Event preview – Surcar North America: Virtual Summit 2020
Automotive coating experts set the scene as networking opportunities reconvene

The impact of lockdown in 2020 has not only seen automotive production disrupted but also curtailed networking opportunities for industry experts. In response, Surcar North America is planning a virtual summit to ensure a continuation of the knowledge sharing for the paintshop community in the region.
Over consecutive Tuesdays in October, a programme of online sessions will be delivered by OEM experts and representatives from the equipment and material suppliers. As well as speakers presenting their technical papers, question and answer sessions will conclude each afternoon’s programme, allowing wider participation and engagement from the audience.
Surcar committee Q&A
To set the scene for the upcoming Surcar Virtual Summit, AMS spoke to members of the organising committee to hear their views on the latest paintshop developments and the issues that will shape the coatings industry through this period of huge change in automotive manufacturing across the globe.
Tim Hayes – Surcar International President
Kenny White – Director, General Motors Vehicle Systems, Global Paint/GMNA Paint Execution
Nadia Benhamida – Senior Materials Engineer, Hyundai Kia America Technical Center
Setting the scene: Whether it’s process, coatings and/or equipment, what developments in car body finishing are you most encouraged by, excited at, and interested to see grow?
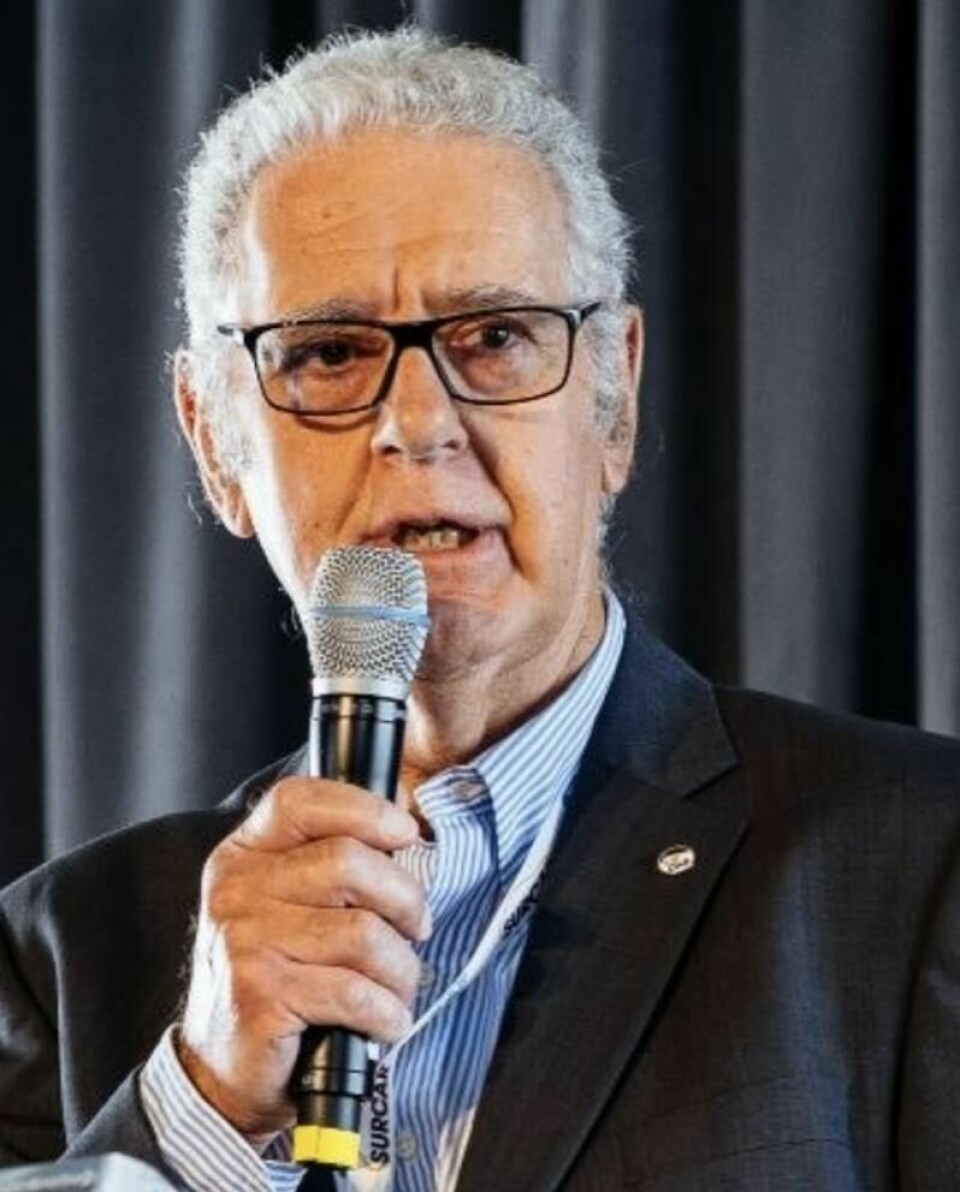
Tim Hayes: The paint process itself is changing, which dictates changes to paint materials and equipment. Today’s paintshops require far more flexibility and economy compared to the traditional paint lines installed throughout the automotive industry. The drivers are clearly different models, with variable production rates, being painted on the same line(s) with extra care being taken on energy, air and material consumption.
Kenny White: I’d like to see a continuation of compact processes that increase first-time quality but decrease process time and investment. Paintshops are a pretty pricey asset and most of them, I would say in the Big Three, are starting to show their age. So when we do get ready to replace the asset, how are you setting up the flow diagrams and what process are you going to use to replace it. One of the bigger challenges that we face, as we continue to rightsize the company, is how we continue to use our assets more and more. So having three-shift and overtime doesn’t allow a lot of time for maintenance. In order to meet production schedules, the summer breaks we used to have to go in and do asset replacement or conditioning, we’re finding less time for that.
Nadia Benhamida: For me, it’s the material improvement. The challenge is how to create a coating that would respond – smart coatings that have functionality other than looking good. For interiors, or the exterior parts that are touched more often. The automotive industry is changing. There is a tendency toward car sharing – using a cars more often than when owned by one person and staying on the parking lot 90% of the time. So having coatings that are anti-microbial, anti-virus, while not so important now, as the car become share rides we will want to see something that means when we get in the car we know it is clean.
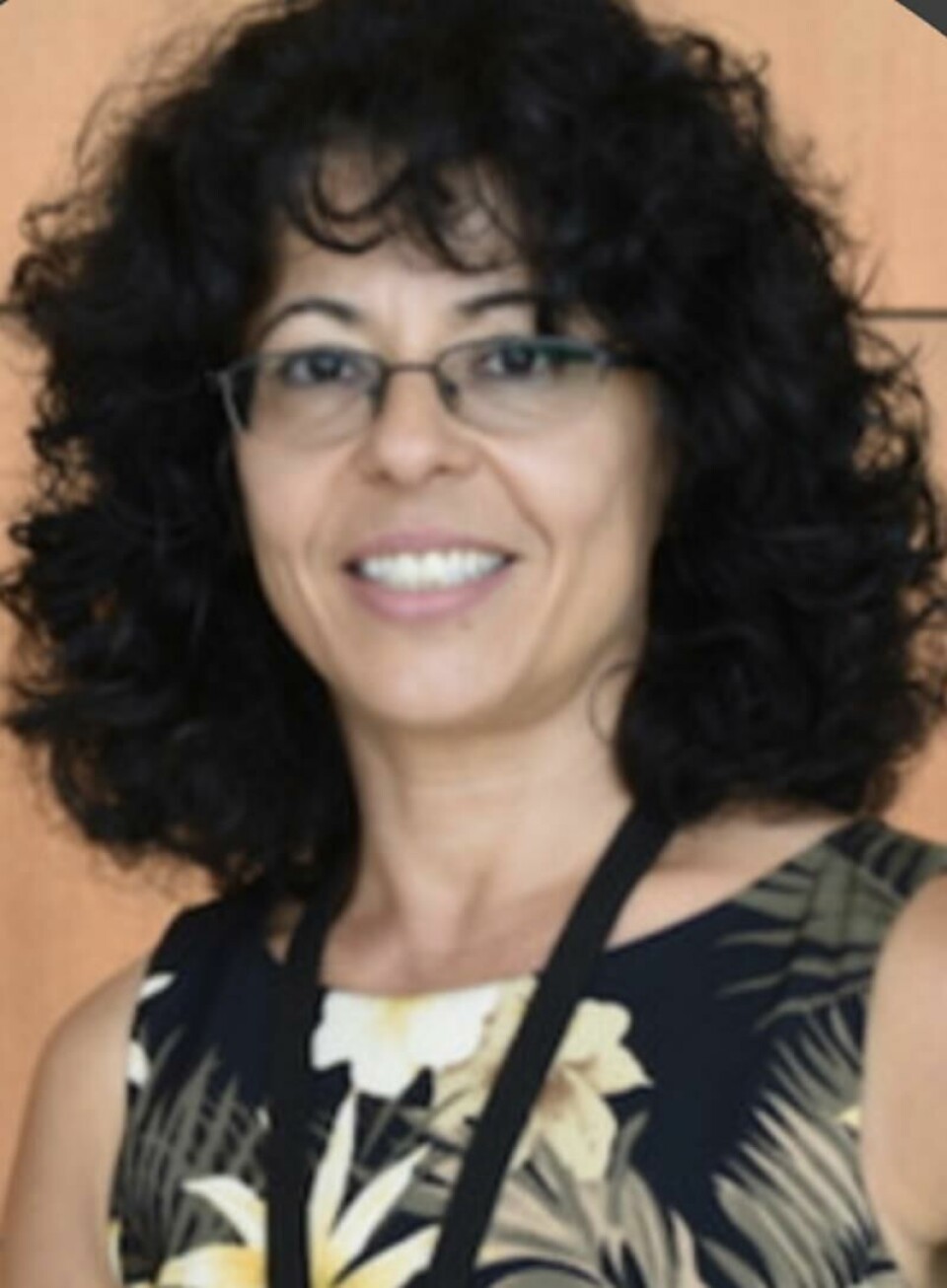
Smart paintshop: What sort of impact is Industry 4.0 or digital manufacturing having in the paintshop?
TH: Vast difference in comparison to even 10 years ago, paintshop management, maintenance cycles, spares availability on time, rapid introduction of new paint materials and again the data allows the paintshop to be used with higher efficiency and added flexibility. Another interesting factor is rapid carry over of production data to ensure production, uptime and reduced commissioning periods in different plants and countries.
KW: I’m anxious to get it. There’s been a lot of discussion on this. I don’t know of anyone who has a paintshop that really ’speaks to you’ - there’s potential but I don’t think anyone has pulled it all together yet. There hasn’t been a leap from 10 years go, but I’d call it continuous improvement with what we have. I look back at the shops we built 10 years ago, and they had some a certain level of first-time quality. We can take those same shops and see incremental improvement in them. I would think the most radical thing on the horizon is how do we combine pre-treatment and e-coat into more of a streamlined, smaller process and footprint, maybe a lower bake opportunity. That’s the big horizon and it’s really going to be material-driven.
NB: I think the materials for coating and the process go hand in hand. In order to improve the material, the understanding of the process is important. We know we are in the fourth industrial revolution, things are changing drastically. The paintshop is changing drastically, with robotisation, with big data analysis: all that information helps to design the coatings of the future. So it’s important for us to understand all that. The material itself is impacted by it. We can’t improve and meet requirements without having that knowledge and looking to future technology.
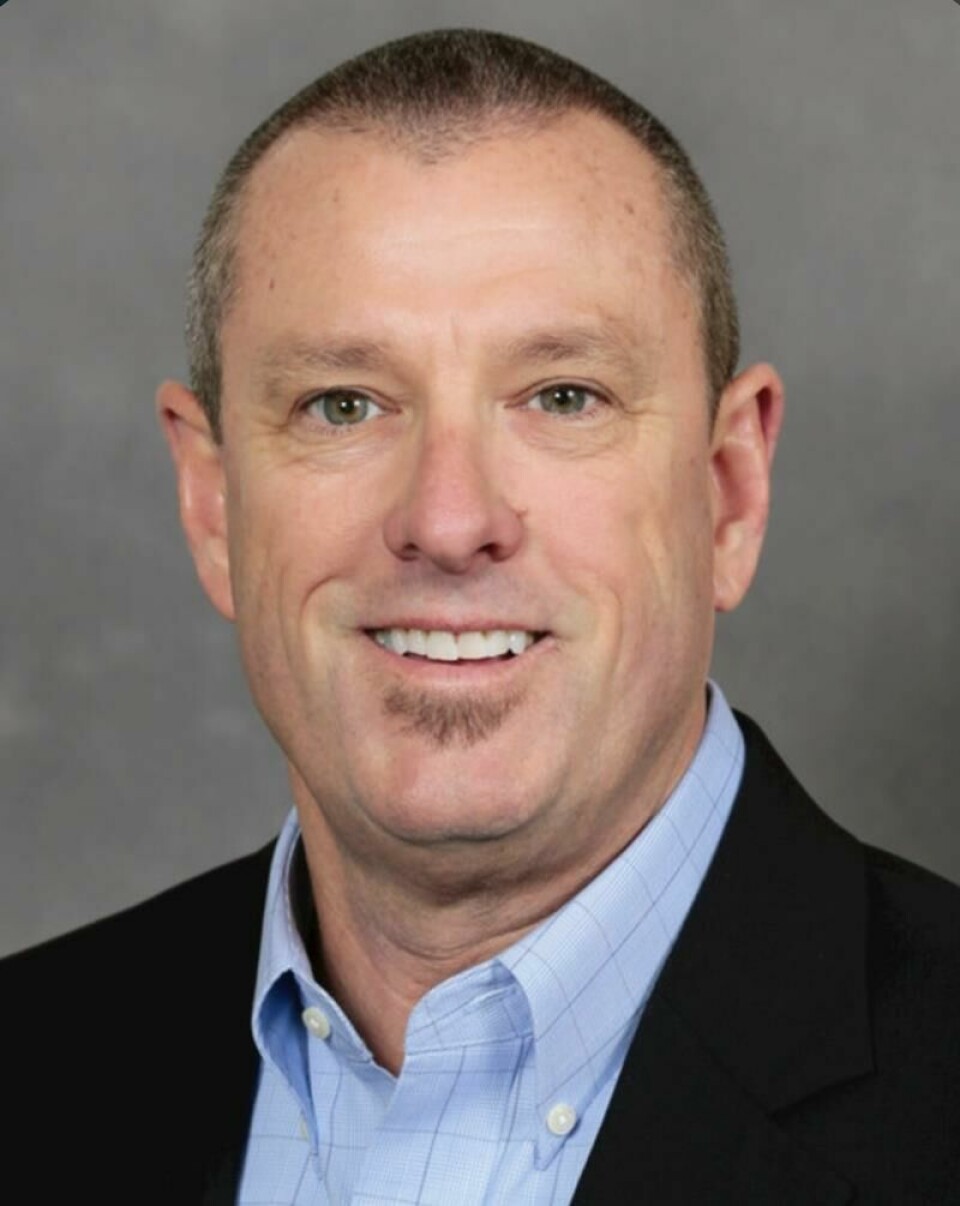
Sustainability, energy and water consumption: What are the sustainability challenges and solutions leading the conversation among the car body finishing community in North America?
TH: In North America, as elsewhere, there is considerable pressure from within the OEMs and from national agencies to reduce the environmental footprint of car assembly plants, especially the paintshops. The solutions are similar, but not always, there is still a competition between high solid paint materials and water-based, accentuated by the introduction of overspray free application and now “printing”. There is a real drive to correct the problem at the source, not just solutions such as solvent abatement, dry scrubbers etc.
KW: I think the move to dry booths and getting rid of waste water and waste-water treatment is moving in the right direction. It’s not easy to retrofit but as new shops are being built that’s definitely the new norm.
NB: How can we give functionality that can target bacteria and at the same time be environmentally – so that we aren’t helping one thing but destroying something else. So far, when you use anti-microbial properties for coating, it can render the microbe more resistance. So to create something that is safe for people, safe for the environment and sustainable. One of the challenges we saw with Covid-19 was the supply chain for different materials for the coating, there were shortages and stoppages. So how to create a product that’s available in the market, with no shortages of material is another challenge.
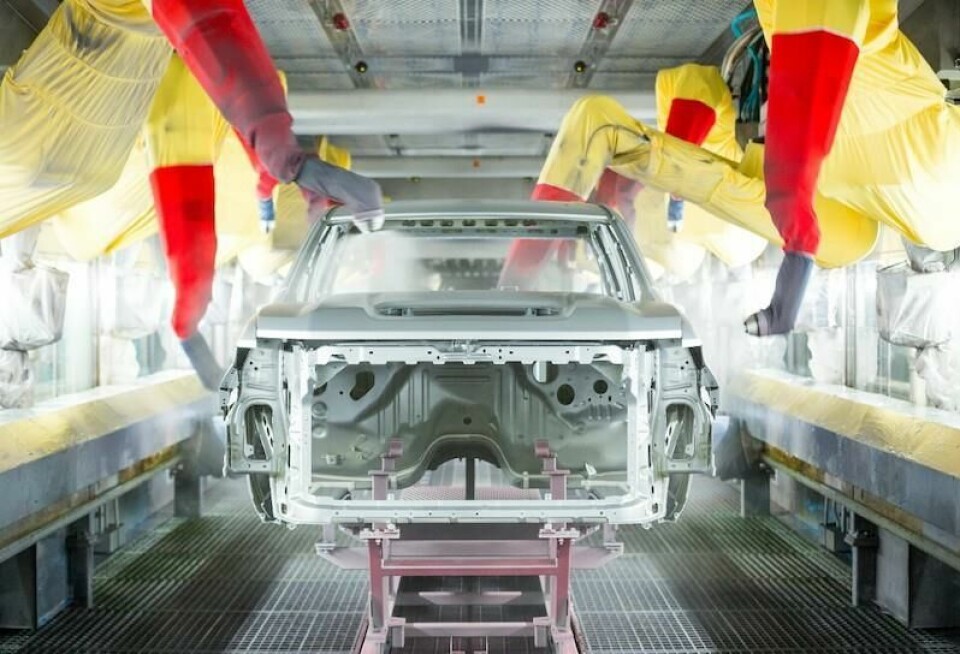
Innovation, regulation and industry challenges are dictating change and improvements within the automotive paintshop process globally
Suppliers: In terms of innovation, how does the relationship between OEMs and suppliers play out? Do OEMs expect integrated solutions from the supplier network or do OEMs take a strong initiative to which suppliers must react?
TH: Good question! It differs between OEMs, some have sizeable and efficient in-house paint engineering structures, others tend to integrate more their major paint material and equipment suppliers during the design, installation and commissioning phase and, yet again, others buy a totally integrated paintshop.
KW: My thought is that there are robotic applicators and there’s several of those to choose from – whether it’s the robot or the applicator. But when it comes to shop design, booths and conveyors, those kinds of things, that’s becoming limited. Not only in North America, but globally. It’s interesting, the dynamics of China are changing, there they are starting to look at a market shift, closing down plants over market capacity. They are seeing the same things we have seen in North America. They were building shop after shop – good shops, and relatively new. But they are not full of wildly new technology – still has a pre-treatment, still has an e-coat. Whether it’s compact process or traditional process, it still goes on with automation, robotic application.
NB: I like to know what’s out there, what do they have. We have roundtable discussions on what we’d like to see happening. It’s not just paint supplier, it’s the robot suppliers, the instrument suppliers. To take it to another level, we look at what’s possible – it’s always teamwork.