Sustainability: Fossil-free steel
Car makers are setting ambitious targets to reduce their carbon footprint in production operations, key to this will be a sustainable supply chain. Experts from steel producer SSAB share some insights into how the company has responded to this important requirement with the development of fossil-free steel
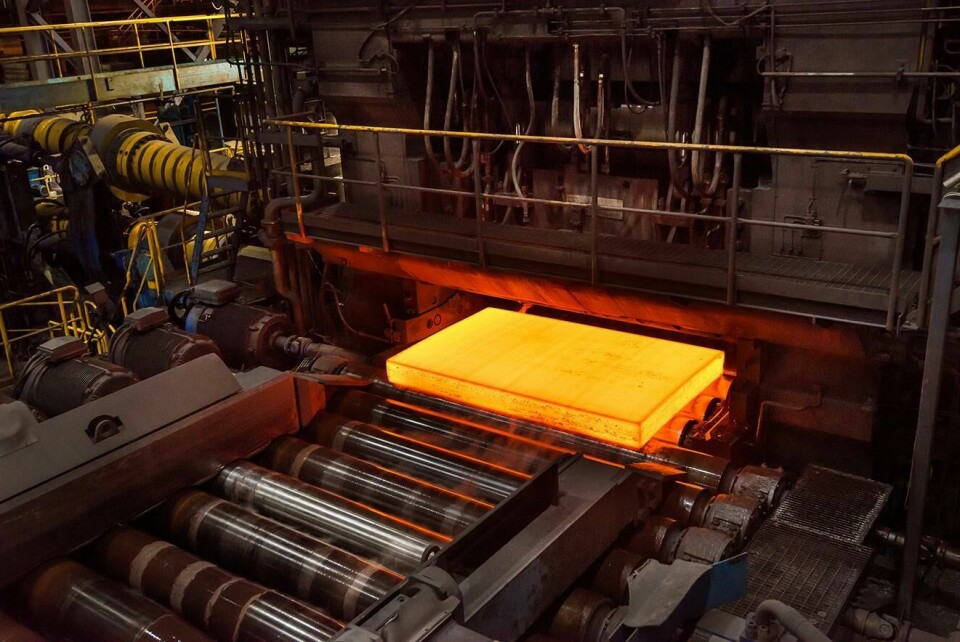
For vehicle makers the issue of sustainability has moved past just being about the tailpipe emissions. Now, the whole value chain of the production operation needs have a high level of transparency regarding sustainability and CO2 footprint.
Offering some context for this around the area of materials supply to automotive OEMs and tier suppliers, Jonas Adolfsson, Business Development, Mobility Manager at SSAB said: “For the end user electrification is more than just the tailpipe emissions, there is a lot of focus on the CO2 being produced in the manufacture of an electric vehicle, including the components and materials.
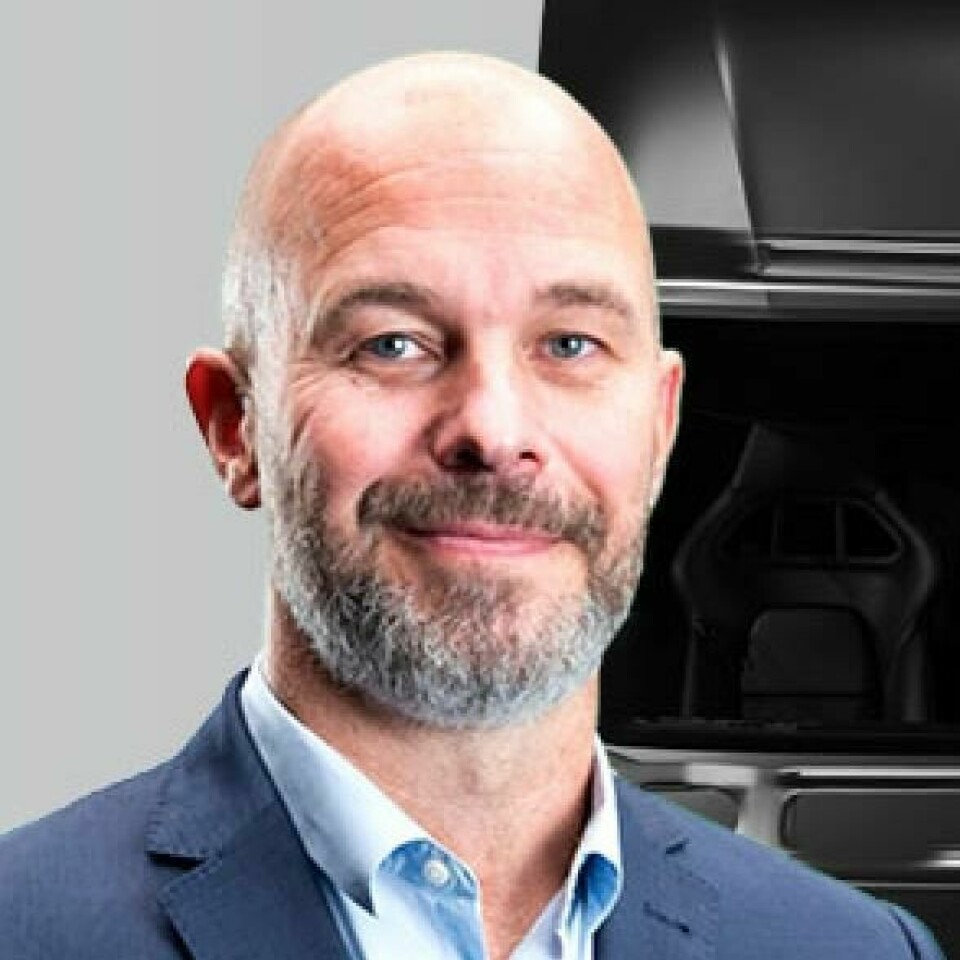
“The battery is a big part of this, and steel, since in average a car contains a lot of steel. So, the focus is really on the materials from a lifecycle point of view and lowering these emissions.
“That’s why the fossil-free steel, where we drastically will reduce/eliminate the CO2 from steel, has attracted a lot of interest from our customers in the automotive industry”.
Improving supply chain transparency
A challenge for carmakers has been the transparency of their supply chain – notably past Tier 2, or 3, it has been difficult to have accurate tracking on the CO2 footprint of components and materials. But now this transparency is very important for them to be audited as low emission or net zero producers of vehicles.
To support this, suppliers are having to manage this process with the onus not just on the production but also the sourcing of materials. In the case for SSAB this includes the ore, scrapped materials as well that the energy source.
“I would say that the carbon footprint will become a design factor in the future, just like stress-strain curves or the forming limit diagrams are design factors and design input that we give to the engineers at the OEMs”
Jonas Adolfsson, SSAB
Adolfsson noted how important this has become for the company and how it will be increasingly important in the future. “It’s always difficult for the OEMs to have a complete picture of the emissions because the car contains a lot of different parts, a lot of different suppliers, and today when they are calculating emissions in a lifecycle assessment, they are using generic figures – generic global figures – for steel or aluminium, and it can differ a lot from supplier to supplier.
“We want to be very transparent, and we’re having detailed discussions with our OEM customers, both to show where we stand and what kind of data we offer, but also so that they learn, so they can ask the same from other suppliers. Because today, unfortunately, it’s not always easy to compare figures, to compare apples with apples.
“We use environmental product declarations (EPDs) which are third-party verified, so we really get that transparency. Also, in our Annual Report we have a big section about sustainability and emissions where we show all the details we can, offering our customers a lot of detail”.
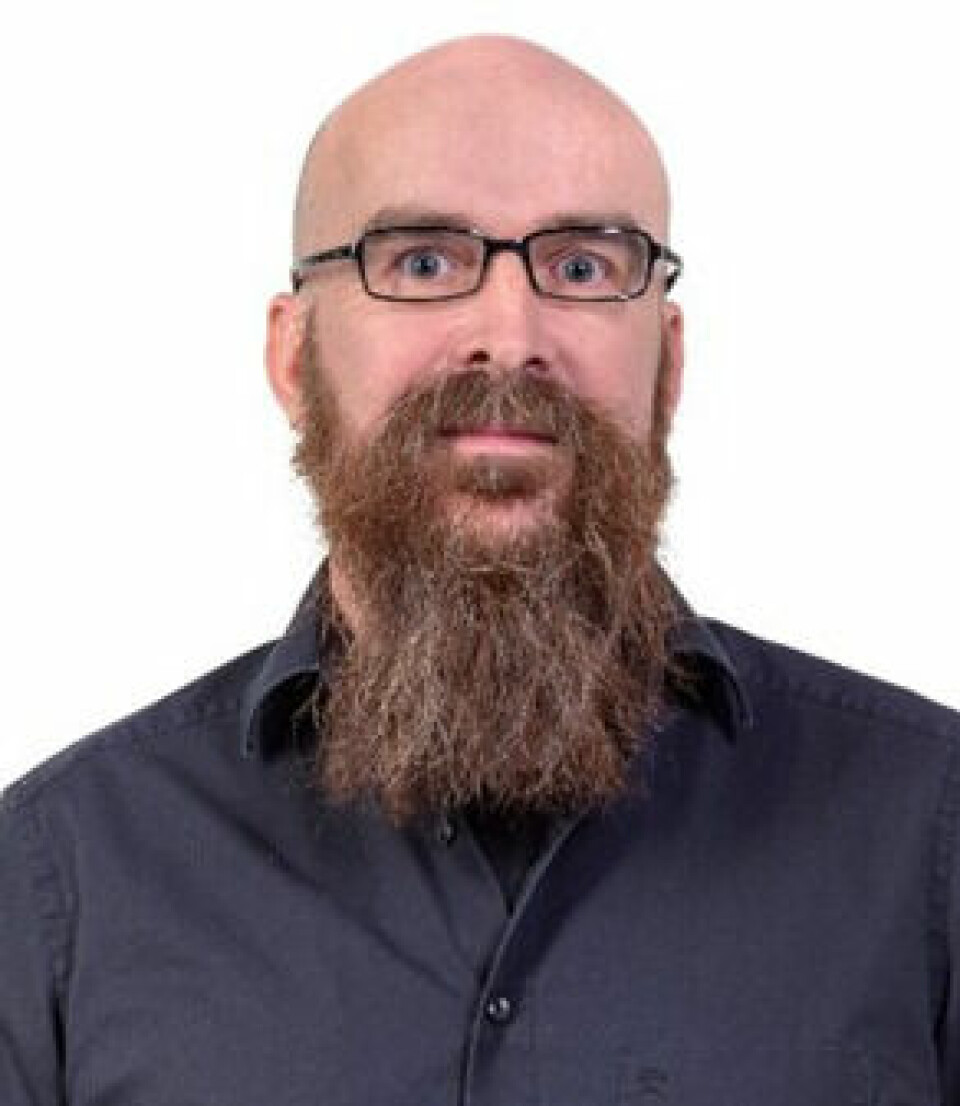
Business Development Mobility Manager, Manuel Otto added: “My personal feeling is that there are still a lot of things to synchronise. Within the industry, the steel industry and on the customer side as well, there are different views coming from different angles when talking to different customers”.
Adolfsson concurred and added: “I would say that the carbon footprint will become a design factor in the future, just like stress-strain curves or the forming limit diagrams are design factors and design input that we give to the engineers at the OEMs. They also need to know exactly what carbon footprint will be when choosing different suppliers or material grades in general. They need to know so that they can design with the lowest [carbon] footprint possible. Because OEMs have set up targets to become climate neutral within 15 to 30 years from now, and to have a climate neutral car you need climate neutral materials”.
Managing complexity, simplifying standards
As with much of the transition to electric vehicles and sustainable mobility there is a steep learning curve for even the most established companies. Creating the required levels of transparency in the supply chain adds another layer of complexity to the manufacturing process.
“We’re all learning day by day and developing our sustainability. It’s the same with our customers. Some are very basic in their requests, while others have now become really deep,” noted Adolfsson. “But you must remember that they are dealing with a wide range of suppliers, so they need to go deep and broad in their questionnaires, so, you have to adapt for every single question from customers,” he added.
Otto also observed how managing sustainability had seen changes in how the automotive industry operates in relation to working with suppliers. “Looking back and remembering how strict an OEM could be with sticking to the specifications, especially if you deliver a commodity, and now looking at the first talks on those sustainability issues, it’s interesting to see that even an OEM can be flexible or must be flexible.
“But it’s getting more synchronised, and the questions are more consistent, but it is interesting to see that not everything is written in stone, as it once was. As Jonas said we are all learning and developing.”
The complexity of all this is a challenge for customers and suppliers alike and is something that needs to be addressed as Adolfsson explained: “When it comes to measuring the carbon footprint there are so many different standards, and they are measuring in different ways making it difficult to compare. Some start with the iron ore and others start at the crude steel. Some stop at the crude steel or at the finished product, so, I think we need a standard specification that everyone works from for consistency and transparency.
Developing fossil-free steels
Producing steel is an energy intensive process using fossil fuels to power the operations. SSAB has been working to produce fossil-free steel since 2014 with a process that utilises direct reduction iron (DRI) and green hydrogen.
Adolfsson explained the development: “We announced in 2015 that we would start producing fossil-free steel with direct reduction and green hydrogen. We have a partnership with LKAB (mining and pellet making) and Vattenfall, which is a Swedish energy supplier, to look at the complete value chain, from iron ore all the way to ready steel, to make that fossil-free.
“We used our research and development plant at Luleå, as a pilot for the direct reduction and hydrogen related processes, where we produced small amounts of fossil free steel. Here we optimised the process, learning and establishing the parameters for bad and good DRIs.
“This has been successful, so, with the HYBRIT development, the company between SSAB and LKAB via Vattenfall, we are now building a full-scale production plant in Gällivare, in the north of Sweden, located close to LKAB to reduce the transportation of materials. That will start operating in 2026, and from that point we will be able to offer our customers fossil free steel on a commercial level. We will have a capacity of 1.3m tonnes of DRI.
“This approach is not actually changing the steelmaking process; we are changing the iron making process, so, how to split the oxygen from the iron ore to get pure iron. Because iron ore is iron and oxygen. And that’s what we do in this direct reduction method”.
He added: “All the downstream activities from crude steel, when you start to alloy it, cast it, hot rolling, cold rolling and metal coating, will be the same as today, except we ensure we are using fossil free energy to power the process. Also, all the steel grades that we can produce today we will be able to offer as fossil-free in the future”.
As a next step, the company has also announced that it will build two completely new steel mills at Luleå and Raahe in the north of Finland. These will be integrated mills, which will remove the process step of reheating of slabs. So, hot rolling starts directly after the slab casting, which further reduces energy usage.
Looking ahead, Adolfsson and Otto both anticipate rapidly growing demand for fossil-free steel from the automotive sector. “Can you make it faster and can we get more?” is now a common question from customers noted Otto, and ramping up production will be one of the next challenges for the company, but the ongoing development and investment in new production facilities means SSAB is well positioned to supply further demand.
Find out more here