Future perfect for GM in South Africa
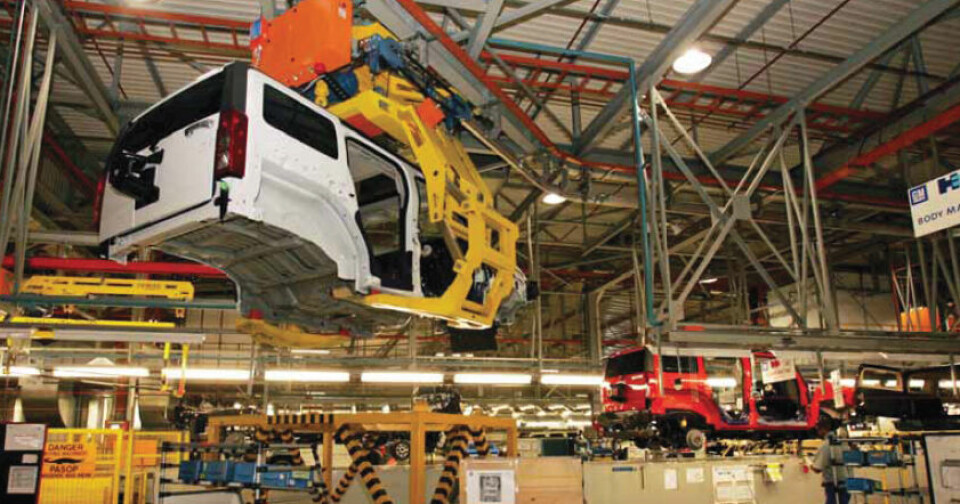
Despite fluctuating demand, high inflation and volatile currencies, General Motors South Africa is optimistic about future prospects
Before being appointed Vice-President of Manufacturing for General Motors South Africa, Rick Demuynck was head of the company’s plant in Shreveport, Louisiana, home of the Hummer H3, among other vehicles. A GM employee for 24 years, Demuynck has run the Struandale and Kempston Road plants in the Eastern Cape since January 2008. The plants build, respectively, the CKD H3 and its derivatives and Isuzu truck and Opel Corsa models.
While some observers would assume there to be a striking contrast between Port Elizabeth, home of GM’s two South African plants, and Shreveport, Louisiana, in America, Demuynck maintains that the differences are “not as much as you’d think”.
“The original plant in Kempston Road dates back to the 1920s and it used to be a full assembly plant with a paintshop,” he says. “This was right up until the capacity was not needed and the cost of upgrading just wasn’t worth it. We bought the Struandale facility in the 1990s. That facility has a paintshop and is capable of handling the capacity of what we assemble at both plants. The reason for the two sites is that we grew into the second location. The opportunity came up to take over Struandale and the decision was made to buy that plant from Ford.” (Ford South Africa still has an engine production facility in Struandale).
“If we were designing our production facilities now, we’d obviously design them so that everything was under one roof, but we were taking full advantage of the existing assets. We’re currently operating at about 60 per cent of capacity. Full capacity would be about 90,000 units per annum. Our single paintshop at Struandale really links the two plants. In fact, we think of one plant as an extension of the other – we leverage our resources across the two, including workers, both hourly and salaried.”
Different plants, similar challenges
Despite differences in population, Shreveport being a relatively small town of 50,000 people and Port Elizabeth a coastal city of 1.5m inhabitants, Demuynck notes that the two have a similar pace of life. Neither bear any similarity to the plants where he worked previously in the metropolitan areas of the eastern US. As such, the experience of having run GM’s operations in Louisiana, which provides the H3 kits for the Struandale operation, has been a major boon. But GMSA’s assembly operations rely on other GM plants, not just the Hummer operation in Louisiana.
“All our vehicles are CKD. We receive materials from Brazil, Thailand and the US,” says Demuynck. “From a logistics point of view that might seem a complex arrangement, but from a manufacturing standpoint, and this is my first time working in a CKD plant, it’s a straightforward operation. Once the material is on board, there’s really no difference. It’s not like we’re receiving builtup modules; it’s really just the sourcing of the parts.” As with any emerging market, and particularly one that features such highs and lows in vehicle sales, as has happened in South Africa over the past 18 to 24 months, it’s difficult for OEMs and suppliers to make large-scale investment plans. “Right now the supply base, which we’re trying to grow, is in its infancy. It’s one of the keys to growing manufacturing for all the OEMs in South Africa, developing a more robust supply base,” he says. “So it’s out of necessity that we get the CKD material from the base plants across the globe. But ideally, we’d really like to source as much from South Africa as we can.”

South Africa’s Motor Industry Development Programme (MIDP) is set to continue, with a new motor-industry policy due in 2020, the country’s Department of Trade and Industry (DTI) announced in December 2007.
The DTI had been reviewing the MIDP since 2005, and missed several deadlines for reporting to Parliament. The provisional outlines were then to be considered, with a full report due in August 2008. This was fi nally delivered in September. While OEMs and Tier Ones awaited the DTI’s recommendations, investment decisions had been held up by a prolonged assessment process.
In the initial outline of the revised MIDP, the DTI stated that the government intended to keep subsidies as a central pillar of its plans for the industry. Indeed, this seems to have been a successful strategy with one of the aims – greater economies of scale – being attained thanks to four vehicle models presently being manufactured in volumes greater than 40,000 units per annum.
The MIDP may well have helped bring more carmakers into South Africa, but the downside remains high vehicle prices and relatively low levels of employment in the industry. The fl ow of incentives will continue as a way of tackling the last of these challenges, in particular, with tariffs to be maintained as a way of encouraging more SKD and CKD assembly, as well as full manufacturing.
The South African government has publicly stated that it wants to see the industry manufacturing 1.2 million vehicles a year by 2020. The APDP, delivered in September 2008, was a revision of the MIDP and has four main components:
- Tariffs – stable and moderate tariffs will remain at 25 per cent for light motor vehicles and 20 per cent for components from 2012.
- Local Assembly Allowance – this will be in the form of duty credits issued to vehicle assemblers based on 20 per cent of the value of light motor vehicles produced domestically from 2013.
- Production incentives – this support of 50 to 55 per cent of value added, computed in simple terms as sales less raw materials, in the form of a duty rebate credit, will replace the current export based scheme in 2013.
- Automotive Investment Allowance – assistance that, from 2009, will replace the Productive Asset Allowance and will be 20 per cent of qualifying investment paid to participants over a three-year period.
Sourcing local suppliers
To that end, GMSA and its competitors continue to work with local suppliers and the South African operations of major Tier One companies to improve localisation rates. “We do have some local suppliers. I would call it a developing supply base but it’s really a chicken and egg situation. To grow the industry, you want to have a strong supply base, but to grow the supply base, you need to have greater volumes, more product coming in. It’s balance, but I think from the government’s industry programme, as well as an OEM point of view, we all have the same objective: to make the manufacturing and assembly footprint much bigger in the medium and longer term. “The suppliers we do have are mostly tyre manufacturers – Goodyear, for example – and glass producers. Also battery suppliers and other similar companies. Some are international operations and some have local sites. Just down the road from one of our sites is the Continental plant that supplies us.”
As well as the ongoing issue of inflation, which continues to play havoc with consumer spending decisions and wage demands for all OEMs operating in the South African market, another concern is the volatility of the country’s currency. This alone underlines the need for more local Tier One and Two operations.
“When you’re bringing your material in from Brazil, as the real strengthens and the rand weakens, it’s hurting us. As far as having a more stable environment, that just adds to the need that GM sees for a stronger local supply base.” Such exposure to a volatile local currency and other overseas currencies, such as the dollar, that have recently suffered a roller coaster ride in value, must surely be causing GMSA’s management sleepless nights.
“No, I don’t see that as a major problem,” says Demuynck. “We have had a good year in a falling market, with our market share rising throughout 2008. I think the way GM in Detroit looks at it is that markets are often cyclical. We were booming two years ago and now we are towards the bottom end of a cycle that will come back up. What GM wants to see is how we perform in a down market and how we take the best advantage of a market that’s recovering.”
As part of ongoing investment in the local market, GM has recently opened a 31-hectare Vehicle Conversion, Storage and Distribution Centre (VCDC). The new complex, equivalent to the size of 60 rugby fields, cost approximately 150m rand (US$16.6m) and provides storage space for 8,500 vehicles.
The new complex centralises many operations, such as vehicle workshops, conversion facilities, pre-delivery activities, upfitment and distribution of local and imported units. All preparation and servicing of company fleet vehicles is also now carried out at this location.
The storage facility can accommodate 6,500 passenger and light commercial vehicles and 500 trucks. The VCDC has 1,500 in-process staging bays, while each parking space is marked and ‘bar coded’ for scanning to reveal a vehicle’s location. Vehicles from GM operations across the globe typically land within hours or days of each other, resulting in up to 2,500 cars and trucks arriving at the storage yard over a three- to five-day period.
“We are now able to deliver vehicles to our dealers in a shorter time frame than before,” says Evan Dold, GMSA’s Vice-President for the Global Purchasing and Supply Chain Division. “This is made possible by a number of process enhancements, including a unique IT-driven process for managing vehicle placements and movements, improved productivity in the new facility for upgrading imported cars and shortened lead times through our state-of-the-art paint repair shop.”
In a bid for even greater efficiencies and cost savings, the company has had a new railway siding built. This private siding, which consists of three sets of tracks connecting to a spur from the main electrified railway line, permits direct loading of vehicles for easy rail transportation.
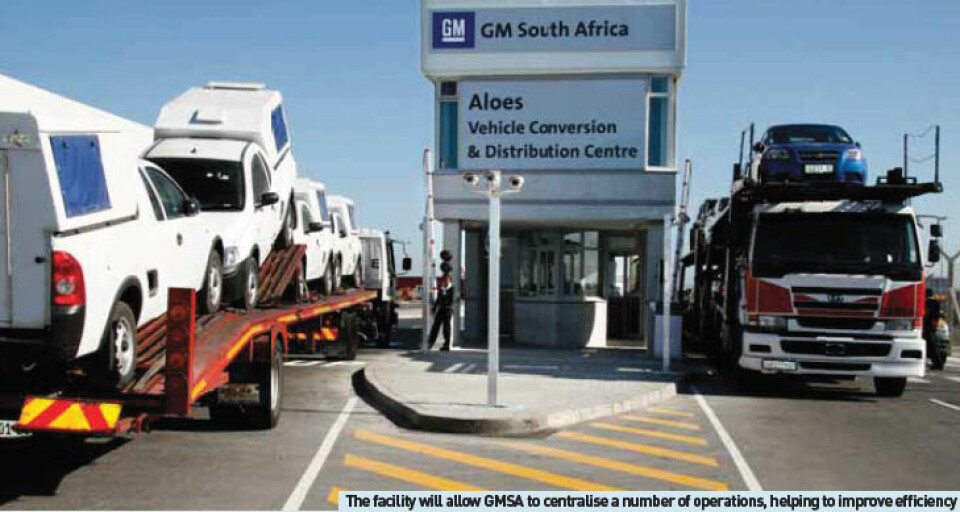
Taking advantage of export markets
Demuynck’s view is that the future of GMSA’s operations in Port Elizabeth does not necessarily depend so much on the ups and downs of the South African market. “Export vehicles are giving us something of a cushion. Currently, the only product that we export is the Hummer H3. It’s a premium vehicle, though it’s lower volume than our Opel and Isuzu products. If you take it across the portfolio of the vehicles we manufacture, it’s not that large, numbers wise, but a weak rand can help us in some of our export markets for that vehicle. Left-hand drive export markets in the Middle East are our major customers, so in this case we have been fortunate, and GM’s operations there are seeing a lot of growth.
“Russia is becoming an interesting market for us too. We also export to Japan, Australia, and both Eastern and Western Europe, but the growing purchasing power of consumers in Russia is great news for us. We don’t have competition from Shreveport – General Motors makes sure that certain markets are targeted by America and we look after the others. If there was ever a massive swing in demand, we certainly have the capacity and capability to help each other out, but the way it’s structured now, there is no need and we’re not looking to work that way.” Another question mark for South Africa, undeniably the region’s economic powerhouse, is how a country that is still not one full generation away from the upheaval brought about by the end of apartheid – and the legacy of that era – still lacks the educational infrastructure for its inhabitants. It is a challenge that the country still has to address, though Demuynck has had experience with sourcing labour in a similar situation.

“The pool of talent in South Africa is comparable with that available in some parts of the US where I’ve run plants,” he says. “In some areas, there’s certainly a skills gap. I don’t think it’s a capability gap, it’s a level of training. If you look at the automation and the level of complexity of the operations at Struandale and Kempston Road, and compare those CKD operations producing between 50,000 and 70,000upa to those of a plant that’s producing 275,000 to 300,000, there are different levels of technology there. The amount of training and the skills that the average worker is going to have is bound to be different. I don’t think there’s any less capability in the workforce here than there is anywhere else.”
Catering for the local market
Many of the vehicles assembled by GMSA are localised versions of models from overseas operations. For example, the Hummer H3 features a right-hand drive conversion, while the small pickup is a type particularly popular with local buyers.
“We’ve been producing the 4303 (Opel Corsa Utility) for a while now, so we’ll eventually see some replacement activity for that model, but the Corsa is still fresh for us,” says Demuynck. “The same applies to the Hummer – it’s just a couple of years into its lifespan here. We’re working on adding a diesel next year, as well as a V8 version. “In our commercial truck operations, we’ll be bringing on several new products in the next few months. We recently launched a heavy-duty version of one of the Isuzu models. This is a profitable market to be in. The brand has a very good reputation as a workhorse truck in South Africa, so we’re confident that we have the right products for when the market recovers again.”
While the truck and LCV market tends to be very sensitive to the recent ups and downs in global and local fuel prices, the issue of alternative fuels, while only in its infancy, is certainly one to watch for the future. In October, GMSA launched the (imported) Hummer H2 with an E85 flex-fuel engine. “Different to where I came from in America, diesel has a strong following in our product lines, in addition to our petrol models. Buyer preference seems to vary with the cost of fuel, but we’re certainly looking to keep broadening our range of engines to meet that demand.”
GMSA is easily the largest division within General Motors Africa Operations (GMAO). The regional grouping sees up to six brands sold in 30 African countries, with a dealer network comprising only 200 outlets. GMAO has tripled its sales since 2002 and has fi ve manufacturing facilities (South Africa, Egypt, Kenya, Tunisia and Nigeria) and a workforce of approximately 5,000 building Chevrolet, Hummer and Isuzu vehicles.
The South African market totalled a record 612,707 new vehicles in 2007, with GM taking a 13.9 per cent share (six months to June 30, 2008). With sales doubling between 2003 and 2006, the period was also marked by the start of left-hand drive Hummer H3 assembly. Right-hand drive models were added in 2007 and both vehicles come down the same line.
GMSA has a workforce of about 3,500 in Port Elizabeth, a city of approximately 1.5m, and is one of the largest private-sector fi rms in the region. In addition, about 1,200 direct and indirect suppliers make up the company’s supplier base. The city’s location, midway between Cape Town to the south-west and Durban to the north-east, gives GMSA two further ports for shipping exports.
History
Chevrolet vehicles were fi rst imported into South Africa in 1913, with assembly operations starting in 1926. The current Kempston Road assembly plant in Port Elizabeth became a manufacturing facility in 1948. An engine manufacturing facility was added in 1965.
GM disinvested to comply with American economic sanctions in 1987, relinquishing operation to Delta Motor Corporation, a local management group that continued to market GM vehicles.
As for supplier operations, Precision Exhaust Systems was set up in 1993, with catalytic converters manufactured locally and shipped to Opel plants in Europe. Another GM subsidiary, Delphi Automotive Systems, became a separate, independent publicly-held corporation in May 1999.
December 2008 marks the 11th anniversary of GM’s return to South Africa after the investment boycott of the apartheid years (the company had pulled out in 1987). GM came back by taking a 49 per cent share in Delta Motor Corporation, buying out the remaining 51 per cent in January 2004. Since then, the company has been known as General Motors South Africa.
GMSA’s head offi ce is at Kempston Road, Port Elizabeth, also the site of one its two plants in the city. Product engineering is based there, as is assembly of the Isuzu N- and F-Series and Isuzu TF KB, as well as the Opel Corsa Lite and Corsa Utility. The Struandale plant, meanwhile, makes the Hummer H3 from kits supplied by GM’s manufacturing complex in Shreveport, Louisiana. Some 3,500 employees work for GMSA.
Products marketed by GMSA
Chevrolet Spark, Aveo Hatch, Aveo Sedan, Optra, Lumina SS Sedan, Lumina SS
UTE, Captiva
Isuzu KB Single Cab Petrol, KB Double Cab Petrol, KB Single Cab Diesel, KB Double Cab Diesel, Extended Cab, Isuzu N Series Trucks, Isuzu F Series Trucks
Opel Corsa Lite, Corsa Utility, Corsa Combo, Tigra TwinTop, Astra, Astra TwinTop, Media, Zafi ra, Vivaro, Movano
Saab 9-3 sedan, 9-3 convertible, 9-3 Sport Combi, 9-5 sedan
Cadillac BLS, SRX, STS
Hummer H3
Products produced in South Africa
Hummer H3 right- and left-hand drive
Isuzu KB Single and Double Cab Petrol, KB Single and Double Cab Diesel, N-Series Trucks, Isuzu F-Series Trucks
Opel Corsa Lite, Corsa Utility
Exported components
Catalytic converters, fl exible couplings, aluminium heat shields, exhaust tailpipe tips, airconditioning components, car jacks, door latches, electronic control systems, leather products, and metal stampings.
Component export markets
Europe, North America, Australia, Chile, Egypt, Mexico, and India
Export markets for Isuzu
Zimbabwe, Zambia, Malawi, Mauritius, Mozambique and Kenya
Export markets for Hummer
Middle East, Europe, Australia, New Zealand, Japan and Israel
BMW (Rosslyn, Pretoria) 3 Series replacement expected in 2013
Mercedes-Benz (East London) C-Class replacement expected in 2012
Ford (Pretoria) Focus replacement expected in 2011 Pickup expected in 2011
General Motors (Port Elizabeth) Chevrolet Montana expected in 2009/2010 H3 successor expected in 2011 Isuzu Rodeo/KB expected in 2013
Renault-Nissan Alliance (Rosslyn, Pretoria) Renault Sandero expected in 2009
Toyota (Durban) Hilux Vigo replacement expected in 2011 Avanza replacement expected in 2012 Fortuner replacement expected in 2013
Volkswagen (Uitenhage, Port Elizabeth) Project RPU pickup expected in 2010 Polo replacement expected in 2010 Jetta replacement expected in 2012
Good prospects for the future
So what does Demuynck see for the South African market in the short to medium term? “From a manufacturing perspective, we’d like to see the market strengthening, and we believe it will. We want to see the economy in general gathering momentum. As far as the overall industry goes, it was growing quite well up until the past year or so when we started on a downswing, but that will rebound and probably to a much higher point than even we saw with the surge in 2007. We see the market continuing to retract next year, but we’re optimistic for growth to reappear from late 2009 or early 2010.
“We have some problems in South Africa with inflation and a lot of consumers are staying out of the new-vehicle market. We also have issues with consumer credit – another reason why the market is slow – plus, of course, the rapid rise in oil prices, which will always be felt particularly badly in an emerging market. But GM is a long-term player here, so as long as we continue to offer this mix of localised product, we’re confident we can hold and maybe even increase our market share, just as we have been doing.” GM, together with competitors like Renault-Nissan, BMW, Ford, Toyota and Volkswagen, clearly believes that there is potential in its operations in southern Africa. To compete successfully, the company had to adapt its global products to meet the needs of local consumers, many of whom have nothing like the spending power of their North American or European counterparts. But what about the way in which vehicles are put together in South Africa? Do lower wages, the high cost of imported tooling and a relatively modest new-vehicle market mean the way in which vehicles are manufactured has also had to be adapted?
“Once you’re inside the assembly plant, there’s probably less difference than you would have had ten years ago because of the company’s Global Manufacturing System. I’ve spent time in a lot of plants, in places like China, Korea, South America, obviously in America, and when you’re in the plant, it’s a similar layout; there’s this standardised approach towards manufacturing. The difference is in your volume. Higher volume drives you to a greater degree of automation. But with our lower volume, that drives a more manual-based operation. So there’s less of an investment needed in tooling equipment, robotics and so on,” says Demuynck.
“There are cultural differences, but walking around our plants, with English as the language of choice, makes you feel you could be in almost any other GM facility. That speaks to the importance of the Global Manufacturing System. Part of the way GM runs this programme is that plants like ours reap the benefits from the experience of operations located in other countries. We have a strong network of best practices across the global manufacturing footprint, and that’s very different to how it was a decade ago. Then you would have had unique operating systems, not just in different countries, but at different plants within those countries. For me, I’d say the biggest surprise after less than a year in this position, is there have been so few surprises.”