Zero Downtime
GM has ambitious plans to implement a zero down time approach using cloud based computing to connect all of its production robots worldwide
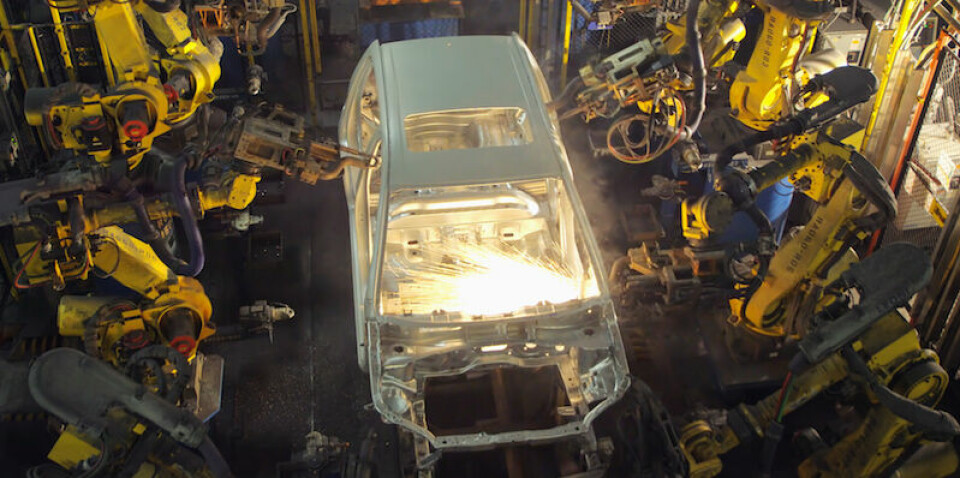
Robots are now not just commonplace items of equipment on automotive factory floors they are absolutely vital to the implementation of automated manufacturing strategies that successfully combine the goals of high speed, consistent quality and the flexibility that underpins product variability. As such their reliability and availability are essential prerequisites to profitable automotive manufacturing.
One major OEM that has been seeking to use the Internet of Things (IoT) approach – in particular 'Cloud' computing – to help achieve those goals for its use of robots worldwide is General Motors (GM). Specifically the company has been working with its robot supplier Fanuc to implement an IoT-based approach to ensuring consistently high equipment availability called Zero Downtime Technology (ZDT).
Someone closely involved with the initiative is Marty Linn, manager for advanced automation technologies with GM based at the company's Global Technical Center in Warren, Michigan – a position that he says also makes him “principal engineer for robotics” with the company. As such, he continues, “my job is to build on the things that we have done for years past to deliver on future strategies.”
Developing predictive maintenance Linn points out the long-standing relationship between GM and Fanuc with the later being a “strategic supplier” to the carmaker. But he also stresses that the relationship is about ideas as well as robot hardware – “we talk with them every week,” he confirms. As such the present project has grown out of conversations that were initiated “several years ago” with the aim of addressing the issue of “predictive maintenance”.
“Robots represent a mature technology that is well-understood and used to replace people in difficult, dirty or dangerous jobs,” Linn states. But at the same time “when you have large numbers of the machines then regular maintenance becomes a significant task that takes a lot of time and effort.”
GM decided that it needed to address this issue, so the carmaker chose to work with Fanuc on a collaborative basis – as Linn observes, “who knows the machines better than the people who make them?” He explains further: “If you want to make something like this work then you have to have an inherent understanding of the equipment, so that if a robot is running you can look at parameters coming from the machine such as torques and recognise the significance of any anomalies.”
According to Linn “the intent is to avoid unscheduled downtime.” Therefore, he explains: “We want to be able to monitor and analyse all the machines that are working on our shopfloors so that we can see to problems before they have any effect and to do so in a non-emergency type of situation.” He says that the company does not have specific figures about robot-related downtime, but that nevertheless that was the area it chose to focus on. Hence the ZDT project that got underway three years ago in 2014.
Cloud computing power Apart from the intrinsic desirability of the objective Linn also says that wider technological developments also facilitated the timing – the one he cites most immediately being the increasing availability of large amounts of computing power via the Cloud. “The ability to store and then anlayse big data items is certainly an enabler,” he confirms, explaining that the key capability is not only to store data on large numbers of robots but also to zero in on particular machines and “run analytics” on them as soon as a requirement is identified. But the fundamental objective remains that of supporting the company's operations at a global level. “It isn't about being able to draw nice graphs of robot trends,” states Linn. “It is about enabling the plants to run in a better safer manner.”
The sheer scale of the project, though, is the factor that Linn identifies as the most challenging. “We are talking about 30,000 robots worldwide,” he explains. “The aim is to connect all of them through the plant floor system, get the data transferred and then be able to analyse that data to identify just one robot in one plant that has a problem and identify just what component of it is the cause. It is about getting the analytics.”
But like any other global initiative this one started at a specific time and place – in this instance with a pilot initiative in 2015 at GM's Orion Assembly plant. Since then the initiative has become pervasive throughout the company's plants in North and South America and moved on to Europe in 2016 with Asia being targeted this year. Altogether GM has 170 facilities in 30 countries and by the end of the first quarter of this year that rate of progress meant that just over a quarter of the company's global roster of robots – roughly 8,000 out of the 30,000 total cited by Linn – had been connected to the system.
Retrofitting challenge All new robots installed by GM are now fitted with ZDT capability, he adds, though Linn also indicates that retrofitting existing machines is a task that the company prefers to avoid if possible. He explains that retrofitting requires some hands-on work at the actual machines and is not just a question of downloading software through the network so ideally it needs to take place during scheduled downtime for the robot. “Someone has to load the software into each individual robot controller,” he confirms.
Nevertheless given the lifetime of industrial robots retrofitting is also a necessity if the capability is to become a pervasive feature the company's shopfloors, so an “active campaign” to do so is underway – with the current focus particularly centred on Europe. The actual retrofitting procedure for an individual machine, he says, takes “about 20 minutes”.
Interestingly Linn also says that there are a few “legacy robots” within the company's global operations – machines that are perhaps 20 or more years old – that simply do not have the on-board computing power to enable them to be retrofitted and hence he cannot hazard a guess about when the company might achieve 100% ZDT capability. But he does say that at the current rate of progress it should achieve a “very high rate maybe 95-98% within the next couple of years.”
Analysing Big Data Very obviously the whole process starts with the robots themselves and Linn says that at that level no particular step-up in technological capability was required. “We are collecting data that the robots already have, but which simply was not being utilised at the level required by the Zero Downtime approach,” he confirms. Some extra capability had to be written in to the robots themselves to collect the data, but Linn makes it plain that the key new “analytical capability” on which the whole system depends is to be found at another level. “The diagnostics to analyse the big data are in the Cloud,” he confirms.
The course the data takes to get there is via the existing shopfloor network to a server within each plant from where it is transmitted straight to the unitary collective Cloud-level database. To be specific it goes to “a private Cloud” that is hosted by computer services company Cisco. The actual amount of data that goes to the Cloud every day is about 1.5MegaBytes per robot, which for the 8,000 robots currently on the system amounts to a daily total of roughly 12GigaBytes. Interestingly Linn observes that as the network continues to expand then local regulations may force GM to add new Cloud service providers, but at the moment that is not an issue.
The data that goes up to the Cloud is analysed on a daily basis, says Linn, and the resulting status information comes back first to Fanuc and then via email to relevant individuals at specific plants. “We get told if we have an issue with particular robot and if someone needs to go to have a look at it,” he confirms.
The consequence of all this is, Linn says, quite specific and identifiable. “We have already avoided over 50 instances where we might otherwise have encountered unscheduled downtime,” he states, confirming that incidents that might have involved unplanned stoppages of six to eight hours have instead been headed off during scheduled maintenance periods.
But robots have had self-diagnostic capabilities for a long time so what does ZDT make possible that was not previously feasible? The answer to that question, Linn indicates, is the ability to carry out daily analysis of individual robot performance that enables minute variations to be detected and trends identified that indicate when a machine is moving towards a possible breakdown well before any serious symptoms become evident.
“If a robot has a certain characteristic of motion and carries that out a thousand times a day then the Cloud-based analytics allow us to look at it over multiple days, so we can detect the most subtle changes,” he explains. Quite simply, he further elaborates, though the machines might have had the ability to detect such changes previously they simply do not have the on-board computing power to enable them to analyse the data and recognise its implications.
Nor, Linn says, could this have been achieved without the Cloud-based analytics of ZDT. “I don't believe it would have been possible previously,” he states. “The ability to look at lots of data over an extended period on a specific item of equipment is what has enabled us to have this enhanced level of analytics and predictability about the maintenance of the equipment.”
(start box)Focus on the future (box head)(image-robot_drive1.jpg caption: The ultimate objective is to enable ZDT to cover all aspects of a robot's fabrication)The automotive industry's absolute need for reliable machine uptime is the key reason why it is regarded as the primary market for ZDT by the technology's developer robot supplier Fanuc. That assessment of the immediate applicability of the system is confirmed by Jason Tsai, vice president of product development for Fanuc America who works out of the company's offices in Rochester, Michigan. “They cannot afford downtime,” he states emphatically.
Moreover Tsai confirms that several other major automotive manufacturers besides GM have already adopted the technology though he says that at the moment they cannot be identified.
Interestingly, though, he does quantify the scale of that wider take-up of the technology quite precisely. Specifically he says that in addition to the roughly 8,000 robots worldwide with GM using ZDT those other users account for at least another 1,200 machines. Nevertheless a further point he makes is that the technology can be implemented if necessary purely at a local factory level with the analytical software running on in-house computing resources – it is not absolutely necessary for the data involved to be sent to the Cloud for processing.
Performance parameters (subhead)But whether the data processing involved is co-located with the robots or takes place remotely Tsai says that two major combined business and technology performance parameters have to be met in order for the system to deliver real benefits and that each was a major focus of development effort. The first is that the system can predict impending problems far enough ahead in order for them to be headed off without interrupting scheduled manufacturing operations. On this count he is again quite specific – “one day” or even “one week” is simply not good enough. Instead, he says, the system needs to be able to provide warnings of potential problems at least “three weeks” ahead in order to be able to satisfy the requirements of the industry.
The second is for “absolute security” of the data involved against any form of unauthorised external access – security that must, therefore, by definition be equally effective in all the areas where the data is present “in the manufacturing operations, in data transfer, in the Cloud”. There must, states Tsai emphatically, be “100% trust” in the system by the users.
Complete coverage (subhead)But though Tsai is confident those goals have been achieved for those aspects of robot operation the system currently addresses he indicates that there is still further development work required to make the technology one that is completely pervasive. The ultimate objective, he states, is to enable ZDT to cover all aspects of a robot's fabrication – “every single component” – and of the processes in which they are involved.
He says this will mean addressing four particular topics: • The robots' mechanical construction• The processes they implement• The wider system in which the robots operate• “Intelligent” maintenance
Nevertheless Tsai does say that the technology is already providing extremely comprehensive analytical and predictive capabilities in several key areas of robot operation. One of them, for instance, is the operation of the reducer that translates the high-speed rotation of the machine's electric motor into necessarily slower-paced motions of the robot arm according to the loading. It is, he observes, a “critical area” with several potential failure modes – even, for instance, something as mundane as “grease contamination” – simply due to the demands made on it during operation, but one that he says, “we can now predict.”
Another concerns the “gear wear” that can result in a “backlash” that can severely impair product quality. Tsai says that the system can make accurate predictions of the likelihood of that occurring for “every single tooth” in a gear ring. (end box)
Pull quote: “We are collecting data that the robots already have, but which simply was not being utilised at the level required by the Zero Downtime approach” – Marty Linn, General MotorsImages: • Fairfax184.jpg caption: So far 8,000 of the company's global roster of 30,000 robots has been connected to the system