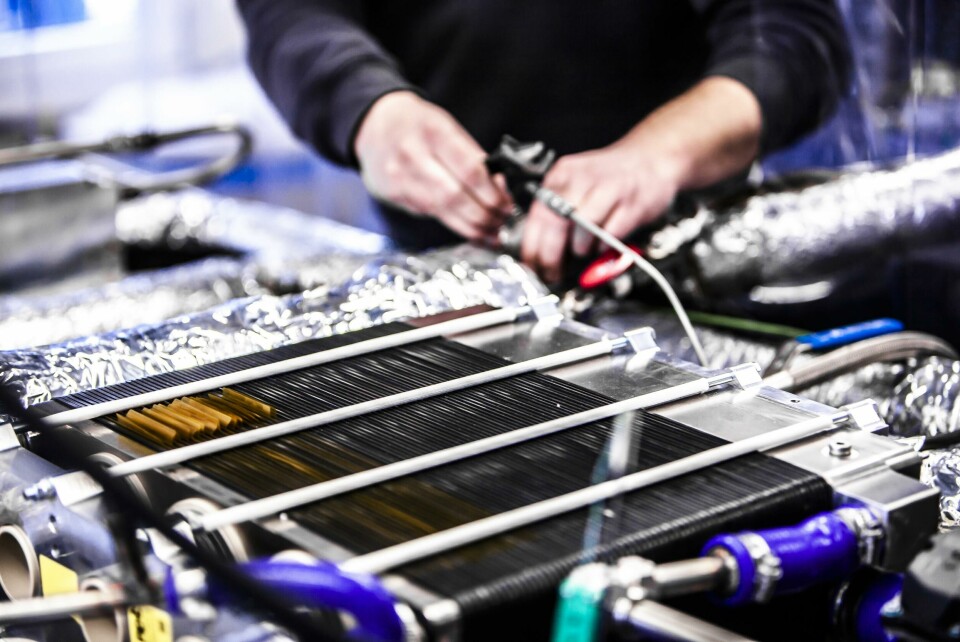
In November 2021, one of the established manufacturers of fuel cells, Canadian company Ballard Power, acquired the much smaller UK outfit Arcola Energy, with the latter changing its name to Ballard Motive Solutions. The UK company had previously used Ballard fuel cells in its own driveline system for commercial vehicles called the A-Drive and earlier in the year had moved into a new manufacturing facility on an industrial park in Dundee, Scotland.
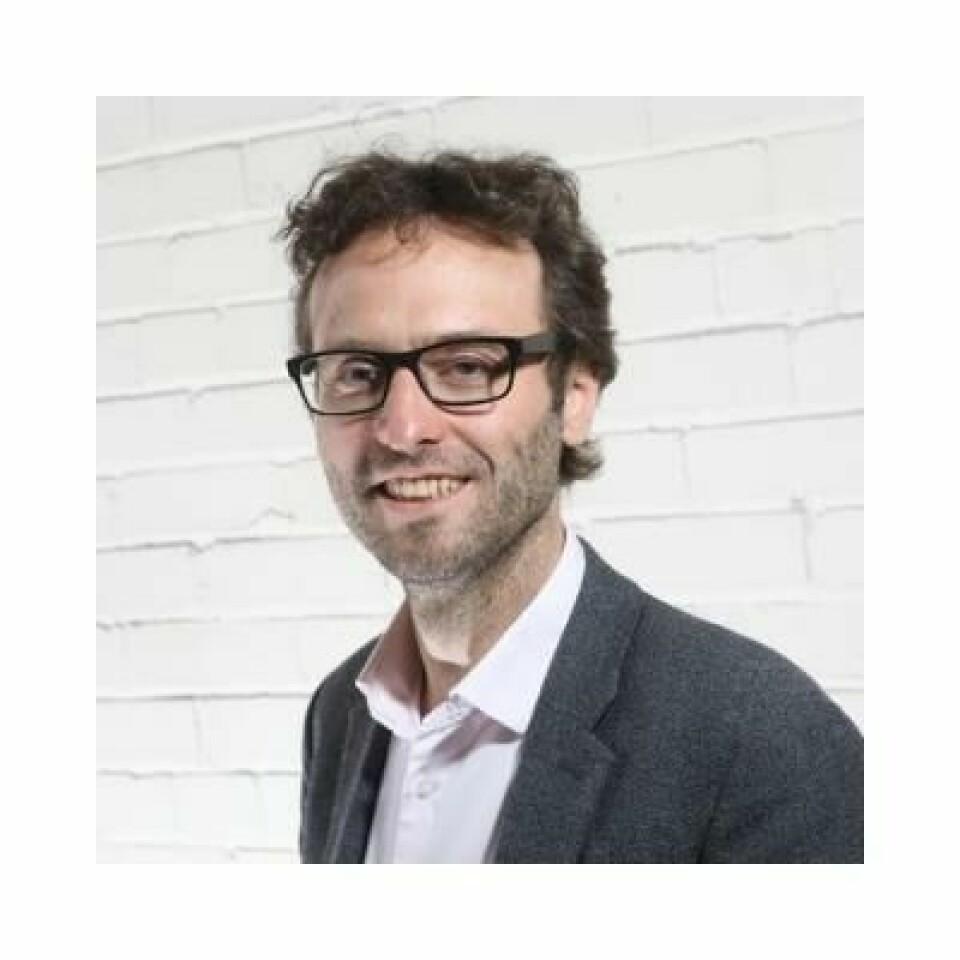
According to Dr Ben Todd, founder and CEO of Arcola who has continued in the same role after the acquisition, Ballard bought more than the rights to a product and in fact, he argues, the deal indicates how the application of the technology will need to be developed to meet both commercial and environmental objectives. “Companies that try to integrate fuel cells into vehicles are often quite small by global automotive industry standards,” he points out, even if the initial fuel cell manufacturer may be a major outfit like Ballard. “But by acquiring Arcola Ballard has now got not just a fuel cell, but also a platform with accompanying integration expertise that they can offer to vehicle OEMs.”
Dr Todd explains that in its manufacturing business the UK operation uses bought-in fuel cells as well as the batteries and hydrogen storage tanks necessary to construct its driveline product. But, he says, “we had to provide our own design expertise, control software and thinking about functional safety, which often sits in the software, as well as high and low voltage power electronics because we just couldn’t access them on the market. Standardised high voltage and low voltage power distribution units, for instance, just did not exist.”
Combining technologies and competences
But even if the necessary hardware to create complete fuel cell driveline systems is now more commonplace there is still a need for companies that want to supply them in volume to have the necessary integrated, in-house knowledge base. “Getting the driveline power management right with a combination of fuel cell and battery is non-trivial,” observes Dr Todd. Hence the deal to buy Arcola, which Dr Todd admits has so far actually built and sold “very few” of its A-Drive systems though it now has a deal to build 20 refuse collection trucks for the city of Glasgow. Expertise rather than existing market share is what is involved. “Ballard had a really nice fuel cell module now they have a really nice smart fuel cell module,” says Dr Todd.
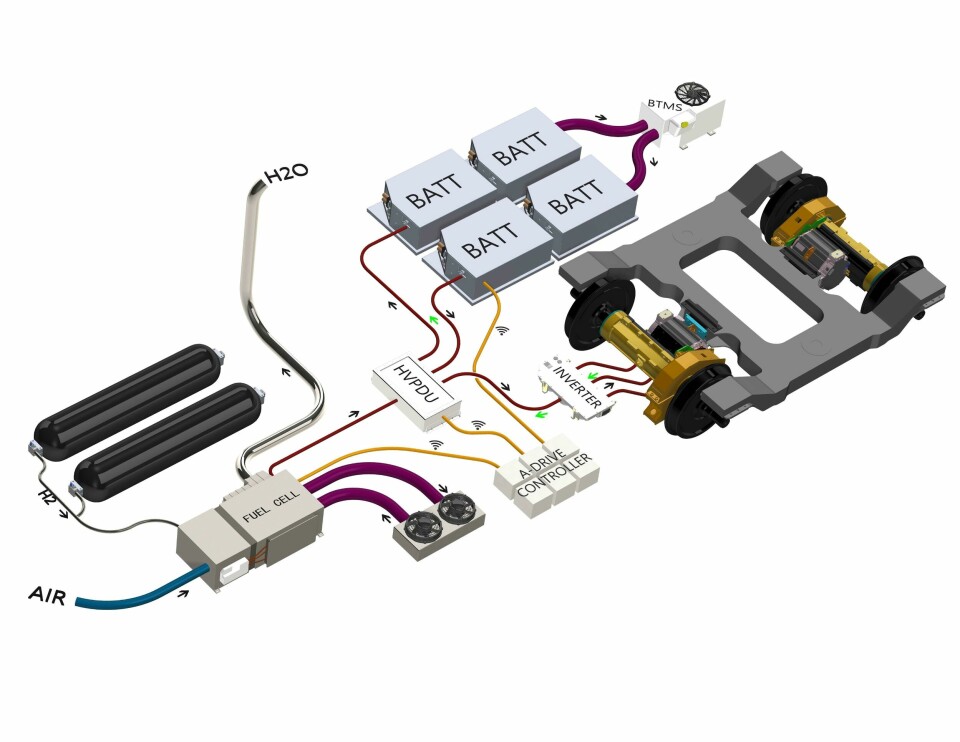
In practice, says Dr Todd, the UK operation will be able to work both with Ballard’s fuel cell development and manufacturing operation in Canada to enhance product capabilities and with OEM customers to support their application in real vehicles. In the first case, he says, “we will be better able to take into account what is happening deep in the electro-chemistry of the fuel cell.” In the second “we can work with them or even build their initial prototypes.”
Dr Todd explains that though the OEMs involved will have experience in the construction of driveline systems based on internal combustion engines they may have significant knowledge gaps impeding their ability to adopt fuel cell technology. “When they adopt fuel cells they may, for instance, say they don’t have the ability to communicate with wheel speed sensor,” he says. “Ballard in Canada will continue to make fuel cells, but the UK now becomes the centre of excellence in complete powertrain.”
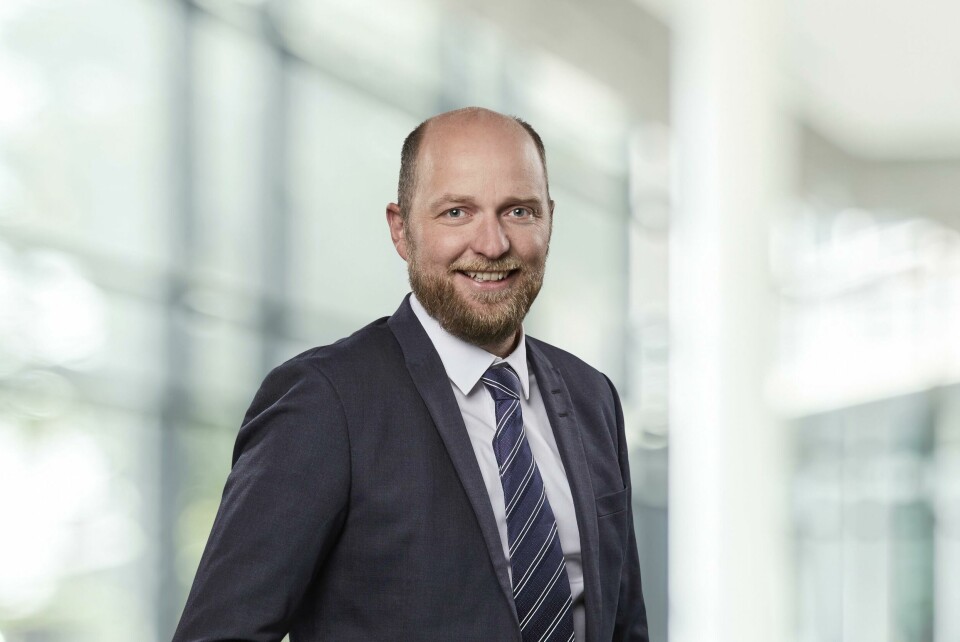
In Aalborg, Denmark, another company Blue World Technologies is setting up a plant to manufacture fuel cells themselves. It is doing so with the aid of an €15m investment from the Danish Growth Fund Vaekstfonden and German engine manufacturer Deutz. But, as CEO Anders Korsgaard explains, the company’s technology does have one unusual feature even in the still young market – its fuel cells use as their fuel liquid methanol which is converted into the necessary hydrogen by integrated ‘reformers’.
A necessary implication of this is that the company’s fuel cells operate at a much higher temperature than those fuelled from the start by pure hydrogen. “We are working with high temperature PEM (Proton Exchange Membrane) technology that operates at 160°C as opposed to more common low temperature systems that operate at 70-80°C,” confirms Korsgaard. “The efficiency of the conversion from methanol to electricity is also substantially higher than with a low temperature counterpart.”
As Korsgaard further explains the higher temperature is also necessary to deal with the slight impurities that can occur with methanol fuel. Nevertheless, there will inevitably be one further emission in addition to the water vapour that is common to hydrogen fuel cell systems – the carbon dioxide that along with hydrogen is the other major constituent of methanol. “There is local CO2 emission,” he confirms.
From an environmental point-of-view, Korsgaard continues, that is why the source of the methanol is important. It needs to be “e-methanol that is produced with renewable electricity with the CO2 content derived from biogas or the atmosphere.” When that is the case, he explains, then there is no net increase in atmospheric carbon dioxide: “It is CO2 that existed anyway.”
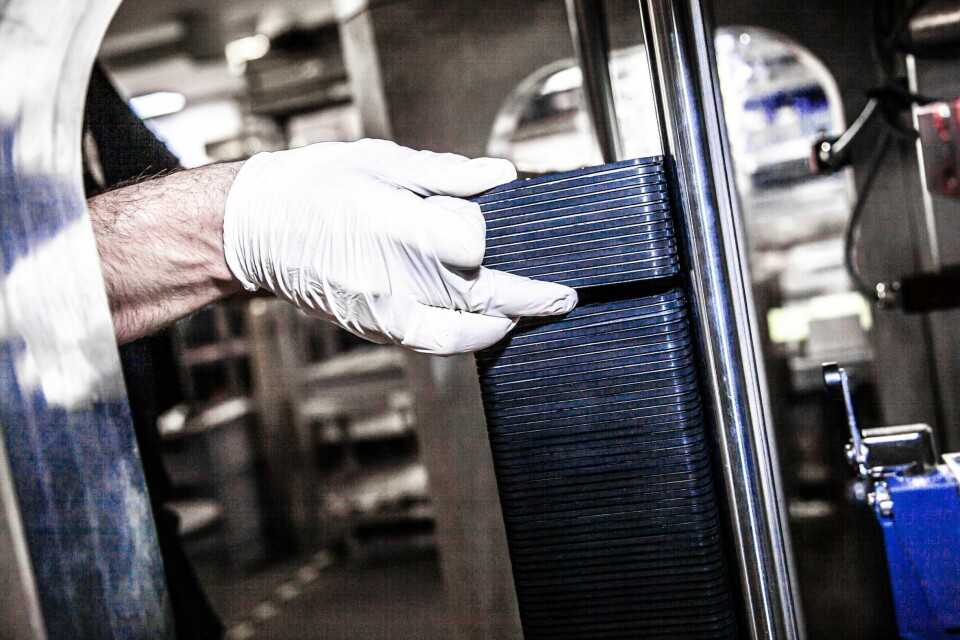
Alternative approaches to alternative fuel systems
With that allowance made then, Korsgaard continues, the multiple advantages of using methanol as the initial fuel can be exploited. Perhaps the most basic is simply that “a fuel cell converts methanol into usable energy more efficiently than any combustion process.”
But perhaps the most immediately important factor is the relative ease with which liquid methanol can be stored and transported compared with either gaseous or liquid hydrogen. “The cost for setting up a hydrogen infrastructure might be two to three times that for a new liquid fuel such as methanol,” observes Korsgaard. “Methanol is a liquid and easily transportable and storable at atmospheric pressure. This is true all the way from production to use.”
Korsgaard says that high temperature fuel cells were invented in 1990s whereas modern low temperature fuel cells originated in the 1960s. The difference between the types, though, is embodied in internal material usage rather than external geometry. “Blue World’s fuel cell uses membrane materials that are substantially different from low temperature counterparts,” he states. “We have a membrane and electrode between separator plates that are typically made of carbon and some polymer binder as in low temperature devices, but we use much higher performance polymer materials.”
The manufacturing plant in Aalborg is now being ramped up with the aim of properly establishing all its processes. “We want to get the plant up and running at volume levels before end of this year,” confirms Korsgaard. “It is one of the largest being built in Europe and will have most of core manufacturing capability in-house. We have just entered series production using ‘hard’ tools in other words actual production equipment.”
Given the variation in output of individual fuel cells according to the application Korsgaard does not put a figure to the number of units the plant may produce. Instead, he says that with a typical power output of 100-150kW for a fuel cell system for a commercial vehicle then with the addition of stationary applications he expects total output of the plant by the end of this year to be of systems with a combined power generation capacity of “tens” perhaps as high as fifty megawatts though further ahead that may grow significantly.
Material development
But the advent of fuel cells as an automotive power technology is also opening up opportunities for established companies with capabilities more directly transferable from the world of internal combustion (IC) engine systems. One such is Novares, a well-established Tier 1 supplier of plastic parts based in Lens, France.
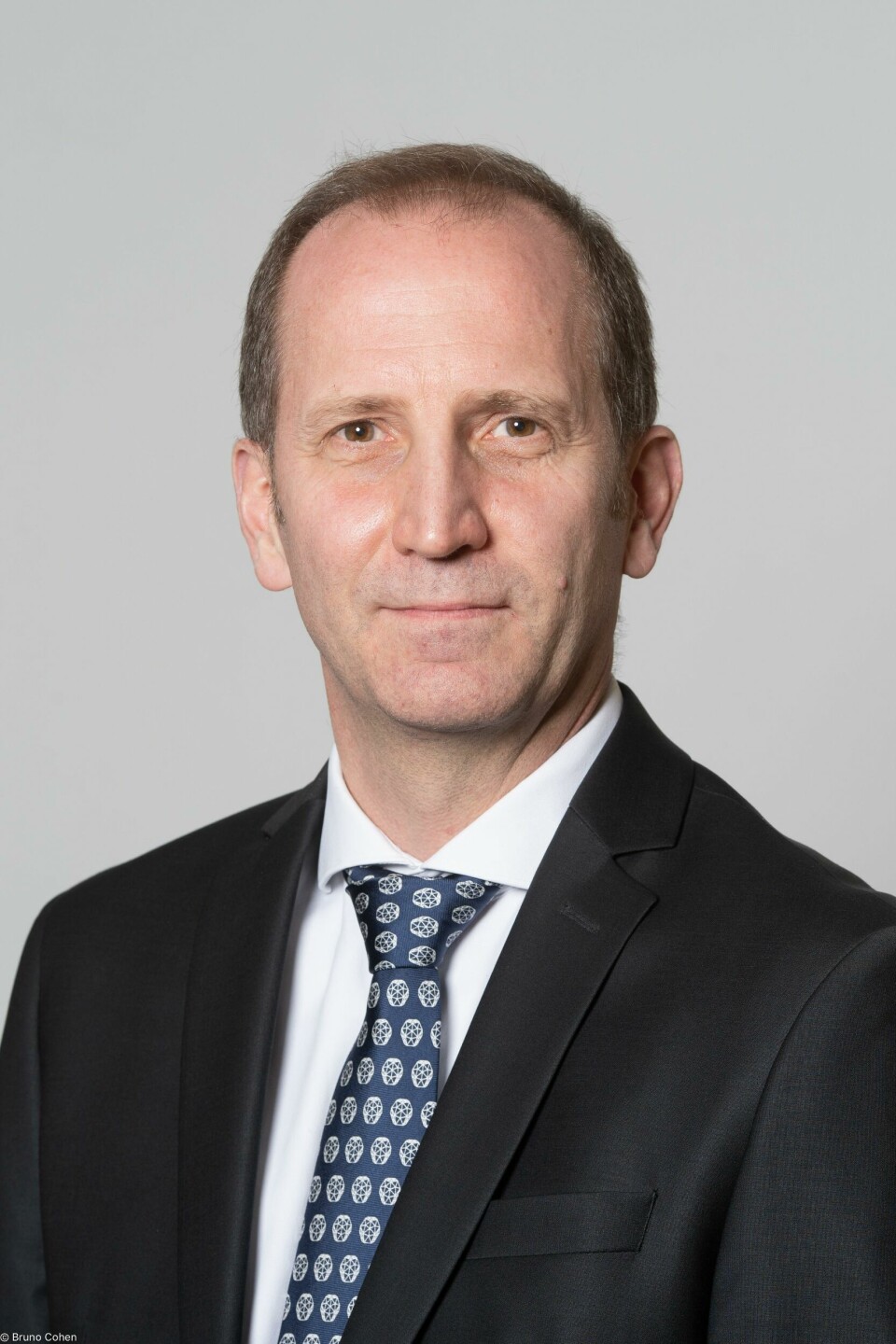
Luc Dornier, senior vice president group product development, confirms that the company has extensive experience in areas such as “acoustic, air and oil management in IC powertrains”. As such while the company has no intention of becoming fuel cell manufacturer it does see that area as offering the potential to exploit one of the major advantages plastic materials can provide when substituted for metals – weight reduction. Indeed, it has already developed its first product aimed specifically at this objective – endplates for fuel cell stacks made from injection moulded PPS material with a glass fibre infill.
The first of the endplates to enter production measure 400x270x50mm and provide a weight saving of more than 35% compared with an aluminium counterpart. “They enable 10kg of aluminium to be replaced by 4.4kg of plastic,” confirms Dornier. “That is for one plate so the saving for a complete fuel stack is 11.2kg.” But there is also cost saving at the manufacturing stage through the obviation of a machining process and its replacement by injection moulding. In use, Dornier adds, PPS is a stable, robust material and the endplates are coupled to the fuel stack by straightforward mechanical fastening.
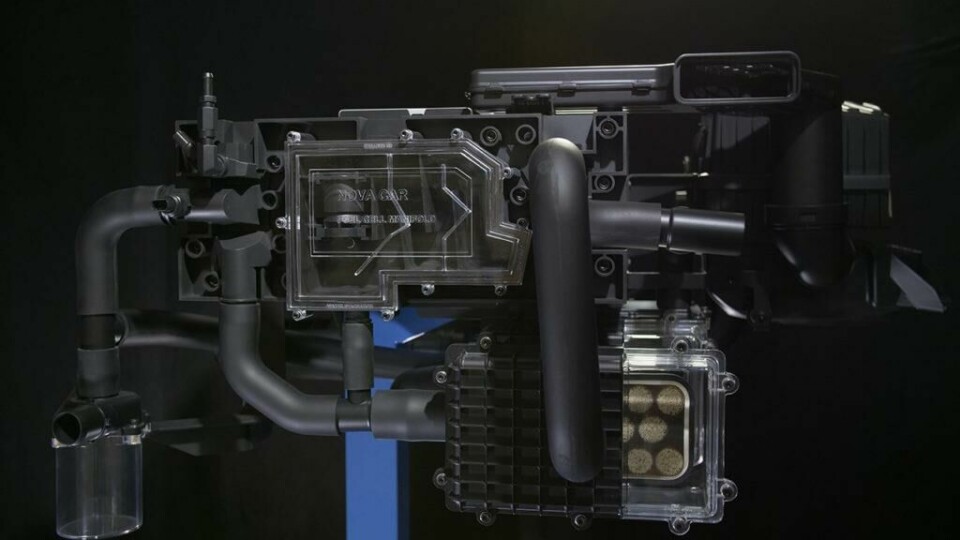
The manufacturing methodology has the further advantage that production can easily be located close to any OEM customer. “We have 42 sites around the world that can carry out injection moulding,” says Dornier. Indeed, this is the case for the first OEM to become a user of the endplates though Dornier can provide no more detail than that they are in China.
For Novares, though, the end-plate product is just a start. Dornier says that in fuel cell systems the company see the potential not just for the end plates but also for what he describes as much of the surrounding “balance of plant” including filters, manifolds and intakes. He confirms that the company already has “several other fuel cell related projects” underway.