ONE’s innovative strategies in chemistry, manufacturing and sustainability are transforming EV safety
AMS explores Our Next Energy’s (ONE) innovative approach to EV battery safety. The company’s CEO and founder, Mujeeb Ijaz, discusses manufacturing solutions to eliminate thermal runaway, enhance range, and optimise sustainability
There’s a vehicle fire every few minutes somewhere in the world, and most of those fires do not involve electric vehicles. Little if any reliable data exists to show vehicle fires by powertrain type, but there’s plenty of mainstream media discussion about the risk of fire in EVs. Well-informed or not, it’s a factor in EV consideration, and EV industry stakeholders have their work cut out to remove fire risk from the discussion.
In a vehicle with an internal combustion engine, a fire is called a fire. In a lithium-ion battery EV, it’s more complicated; a thermal runaway, as it is known, involves a rapid and uncontrollable increase in temperature and pressure within the battery cells, triggered by events such as overcharging, a short circuit, impact, manufacturing defects, or extreme environmental conditions. A thermal runaway can result in cell damage, fires which are difficult to fully extinguish, or even explosions.
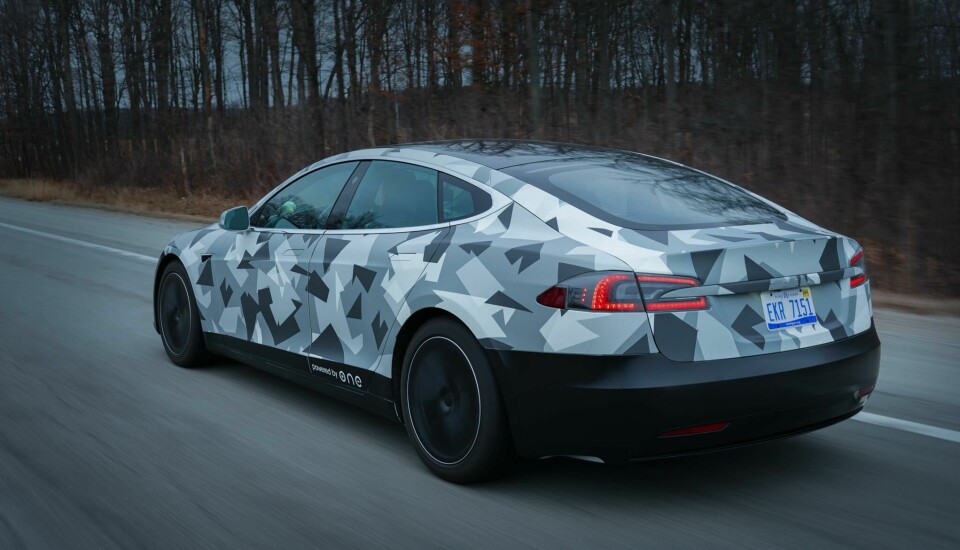
Much of a Li-ion battery’s performance can be attributed to the chemistry used in the cathode-active material (CAM). But there’s only so much that can be done to improve performance and safety by adjusting chemistry alone, and Detroit-headquartered battery start-up Our Next Energy (ONE.ai)believes it has a manufacturing solution to increase range and safety.
ONE made headlines in early 2022 when it completed a 752-mile (1,210 km) test drive through the US state of Michigan on a single charge, in the Gemini 1, a Tesla Model S equipped with a ONE battery – a feat which it then followed on a controlled dynamometer setting with an even higher single-charge range of 882 miles.
At its factory in Van Buren Township, Michigan, ONE produces cells and assembles full battery packs. The company is preparing to increase output to the equivalent of around 35,000 automobile battery by the end of 2024, and 100,000 the following year.
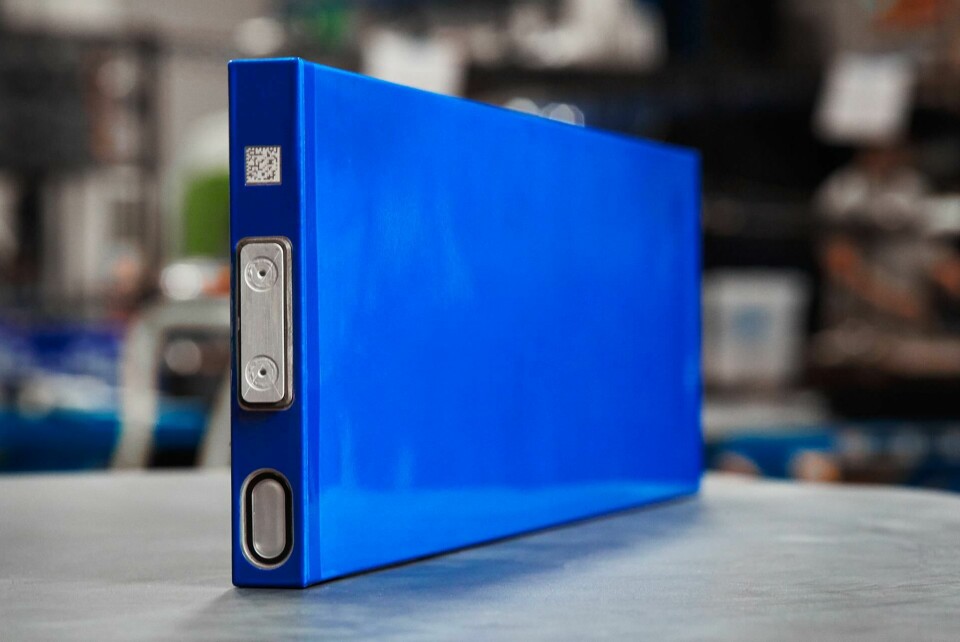
Taking a total systems approach to battery supply, and favouring lithium iron phosphate (LFP) batteries over lithium nickel manganese cobalt (NMC) chemistry, ONE claims it can deliver improvements on cost, energy density, and remove fire and thermal runaway from the conversation.
Three ingredients that take centre stage
Three ingredients are required for a Li-ion EV battery to present a thermal runaway risk, namely ignition, fuel, and oxygen, explains Mujeeb Ijaz, founder and chief executive of ONE.
In a Li-ion battery, an unexpected ignition event such as a short circuit, can release energy, and cause a sharp increase in temperature; electrolyte and other flammable battery pack contents tick the fuel box. But while materials and energy are unavoidable pillars of any battery, notes Ijaz, “the third thermal runaway issue, which we can engineer and manufacture out of a battery, is the content of oxygen inside the cathode active material.”
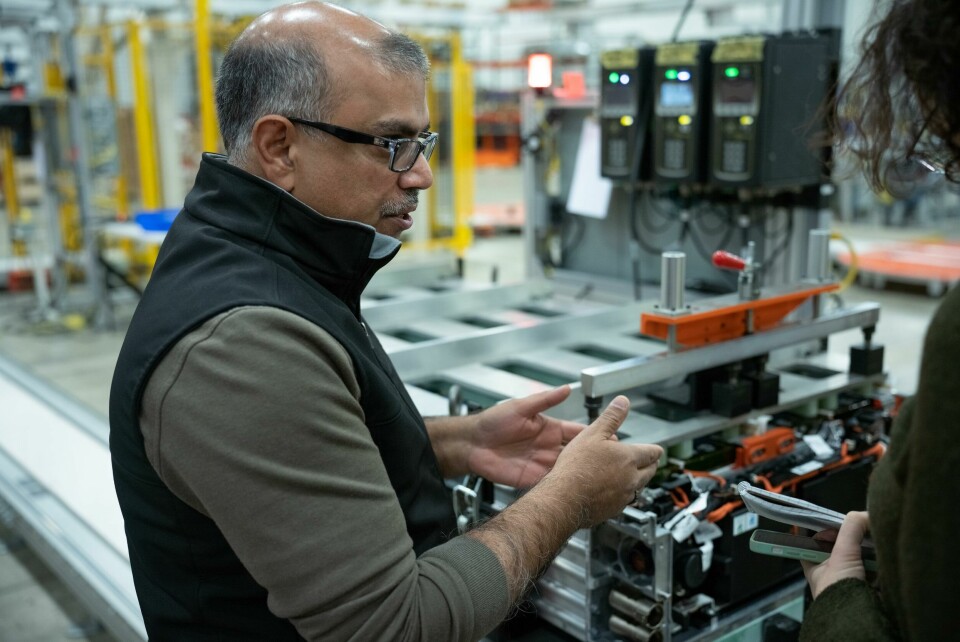
The CAM in a typical NMC chemistry, he explains, holds considerable trapped oxygen. “Effectively, you have a nickel cobalt manganese oxygen battery. The electrolyte may be relatively insignificant, but the CAM is a big player. In terms of mass, it accounts for about 40% of the battery, and is also one-third oxygen. In other words, you’re carrying all the oxygen necessary for thermal runaway.”
That’s one of the main reasons why ONE is developing LFP batteries, eliminating the oxygen content in the cathode.
According to the International Energy Agency (IEA), NMC accounted for 60% of global demand in 2022, with LFP accounting for just under 30%. Demand for LFP is rising, however, and it is expected to soon become the dominant EV battery chemistry. The automotive industry is drawn to several LFP advantages over NMC, including safety factors, longer cycle life, and lower costs thanks to the absence of valuable materials, notably cobalt.
ONE’s innovative cell-to-pack approach
Of interest to this publication, however, is not so much ONE’s interest in the battery chemistry, as its approach to battery pack manufacturing. Ijaz says ONE operates as a pack systems integrator, focusing on supplying stiffer structural packs, with simpler mounting strategies, using lighter materials to reduce cost.
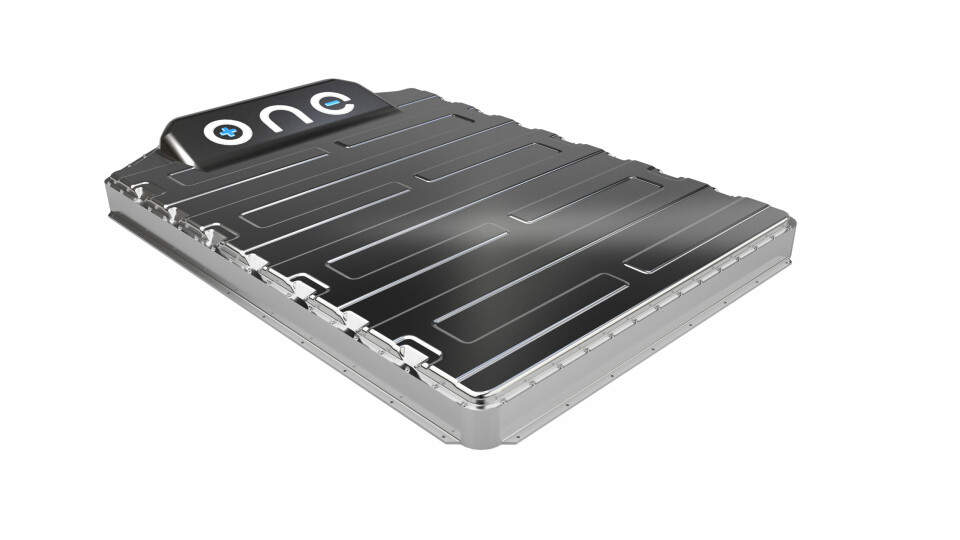
“We’re trying to make a lighter, smaller battery,” explains Ijaz. “Most current battery packs involve cells assembled into modules, which are in turn assembled into the battery pack. But this requires module mounting rails, frames, and crossmembers, all of which consume considerable weight and volume.”
In some leading mainstream EV batteries using cylindrical cells, he continues, the aggregated volume of all cells is just 32% of the volume of the whole battery, the rest accounted for by module packaging and mounting, cooling, electronics, and the battery enclosure. “Sometimes, the cell-to-pack volume can be up to 50%. But whether 32% or 50%, neither number is very impressive,” says Ijaz.
With its new LFP battery, ONE claims to have closed the energy density gap to within six percent of leading NMC EV battery packs, and attributes a combination of lightweighting and increased energy density to the Aries II battery’s range of over 350 miles.
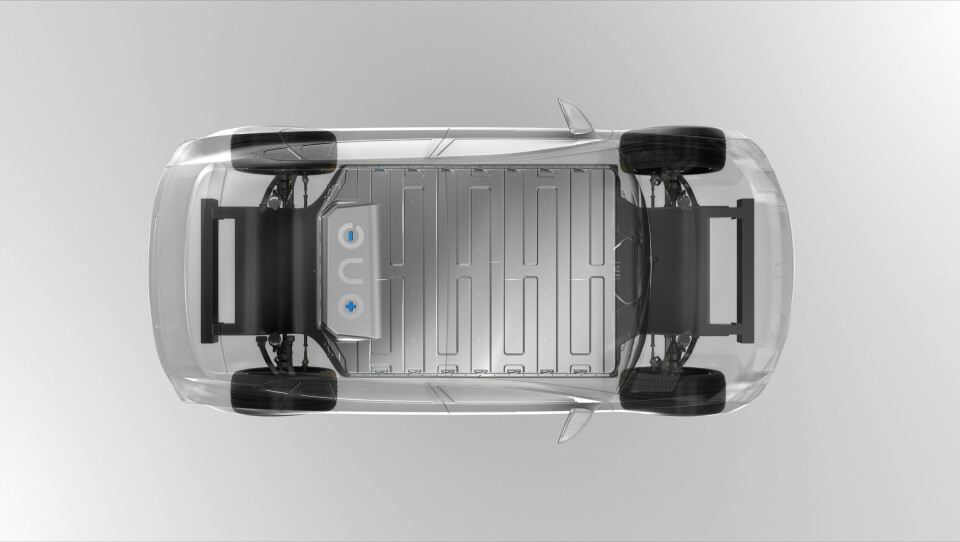
The company’s view is that while it cannot change the science of battery chemistry, it can design for system level density—hence opting for LFP, to remove the oxygen content alluded to earlier, and removing the modules for a cell-to-pack arrangement.
“With cell-to-pack, we eliminate the module and other interior hardware, and use the pack to compress, hold, and manage all the structure,” explains Ijaz, likening the battery structure to the honeycomb design of an aircraft wing. “This increases the density of power storage inside the pack for the same volume.”
Optimising weight and cost in battery enclosures
Enclosures significantly impact the weight of the complete battery pack, typically accounting for around 18% of the battery mass, notes Ijaz. “The rest made up of the enclosure, including the cover, cooling, and module mounting.” Battery electronics account for only a small proportion of battery mass, he adds.
For cost reasons, ONE prefers aluminium over composites such as carbon fibre. “We’re working to lighten the materials by design. Considerable engineering goes into halving the current enclosure weight, and aluminium is the best material for the balance of strength versus weight and cost. Composites also have recyclability challenges, and don’t add sufficient value.”
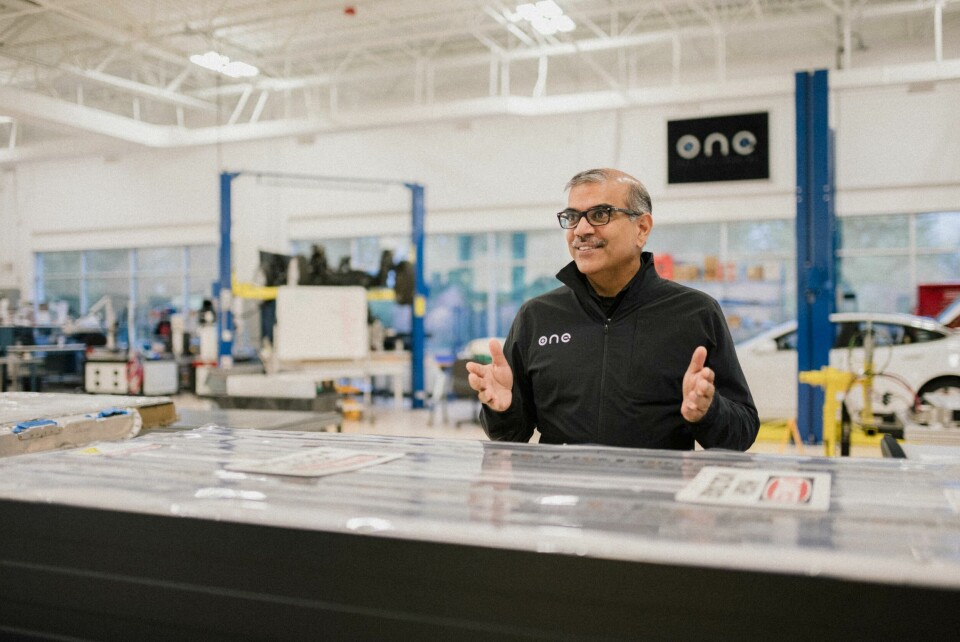
Although acknowledging the advantages of thermoplastics in terms of moulding and its insulating properties, Ijaz harbours reservations about weight and cost. “The two things we want are lighter materials, and less material. We’re trying to drive the weight of the aluminium out, and the cost of the enclosure down. Using thinner and less aluminium is an equally good way to achieve cost reduction,” he says.
A simple and straightforward approach battery lifecycles
Ijaz describes ONE’s cell-to-pack assembly as a simple three-step process: “To our enclosure we add all the cells, which we bond together, then add the busbar and electronics. By going busbar to busbar, we’ve eliminated all the costly connectors and high voltage wiring, which in turn cuts weight and volume. And we’ve taken a different approach to securing the cells, by bonding, welding, and compressing the cell groupings. And in the manufacturing process, the enclosure surrounds our cell groupings, permanently integrating them.”
All this is done on what Ijaz describes as, “a very simple, straightforward, 3GWh line in 5,000 sq-ft space. It’s a very dense, very compact, very straightforward way to build battery packs.”
He talks about three key topics in battery manufacturing, namely thermal runaway, range anxiety, and sustainability. Having touched on manufacturing and range, we turn to sustainability, which spans everything from the design stage through to repairability and end of life handling.
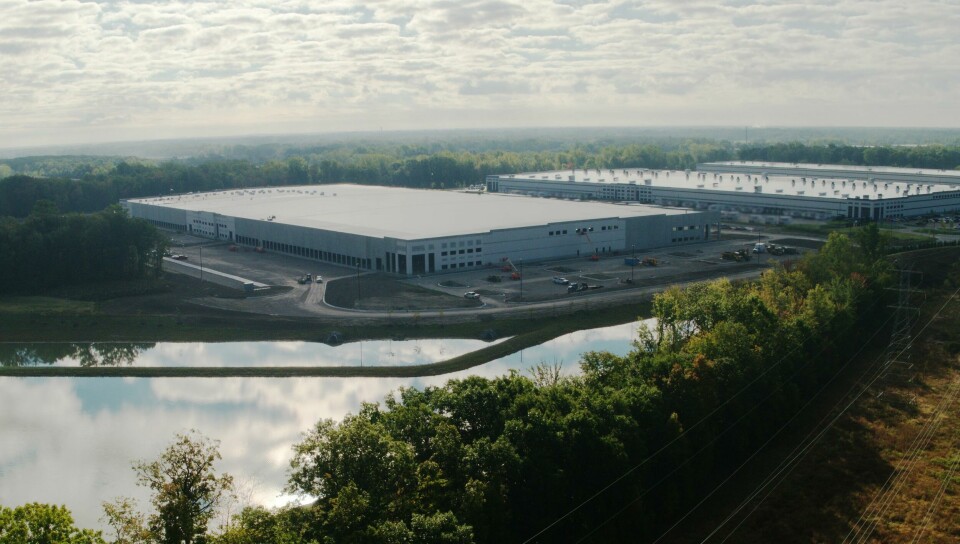
“We’ve analysed millions of electric vehicle miles, in terms of reliability and durability in different product segments,” says Ijaz, “and the electronics represent the greatest risk in a lithium-ion battery, not the cells. The cell itself is durable, so we make sure the electronics are replaceable. We integrate the cells permanently, and make sure that at end of life, lithium and other valuable materials can be extracted through recycling.”
The journey to a denser, safer EV battery chemistry
How can a small US battery supplier ramping up to full production stand out from the major Asian battery suppliers? “We see ourselves as a system supplier, not a cell supplier,” explains Ijaz. “By optimising the system, rather than the component, we constrain mass while still delivering function. This creates the best opportunity for reducing cost, and it’s what makes our approach different.”
Ijaz says he draws inspiration from Henry Ford: to reduce cost, you reduce mass. Furthermore, reducing cell density not only creates the opportunity to increase pack efficiency, but also improve safety.
“Switching to LFP resulted in a less dense battery by cell chemistry, so we had to further improve the density by mechanical design, making the pack more efficient,” concludes Ijaz. “We’re at 92% by mass of cell in our batteries, while a typical battery is 80%. And we’re at 76% by volume, where it’s typically 50%. We’ve taken a different approach to how to make a denser, safer chemistry, and that’s how we’re manufacturing out the risk of thermal runaway.”