Building the battery pack
While cell manufacture is still largely in the realm of specialist producers, more OEMs are now assembling the battery pack inhouse, but this can be a complex task requiring specialist tooling. Nick Holt reports
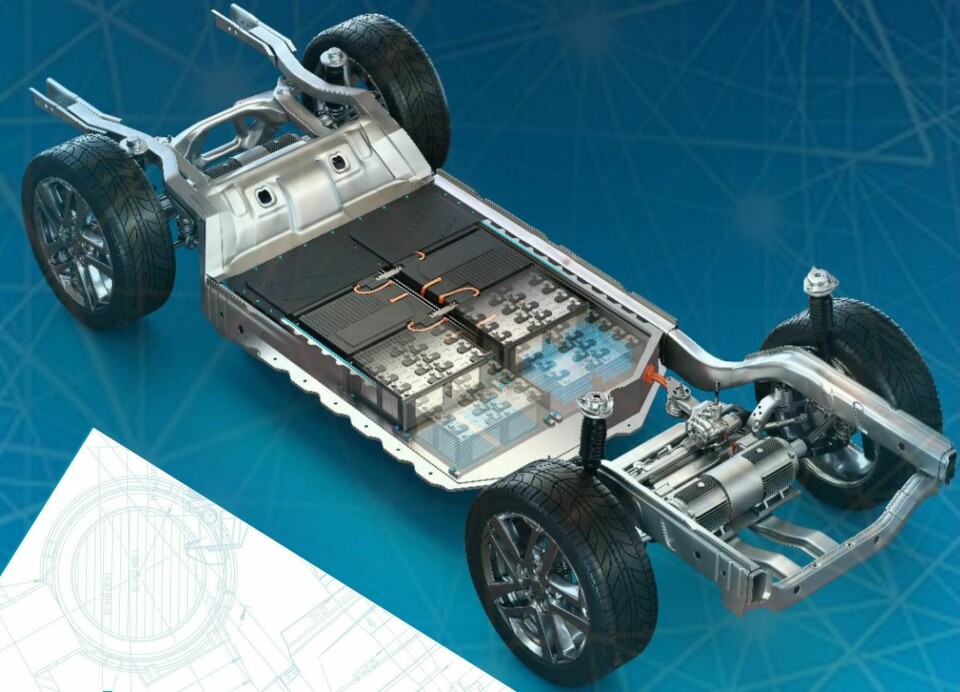
When it comes to battery pack assembly it’s fair to say that quality control is everything; once the enclosure is sealed any failures are difficult and costly to rectify. So, the assembly processes have to be exacting, and as production volumes of this component rapidly increase, the assembly operations have to deliver precision and repeatability. To get some insight into the assembly challenges and solutions we spoke with Atlas Copco Tools & Industrial Assembly Solutions’ (ACTIAS) general manager, James McAllister and Business Line manager, Paul Freeman.
AMS: Looking at EV battery assembly, what are the key process steps?
Paul Freeman: The first step is the cell-to-cell (cylindrical) joining. Currently these are packed into a cradle but this takes up space in the pack, so OEMs are investigating the option of gluing these cylindrical battery cells together. To ensure a strong joint this type of bonding operation requires very precise, micro-dispensing and application of the adhesive. For the prismatic type batteries, these are larger blocks and so the requirement is for a larger volume of bonding material.
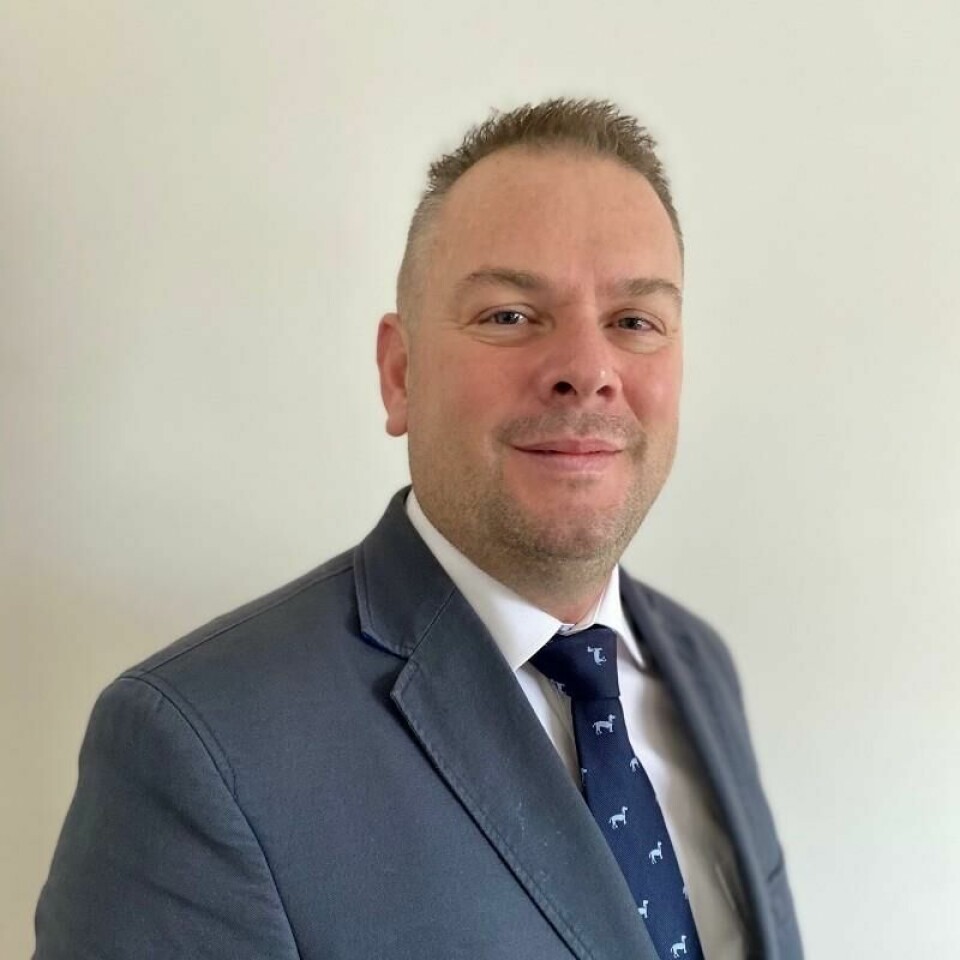
The next step is the modular assembly of the joined cells into a frame that secures them. Our approach to building the frames is to use self-piercing rivets. These frames are then bolted into the battery tray, and it’s important to ensure the tightening process is performed accurately. The next step is to ensure the battery enclosure is sealed to prevent moisture ingress. This is an important part of the process to ensure the environmental conditions in the battery pack are as stable as possible.
Also, the enclosure lid needs to be removable so we apply a liquid sealing gasket, which is then sometimes cured using a UV process. To secure the lid we use flow drill screwing technology. The advantage with this is that is doesn’t create swarf, which could contaminate the battery pack and potentially cause shorting of the electrical systems. During the process we use a vacuum system to remove any fine metal particles. Another benefit of the flow drill screwing technology is that while it effectively secures the lid, it also allows it to be removed for maintenance purposes.
“Our aim is to be a long-term vision and joining technology partner to our customers, providing complete solutions rather than just individual products” James McAllister, ACTIAS
AMS: Given there has been a lot of focus on ensuring the integrity of the battery pack, is there now a recognised need for the cells to also be accessible. Has this become another important criteria from OEMs?
PF: Initially packs were welded closed but this creates a lot of work to access the cells if needed. OEMs are now looking at ways of making the internal components of the pack more accessible but without compromising the long-term integrity of the enclosure.
AMS: In terms of the battery pack architectures are there any notable differences between OEM’s choice of cell types and any trends emerging?
PF: We’re currently working across all the common architectures, cylindrical, prismatic and pouch types, and this does vary depending on the OEM’s own design approach and production strategy. But we’re not seeing any big shift to one of these types at present, however, the pouch type cell is probably the least used in our experience.
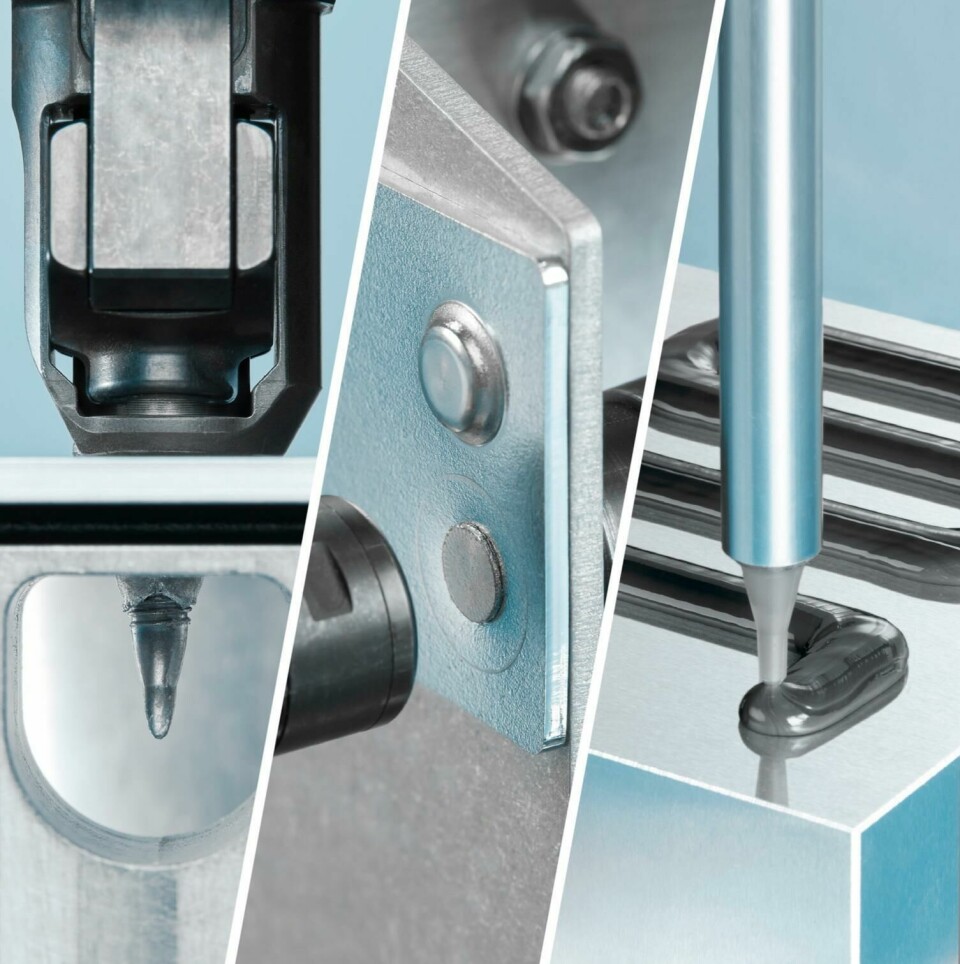
AMS: Has Atlas Copco had to develop new technologies, processes or equipment for EV assembly operations?
PF: We have and this is in part due to the materials used in the assembly process. There is a big emphasis on thermal management, maintaining a constant temperature within a few °C. We are using some special insulating pastes applied between the cells and the enclosure base plate, to help keep the temperature stable.
These pastes have a very high aluminium content, around 80% of the material. This higher density creates a challenge for storing and dispensing these materials. The standard containers for paste materials can’t handle the weight of like-for-like volume with the heavy insulation paste, so we have developed specially strengthened vessels, specifically for these high-density pastes, to allow for the volumes required in series production operations to be located at the pumping stations.
We have also had to develop our dispensing equipment in-line with the new materials we’re using. For example, initially we found that the highly abrasive nature of the thermal insulation paste, discussed earlier, was causing excessive wear to our dispensing pumps, creating problems with seals. So, we have upgraded these pumps with high-strength steel parts and all-metallic sealing. We have now introduced a new, higher spec range of equipment to manage volumes of these high-density pastes.
James McAllister: With the flow drill technology we have developed a special magazine attached to the robot, that holds a larger quantity of screws, so for example the robot can complete a number of complete cycles when securing the battery enclosure lid, reducing the number of times it needs to reload. This cuts the number of operations the robot needs to perform and speeds up the cycle time. It also reduces the tooling requirements.
Also, during the tightening process securing the cells into the battery pack, there’s a danger of high-voltages running through the tooling. So, we have developed a series of isolated sockets and insulated accessories to protect the operators and equipment. There is a lot of safety training around the high voltage stages of the battery assembly process. As part of this tightening capability, we’ve developed tools with process control and traceability.
AMS: To be able to deliver these solutions have you acquired other businesses or formed technical partnerships to bring in new competences?
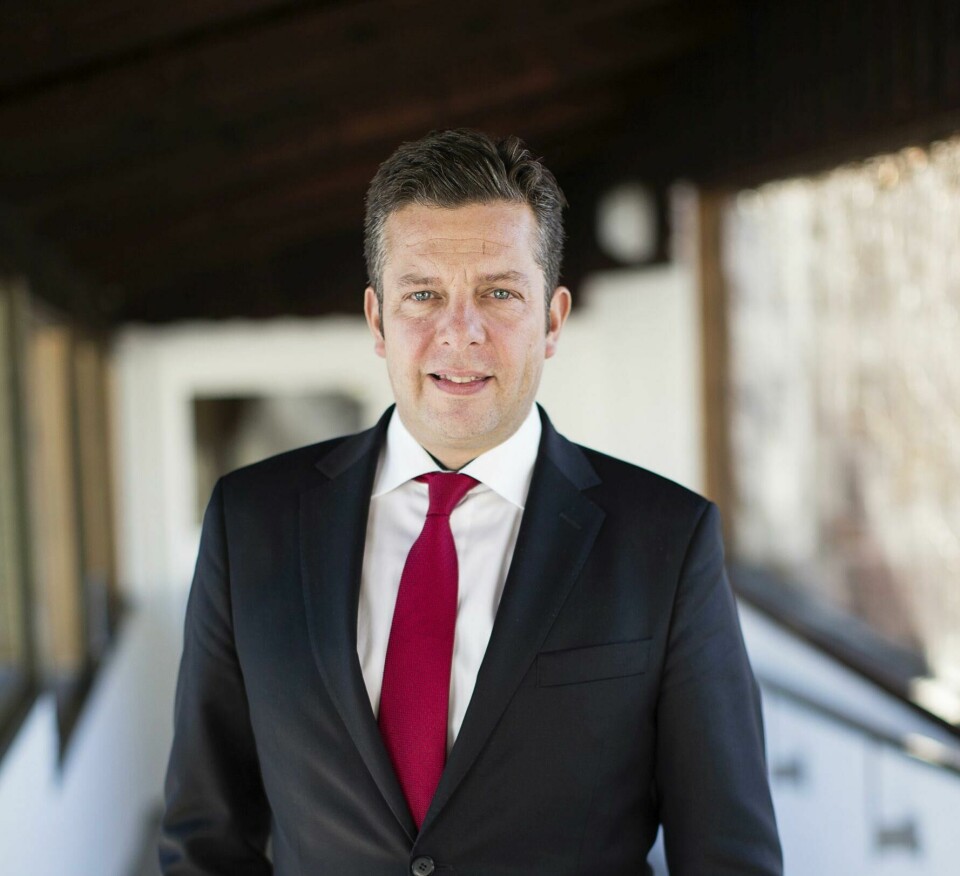
JM: Over the last 10 years we have acquired a number of businesses. Paul joined our team following the acquisition of SCA dispensing, a German company. Their primary competencies and equipment involve mid to high-volume dispensing operations.
Henrob provides self-pierce riveting technology. This was primarily used for aluminium-to-aluminium but now for reasons around strength and cost, this joining method is being applied in mixed-material applications (aluminium, high-strength steels, composites, etc) especially with some of the German OEMs expanding their joining technologies.
Our SCA bead inspection vision system complements our dispensing to verify correct application and position. K-Flow flow drill fastening delivers the fastening technology for the battery enclosure lids.
Scheugenphlug micro dispensing, provides the cell-to-cell joining process. They have a great deal of experience across the electronics industry for ‘potting’ where a sealing compound is applied to electronic components to secure and protect them.
We acquired the machine vision company ISRA in the middle of last year. This was a very strong acquisition as they are a leading company in this field , offering technologies such as inspection and robot guidance, etc. We have also created a new division for machine vision technologies and added Perceptron metrology to this in December last year.
PF: All the major OEMs are looking at increasing levels of automation, so we can see how important vision systems are to this development. These acquisitions complement each other and give us technologies to create future factory operations.
JM: Our aim is to be a long-term vision and joining technology partner to our customers, providing complete solutions rather than just individual products.
AMS: Where do you see the biggest assembly challenges in building EVs?
JM: There are a few. Being able to successfully join a number of different materials is one challenge and we are able pull together the different joining technologies and provide some analysis on the performance of these. Another aspect of this is that the steels being used are getting harder, which adds to the challenge. And this is part of the overall trend to reduce vehicle weight.
I think vehicle makers are also faced with a difficult transition from producing only ICE powertrain vehicles to hybrid or full BEV.
AMS: Do you see EV production and design becoming more standardised in terms of structures, configurations, materials, etc.?
PF: Currently OEMs are pursuing a number of different design and configuration paths and there are many considerations and reasons as to why a carmaker goes in one direction and another has taken a different approach. So, while there are shared approaches to materials and drivetrain technologies, currently we don’t see a truly standardised approach across the industry in regard to EV battery assembly. There are, unsurprisingly, many small differences in the structures, materials and systems that have to be considered in the assembly processes. This means we are working on solutions that are adapted and customised for each customer’s requirements. However, in the next decade I think there will be far more commonality as the technologies mature.
“All the major OEMs are looking at increasing levels of automation, so we can see how important vision systems are to this development”
Paul Freeman, ACTIAS
AMS: Looking ahead, what do you see as the next technology or equipment step, in terms of EV assembly?
PF: OEMs are looking to cut the costs of production processes and the associated overheads. So, from our side, if we can increase the speed of the dispensing, tightening and joining processes, without compromising on quality and performance, then that will shorten cycle times, increase throughput and reduce costs. Also, it could reduce the size of the production cells, cutting the overhead costs. We hear from our customers that they want to reduce the floor space needed, so we have been developing more compact equipment solutions.