Automating complex assembly processes
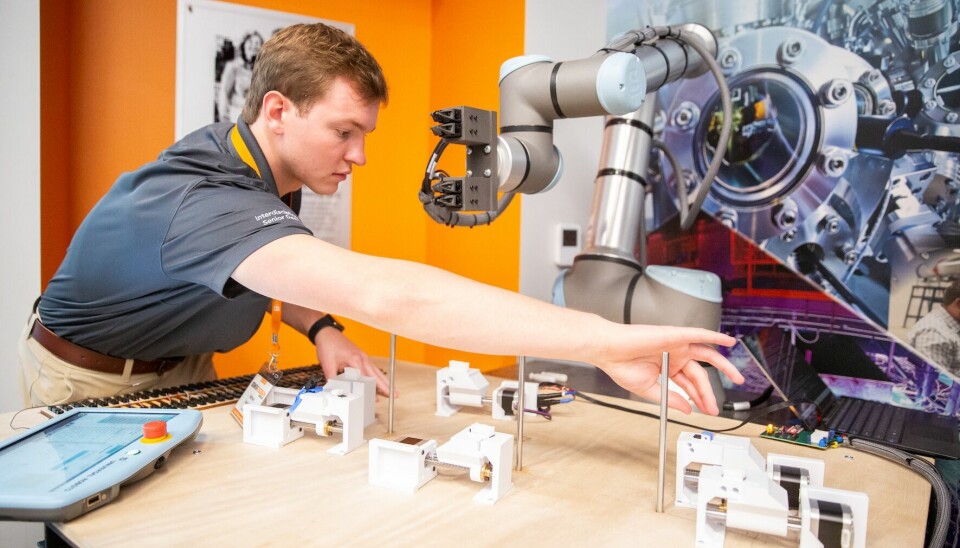
Next steps for automating wire harness assembly
The wire harness assembly process has long been the most difficult to automate; complex layout, flexible wires, small connectors and tight grouping all conspire keep this job as a manual operation, until now.
The Nissan-University of Tennessee wiring harness automation project is an innovative collaboration aimed at addressing one of the last major manual processes in automotive manufacturing: wiring harness assembly. The initiative began in July 2024, with hands-on student involvement starting in September. Nissan tasked a group of undergraduate engineering students with the challenge of routing wires using robotic automation, deliberately keeping experienced harness engineers out of the process to encourage unbiased, original thinking.
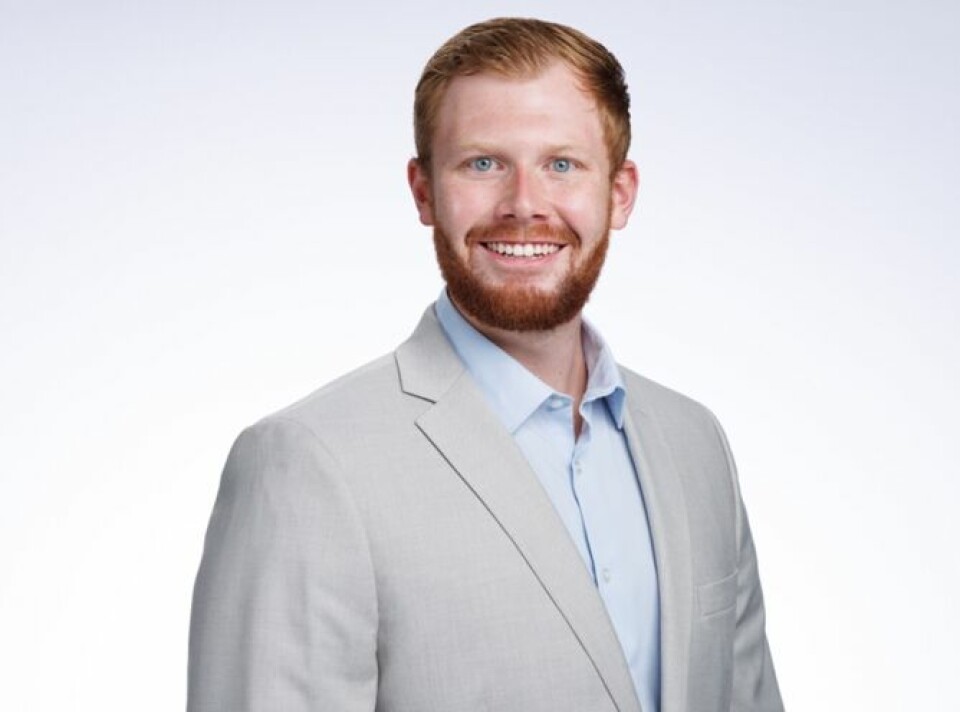
Aaron Hall, an Industrial Strategy Engineer at Nissan, has been closely involved in facilitating this partnership. “I serve as the liaison between Nissan and the university,” Hall explains. “Any questions the students had I tried to use my engineering background to guide them… but that was quite minimal. 99.9% of the project… was guided by the students.” Hall emphasises the project's purpose was not just technical achievement but exploring whether automation of this kind was even possible.
We actually opted for this harness project to keep the wiring harness experts out… to allow the students to kind of take a unique perspective
Aaron Hall, Nissan
Challenges in automating wiring harness assembly
Automating wiring harness assembly faces several challenges.
As Hall explains, “A wire is not a rigid structure like you would see in body
assembly or general assembly. It’s unpredictable and almost uncontrollable
unless you have a grasp on the entire thing.” This fundamental flexibility and
variability make automation difficult, as robotic systems struggle with
components that don’t behave in a fixed, repeatable way.
We actually opted for this harness project to keep the wiring harness experts out… to allow the students to kind of take a unique perspective” – Aaron Hall, Nissan
Historically, wiring harnesses have been assembled manually in low-cost regions, but COVID-era supply chain disruptions exposed vulnerabilities in this approach. As Hall notes, this experience “pointed to a very big issue,” pushing Nissan to explore more resilient, local automation solutions.
Student contributions and innovations
The university students involved in Nissan’s wiring harness
automation project made major strides that exceeded expectations and brought a new
energy to a long-standing manufacturing challenge. Without prior automotive
experience, the students approached the problem with a fresh perspective. “We
actually opted for this harness project to keep the wiring harness experts out…
to allow the students to kind of take a unique perspective,” explains Hall.
They were able to take a wire from point A to point B and put it into a connector… and they were able to do it repetitively
Aaron Hall, Nissan
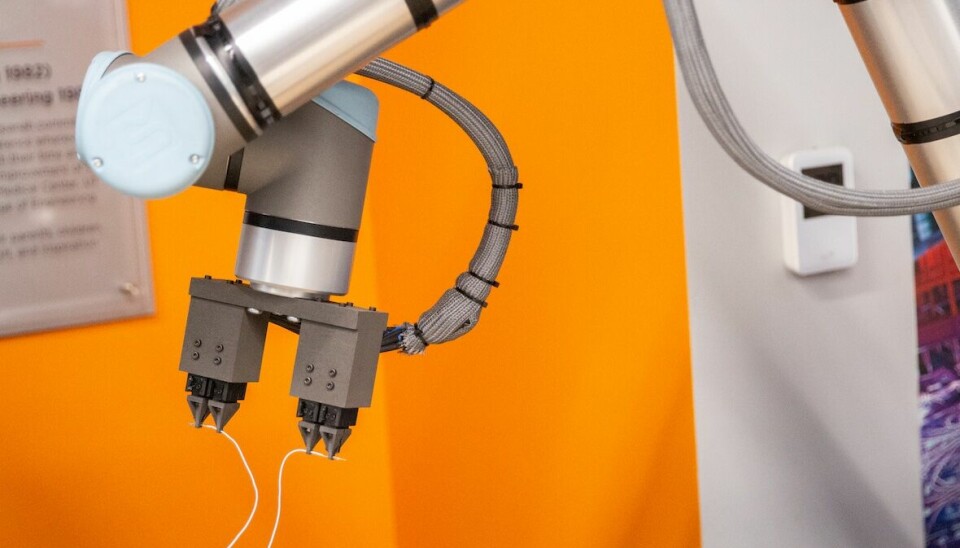
Their key achievement was building a robotic system capable of repetitively routing a wire into a connector with high precision – 1.6 mm terminals into 1.8 mm connectors – over just a three-month span. “They were able to take a wire from point A to point B and put it into a connector… and they were able to do it repetitively,” Hall said. This prototype validated the feasibility of robotic harness assembly and opened the door for further innovation. This achievement also unlocked a new set of challenges: “What happens whenever you populate an entire connector with wires? Do you still have enough space to fit that final one?”
The students also brought significant process efficiencies. Hall highlights a breakthrough in routing design: “They determined that instead of needing 15 pegs, they only needed two to be able to do all the routes… It reduces complexity and time.” Their suggestions also included implementing vision systems to replace manual XYZ coordinate programming, further enhancing automation.
Future directions and implications
Looking ahead, Nissan’s wiring harness automation project is set to continue
evolving through sustained university collaboration and iterative development.
As Hall notes, “We are continuing with the university to work on this from a
few different angles… at least into next year.” A new cohort of students will
build on the existing prototype, tackling more complex tasks like full
connector population and harness bundling.
The current system proved that robotic wire insertion is feasible, but Hall emphasises that it’s not yet ready for manufacturing. “This will not be a manufacturing-ready process… but by the end of the following year, we will have a very good system that we could then take back… potentially bringing it in-house or sharing with a supplier,” he noted.
While the immediate manufacturing impact is modest, the broader implications are significant. “In the physical time to create the harness? No,” Hall admits. “Where you can see potential improvements... is 90% in the supply chain.” Local automation could streamline logistics, reduce lead times, and enhance production flexibility.
Ultimately, the project’s flexible path forward keeps options open: internalisation, supplier integration, or hybrid manual-automated workflows. As Hall put it, “Everything’s an option at this point… we don’t know what the system can do yet.”
The project will continue with a new student team, iterating on the current design and integrating features such as vision systems. Hall remains involved as a strategic guide, ensuring continuity and helping bridge academic innovation with industrial application.