Bridgestone commits a European record €207m investment to its Burgos tyre plant in Spain, aiming for BCMA principles and sustainable production
The record €207m investment aims at integrating BCMA to streamline production, boost capacity and promoting sustainable manufacturing
Bridgestone, the global tyre manufacturing leader has announced a material investment in its Burgos passenger tyre manufacturing site in Spain. The landmark funding, totaling up to €207 million, represents one of the largest single investments made by Bridgestone Europe to date; geared at innovation, sustainability and, according to the company, meeting the expectations of the tyremaker’s regional customers. The project, which aims for completion by 2030, includes a series of technological innovations focused on enhancing the production of high-value High Rim Diameter (HRD) tyres, specifically those measuring 18 inches and above.
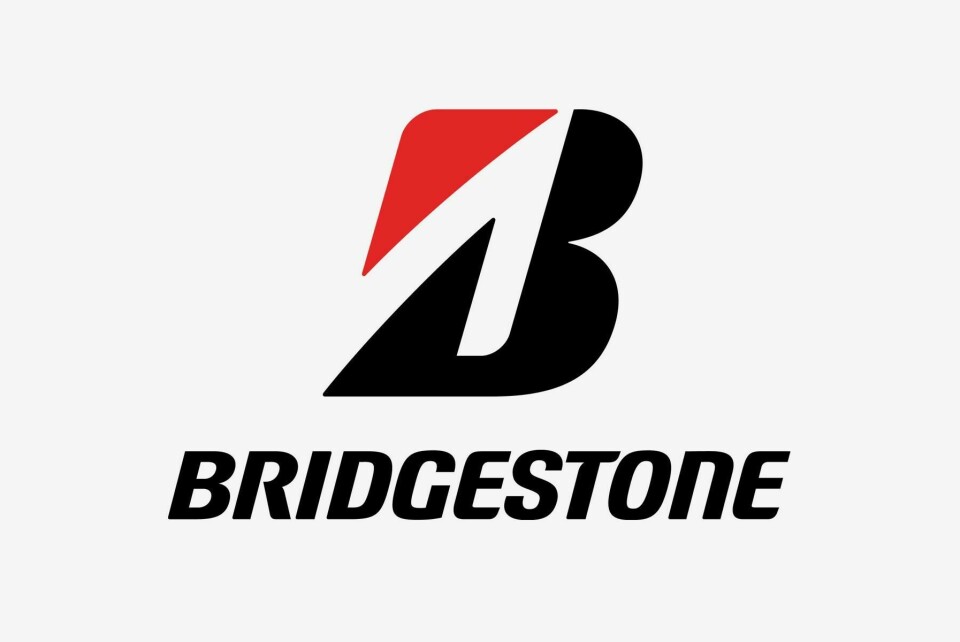
With an anticipated productivity increase of approximately 20% compared to current levels, (according to Bridgestone), the initiative will cater to the growing demand for premium and high-tech tyres across Europe.
Key elements of the technological transformation include advancements in automation to boost productivity, expansion of vulcanisation capacity, and the establishment of an automatic high bay warehouse to bolster tyre stock levels and streamline production processes. Through the implementation of Bridgestone Communality Modularity Architecture (BCMA), the company is positioning itself to further enhance its operational agility and efficiency, in an attempt to ensure adaptation to evolving market dynamics.
Aiming to exceed 7 Million tyres per annum
The Burgos facility, recognised for its robust production capabilities, is expected to achieve a 75 percent increase in HRD tyre production capacity, exceeding 7 million premium tyres annually. This transformation, if achieved, will position the Burgos plant as one of Bridgestone’s primary van tyre producers in Europe, further diversifying its product portfolio to cater to diverse customer demands.
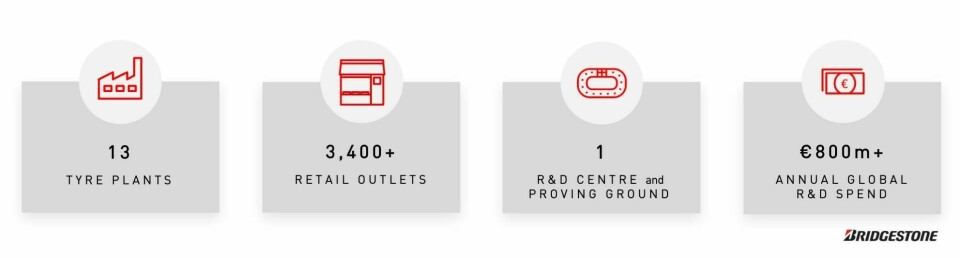
Emilio Tiberio, West Chief Technology Officer (CTO) of Bridgestone West, expressed enthusiasm about the strategic implications of the Burgos investment, stating: “At Bridgestone, we are moving into a new phase of European and global growth by combining innovation and sustainability at our Burgos facility in Spain. This multi-million-euro investment is aimed at strengthening our premium tyre business by increasing our productivity, logistics autonomy and tyre offering in the high value segments.
“Furthermore, we are proud to contribute significantly to the economic development of Burgos, Castilla y León and Spain by continuing to strengthen our manufacturing and sustainable footprint in a strategic region for us at the European level”.
Solar powered production: Burgos’ sustainability boost
Beyond enhancing manufacturing capabilities, Bridgestone’s investment holds important implications for sustainability. By integrating cutting-edge technology, automation and research and development (R&D) initiatives, the Burgos plant is set to significantly reduce carbon emissions, with an estimated reduction of 410 tons of CO2 annually - compared to current levels. The efforts also align with Bridgestone’s broader objectives of achieving carbon neutrality (across scopes 1 and 2) by 2050. According to Bridgestone, sustainable production is central to Bridgestone’s Burgos operations, a site which saw the recent installation of over 20,000 solar panels covering an area “equivalent to five football fields”. With a total output of 9.2 MW, the solar installation allows the plant to derive between 10% and 14% of its electrical energy directly from renewable sources, marking a significant stride towards reducing its environmental footprint.
Tiberio commented: “In line with the Bridgestone E8 Commitment, this project will fortify the Burgos plant’s capabilities towards 2030 and beyond, ensuring sustainable employment and a strategic evolution towards smart and green manufacturing. These advancements will also accelerate our goal of carbon neutrality (scopes 1 and 2) by 2050.
“By boosting production and optimising environmental practices through technology, automation, and R&D, the Burgos plant is geared for the future, setting a new benchmark within Bridgestone’s manufacturing network.”