Painting sideways
With its new paintshop at Mladá Boleslav, Skoda is bringing some unique approaches to conveying and curing
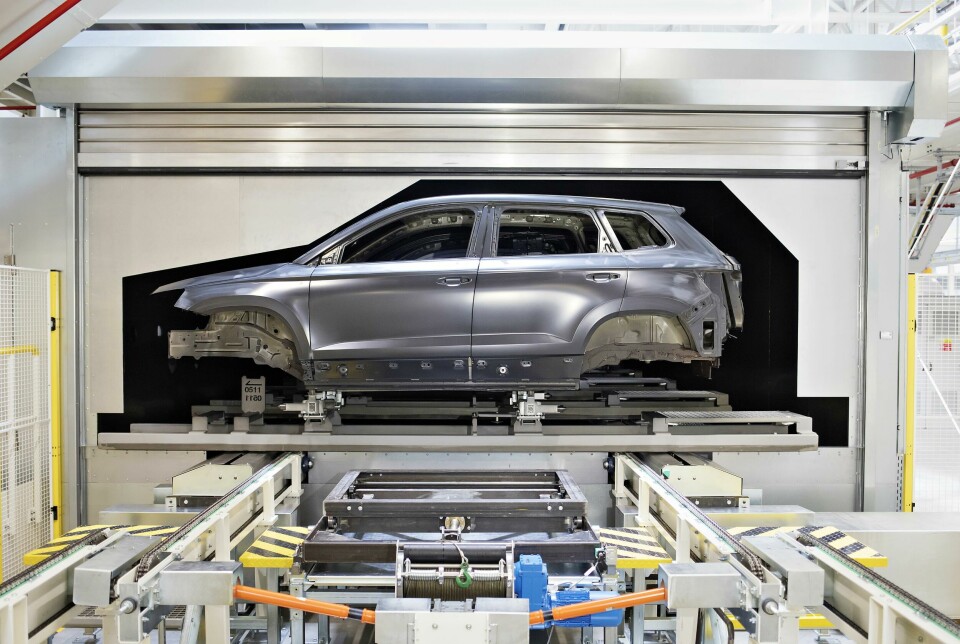
The northern rim of the Czech Republic is home to one of the newest automotive paintshops currently in operation and, according to its operator, it is also one of the most innovative in the world. The €214.5m ($238.78m) installation at Skoda’s Mladá Boleslav plant, which began operating in August of this year, has a total floorspace of 25,094 sq.m and will process 168,000 car bodies a year with a maximum possible daily throughput of around 700. This boosts the total painting capacity of the plant to 812,000 vehicles a year, since it will supplement, not replace, the existing paintshop resource. At 35 metres in height, the structure is also the carmaker’s tallest building.
More pertinently, the key hallmarks of the installation are its high levels of automation, commitment to energy saving, and environmentally benign technologies. On the first of those counts the installation will, most obviously, operate 66 robots. On the second, relevant figures compared to existing levels for similar work include a 20% reduction in power consumption, mainly due to what Skoda describes as a unique paint drying procedure; a 17% reduction in paint usage compared to previous consumption levels; a 36% reduction in emissions of organic substances; and obviation of one complete drying cycle.
Specialist technology suppliers involved in the design and development of the facility include Dürr, Eisenmann and Geico. The Karoq, Scala and Kamiq currently pass through the new paintshop, and Skoda is said to be working on an electric car that could also be painted in the new installation. In fact, the company is adamant that the paintshop could, in principle, be made to handle any of its vehicles.
Innovation and rotation
The painting sequence that vehicle bodies undergo seems fairly conventional. Skoda identifies nine stages in the overall sequence from the entry of bare metal bodies from the plant’s welding shop to their exit to subsequent assembly operations. Innovation, at least in comparison with previous Skoda practice, begins with the initial phosphating process that involves complete immersion and 360-degree rotation of the car bodies in a tank of the phosphating solution. The company states that this is a new development, though it also acknowledges it is playing catch-up as similar rotation systems are commonly used around the world.
An identical rotation of the car bodies is also employed during the catophoretic coating process. A feature of the high degree of customisation that the paint line can accommodate is that the angle at which car bodies can submerge into or emerge from the immersion tank is variable according to the demands of each body shape.
The subsequent oven drying process lasts for 56 minutes at a temperature of 180°C, and in addition to curing the cataphoretic coating, it also performs the same function for all the adhesives involved in the welding operations that take place prior to the bodies’ introduction to the paintshop.
But this first curing stage is also where a genuine innovation comes into play that Skoda claims is unique across the complete global automotive manufacturing industry. That is, quite simply, that instead of entering these and all subsequent baking ovens in a perpendicular manner – i.e. front first – the car bodies are angled round by 90 degrees so that they do so transversely – i.e. sideways.
According to Skoda, this seemingly incidental detail in fact has quite significant implications as in each of the drying cycles in the whole process the hot air in the ovens flows into the vehicle bodies through the engine compartments and window apertures. In consequence, the company says, the drying process takes place in the direction away from the sheet metal and not from the top layer down. This helps shorten total drying line length to around 100 metres or about half the length that would be required otherwise.
Balancing manual and automation
The following operations morph from those that are initially human-centric to a mix of human and automated, then to ones that dispense almost entirely with human involvement. Inspection and remediation routines rely entirely on human vision for fault detection and manual procedures for any necessary remedial work. The aperture plugging is again manual but with the vehicle bodies manoeuvred automatically to orient them appropriately for ease-of-access by the personnel involved. The plastisol application is, however, carried out almost, but not quite, completely robotically with human operators applying finishing touches in zones that the robots cannot reach effectively, such as the area where the rear lights are fitted.
The degree of human involvement in inspection routines in the paintshop is nevertheless one of its most marked characteristics. Skoda stresses, though, that these are supported by appropriate technologies and that more automated procedures will be implemented in due course. Quality inspection is implemented using state-of-the-art devices such as spectrophotometers, fluorescence spectrophotometer and ultrasound devices for measuring of layer thickness, and automatic inspection systems are still being developed and tested, but the company adds that the structure of the equipment of the new paintshop is ready for application of these systems.
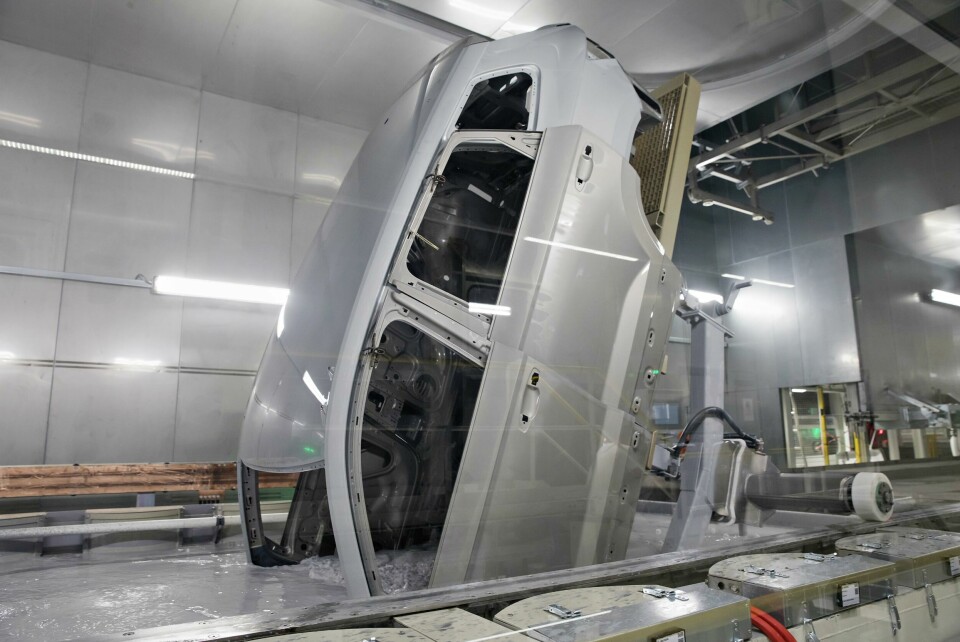
Thrice-baked bodies
The painting process itself then follows, with four primer colour options – white, black, grey, red – supporting up to 17 final water-based paint colours that may or may not also incorporate metallic or pearlescent effects. The clearcoat is a two-component solvent-based polyurethane material. The drying cycles that occur as part of the painting process are 40 minutes at 160°C after primer application, 15 minutes at 85°C after colourcoat application and finally 50 minutes at 140°C after clearcoat application. Hence there are three full-scale oven-bake procedures in the complete process plus the quick intermediate drying cycle.
As such there is only “partial material setting” of the colourcoat before clearcoat application. Compared with previous practice, Skoda says that it has entirely skipped drying of plastisol (PVC) sealing as a separate procedure. The company adds that the flexibility of the installation is such that no batching is involved and that each successive vehicle travelling through the paintshop can be given a different paint scheme to the one preceding it with no interruption to the pace of throughput.
Moreover, Skoda is confident that the whole process achieves very high levels of efficiency and innovation, stating that ‘in the area of anti-corrosive coating the application of the turning conveyor system reduces transfer of bath material. In the case of exterior coating instances, included is the use of state-of-the-art robots with an integrated seventh axis, which allows the reduction of overlapping of paintcoats by providing optimal access to the car body. Furthermore the use of ECOBELL 3 atomisers ensures a maximum paint loss of 10 millilitres during paint exchange.’
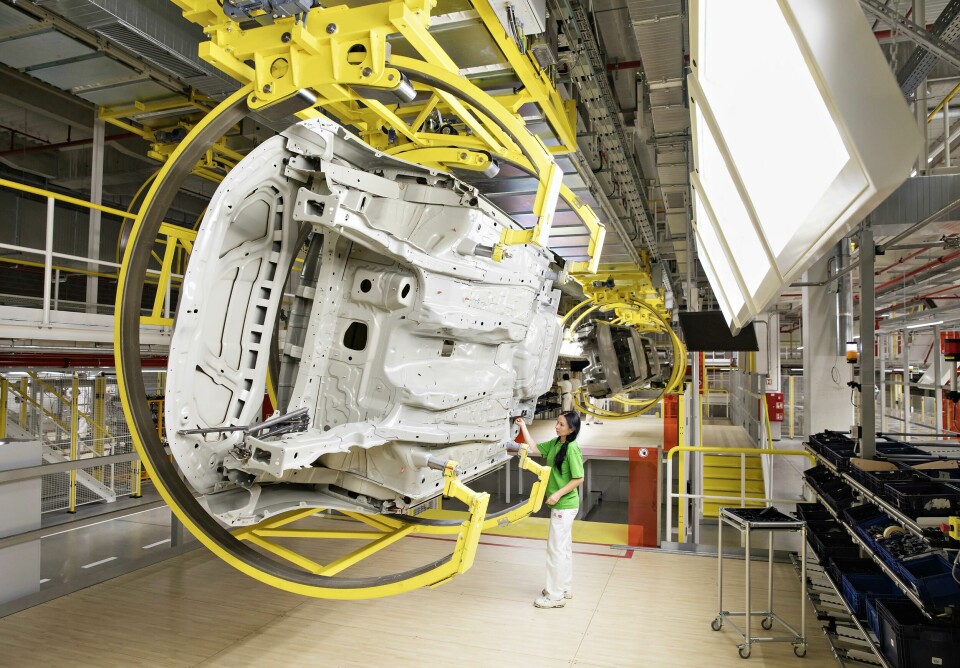
In addition, dry separation of overspray utilising limestone is used to obviate the creation of waste paint sludge. Indeed, Skoda pinpoints the fact that this dry separation of excess paint integrates both the reduction of energy consumption and elimination of waste production as one of the key attributes of the whole paintshop. Quite apart from the way the vehicle bodies are oriented when entering the drying ovens, those installations also employ a clever procedure to utilise their own waste products to enhance their energy efficiency. Volatile substances produced in drying are exhausted from the ovens and subsequently incinerated at 700°C producing water and carbon dioxide. The thermal energy generated in this process is then used for heating the ovens.
In summary, Skoda believes the whole installation represents a major step forward for the company in all aspects of its operations from product movement and manipulation through its levels of automation to the energy and environmental efficiencies it achieves. The equipment of the paintshop also includes, for example, an autonomous conveyor system for individual car bodies on the pre-treatment line and application of the primer, which allows the selection of process parameters individually for each vehicle. Other advances of note are the transverse dryers heating up the inside of the car body, the ergonomic car body turning suspensions for application of PVC, robotisation of sealing of panel parts, dry separation of paint in spray booths and cleaning of waste air from spray booths eliminating volatile organic compounds.”