As automotive manufacturing digitises, new smart factory roles in AI, data and IIoT are replacing traditional shopfloor jobs and transforming skills requirements
As automotive manufacturing becomes more intelligent, connected and software-defined, factory roles are shifting. New digital profiles are emerging, while traditional ones risk becoming obsolete.
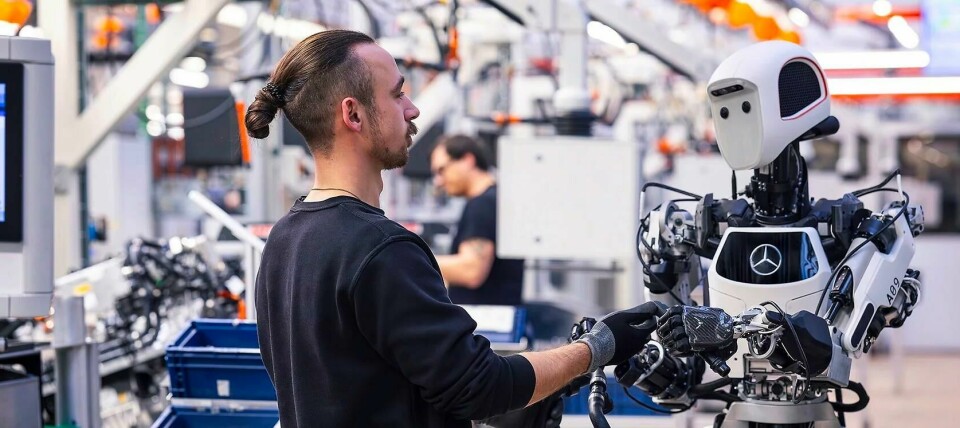
How have the requirements for jobs in the smart factory changed in light of the digital revolution? Georg C. Scheiber, Partner and Director at the human resources consultancy von Rundstedt, uses the term “revolution” rather sparingly. However, the transformation of the industry, now driven by Chinese competitors, is tangible: “The concept of the software-defined vehicle is also changing the concept of the smart factory,” emphasises Scheiber. “This means completely new challenges for the German automotive industry, which will also have significantly greater consequences for its employees and their skills than was assumed five years ago.”
”Employment in IT professions in the automotive industry has increased by around a quarter since 2019 and by as much as 85 per cent since 2013”
Scheiber cites five job profiles in particular that are becoming increasingly indispensable and relevant for the reskilling of workforces: industrial data analyst (preferably for engineers), robotics coordinator (further development of technical apprenticeships), industry cloud architect (preferably for computer scientists), IT/IoT solution architect (preferably for electrical engineers and computer scientists), and automation technician (further development of the apprenticeship of electronics technician for automation technology).
The change will not be without pain, namely, the “devaluation of the core competencies of white- and blue-collar employees, resulting in salary cuts or even job losses,” says Scheiber.
These factory jobs have a future
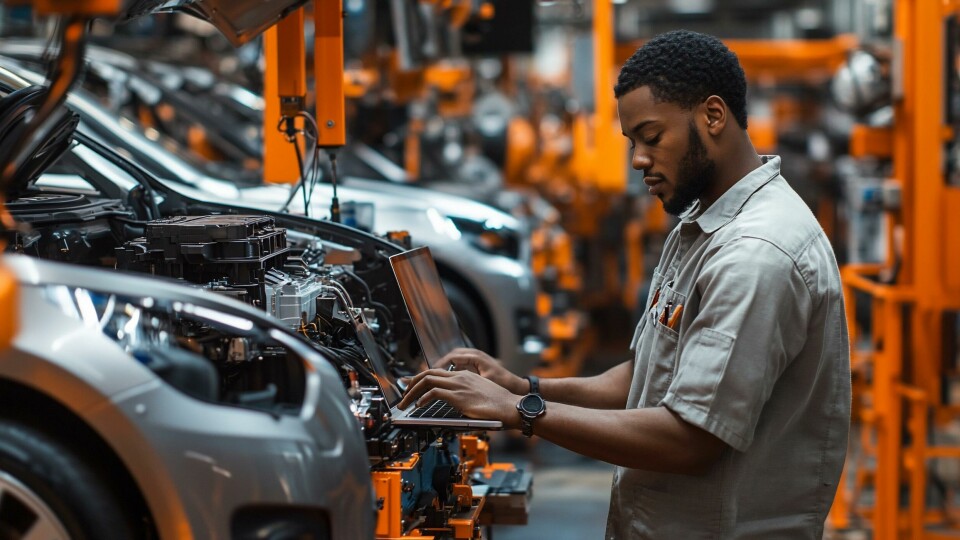
The VDA has specifically published a study that shows how 700 professions in the industry will develop in the future. “Due to the electrification of the powertrain, vehicle manufacturing requires less overall employment than in the past,” the authors state.
“Furthermore, there are significant shifts within employment.” Occupations in mechanical and industrial engineering, as well as metalworking, in particular, have already lost relevance. In contrast, there have been increases in occupations in automotive engineering, technical research and development, as well as in computer science, electrical engineering, and software development - profiles without which nothing works in the smart factory.
“For example, employment in IT professions in the automotive industry has increased by around a quarter since 2019 and by as much as 85 per cent since 2013,” the study states. The shortage of skilled workers is noticeable in areas such as IT network technology, IT coordination, IT administration, and IT organisation. The deficit here is likely to grow even further in the future, according to the authors.
The Big Three: Big Data, IIoT, AI
“The most important career fields in the smart factory today revolve around security, big data, cloud architectures, the Internet of Things, and artificial intelligence,” explains Florian Harzenetter, Senior Director and Global Advisor for Industry, Electronics & High-Tech Customers at software manufacturer PTC. Experts in the Industrial Internet of Things (IIoT) are particularly needed. “One promising position for the future is IT/IoT solutions architects,” says Harzenetter.
Specialists in this field develop the system design for all people, machines, materials, platforms, and products connected in real time. “In a sense, they are the architects of the entire IT architecture,” emphasises Harzenetter.
Read more Smart Factory stories
Boosting productivity in automotive manufacturing with Digital Twins
Mercedes-Benz excels in connected manufacturing at Berlin-Marienfelde
Employees with skills in additive manufacturing also have good prospects, as the technology is becoming increasingly relevant, especially in the automotive sector, not only for prototype construction and small series production. 3D printing, for example, can support smart factories with automated on-demand production - which is particularly helpful in the event of supply chain disruptions.
The general topic of resilient production also includes experts in predictive maintenance who are familiar with machine learning and corresponding tools to minimise downtime. “In the future, no smart factory will be able to do without AI experts to gain real-time insights into processes and thus increase resilience and efficiency,” emphasises Harzenetter.
“The systematic acquisition of these soft skills must be given significantly greater priority in academic training and in company upskilling and reskilling measures”
Georg C. Scheiber, Partner & Director, von Rundstedt
All the better if this is underpinned by expertise in virtual reality (VR) and augmented reality (AR). “When AR/VR tools are combined with artificial intelligence in quality management, for example, then visual quality control is taken to the next level,” Harzenetter is convinced. Therefore, inspection engineers who can integrate corresponding tools as an integrated solution, for example in end-of-the-line processes, are in demand now and in the future.
“Not only does this make quality control faster and more precise, but it also significantly improves overall production efficiency,” says Harzenetter, “because it identifies hidden problems throughout the entire manufacturing process.”
Are companies prepared for this?
In general, Scheiber still sees some uncertainty about the direction in which requirements will change: “Due to the accelerated development of generative AI for industrial applications, it is currently not possible to predict which clearly defined job profiles will emerge.” In current projects, the specific academic qualifications of team members play a subordinate role; rather, a strong willingness to learn, a keen curiosity beyond the boundaries of one’s own discipline, and strong cooperation and communication skills in intercultural teams are of great importance.
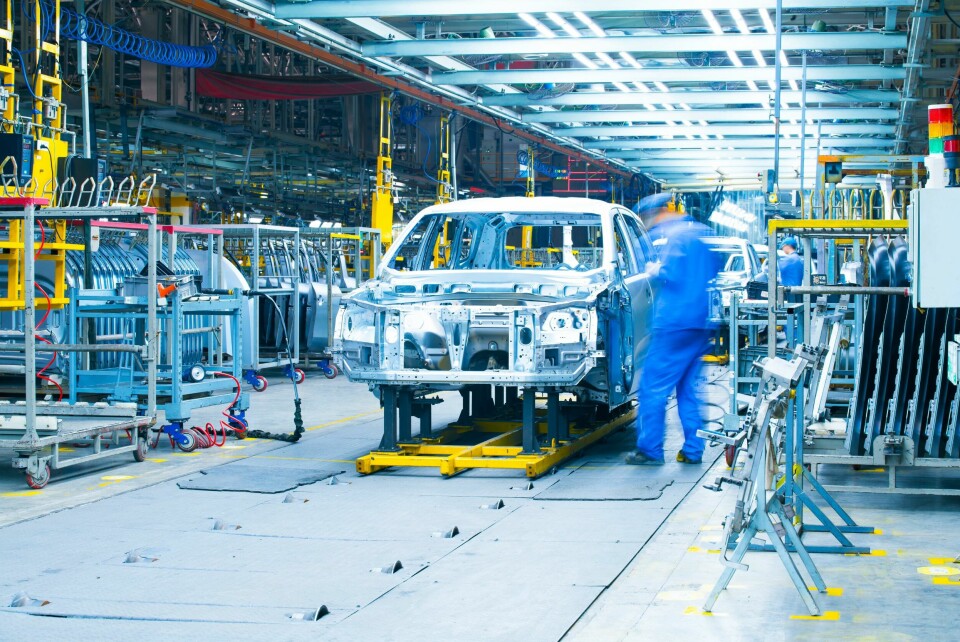
His advice: “The systematic acquisition of these soft skills must be given significantly greater priority in academic training and in company upskilling and reskilling measures.”
Scheiber believes that automotive manufacturers and suppliers are grappling intensively with the broad topic of new qualification requirements, both in the context of the software-defined vehicle approach and in the further development of the smart factory concept: “Due to the sharply increasing competitive pressure from the Far East, the scope for maneuver in the important factors of budget and time is severely limited.”
The crucial question will be how the transition from the hardware era “with all the hard-earned development and manufacturing know-how,” according to Scheiber, to the software era can be successful and how completely new knowledge and skills can be developed in a short time: “This transition can certainly be described as a revolution.”