Factory Investment
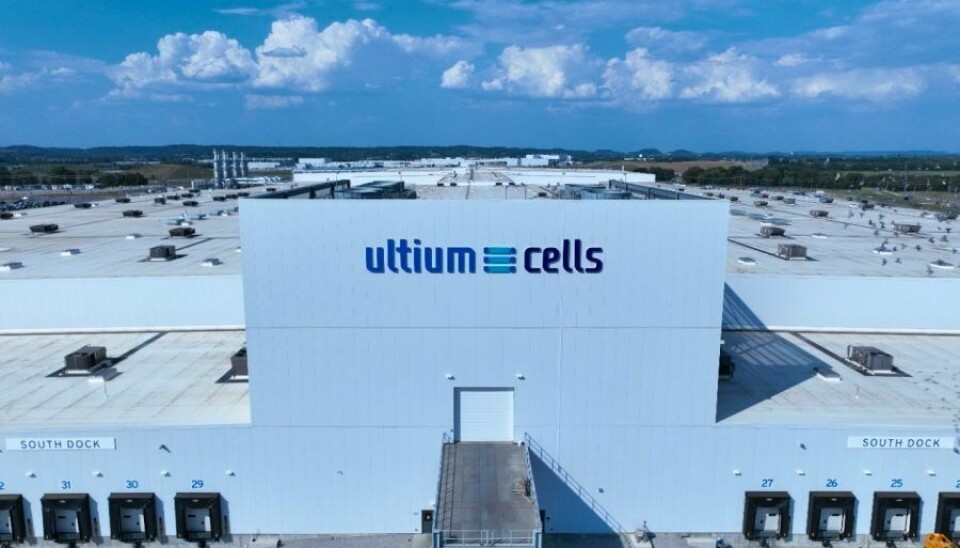
Ultium boosts Spring Hill for next-gen EV battery innovation
Ultium Cells, the GM-LG joint venture, is investing in Spring Hill, Tennessee, to produce low-cost LFP battery cells by 2027, strengthening EV affordability and diversification in the US market.
Ultium Cells LLC, a joint venture between General Motors and LG Energy Solution, is upgrading its battery manufacturing facility in Spring Hill, Tennessee, to produce low-cost lithium iron phosphate (LFP) battery cells. This move builds on the original $2.3 billion investment announced in 2021 and marks a significant step toward scaling affordable electric vehicle (EV) technologies.
Conversion of battery cell lines at the site will begin later this year, with commercial production expected by late 2027.
“At GM, we’re innovating battery technology to deliver the best mix of range, performance, and affordability to our EV customers,” said Kurt Kelty, vice-president of batteries, propulsion, and sustainability at GM.
“This upgrade at Spring Hill will enable us to scale production of lower-cost LFP cell technologies in the US, complementing our high-nickel and future lithium manganese rich solutions and further diversifying our growing EV portfolio.”
Scaling for cost and choice
General Motors’ Ultium platform is designed for flexibility, supporting multiple battery chemistries and form factors. The Ultium Cells plant in Warren, Ohio, will continue producing cells using nickel cobalt manganese aluminium chemistry, which has enabled GM to deliver vehicles with ranges exceeding 300 miles per charge.
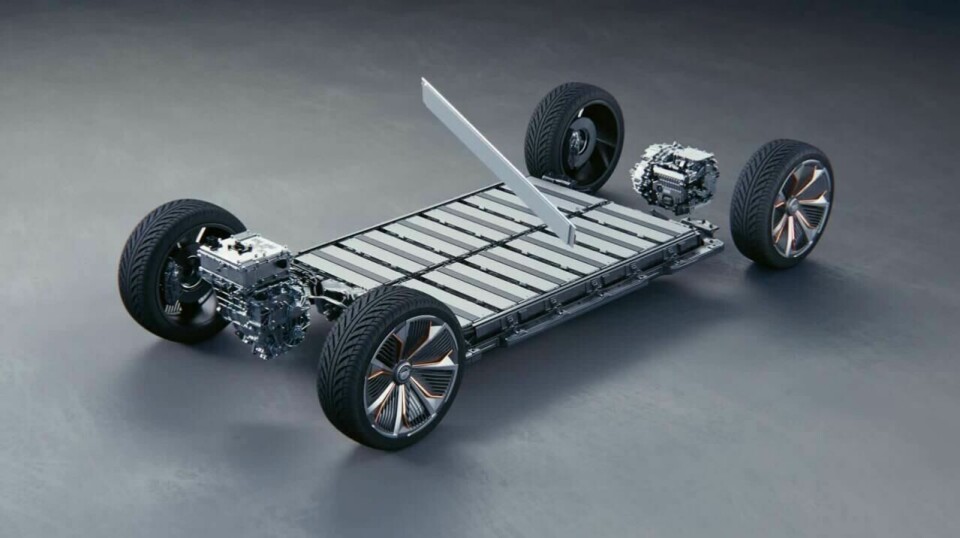
With the introduction of LFP cells, GM aims to reduce battery pack costs while broadening consumer options in the EV segment.
“The upgrade reflects the continued strength of our partnership with General Motors and our shared commitment to advancing EV battery innovation,” said Wonjoon Suh, executive vice-president and head of the Advanced Automotive Battery division at LG Energy Solution.
“We will bring our extensive experience and expertise in US manufacturing to the joint venture facility, further accelerating our efforts to deliver new chemistries and form factors that effectively capture the unmet needs in the EV market.”
The regional impacts of this latest Ultium investment and future outlook
The Spring Hill site currently employs around 1,300 people and will play a pivotal role in supporting US battery innovation and manufacturing leadership. The ability to manufacture multiple cell chemistries at one location is expected to give Ultium Cells an edge in a competitive market.
“Ultium Cells’ additional investment and commitment to innovating and enhancing its Spring Hill operations is a testament to the state’s longstanding, cohesive partnerships, which started with General Motors, and grew to include LG Energy Solution in 2021, and we stand ready to continue supporting these companies and their joint venture for years to come,” said Stuart C. McWhorter, commissioner of the Tennessee Department of Economic and Community Development.
“This investment expands our capabilities beyond a single battery cell chemistry, allowing us to produce new chemistries alongside our existing cells.
Kee Eun, president, CEO of Ultium Cells,
Kee Eun, president and CEO of Ultium Cells, added: “We are grateful for the continued partnership and support we've received from the State of Tennessee as we continue to advance our lead in EV battery cell manufacturing.
“This investment expands our capabilities beyond a single battery cell chemistry, allowing us to produce new chemistries alongside our existing cells. Expanding our product portfolio ensures Ultium Cells will remain at the forefront of battery cell innovation and sustain our commitment to be a stable, long-term employer for the communities we serve.”
Analysis: Strategic Implications of Ultium's LFP Shift
Ultium Cells' pivot to Lithium Iron Phosphate (LFP) battery production at its Spring Hill facility by 2027 represents a calculated move with significant implications for the EV market. This isn't merely an incremental upgrade but signals a material shift in GM and LG Energy Solution's approach to EV affordability, market diversification, and supply chain resilience.
The embrace of LFP technology directly addresses the persistent challenge of EV sticker price, often cited as a major barrier to widespread adoption. LFP batteries are inherently less expensive to produce due to their reliance on more abundant and less costly materials like iron and phosphate, compared to the nickel and cobalt used in higher-nickel chemistries.
By integrating LFP into their portfolio, Ultium is poised to enable GM to introduce more competitively priced EV models, potentially opening up the EV market to a broader demographic and accelerating the transition away from internal combustion engines.
This diversification means GM can offer vehicles tailored to different consumer needs and budgets, from long-range performance EVs using nickel-based batteries to more affordable options powered by LFP.
Supply chain security and disruption mitigation
Beyond cost, the move to LFP also bolsters supply chain security. The reliance on nickel and cobalt for high-performance batteries has exposed automakers to price volatility and geopolitical risks associated with their concentrated mining regions. LFP's material composition offers a more stable and geographically diversified supply chain, reducing dependency on specific critical minerals. This foresight not only mitigates potential disruptions but also contributes to the long-term sustainability and predictability of EV production.
Finally, this investment points to an increasing commitment to domestic manufacturing and innovation, that is ‘localisation’. By producing LFP cells in Spring Hill, Ultium Cells is both creating jobs and strengthening the US's position in advanced battery technology. The ability to produce multiple battery chemistries under one roof provides Ultium with a distinct competitive advantage, allowing for greater flexibility in responding to market demands and technological advancements.