Expansion plans, sustainability and new EV batteries
The UK has ambitious plans to create a network of giga factories producing electric vehicle batteries. Scotland-based cell manufacturing company AMTE Power is part of this programme and CEO Kevin Brundish spoke with AMS about the company’s involvement and its expansion plans
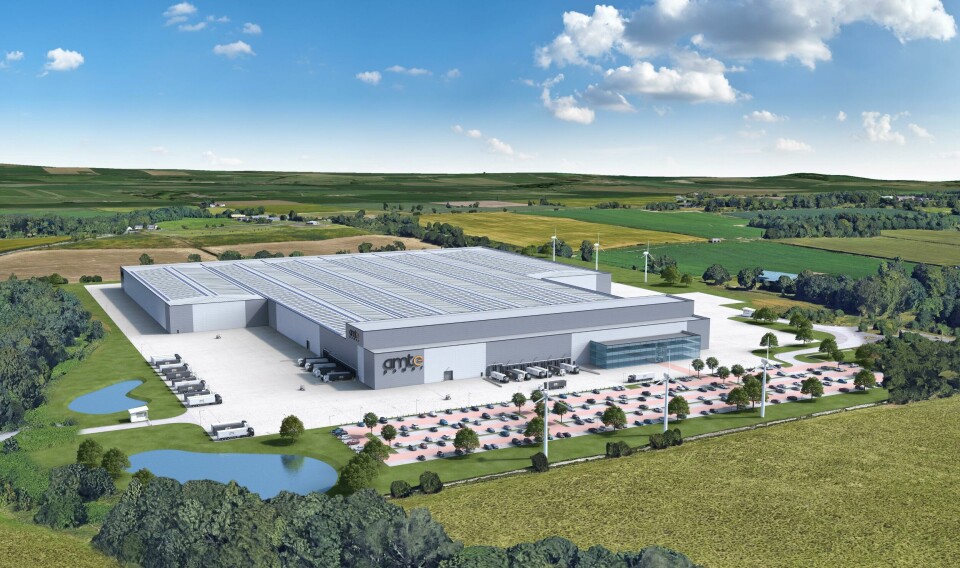
AMS: We’re calling you a battery manufacturer but obviously it’s a complicated value chain between battery cells and packs. Could you talk us through what part of this value chain AMTE is focused on?
Kevin Brundish (KB): AMTE is a lithium-ion cell manufacturing company based in Scotland. We founded in 2013 but we procured the manufacturing facility up on the North Coast of Scotland, which has been operational since the late ’90 and we’ve been making cells here in the UK for that time.
There is a complicated tiered supply chain. Where we fit into that into context is manufacturing cells. We take the processed chemicals and create a cell in one of two formats: either a cylindrical cell – a format used in the batteries you might buy in a supermarket – or a pouch format, commonly used in mobile phones.
From there the next tier in the supply chain would be [producing] a battery pack, where they take those cells and assemble them into a pack with all the control elements that’re required for the end application, which in the automotive context would be going into a vehicle at that point.
When we bought the manufacturing plant in Thurso, we decided to repurpose it and utilise the facility to help us bring to market some differentiated cells focusing on more specialised markets. Production is at a modest scale but fully functional and does all the manufacturing parts of the cell. Our view in 2013, was that there had been a big shift in the market dynamics. The automotive industry was going to go electric and that the large, mainly Far East supply chain were going to focus on that mainstream market, and it would leave a lot of other markets less well served. Either because they’re not competitive on their volumes compared to automotive or because they wouldn’t want what automotive was looking for.
It’s not a short journey bringing a product to market, particularly in automotive, so we have focused on a more specialised, premium market. For this we have developed three differentiated cells, which will be introduced into the market over the next three years. The substantial part of the development is done, and our real focus now is on scaling up production. I should add, we can also produce conventional cells, but you must be at very large volumes to be competitive.
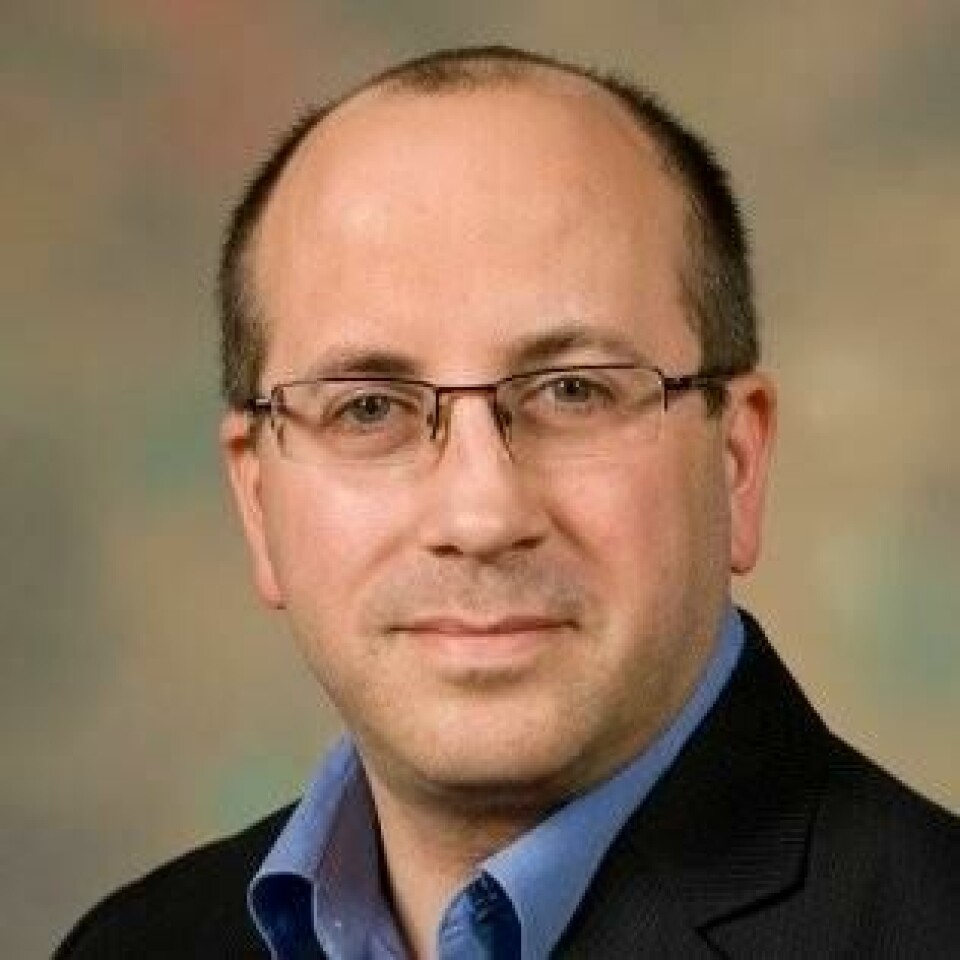
AMS: Could you offer more insight into the specialised aspect of the cells you’re developing and what specific vehicle segments – high performance vehicles, for example – you are targeting?
KB: The differentiated cells, taking an automotive related example, are high-power cells. We’re packing as much power into as small a volume and weight as possible. The reason for this is because, at present, conventional cells are focused on the energy, which is all about range; the power is all about the transience, the acceleration, getting the vehicle up to the speed. Using an ICE comparison, the energy is all about the amount of fuel you have in your tank and power is all about how much fuel flow – how fast the fuel is flowing.
For the performance vehicle segment, they’re differentiated on their performance and acceleration is one of those features. They need something that’s different to the solutions used in more mainstream vehicles. So, we have focused on that second aspect – putting as much power into as small a space and volume as possible.
As we’re taking this development forward, we are seeing is that there’s a broader market than perhaps we had recognised. For example, with a fuel cell vehicle you still need a solution that deals with the transience, so a power cell would be a good solution.
Also, trying to get a higher level of transience from a standard energy cell can adversely affect its service life and range capacity. Having a power cell that’s doing that aspect and then having an energy cell that’s providing the range is something that we are seeing as being an interesting space. So, initially targeting the high-end brands but as we develop the product, we’re now expecting to have the ability to expand into a more mainstream end-use position.
In 2019 the UK Government published data saying that the UK would require eight giga-factories to supply every vehicle made here. Obviously, we’ve been through an interesting 18 months so far but that was based on one and a half million pure electric vehicles being produced a year in the UK.
However, we aren’t anywhere near that scale of capacity emerging in the UK just yet. So, there is still a space for us to expand with a more conventional cell. Not what we set out to do originally but, obviously, if the demand is there it’s something we can do. So that’s really the logic behind our expansion plans.
AMS: Let’s talk about your current production footprint for manufacturing cells, and the ambitions. You mentioned the plant in Thurso, and I believe there’s also some expansion plans that are already on the way.
KB: We have two activities, the production plant in Thurso that’s at the around the 0.1-gigawatt hour scale. That’s fine for the specialised markets but it isn’t competitive for a broader, higher volume market. Part of the UK Government’s electrification investment is to effectively create a government funded production facility that allows companies like us to step into a giga-factory environment. So, it enables us to take our production up to that sort of gigawatt hour pace and that’s what we’re in the process of doing. As part of this we’re also active in the UK Battery Industrialisation Centre (UKBIC), which is based in the Midlands, but behind that we’ve been designing a larger facility and we have targeted two gigawatt hours as our launch platform. We’re not limited on this, as cell manufacturing has a modular element to it, so scaling up beyond two gigawatt is achievable. We have plans that take us up to 10 gigawatt and we have the potential to go beyond that depending on market demand.
AMS: Can you tell us more about your manufacturing operations?
KB: The Thurso plant is less automated and therefore quite flexible. Manual intervention is reasonably high, which affects the cost level, but it makes us strong in developing those processes. There are process differences between making a high-power cell as compared to making an energy cell, even if we used the same chemistry. But we’ve been exploring very different chemistries.
Scaling up isn’t simple, you’ need to hit a certain level – say two gigawatt hours – and have all the processes behind that, then it becomes simpler to scale up by using a modular approach. Getting into the UKBIC enables us to make sure the processes we have can be utilised at that faster pace, at that giga pace. So, doing that then sets us up to build that modular approach.
When you get to those big scales it’s very automated and very optimised. So, flexibility starts to drop off and that’s where a lot of the process tightening comes up. If your plant is optimised to make a 21700 cylindrical cell, you aren’t going to be making 18650s, typically it doesn’t have that broad range of capabilities, whereas our [less automated] plant in Thurso does.
AMS: What do you identify with UKBIC as the really important areas to support the scale up that you mentioned? What are the areas you expect to be focusing on most in that partnership?
KB: When you’re making a cell from the raw materials, which typically come in as powders, there’re two core elements. There’s manufacturing the electrode and then there’s assembling the cell, either in cylinder or in pouch format. For the electrode production you’re essentially creating one large roll, obviously there can be a few differences with that but that’s typically what you end up with.
Scaling this up revolves around getting your initial recipes for those energetic containing compounds that you then deposit onto the foil and all those processes right – are you drying at the right time, what is the line speed, etc. Those are all the sort of metrics that you must get right in a process. Once you’ve done that it’s a matter of either punching out or slicing the electrode foils depending on what type of cell being produced. Typically, cylindrical cells are cheaper to make because the process of winding is faster and less capital intensive, but the pouch cell offers benefits of large surface area, so less cooling required and less weight. This must be considered at the whole system level when you get the battery configured. So, exactly what you choose to do is dependent on both the manufacturing process of the cell but also of the end application.
Our relationship with UKBIC has enabled us to take all our processes and overlay them on that giga pace production. We expect to complete this development this year to produce our first products.
AMS: Do you have finite cycle times on various parts of the process making the cells? Are there bits that you can’t speed up such as the aging process?
KB: Once the cells are substantially formed you go into the formation and ageing approach, and that tends to be quite fixed. If you are looking to scale up that process just must put more lines in. The formation and ageing cycle do differ chemistry to chemistry and, in fact, can differ even for the same chemistries if you’re using it in different ways. So, getting that right is one of the key processes that you must own as a manufacturer.
You can speed things up like [electrode] drying times, etc. but once you’ve set that maximum pace, it is then just more of the same units, particularly on the assembly line. If you go into what we call the wet area, the electrode production, you’ve got a mixing and coating process, those can scale in the output, depending on the size of the equipment but when it comes to the cell assembly side, it tends to be the same equipment, just more of it.
AMS: How do you work with UKBIC? Do they have staff seconded to your facility to work processes there, or are you using Coventry to develop a process or is it a mixture of both?
KB: Our initial plan is to utilise the team that exists to get that transition/translation activity done from our Thurso plant into the UKBIC, but our ambition would then be to start to take a greater level of control over that, our team becoming a more dominant feature in that. Also, we need to start generating a broader skill base, which is going to be necessary for us as we scale up production.
AMS: What do you see as the biggest challenge for a company like yours in its ambitions, in this next step of scale?
KB: I think a big thing for us is doing as much as we can to provide an onshore supply chain in the UK. So, both ourselves fitting into that but the tiers that supply into us and the tiers that come after us.
As an example, an area of focus for us is ensuring that the supply chain can deliver what we need. Also, government support does cover the broader supply chain range. I’m part of the Faraday Challenge Advisory Group and so I’m aware that the activity has gone beyond the automotive companies, engaging with companies in the supply chain, the chemical processing industry, etc.
There’s already lot of capability in the UK, but probably not enough if we want eight giga-factories. So, there’s going to be a level of importing that will remain until that has been solved.
I think the last point is the end-of-life element to it. It is good that we’re seeing the manufacturing scaling-up in the UK, but here’s got to be a consideration around the sustainability of that. We are lucky manufacturing in Scotland with a lot of low carbon energy, but obviously we’re quite small. When you get into giga-factory scale, using renewable or green energy sources is key, so we must plan that in. And what you do with the cells at the end of it? Is that a recycling or a reuse approach? There’s still a bit of work to be done there but we’re actively engaged with companies that are getting quite close to commercially viable processes in recycling.
AMS: Is there a critical risk that some supply shortages could hold things back if that investment doesn’t follow, as we see happening in other parts of the sector?
KB: If the supply chain doesn’t match the production capacity that’s coming online, then clearly there will be a mismatch and that won’t be good. I’m not really seeing that now, and there’s still a lot of expansion potential in this space. But I do also think that once that expansion starts it does tend to facilitate expansion through the whole supply chain as it’s essentially demand-driven. As a company we’re very conscious of that and we’ve forged relationships the UK and we’ve also been looking at a joint venture in Australia where there is an abundant source of the raw materials.
We’re doing other things, perhaps not immediately related to automotive such as looking at a sodium ion-solution rather than lithium-ion. It doesn’t require some of the more sought-after materials. And as we’re seeing the LFP type of chemistry has become attractive in automotive, so sodium-ion may well become attractive in that space as well.
AMS: As you move forward, are you going to lose that flexibility and that USP of your business of being quite diverse by having to commit to the large giga scale production operations and perhaps higher levels of automation?
KB: The short answer is, not really, but I need to put some context around that. There has been a fixed format for some time in lithium-ion cells, it was the 18650, that has morphed into the 21700, typically cylindrical, that is dominating the space. But there are other pouch formats that have typically been used for more high-power cells, etc. So, there are some standard formats emerging for both types but that’s not to say this won’t change. But the reality is, most of the infrastructure is going to align against a relatively fixed format.
There’s still a degree of flexibility in the wet section of electrode production, working with different chemistries. It’s only when you come to package it into the cell that you start to become less flexible. Theoretically you can make an electrode of a completely different compound but still use that same fixed format of cell assembly but it’s the assembly side that has some limits.
So, I think, in practice, you will see quite a lot of narrowing and focus on those formats but, if it all had to change, is there flexibility available? Yes.
AMS: Do you foresee working more directly with car makers? Do you understand what their needs are and particularly as it will relate to some aspects of manufacturing too?
KB: We do engage with them right from the outset. The advantage we have that is we’ve been able to provide prototypes and samples into several our end clients from our production plant. We’ve made a couple of announcements recently on engaging with different end users. Most recently we’re working with BMW was one of those partners. This doesn’t guarantee that the cell will be adopted but typically, in the early stages it’s more an arm’s length relationship where we are engaging and providing cells, and once that interest is there, we’ve seen a developing relationship.
AMS: When we talked about the expansion to two gigawatts and potentially beyond, are you already looking at specific sites? And what are some of the key deciding factors that you think will drive that?
KB: We’re looking at number of different sites and we’ve started to narrow this down. The key features are you’ve got to have a certain scale of resource available and certain type of skills base. Proximity to the end client is a consideration and obviously proximity to the supply chain.
Probably the most important is the power supply and its form [renewables]. If it’s not a low carbon source of power or you’re importing cells from places that aren’t using green energy, then the entire carbon footprint for the cell is still significant. So, a real core part of becoming part of an on-shore supply chain is to make sure you can offer as low carbon and as sustainable position as is possible.
AMS: Looking ahead, what are the key milestones for AMTE in both the short and medium term?
KB: All our products are following the same top-level roadmap. We use our own plant to develop it, which removes the technological risk, and that’s substantially done. We then are stepping into the UKBIC, which is where we’re active now, to remove some of the scale-up risk. And in parallel to that, we’ve been designing and costing out and planning for a larger production facility. In parallel to that, bringing the product to market, we’ve obviously been addressing and engaging the market to get the demand side solved.
The milestones that are left on that journey are completing our scale-up in the UKBIC, making the products available for release, and it’s the differentiated ones, one over each of the next three years. Planning and down-selecting a site, which we expect to do next calendar year, and then looking at the build-out, really, against the demand profile.