Can an electric van deliver for LEVC?
Following its success in reinventing the iconic London black cab, Geely plans to produce a one-tonne electric van under the London Electric Vehicle Company brand
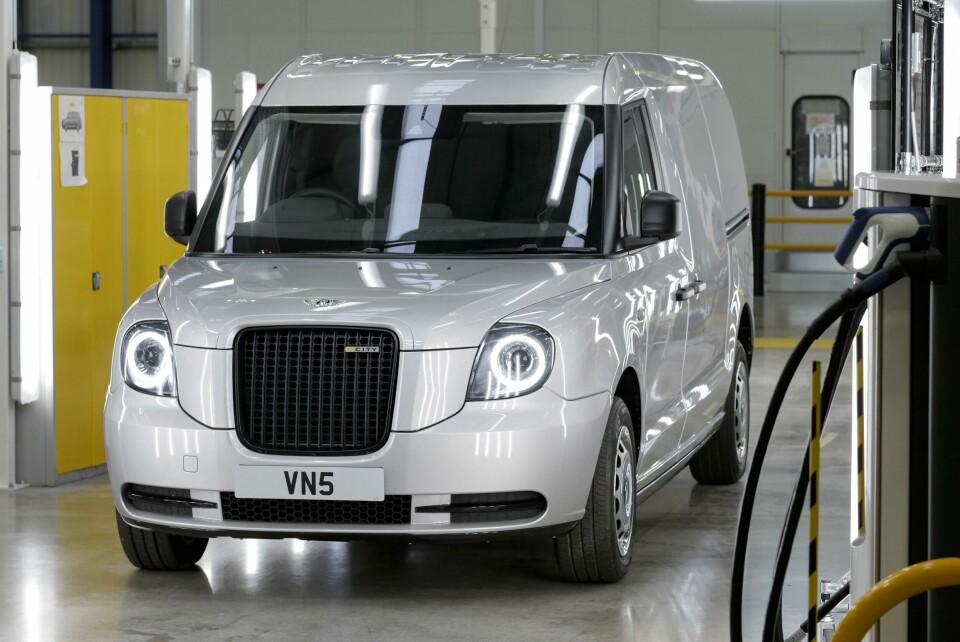
The first part of the £500m project has succeeded. LEVC, aka the London Electric Vehicle Company, last year built 2,500 range-extended taxis from its production hub on the outskirts of Coventry, central England, taking the total built to 4,000. London is now teeming with these mostly silent, elegantly designed cabs packed with technology mainly repurposed from Geely’s Volvo brand.
But now comes the moment in the plan where, all being well, the company can turn a profit. This year LEVC will launch a one-tonne electric van built using many of the same parts that the company hopes will take the plant closer to its 24,000 capacity. Eventually, the van will account for 70% of production, it hopes.
LEVC needs the economies of scale the van will bring. Both the TX5 taxi and the VN5 van, production of which starts in the third quarter of this year (coronavirus depending), use a costly combination of bonded aluminium body and petrol-electric drivetrain. The long supply chain meanwhile stretches to South Korea for the battery cells and China for the 1.5-litre three-cylinder petrol engine.
New CEO, new approach
The young company has already replaced its CEO. The replacement, Joerg Hofmann, arrived early last year from Audi and immediately set to work cutting costs in a bid to bring the profit target closer. “This was a big challenge which caused some turbulences as well,” he said of LEVC’s vehicle strategy in an interview last October. “Maybe the turbulences in the past haven’t been addressed in the right way, and that is what we are doing now.”
We asked plant director Mofid Elkemiri to give us an example of some of the ways he has cut costs in a plant that was only inaugurated back in 2017, and he mentioned a simpler way to fit the range-extender engine using £1,000 trolleys rather than a £30,000 lift system.
However, the switch to incorporate the van on the same line as the taxi has required investment of more than £5m, mainly to increase the number of stations to speed up the takt time from the current 29 minutes to an eventual 10-12. That means pushing the workforce from around 200 now to 500 by the end of next year with the addition of an extra shift. If the van proves a hit then they’d need a third shift to reach the 24,000 capacity.
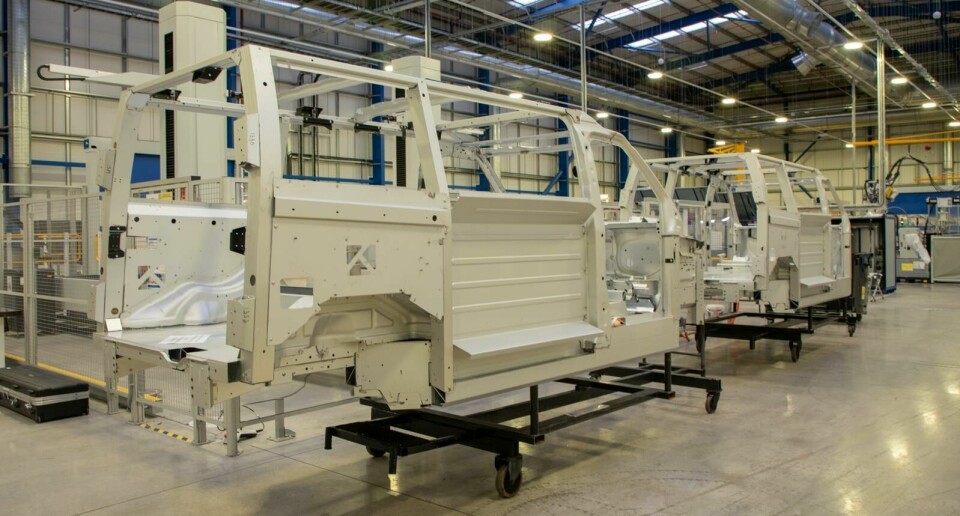
Common parts offer economies of scale
The economies of scale are there. As well as being built on the same line as the taxi, the van also uses 65% of the same parts. The front end is the same, as is the drivetrain. The slow speed of production at the moment means that LEVC can even build prototypes on the taxi line. “The advantage is that staff use real production tools, so they get experience and you learn the steps you have to change in the real world,” Hoffman said when we visited the plant early March.
LEVC’s UK localisation rate is only around 30% of parts and 40% by value. The big UK value piece is the supply of extruded aluminium parts from Hydro in Caerphilly, south Wales, which LEVC then bonds in its body shop. There’s no riveting used to attach these parts except to locate them ahead of bonding, meaning the body shop is incredibly peaceful. Once the glue has been applied, a combination of lasers and cameras check that the 400 parts are exactly in place, then the bodies are baked in one of four ovens for 20 mins at 185°C (“same as a pizza,” Elkemiri says).
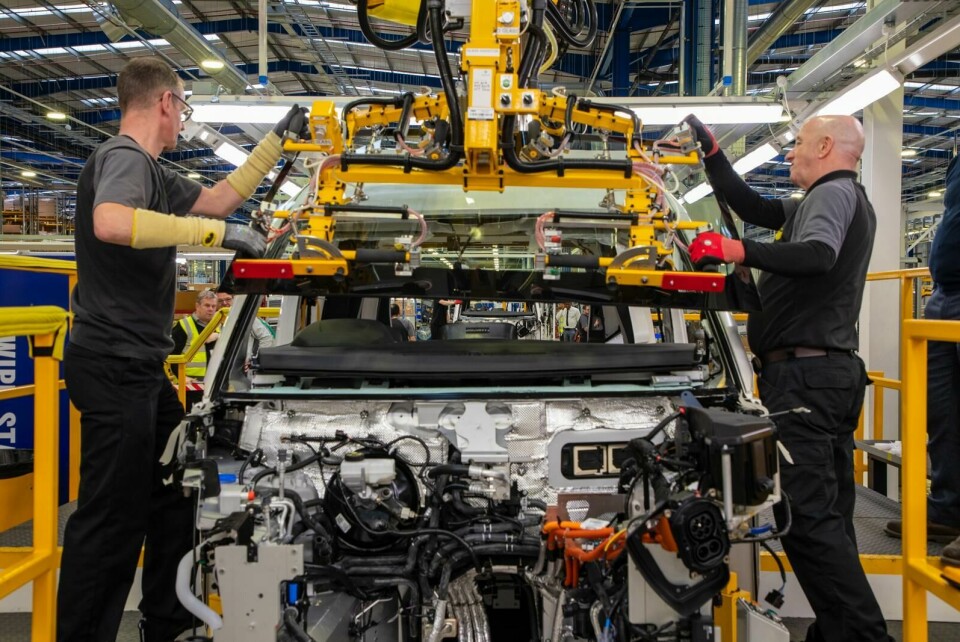
Then pre-painted panels are glued onto the body on a cold cure line before heading off to the assembly line and its EMS monorail carriers. The vehicle briefly leaves the EMS to be carried by AGV to have brake pipes and wiring harnesses attached before heading back to the EMS to have its 31kWh battery pack, three-cylinder engine and ancillary parts fitted. Then comes trim, where the van skips the five stations focused on the taxi interior.
Succeeding in a cost-conscious market
When the van launches it will largely have the electrified LCV market to itself, bar the Ford Transit Custom plug-in hybrid. But while urban emissions legislation is moving to the side of the VN5, the likely high price will count against it in a notoriously cost-conscious market. It’s too early to say whether LEVC’s high-risk gamble will pay off, but the rigour obviously going into production of the vehicles should give them a fighting chance of becoming another British automotive success story.