NVH reduction for electric vehicle interiors
Brian Pour, president and CEO of Auria Solutions, identifies the increasing importance of electric vehicles as a major factor influencing the development of vehicle interiors and one that will pick up even more pace given recent political change. Mike Farish reports
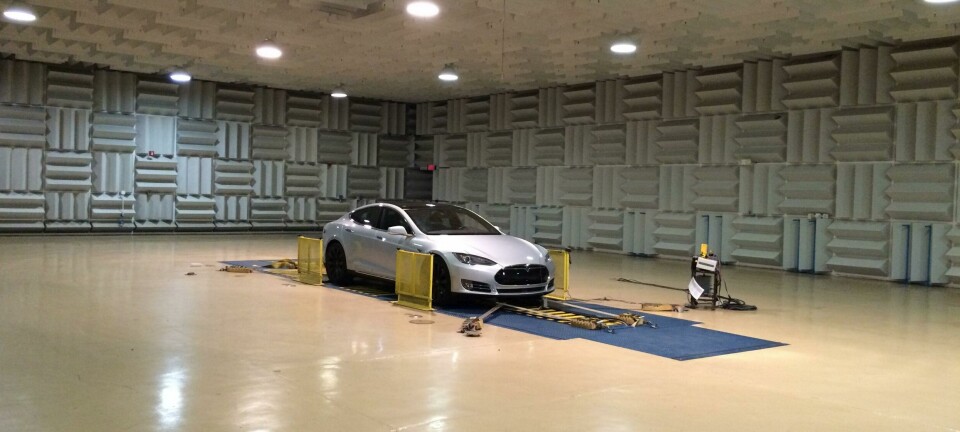
“The incoming Biden administration has already hinted at policy changes that will increase fuel economy standards and further incentivise electric vehicles,” Pour explains. “So, we expect to see increased emphasis on the development of solutions that reduce overall vehicle weight. For Auria, this affirms the direction we have taken since the company was established in October 2017, to develop lightweight acoustical materials and the methods used to apply them.”
Lightweighting the sound deadening
But, as Pour also points out, lightweighting and enhanced acoustical performance are not naturally complementary objectives. Indeed, given that the traditional approach for removing unwanted noise from the vehicle cab by adding more heavy-layer sound deadening material can increase weight dramatically “they conflict.” As such Auria has adopted a twin-track product development strategy to reconcile these objectives.
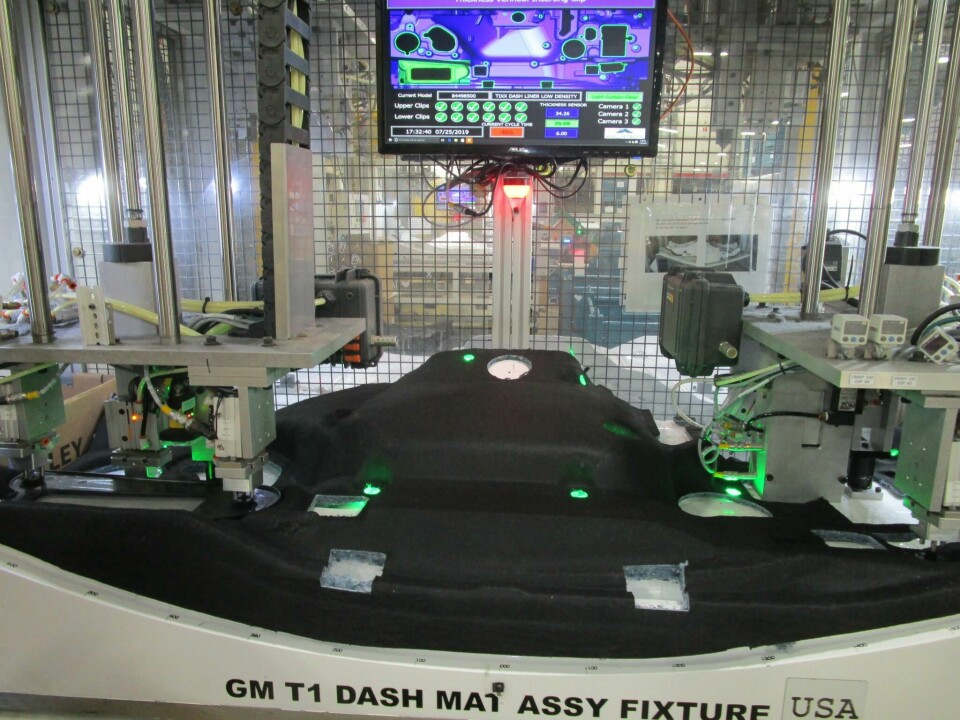
Firstly, Pour says, Auria adopts “a total acoustical systems approach in which we look at the entirety of the vehicle.” As he explains “this allows us to identify where in the vehicle different noise sources are coming into the interior along the RPM (revolutions per minute) curve, so that we can put a system solution in place that will optimally tune a particular vehicle.”
Secondly, Pour continues, Auria is addressing the specific acoustical challenges posed by electric vehicles through the adoption of “component level approach”. The absence of a relatively noisy internal combustion engine, he says, means that sounds that were previously masked such as those of hydraulic fluid movement now become audible. Auria’s approach to solving this issue is to “extend our efforts beyond just stopping the noise where it enters the interior and instead go to the source of the noise in order to encapsulate it with proprietary insulator materials.”
Auria adopts a total acoustical systems approach in which we look at the entirety of the vehicle. This allows us to identify where in the vehicle different noise sources are coming into the interior along the RPM curve”
Brian Pour, Auria
As an example of what he describes as Auria’s “unique approach” Pour cites the dash insulator developed for GM’s full-size SUVs. This application, he states, which was introduced as recently as 2019 combines a highly automated manufacturing process along with a new proprietary lightweight sound-absorbing material blend to provide significant weight saving in a single product. The new unit weighs “approximately 4lbs and replaces the former heavy foam layer product GM used at just under 20lbs.”
The influence of social and political trends
Elsewhere, Pour continues, other current social and political trends are influencing the company’s product development and manufacturing strategies. One such is the need to develop more durable, cleanable and antimicrobial surfaces in the vehicle interior, a requirement driven by increasing demand for ride-share vehicles may well carry as many as a hundred different passengers each.
Another is to produce products from recycled materials, which is a formal objective stated in the company’s Corporate Sustainability Report. Pour says that Auria already produces many of its products from post-consumer resins (PCR), such as plastic drinking bottles, and/or from post-industrial recycling (PIR). These currently include: tufted carpet with 50-50 mix of PCR and PIR yarn; heavy-layer insulator, vinyl flooring and tufted substrate with up to 50% PIR in the first two cases and up to 75% in the third; fibre insulators with up to 75% PCR/PIR; and nonwoven carpets with up to 100% PCR.