Lamborghini puts the AI in paint
Lamborghini’s chief manufacturing officer Ranieri Niccoli speaks to AMS about the key features of the company’s new paintshop in Sant’Agata Bolognese
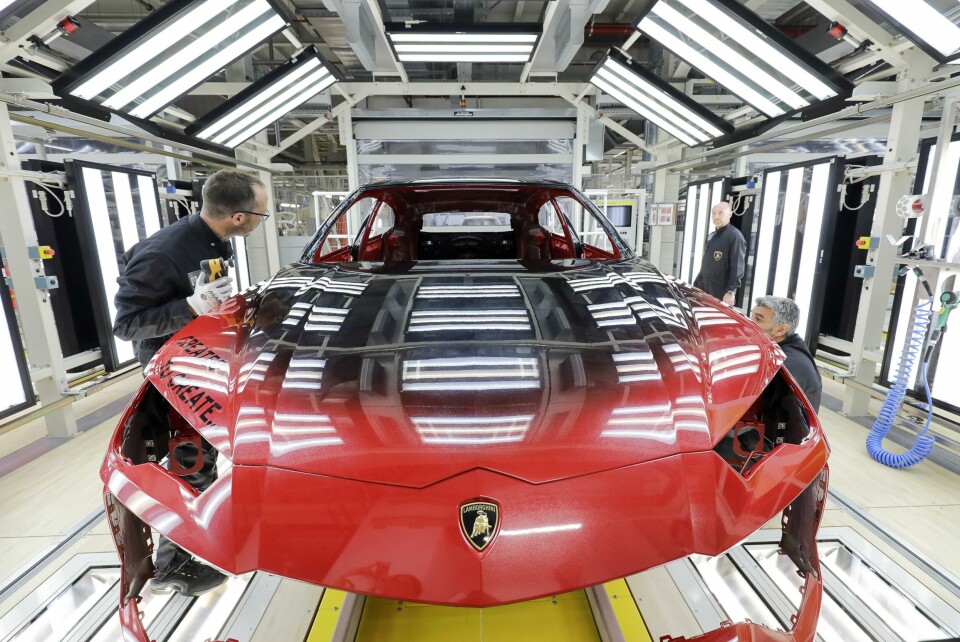
In the middle 2019, Automobili Lamborghini opened a new paintshop at its plant in Sant’Agata Bolognese, in the north of Italy, specifically for its Urus Super SUV. It describes the facility as bringing the principles of industry 4.0 (i4.0) to automotive painting, and as the ‘first in the world’ to apply artificial intelligence (AI) to that application. The aim is to satisfy stringent demands for both painting quality and versatility, allowing customers to specify vehicle colours from an ‘infinite’ range of options.
Those objectives are confirmed by Ranieri Niccoli, chief manufacturing officer of the company. “The key feature of our new paintshop is total flexibility related to both the products and the paint processes,” he states. “This allows us, for instance, to paint both the body and also hang-on parts in one line to ensure perfect colour matching between all parts. To make this flexibility happen, all equipment, such as workstations and ovens, is used in a modular way by different processes in an optimised space.”
As Niccoli further explains, the basic configuration of the facility as well as the technologies it employs contributes to the overall strategy. “There is no strict line flow nor a predefined, fixed sequence of process steps and workflows,” he says. “Instead, a dedicated sequence and flow is created for each specific customised car configuration”. As such, he continues, “there are no lines but single manual and automatic workstations, which allow complete flexible operation times related to the specific work content and process needed for a particular vehicle.”
One capability this facilitates is that a car body can be run multiple times through the paint lines to enable the application of multi-layer paints in support of vehicle customisation.
None of this would be possible without a highly sophisticated control capability which, Niccoli confirms, had to be specially developed to meet the paintshop’s requirements. “Because this is the first paintshop to follow this concept of complete flexibility, there was a requirement to develop a complete new software solution to steer the internal and external flows, processes and production times,” he states. He adds that, in comparison with what have previously been regarded as state-of-the-art systems, a key enabling factor is that the logic to control the flows and processes is no longer at programmable logic controller (PLC) level. Instead, “all the intelligence of the paintshop” is inside the overall manufacturing execution system (MES) with actions at PLC level restricted to those based on information and targets received from the overall control system. The system maintains a memory of each process carried out, calculates the time needed for each vehicle and ‘learns’ to program the subsequent steps based on past experience, for example, the quantity of a particular colour needed to paint a vehicle.
Furthermore, says Niccoli, beside this new overall concept, the paintshop at Sant’Agata Bolognese also represents a break with the first-in, first-out (FiFo) flow concept that has previously been standard practice for paintshops. “Due to a huge spread in the overall lead-time of the customised bodies, the paintshop process and the related lead-time is the master for the production planning of the whole plant,” he explains. “This means that the trigger for the bodyshop start, the call-off of bodies from the warehouse in front of the paintshop and the continuous optimisation of the flows and sequences inside the paintshop is effected by the overall control system.”
But innovation is not confined to product flow and control technologies. It is also evident in the physical configuration of the new facility. “A difference between a standard paintshop and the new Lamborghini installation is the usage of a centralised, full automatic highbay warehouse instead of buffer lines after each process step,” states Niccoli. “By using a centralised buffer concept the number of buffer places is reduced.” Furthermore, the racking system of the warehouse allows the stock of bodies and hang-on skids to occupy a minimum of space, which also has an important implication for energy efficiency. “It reduces the overall footprint of the building, which leads to lower energy consumption for the air conditioning,” he explains. The company estimates that the facility achieves a 30% reduction in footprint with respect to a comparable painting plant.
In practical terms, the paintshop has to combine fully automated exterior painting with mixed manual and automatic processes, and even the possibility of painting bodies completely manually. Some 95% of all the materials used to provide vehicle colours are water-based. “The tradition of Lamborghini is the creation of customer satisfaction by producing individualised cars by our specialists in the finest handcraft,” explains Niccoli on the importance of manual painting procedures. “One of the challenges during the design phase was the implementation of probably the most innovative small series paintshop in the world, inside a handcrafted environment.”
In consequence, Niccoli confirms, robots are utilised in just two particular areas: in PVC sealing on the underbody of vehicles and to ensure optimal sealing on corrosion-critical areas with poor accessibility; and for exterior painting in primer, basecoat and clearcoat to ensure process stability for series colours.
Niccoli confirms that the actual paint application technologies involved are as modern as possible. “For painting primer, basecoat and clearcoat, we are using electrostatic bell application with a direct charging system and high-speed turbine,” he states. “This reduces the overspray to a minimum. There was also a special development of a bell cup, which allows us to paint exteriors and interiors as well as hang-on parts in the same tact by the same robot.”
Another unavoidable element of ‘hard’ automation is, of course, oven-bake curing of the paint layers. Niccoli says that a particular focus in the design of the paintshop was environmental protection and the conservation of resources, and that this is reflected in both the hardware and processes involved in paint curing. “That is why the curing of PVC sealings and primer paint is combined in one oven,” he states, though he adds that there is an additional intermediate oven between basecoat and clearcoat application as well as ovens for curing the final clearcoat layer.
The overriding aim of flexibility is also supported by the fact that there is not just one single oven but four modular ovens, each one independent of the others. “Each oven has one heat-up tact and one holding tact,” reports Niccoli. “Each can run with different temperatures in the range 80-165°C, which means there is no dedicated oven for primer, topcoat or hang-on parts.” But after the ovens there is a single centralised, modular cooling tunnel.
In addition, the design of the ovens follows a new concept. “The oven modules are directly heated, which allows a fast adjustment of temperatures, saves energy and also leads to a stable process in different loading conditions.” Furthermore, the exhaust air of the ovens is treated by the same centralised air purification system as the exhaust air of the paint cabins.
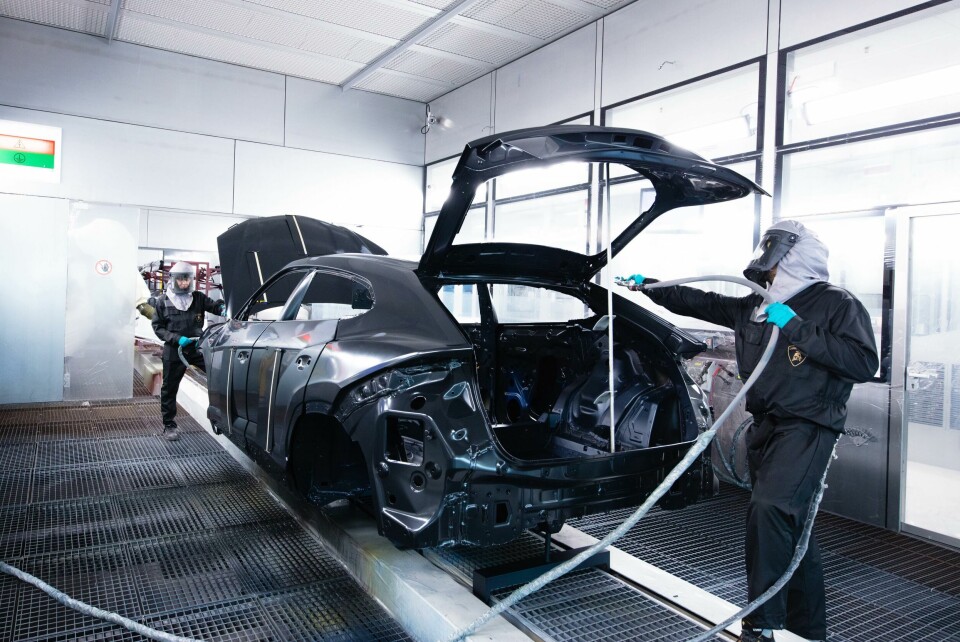
“There is an air flow cascade concept which means that conditioned air is first supplied to the workstations to guarantee a perfect environment for our employees,” says Niccoli. “As a last step, the air is sucked in by the paint cabins’ air supply system, reconditioned and used for the downdraft inside the main paint lines. The control system recognises if it is better to use external or internal air to minimise resource consumption.”
In the automated paint cabins, 80% of the air flow is reused, while 20% of the air, as well as the exhaust air of the manual paint cabins, is sent to a solvent absorption system that collects and concentrate the solvents from the exhaust air flow. “This solvent, as well as the exhaust air of the ovens, is treated by a post-burner system of the latest generation and the heat of the post-burner system is used to heat the ovens,” reports Niccoli. “The remaining heat of the post-burner system, as well the heat or in summer time coldness collected by the heat recovery systems of all the exhaust air of the paintshop, is then reused for conditioning incoming air.”
Niccoli says the new paintshop completes Lamborghini’s strategic plant expansion project for the Urus, which has just reached an output of 5,000 vehicles a year and has seen the total built-on area at Sant’Agata Bolognese increase from 80,000sq.m to 160,000sq.m. The facility will ultimately employ some 200 people, about half of whom were already on-board when it started operations, at which point total employment at the site was 1,750 people. Moreover, as Niccoli also makes clear, the installation is very much an embodiment of Lamborghini’s own vision: “The design concept was developed by Lamborghini and together with an external technology supplier both the detail design and realisation were completed under our responsibility.”