North America's rise before a fall?

Global vehicle-makers are investing in their manufacturing operations across the US and Mexico; AMS reviews the latest developments – and how they position the automotive industry for the next downturn
- GM splashes the cash
- Ford shuffles production line-up
- FCA holds back on expansion
- Toyota prepares for mega-platform
- Nissan expands in the US and Mexico
- Honda boosts engine footprint too
- Hyundai-Kia considers the options
- Mazda arrives in Mexico
- BMW makes Spartanburg its greatest
- Mercedes adds to Alabama line-up
- VW expands at Chattanooga
- Volvo arrives in the US
In the aftermath of the 2008 recession, the ‘Big Three’ American car companies, Ford, GM and (before it merged with Fiat) Chrysler, cut 19 plants and their suppliers also made several closures. This was arguably the biggest restructuring of the North American automotive manufacturing sector in modern history. Yet now, with annualised sales of 17m cars and light trucks, and even with the important export markets of China and Russia suffering slowdowns, North America’s automotive sector is again witnessing a major investment boom.
Although low-cost, free-trade Mexico is benefiting hugely from this investment, within the US too, vehicle companies are once again investing, expanding and adjusting their manufacturing footprints. This renewed confidence is evident not only among the ‘Big Three’ but also the German brands, the incoming Volvo, the Japanese OEMs and even Hyundai-Kia.
With the last recession still fresh in the memory, one might ask if all this expansion and investment is wise. China’s summer economic dip may become something more permanent and structural, and with no sign of any resolution of the political uncertainty in the Middle East and Russia-Ukraine, at some point the US economy may well come under pressure. When it does, how will consumers react and what will be the impact on the car companies? Will their renewed investment come to be seen as a folly?
Certainly, the industry has always been highly cyclical, with periods of significantly rising sales followed by downturns in which underused plants are idled or closed and thousands of workers laid off. Yet there are many in the US who think it could be different this time around, and even with additional capacity still to come on stream at new or reconfigured plants, there is even talk of a lack of capacity for both vehicles (especially SUVs, pick-ups and crossovers) and for components. GM’s CEO, Mary Barra, recently told an investor conference that dealing with production bottlenecks in its own plants and in its supply base was one of the major challenges the company faced.
Earlier this year, analyst IHS suggested that North American production would rise from 17m in 2014 to 19m by 2022, with nearly 4m vehicles coming from new plants and production at existing plants actually falling by 2m. Whether that will mean further plant closures remains to be seen; more likely are adjustments in production and gradual reductions of volumes at older plants. However, marginal plants like Mitsubishi’s in Normal, Illinois, will soon be a footnote in history.
Three shifts or two?
To give an idea of the strain on the production base, IHS suggested that in mid-year, close to two-thirds of vehicles made in North America were being produced in factories operating three shifts. Given that full capacity is generally defined as two shifts running at full rates, the plants currently on three shifts will find it much easier to absorb any blip, even if the third-shift workforce might not be so sanguine about their dismissal.
For example, at Ford Wayne in Michigan, where the Focus and C-Max are made, demand has slowed as consumers have switched to newer crossovers, with production dropping from three to two shifts. But at this level, the plant is still highly profitable. One of the reasons for this profitability despite the production cutbacks is the new labour agreement which Ford managed to negotiate with the United Auto Workers union (UAW) in the aftermath of the 2008 recession.
In addition, vehicle companies have invested strongly to make their plants more flexible. Traditional vehicle plants were set up to make one or two specific models and changes to other vehicles were slow and expensive; the spread of mega-platforms, such as Volkswagen’s Modular Transverse Matrix, as well as clever design of assembly systems means that switching to new models can be quicker and significantly cheaper than in the past. Furthermore, the Japanese and European OEMs have switched more production to the US rather than importing vehicles; for example, the Nissan Murano and Lexus ES are now made in North America, as are the Mercedes C-Class and Volkswagen Passat. Some of the production switching will involve plants in Mexico (for example at Audi and BMW), but the US is managing to retain some of this new investment boom for itself, too.
Although much production of small and some compact cars has moved to Mexico for cost reasons, demand remains strong for large SUVs, pick-ups and new crossovers, vehicles which the US factories seem adept at producing. The revival in the US market has maintained many of these factories on three-shift systems, and so far the downturn in the Chinese market has yet to hit North American production. It may do, but OEMs are continuing to invest in the US; having survived one recent downturn, they want to make sure they are better positioned for the next one, whenever that comes.
‘BIG THREE’ GEAR UP FOR GOOD TIMES
General Motors splashes the cash
GM is in the midst of a $5.4bn investment programme. Some $1.2 billion of this is being spent at Fort Wayne, Indiana, where it makes full-size pick-up trucks on a three-shift system, notably the Chevrolet Silverado and GMC Sierra; the investment will come to fruition with the new versions of these, due in model year 2019 and will encompass an expansion to the bodyshop, a new paintshop and a major overhaul of the material and component sequencing centre. In assembly, new handling and ergonomic systems will improve instrument panel installation.
In addition, an investment of $1.4 billion is going to Arlington, Texas, where GM makes its large SUVs, the Tahoe, Suburban, Yukon and Cadillac Escalade. Here, the focus is on a new bodyshop and a new paintshop. The investment was required because GM has been unable to cope with demand for these vehicles since early 2015, despite running three shifts. The Arlington plant can already make 1,200 SUVs a day, and with GM looking to find a way of producing another 60,000 vehicles a year, either a lot of overtime will be required or the new investment will need to come on stream very fast indeed. GM is also investing $877m in a new bodyshop at its Flint Truck plant between 2016 and 2018.
Furthermore, GM has assured the UAW that it will not move small-car production out of the US, making a commitment to keep the Chevrolet Sonic at the Orion plant in Michigan; this is actually the only sub-compact model made in the country and therefore highly symbolic. One of the reasons why GM has been able to retain this vehicle in the US is because the workers of tier-two suppliers are involved in its assembly within the Orion plant, on significantly lower wages than GM’s UAW employees. The company and UAW are due to reach agreement on the next labour contract by the end of September.
Ford shuffles production line-up
The vehicle-maker is concentrating on optimising production across its still vast North American manufacturing network. In 2016, it will bring back its Lincoln Continental model, replacing the MKS which is currently assembled in Chicago; the Continental will be assembled at Flat Rock in Michigan, the former Ford-Mazda joint-venture plant. This factory currently makes the Mustang sports car and Fusion sedan, with the new Continental expected to be built on an extended version of the Fusion platform. Production of the Focus and C-Max is also expected to move from Wayne in Michigan, where production has already dropped to two shifts, but there is no confirmation yet as to where these models will be made in future and what will replace them at Wayne.
North American production will rise from 17m in 2014 to 19m by 2022 – IHS
Nearly 4m vehicles will come from new plants while production at existing plants will fall by 2m – IHS
Back in 2009, Wayne received $550m for its transformation into a centre of small-car production, so it seems unlikely that Ford will want to waste this investment; probably, a new crossover will be made there. Continued investment by Ford in Michigan is certainly on the cards, with a report in June suggesting that it would have to invest more than $3 billion in the state by 2025 in order to maximise its tax credits; in 2009, the company agreed to invest $6.2 billion in Michigan by 2025, with $3 billion committed so far. Some of the investment may be in R&D and engineering facilities rather than purely production, but continued investment in and around Detroit will happen.
Fiat Chrysler holds back on expansion
New vehicle plants or even major expansion in vehicle production volumes may be off FCA’s agenda right now, but improving the efficiency of its existing operations is of great importance. A relatively modest investment of $166m in three new press lines at its Sterling Heights plant, Michigan, will increase stamped parts capacity by 20m per annum. Crucially, this facility supplies many of the large stampings for some of FCA’s most popular models in the US, namely the Jeep Grand Cherokee, Ram pick-up and even the Chrysler 200 compact car.
FCA is also focused on optimising its manufacturing footprint, having reportedly decided to keep production of the Jeep Wrangler in Toledo while moving the Cherokee to another plant, probably Sterling Heights; to maintain utilisation at Toledo, FCA will add a pick-up version of the Wrangler.
ASIAN OEMS MAKE HEAVY INVESTMENTS
Toyota prepares for mega-platform
Across the world, Toyota is investing heavily in production systems so as to make vehicles on its new mega-platform, TNGA, which stands for 'Toyota New Global Architecture'. In the US, one of the first plants to be affected by the decision to invest in new manufacturing systems was the Bodine plant, Tennessee, which supplies all of the OEM’s North American engine blocks and heads. Here, small and efficient production systems have been installed with dies that can be swapped over in just 15 minutes. The factory has been extensively remodelled since the 2008-2009 downturn and is one of three Bodine sites acquired by Toyota in 1990. It is therefore an unusual operation, since Toyota prefers to build its own plants; time and pressure on investment funds in 1990 meant that buying and gradually converting the company to Toyota’s production system was the best way to proceed.
Nissan expands in the US and Mexico
As well expanding in Mexico via a joint-venture plant with Mercedes at Aguascalientes, Nissan is expanding within the US. The OEM’s facility at Smyrna, Tennessee, is now its largest in North America, having produced nearly 650,000 vehicles in 2014. Here, one of the ways in which Nissan is improving efficiency and output is not so much investment in new equipment, but by bringing more suppliers close to the facility, or even inside it. In fact, this strategy replicates a move by GM which is aimed at cutting around $900m a year from its logistics budget by 2016; Magna has built new bumper fascia plants in Lansing, Michigan, to supply the two GM plants there. Nissan has not entirely forgotten Japan even while demand in the US booms; it makes 150,000 Rogues already in the US, but in order to maintain the utilisation of its Japanese plants and benefit from the cheap yen, it will also supply around 100,000 Rogues a year to the US from Japan, as well as 80,000 a year from Korea.
Honda boosts engine footprint too
The OEM has not only expanded its vehicle manufacturing in North America in recent years, for example with a new plant at Celaya in Mexico to produce the Fit sub-compact car but has also invested heavily in its engine production capacity. In Lincoln, Alabama, the OEM has installed 92 robots to more than double the automation of the engine production process to 75%. Castings are moved by robots from station to station, while the workforce has been reduced from 340 to 240, with further job cuts likely as robotics improve in efficiency and the company learns how to get the most from its investment ($71m for the building alone).
Hyundai-Kia considers the options
Both companies are looking at Mexico, with a $1 billion, 300,000-unit plant in Nuevo León planned for launch in 2016, but they may yet expand again in the US, especially if demand for the Hyundai Tucson proves strong, Hyundai having hinted at an increase in capacity for this model.
Mazda arrives in Mexico
Last October, Mazda opened its first full and independent factory, at Salamanca in Mexico. The planned investment was $500m, but by the launch of operations this had grown to $770m with the addition of an engine machining facility. The plant has a capacity of 250,000 units, and at the rate of 1,000 vehicles per day is now turning out Mazda 2s and Mazda3s as well as a model for Toyota while the latter sets up its own factory in Guanajuato by 2019. In establishing its Salamanca plant, Mazda is aiming not only to take a slice of the lucrative US market but to re-balance its global production footprint, which until now has been almost completely focused on Asia.
EUROPEAN OEMS FLOOD IN
Recent years have seen Mercedes, BMW and Volkswagen all expand in the US, as well as in Mexico. Volvo has now confirmed that it will build a factory in the US, and while Jaguar Land Rover appears to have put plans for a North American plant on hold, Aston Martin may well become the next premium European brand to arrive in the region. Having run out of space at its Gaydon factory in the UK, it needs a new facility to build its DBX crossover and might join Mercedes in Alabama; the DBX will share core technologies and components with the GLE and GLS models made there. A final decision on the location will come in the fourth quarter of 2015.
BMW makes Spartanburg its greatest
The German OEM’s decision to expand the X Series made in Spartanburg will increase capacity there to 450,000 vehicles a year and is highly significant. Once the X3, X4, X5, X6 and super-sized X7 are in full production flow from 2016, this will be BMW’s largest factory in the world – bigger than any plant in Germany. Spartanburg exports more than 70% of its output worldwide, making it the biggest vehicle-exporting plant in the US for non-NAFTA markets.
Mercedes adds to Alabama line-up
The German OEM has added the C-Class to the GLE (formerly ML), GLE coupe and GLS (formerly GL) models made in Alabama, while shifting the low-volume R-class which is still made for the Chinese market to AM General in Mishawaka, Indiana, for the economical production of just 12,000 vehicles a year. On the negative side, a worrying issue for Mercedes is that it has the highest hourly labour costs of all the major vehicle-makers in the US. The Center for Automotive Research in Michigan found that Mercedes workers in Alabama earned $68 an hour, versus $38 at Volkswagen Chattanooga plant and $58 at GM, $57 at Ford and $48 at FCA. The Japanese and Korean OEMs also pay $40-50 an hour, so the differential means that Mercedes has to maintain its premium status and pricing; this may also explain why it decided to make its small cars for North America in Mexico at the joint plant with Nissan in Aguascalientes.
Volkswagen expands at Chattanooga
VW has been a major investor in the US in recent years. It has had an operation at Puebla in Mexico, making the Beetle and Golf, for many years but in the US it now has a plant at Chattanooga, Tennessee, where it produces the US version of the Passat and will also add a new seven-seater SUV based on the CrossBlue concept. This model will come into production during 2016, after an investment of $600m in a factory extension which includes a new bodyshop and will add 2,000 jobs. VW’s growth in the US has been accompanied by major investment at its suppliers, for example Gestamp, which is expanding its factory in Chattanooga to produce body panels for the new SUV, and also to install a new hot-stamping line to make bumpers, A- and B-pillars and other structural components. Another major supplier expanding nearby is Chinese company Yangfeng, which will supply floor consoles, instrument panels and boot trim for this SUV from the end of 2016.
Volvo arrives in the US
The latest vehicle manufacturer to announce investment plans in the US is Volvo. Earlier this year, the Swedish OEM (now owned by Geely) confirmed that it would open a plant at Ridgeville, South Carolina. It will invest around $500m, receiving $200m of tax breaks along the way. The first vehicles will come off the assembly line in 2018 and the new factory will have an annual capacity of 100,000 vehicles year. Volvo clearly has great ambitions for this factory, as it plans to double the workforce to 4,000 in the long term; it is not yet known whether this will be for increased vehicle production or the addition of engine manufacture.
This new plant is part of the globalisation of Volvo’s operations, during which it has moved away from a Europe-centric focus with its new owners funding the construction of two vehicle assembly plants and an engine factory in China. The US plant will bring Volvo’s capacity to 800,000 units a year worldwide, with scale economies likely to mean that the production focus will be different in Sweden, China and the US; the most obvious candidates for the US are some of the new 60 series models, probably the XC60 SUV and S60 sedan, possibly including the long-wheelbase S60L which is currently imported from China.
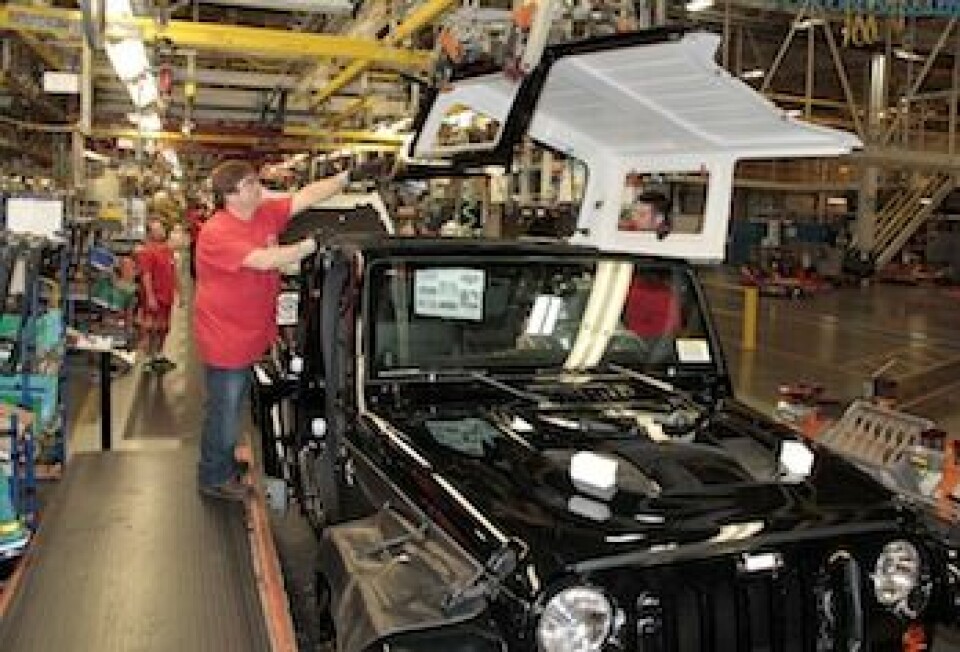
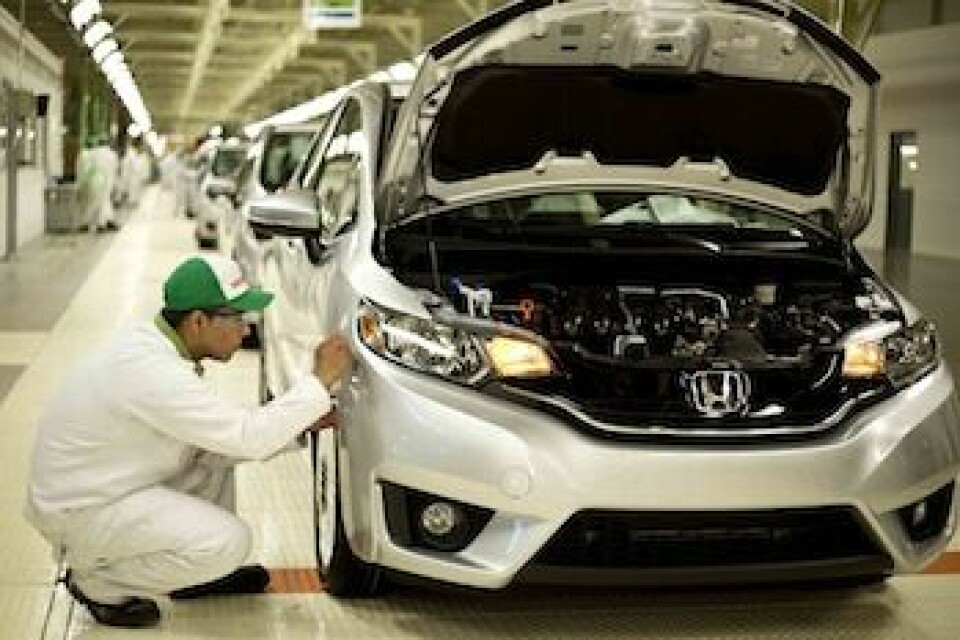
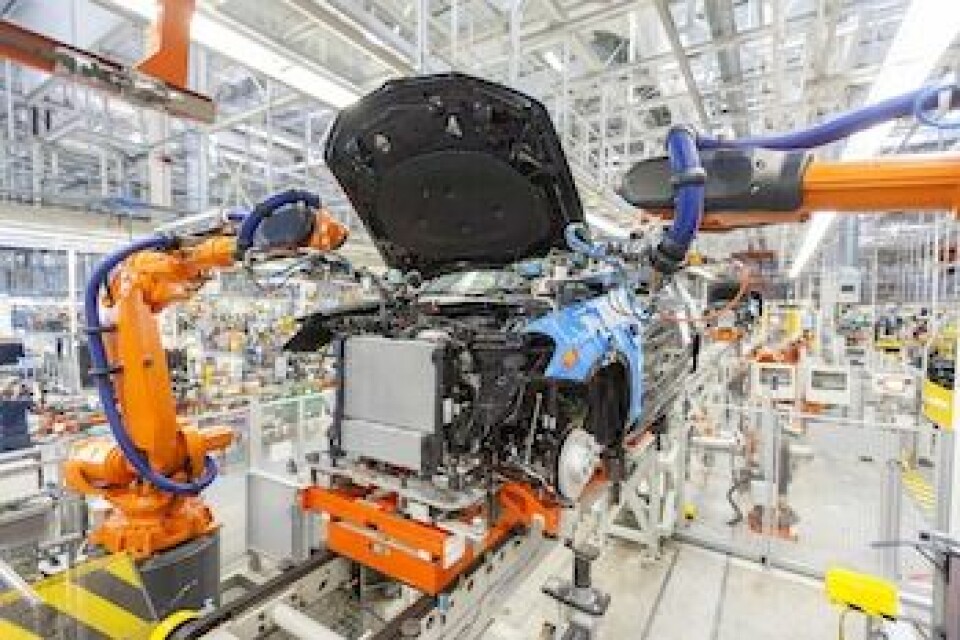
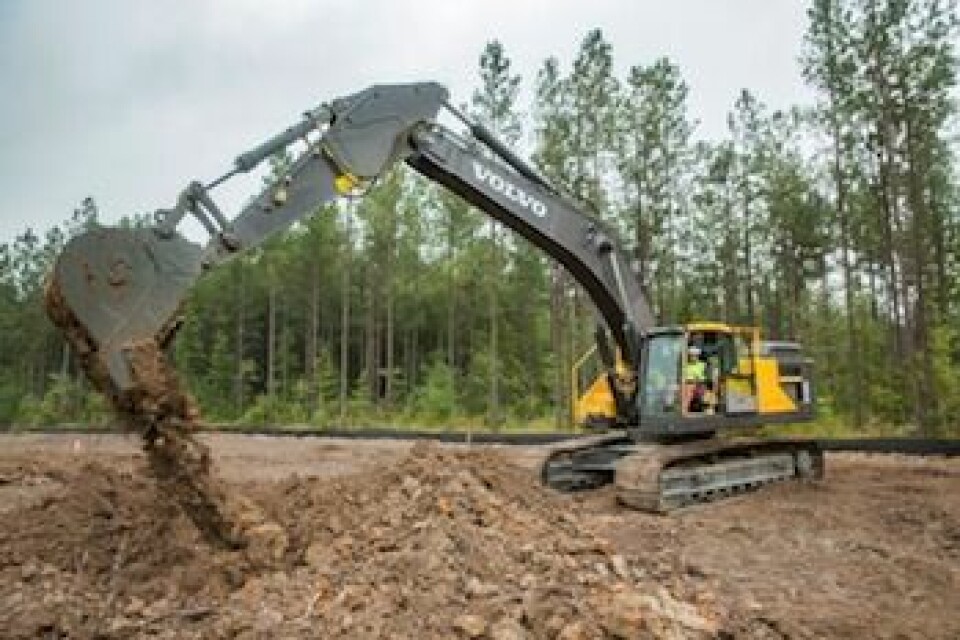