Flexible production logistics
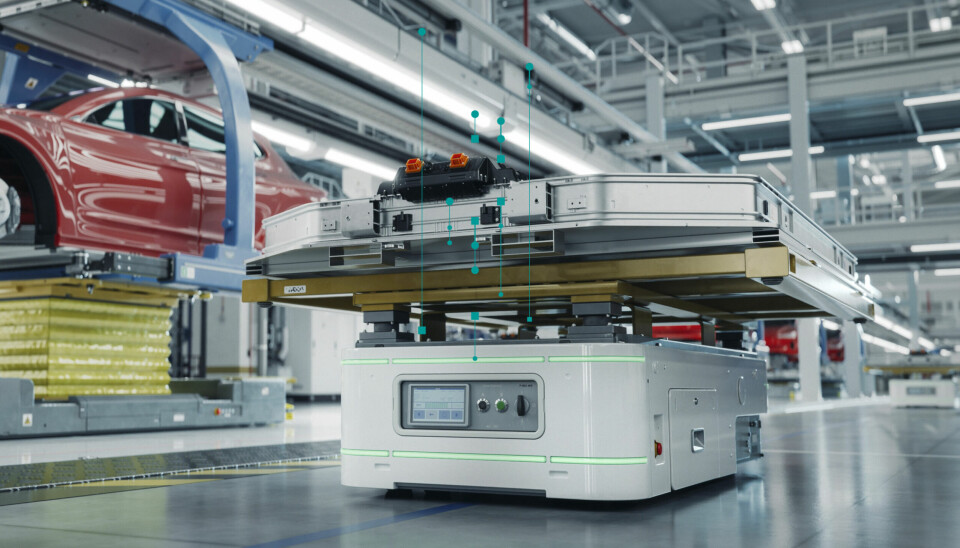
How smart material transportation can support flexibility in automotive production operations
As the automotive industry faces multiple economic and geopolitical challenges, impacting costs, market demand and supply chains, developing agile, flexible production lines becomes a necessity.
Siemen’s white paper: Material Transportation for Automotive: Maximising your production flexibility, outlines how smart logistics systems can support the optimisation of production flows, improving efficiency and flexibility.
AMR/AGV planning and simulation
As manufacturing demands intensify with higher product variance, leaner operations, and faster cycle times, digital planning becomes essential to ensuring flexible, efficient, and cost-effective logistics. Supporting this, Siemens says its advanced Autonomous Mobile Robots / Automated Guided Vehicles (AMR/AGV) planning and simulation tools can transform material transportation in automotive applications.
A prime application is the optimisation of material flow in bodyshop and assembly lines. With increasing reliance on AMRs and AGVs for just-in-time delivery, planning their routes, loads, and availability is critical. Siemens enables virtual simulation of fleet operations – allowing manufacturers to evaluate layouts, workloads, and real-time system responses before equipment is installed.
Challenges and solutions
Traditional manual planning methods are time-consuming and struggle with the complexity of mixed fleets and diverse manufacturing workflows. Disconnected systems between simulation tools and real-world fleet managers further limit efficiency. As the number of AMRs and AGVs grows, so does the need for precise coordination, space optimisation, and traffic control.
Siemens addresses these pain points through digital twin technology and intelligent fleet management. By combining virtual models with real-time fleet data, manufacturers can simulate production scenarios, identify bottlenecks, and adjust operations proactively. Standardised interfaces connect planning tools directly to fleet control systems, enabling seamless transitions from virtual design to real-world execution.
Key value points:
30% reduction in planning effort and 25-33% fewer production delays compared to manual methods.
Increased trips completed on time (+25-30%), leading to better on-floor synchronisation.
Higher production capacity and flexibility, with minimised shop floor disruptions.
Faster commissioning, as problems are resolved before physical deployment.
Fleet automation and commissioning
Siemens addresses the challenge of deploying diverse AMR/AGV fleets with its Fleet Automation and Commissioning solutions, designed to maximise uptime, reduce cost, and simplify integration.
Modern automotive facilities use a variety of AGVs and AMRs to transport different materials – ranging from small parts in assembly to large body components. Siemens says its solutions enable standardised fleet automation across this heterogeneous environment, ensuring reliable performance and coordination.
Challenges can arise with the integration of multiple AMR/AGV types, leading to fragmented automation architectures, inconsistent diagnostics, and varying maintenance requirements. This complexity increases training needs, raises personnel costs, and requires extensive spare part inventories to avoid operational interruptions.
To manage the integration process Siemens offers a comprehensive platform – Simove – that standardises hardware, software, and control systems across fleet types. It includes open controllers, sensors, and modular interfaces from Siemens’ automation portfolio. Siemens says this unified approach allows for easier system scaling, reduced integration time, and simplified maintenance.
By reducing complexity and boosting standardisation, Siemens says its Simove solution enables manufacturers to scale their automation quickly while maintaining high levels of efficiency and flexibility. The company also notes that this platform can deliver up to 20% increase in fleet availability, lower maintenance costs and reduced spare parts spending as well as enhanced productivity and system reliability.
Fleet integration
Seamless integration between AMR/AGVs and automated production cells is crucial for operational efficiency. Siemens says its Fleet Integration solution bridges this gap by standardising communication, automation, and fleet control across diverse systems.
A key application is the automated interaction between AGVs and robotic cells for tasks like loading and unloading trolleys. These systems must function safely and efficiently together, requiring consistent communication between the fleet, robotic stations, and systems like the Manufacturing Execution System (MES).
As mentioned earlier, many manufacturers face fragmented automation environments, with different AGV/AMR vendors, protocols, and interfaces. This lack of standardisation leads to inefficiencies, increased commissioning time, manual interventions, and operational risks.
Siemens addresses these issues through unified automation architectures. These harmonise production and transport systems, and standardised automation and communication protocols. This enhances interoperability with advanced fleet control systems that use intelligent algorithms for reliable coordination between all automated elements.
By implementing open and standardised APIs, Siemens says this allows for future upgrades or integrations without overhauling systems.
Key value points:
Up to 20% increase in productivity due to better coordination between fleets and production cells.
Improved safety by reducing manual interactions and standardising operations.
Enhanced flexibility to adapt quickly to new production demands or configurations.
Fleet orchestration
Effective traffic control is vital in automotive factories where multiple types of AGVs and AMRs must coexist. Without a unified control system, facilities suffer from non-standard communication protocols, siloed traffic managers, and inefficient routing – all leading to bottlenecks, longer commissioning times, and reduced productivity. Legacy systems also hinder scalability and adaptation to changing production volumes.
Siemens says its Fleet Orchestration solution provides the critical intelligence to harmonise traffic, avoid congestion, and ensure seamless material flow.
In a typical application, a manufacturing facility using different AGVs – from forklifts to small-part carriers – needs to coordinate their movement across shared shop floors and varied production areas like the bodyshop, final assembly and paintshop. Each AGV type is often from a different vendor, adding complexity to fleet-wide management.
Siemens tackles these issues with a holistic traffic management system that features a unified fleet control system, which manages all AMRs/AGVs, regardless of manufacturer, through open, modular interfaces. There are standardised communication protocols to ensure consistency across the fleet for reliable data flow and command execution. The system also offers advanced routing and scheduling algorithms that optimise material movement, reduce delays, and increase overall throughput.
Key value points:
+30% increase in trips completed on time.
-30% reduction in planning time.
-25% drop in cumulative delays.
Smooth and scalable integration of new AGV systems.
Lower operational costs and increased production reliability.
Summary
Smart materials handling technology – such as Siemens’ AMR/AGV planning, fleet integration, and orchestration – enables automotive manufacturers to build more agile and flexible production lines in response to rising economic and geopolitical pressures. By digitally simulating and centrally managing transport operations, manufacturers can reduce delays, adapt quickly to shifting demands, and future-proof their operations. The result is a smarter, more responsive manufacturing environment that supports continuous change, higher efficiency, and improved resilience across the entire value chain.