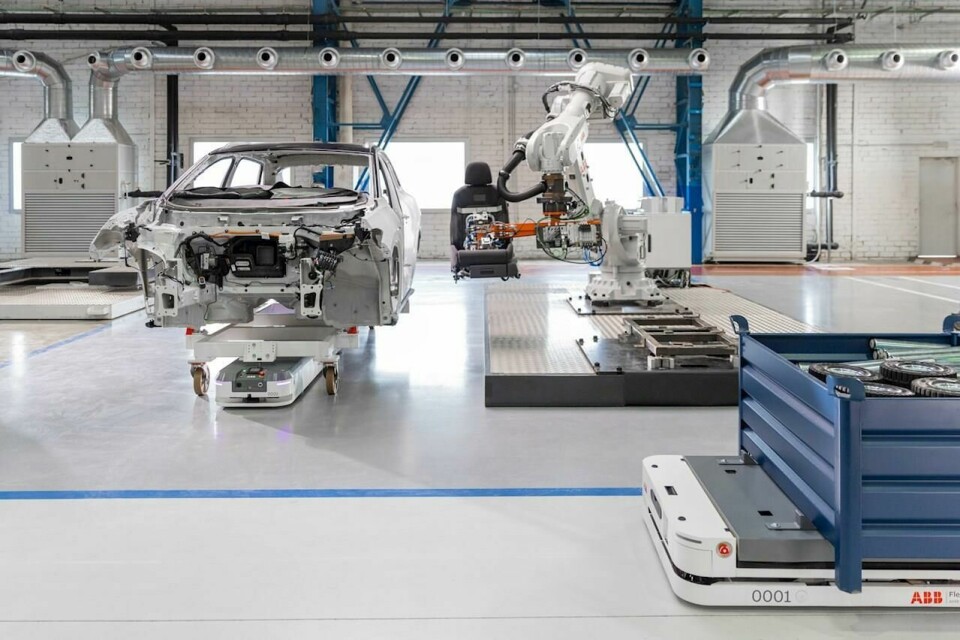
More than moving parts – autonomous mobile robots
The fundamental changes in the type of vehicles emerging from automotive manufacturing plants worldwide most obviously the increasing proportion of electric vehicles (EVs) are also having repercussions for the development of another type of vehicle – autonomous mobile robots
These vehicles are developing beyond just electric trucks or trollies used to transport parts and increasingly vehicle assemblies around manufacturing plants. As Veronica Pascual Boé explains they are changing from something that might once have been described as an automated guided vehicle (AGV) to what is now termed an autonomous mobile robot (AMR).
Pascual Boé is global head of AMR business for ABB Robotics. Until a little over a year ago she was CEO of Asti Mobile Robotics, a Spanish company that had developed its own range of AMRs and which was then acquired by the Swiss-based multinational. All of Asti’s former products and technology are now part of the ABB portfolio.
The difference between the two concepts, Pascual Boé continues, is not one of physical configuration or capabilities – they are still driverless wheeled devices that transport loads from one point to another in a production environment. “The essential distinguishing capabilities between the two are concerned with navigation and the ability to respond to unstructured environments,” she states. In turn those attributes form the basis of the autonomy that is the key feature of AMR technology.
As Pascual Boé explains actual applications for AMRs neatly divide into two distinct areas. The first is relatively straightforward in terms of its purpose – the transport of materials and components from one point to another prior to their use in actual manufacturing. Applications in this “intralogistics” area, she says, comprise “moving goods between different areas such as unloading, warehousing, lineside ‘supermarkets’, order picking and delivering to manufacturing cells.” In this context the essential requirements for the AMRs are, she explains, “that they are able to interact with humans and to changes in their surroundings.”
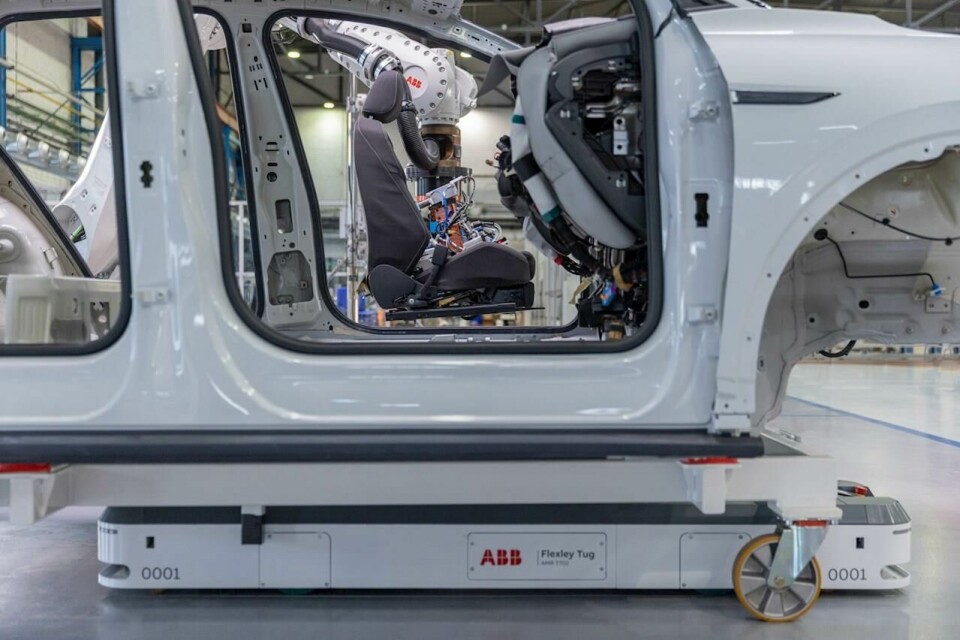
Supporting flexible production
The second is what Pascual Boé terms “sub-assembly” operation, which effectively means replacing fixed conveyors for the transport of vehicle assemblies from station to station on production lines. This is obviously a newer application though one that is already established in the industry at least for lower volume, higher end vehicles. Asti, she confirms, was already well used to providing AMRs for this purpose even before the acquisition by ABB.
This is, Pascual Boé says, an application that will become much more important as that fundamental shift towards EV production increasingly kicks in. A reason for this, though, is not an immediate requirement to support some specific type of manufacturing procedure but the opposite – the need to enable vehicle makers to experiment in order to establish the optimal procedures for the manufacture or assembly of new types of vehicle structures with which they may be unfamiliar.
Quite simply, Pascual Boé says, “many processes are still not fixed.” An example she cites is that of the fitting of battery trays into vehicles. Is that task best effected before or after the batteries themselves have been installed? At the moment, she estimates, a little under a third of ABB’s AMR applications are in support of direct manufacturing as opposed to ancillary logistical operations but she indicates she expects that proportion to increase significantly.
As such, Pascual Boé states, “flexibility” is the key requirement. In fact, she continues, two types of flexibility are needed. AMRs, she explains, can play a crucial role in supporting not just the ability of manufacturers to make different types of vehicles in the same production space but also to vary volumes.
As Pascual Boé further notes, not only are automotive production environments having to cope with the transition from internal combustion engine (ICE) vehicles to EVs they are also having to satisfy individual purchaser demands for high degrees of personalised customisation of finished vehicles. She is confident it will increasingly be provided by production environments comprising manufacturing cells serviced by AMRs moving between them – a type of configuration that has the intrinsic characteristic that it can be reprogrammed or even reconfigured quickly and easily according to changing requirements.
An important part of ABB’s strategy, Pascual Boé confirms, is to tap into the expertise of specialist technology development companies. It is doing so right now as it prepares itself for an upgrade in the on-board technology used by its vehicles that she believes will significantly enhance their capabilities.
So far, Pascual Boé explains, the autonomous navigation capability of its machines has been affected by an approach known as SLAM standing for Simultaneous Localisation and Mapping which utilises laser-based LIDAR technology. But ABB is now targeting the second quarter of 2023 as the date to introduce an enhanced navigation technology known as VSLAM in which the extra letter stands for Visual because the primary navigation capability is now provided by a camera array that provides the AMR with a comprehensive all-round awareness of its surroundings.
Adding vision technology
In this case the technology developer is Sevensense based in Zurich that was spun-off from the Swiss Federal Institute of Technology some four years ago and now employs 36 people in developing what chief business development officer and co-founder Gianluca Cesari describes as the “eyes and brains for mobile robots”. Cesari says that when vision technology is used as the means of navigating AMRs then both robustness of operation and flexibility of application are greatly enhanced compared with LIDAR-based systems. Indeed, when vision technology is combined with on-board artificial intelligence (AI) computing power then, says Cesari, the difference between the two is “of an order of magnitude”.
Cesari explains that several factors are involved. That older technology, he points out, usually requires physical reflectors to be positioned around the routes it will be programmed to follow. In addition, he continues, 2D technology suffers from the limitation that it “sees everything as a plane”. In contrast VSLAM utilises a camera array to provide a comprehensive “all round” vision capability without any need for reflectors.
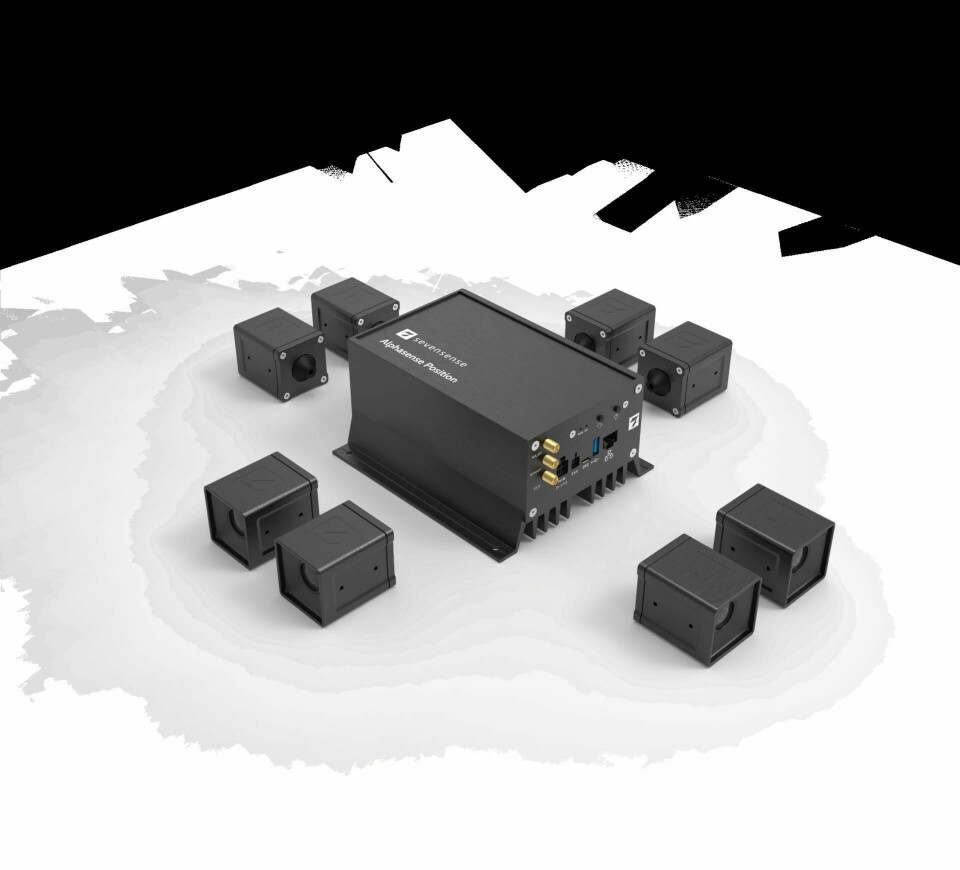
In practical terms this combination of data gathering and information processing has several immediate benefits. “It can cope much better with dynamic environments in which people or other carts are moving around,” Cesari states. But perhaps just as importantly the technology can adapt itself immediately to changes in the surrounding infrastructure that provides its reference system. An example might be when a stack of pallets is moved. “It can withstand very deep levels of change in its environment,” he confirms.
A further benefit, Cesari adds, is that AMRs equipped in this way can move seamlessly and safely between indoors and outdoors operating areas. In fact, the technology has in one respect run ahead of itself because, as he concedes, vision systems “are not yet safety-certified” and so some LIDAR is still necessary to provide mandatory collision avoidance capability.
Sevensense calls the VSLAM technology it has developed Alphasense and Cesari confirms that the company has been refining it ready for market launch with potential customers for the last couple of years. He has no doubts about its capabilities but does concede that the wider market is perhaps not yet fully aware of them. To help ameliorate this situation the company launched evaluation kit last year that he describes as a “plug and play box that can be mounted on vehicle to allow users to evaluate potential of technology.” As far as he is concerned that potential can be quantified quite precisely. “VSLAM provides repeatability to an accuracy of 4mm,” he states.
In fact, the automotive industry is not just a user of AMR technology but also a source of it in the form of idealworks, a BMW Group subsidiary spun out of the car maker two years ago to bring its experience and expertise in the area to the market. CEO Michael Schneider is quick to make the point, though, that the Munich-based company can serve the needs of a much wider market.
“Precisely because our products and technology were initially developed to cater to BMW Group use cases, such as complex logistics and material flow processes with challenging layouts, working with dollies and pallets, and connecting to peripheral devices and computer systems they are relevant to any environment with highly complex material flows,” Schneider states. “Features such as our AnyFleet traffic management and iw.hub dynamic obstacle avoidance capabilities allow us to interact safely and efficiently with human operators or other AGVs and AMRs.”
As Schneider further explains the company aims to support a change in the use of technology in industry from automation towards autonomy. “Our AMRs run at speeds of 8km/h and can autonomously pick up, transport, and deliver payloads of up to 1,000 kg,” he states. “Moreover, implementation does not require any structural adjustments to the existing facility, so that no markers, magnet, or QR codes are needed. Instead, the system navigates autonomously. Literally, all we need is a good WiFi connection and a working power outlet.”
A crucial enabling factor to comprehensive AMR implementation, Schneider continues, is compliance with the VDA 5050 standardised interface that enables communication between different mobile robots and a central fleet management software system. “Mobile robot interoperability that allows users to manage their fleets from one central place is a core focus point,” he confirms. “VDA 5050 is the answer to some complex challenges customers were facing if they wished to implement AGVs and/or AMRs from more than one supplier. If the machines were only able to communicate with their own fleet management system, the implementation of solutions from two or more suppliers would result in interoperability issues.”
In this context Schneider explains that the name of the company’s central cloud platform is not accidental. “AnyFleet enables the standardised integration of third-party devices and also connects to IoT devices such as doors, sensors, stations and traffic lights as well as computer systems including both WMS and ERP systems,” he confirms.
In fact, continues Schneider, both cloud communications and artificial intelligence (AI) are vital underpinning capabilities. “The robot streams its data, including accurate position, telemetry and temperature, and receives tasks to be executed from the cloud,” he explains. “AI allows us to deploy scalable services, such as traffic management, task assignment and collision monitoring, which are crucial for the operation and optimisation of robotics fleets.”
The intelligence is split between the robot and the cloud. Software on the robot running on what Schneider says is “a proprietary compact industrial PC powered by an NVIDIA GPU” enables the machine to navigate itself through a dynamic environment by making decisions based on its surroundings and predefined rules. At the same time AnyFleet controls overall logistics processes and material flows.
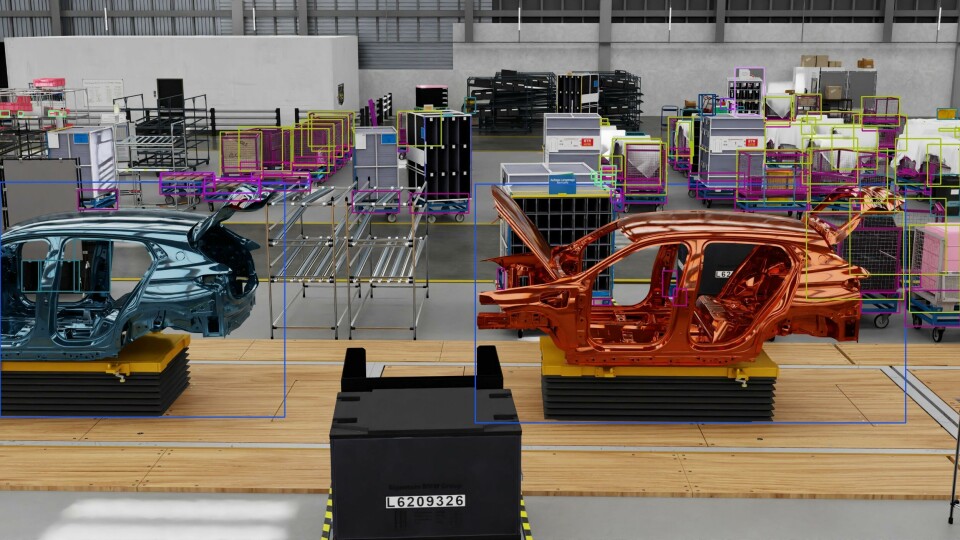
But now idealworks along with NVIDIA, Microsoft and BMW GROUP’s own TechOffice MUNICH have been involved in the development of a new capability called SORDI that Schneider is confident will prove a major asset to the company. Short for Synthetic Object Recognition Dataset for Industries, he says it consists of “more than 800,000 photorealistic images of production resources in 80 classes and includes objects of relevance in the core technologies of automotive engineering and logistics.” In fact, he states, “it is the world’s largest reference dataset for artificial intelligence in manufacturing and production.”
Schneider says that SORDI is specifically designed for industrial environments and that it “accelerates neural network training for object recognition in the factory environment, allows much faster training of AI models and thus serves significantly to increase the cost efficiency of AI in production.” He says it effectively constitutes “a starter kit for companies that want to get into AI model training that will enable them to supplement their own dataset or to fine-tune their own models particularly do not have the necessary resources to generate synthetic data themselves.”
Currently, Schneider reports, idealworks has its logistics technology running in about 20 locations worldwide, including BMW’s Hams Hall engine plant in the UK. For the future the vision is “to offer a holistic robotics ecosystem consisting of three independent but compatible core components – robotics intelligence, robotics fleet and a central cloud platform – that will allow users to have a single point of contact in their logistics automation projects. This will be achieved by providing them with a centralised, but user-friendly platform that will enable them to operate heterogeneous fleets of robots, while leveraging IoT devices, computer systems and microservices.”