How to test EV battery packs
Testing EV components is now an important addition to OEM and tier supplier quality control processes. Chuck Hagyard from Cincinnati Test Systems, shares some insights into critical leak test-related challenges and considerations
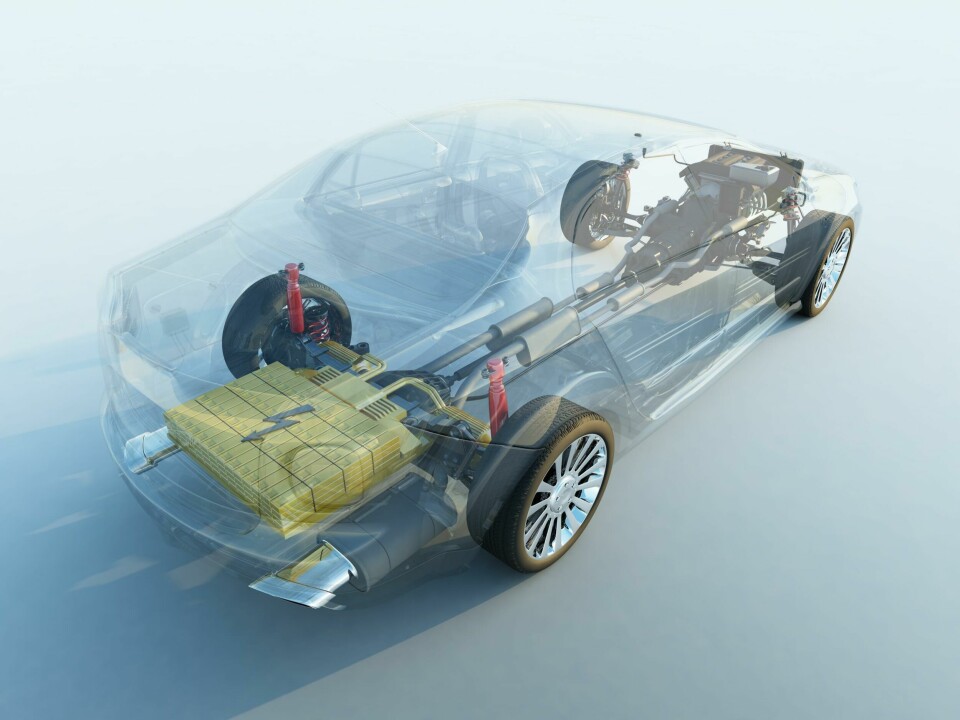
OEMs and tier one suppliers are spending a significant amount of time developing their electric powertrain products and assembly processes, and looking for ways to be more competitive in their industry space. The challenges around component testing are something that must be accounted for as they move forward with their EV implementation plans and product launches.
This includes occupant safety as well as product and process design considerations. If those considerations were not challenging enough, manufacturers must also balance commercial interests – the capital equipment expenditures required to implement the best leak test solution for the application at hand.
“Without question, leak testing an EV battery is one of the most challenging applications that any leak test company will tackle”
Chuck Hagyard, Cincinnati Test Systems
The problem with water
Water ingress is the great risk for EV batteries and could cause a catastrophic failure, potentially jeopardising the safety of the vehicle occupants. Care must be taken to ensure that the product design is robust and that an appropriate leak test specification is implemented to ensure that water will not leak into the battery and create a fire hazard. Automotive OEMs develop test specifications with sufficient sensitivity, accuracy and repeatability by considering these worst-case user scenarios. The integrity of a pack to resist water intrusion, for example, is typically measured to the IP67 standard. Anything rated to IP67 will remain watertight after 30 minutes immersed in water one meter in depth.
But what equates to an acceptable air leak rate for a pack to meet the IP67 standard? Different manufacturers have different answers, though some trends are starting to emerge. Manufacturers must also determine if they are going to test with a positive or negative (vacuum) pressure within the pack.
Process and design considerations
Without question, leak testing an EV battery is one of the most challenging applications that any leak test company will tackle. The impact of a safety issue is easy to understand, but what is not always readily understood is how the design considerations of the battery pack can also be a key determinant of what will be best way to leak test it. The size, structural characteristics and applications of a battery pack present a multi-faceted challenge in devising an appropriate leak test.
Battery packs are large and often have flexible surfaces. These large internal volumes and expansive surface areas increase variability, which ultimately impacts the accuracy of the selected test method. Even a very minor amount of deflection is amplified when a large surface area is involved.
The challenge of size varies with the type of EV. The manufacturer may determine that a costlier tracer gas test method is best for a plug-in EV battery pack, because its large size makes it highly sensitive to environmental fluctuations. A hybrid EV pack, on the other hand, poses fewer of these challenges due to its smaller size. In this case, a less expensive air-based test solution may be sufficient. It all depends on the variables of part volume; how unstable the pack is due to its flexibility and its expected operating environment.
EV battery packs are also particularly susceptible to environmental influences that are very difficult to control in the plant where they are assembled. It may not be practical to closely control the ambient temperature or the barometric pressure on the plant floor. Quite often, no effort is made to do so. Temperature variation can be particularly problematic and very difficult to manage, dependent upon the test method that has been selected for the application.
“Product and manufacturing engineers must work side by side to design products and systems that can be reliably tested in a production environment”
Chuck Hagyard, Cincinnati Test Systems
I mentioned that packs are flexible. Designers are always trying to make batteries lighter with components and subsystems made of thinner materials that are more easily deformed. These design characteristics can result in the components ballooning and deflecting to the point where trying to reliably measure the leak is problematic due to the leak test method that was selected.
Although algorithms can be developed to account for the flexible nature of these components, it’s a challenging proposition to understand how these factors relate to one another and can be controlled. Barometric pressure, wall thickness, and whether to use pressure or a vacuum for the leak test are factors that must be carefully thought through before the product design can be finalised.
The relationship between the design considerations of the battery and its ideal test method are inevitably interconnected. For example, if an automotive OEM is dead set on using a pressure decay or mass flow technology with air, the design characteristics of the product must lend themselves to the selection of that specific test method. Air decay and mass flow technologies are influenced heavily by changes in the part volume regardless of what may cause the volume change. In simple terms, the laws of physics cannot be ignored. This is where the goals of battery weight reduction and achieving a repeatable and reliable test may collide.
With all these factors in play, product and manufacturing engineers must work side by side to design products and systems that can be reliably tested in a production environment.
Balancing safety and design with cost
Automotive OEMs and suppliers must scrutinise capital investment through the lens of how they can yield the best return. Numerous leak testing technologies can be considered when a product is being designed and the leak test method is being evaluated. While tracer gas technologies may be more expensive in terms of the initial capital investment, it’s quite possible that the return on that investment may be better when goals like shorter test cycle time and higher first-time yield are considered. Pressure decay and/or mass flow are often preferred because they’re are less expensive technologies to acquire and deploy. However, when a manufacturer considers the challenge of managing factors such as ambient temperature variation, part temperature variation and barometric pressure change, a tracer gas technology could begin to look more attractive.
Understanding the relative pros and cons of the available leak test methods is critical. The trade-offs need to be understood before a robust test method can be selected. Higher instances of false rejects, lower first-time yield, and longer cycle times can be accounted for when a holistic analysis of the cost to produce a product is considered. These factors are just not as visible as the initial capital investment.
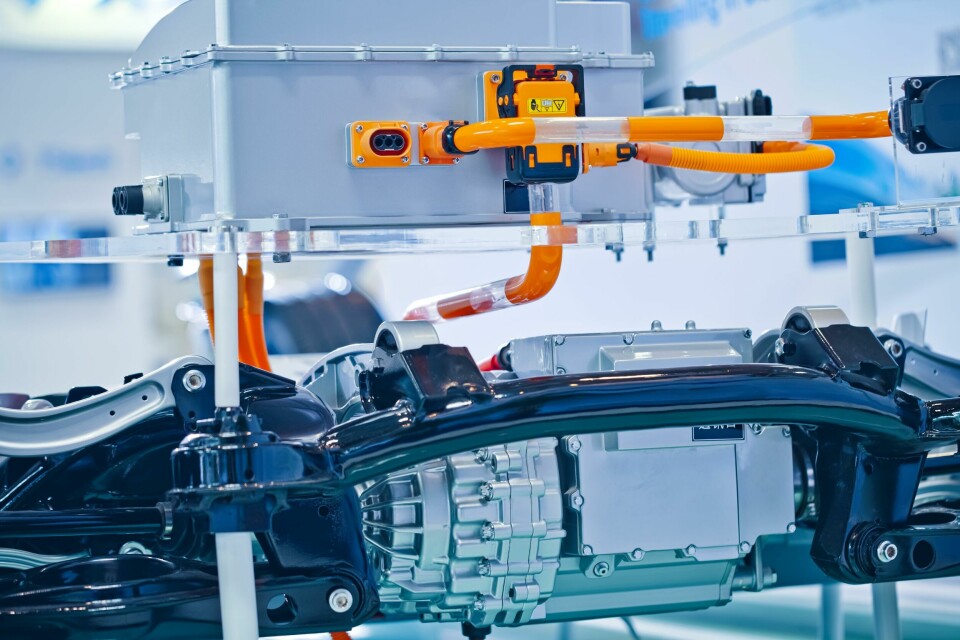
Consider options early in the process
Evaluating the best test method should start very early in the design phase of an EV-related product. A robust leak test selection process takes into consideration all of the factors that I have presented.
Each of the available technologies have their place in the world of leak testing. Some technologies are more adversely affected by factors that are naturally inherent to the design of battery systems and components. This doesn’t cast a negative light on any particular technology, but it does emphasise the fact that identifying the best test method depends on understanding and weighing the specifics of how an EV will be used. The automotive industry is changing rapidly. EV technologies dominate the product roadmap of many OEMs and leak testing will play an essential role in the launch of these EV platforms over the next decade.