An industry up in the air
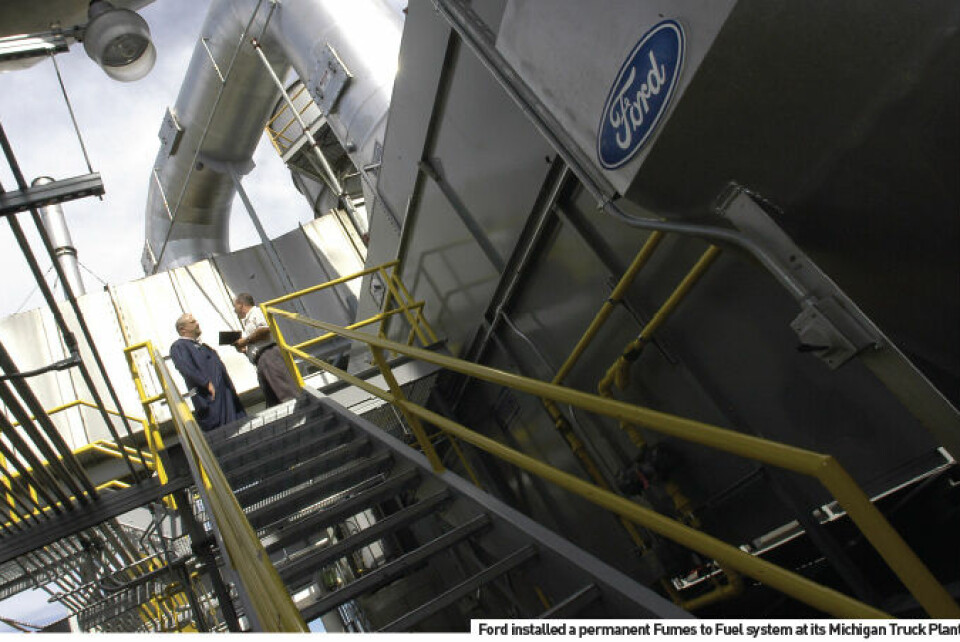
The paint shop accounts for almost all the VOCs coming out of a car plant. AMS considers the range of air quality legislation around the world and the ways that vehicle manufacturers are minimising the release of VOCs into the atmosphere
Stricter air quality regulations, as well as health and safety considerations, mean that emissions control from assembly plants is big business in the automotive industry. The biggest area of concern is the paint shop, where manufacturers have to prevent the release of volatile organic compounds (VOCs) into the air in order to avoid ground-level ozone formation. New European legislation has meant huge investment across the region in waterborne paints, but abatement systems are still needed to bring VOC emissions down to acceptable levels. In the US, requirements vary depending on the region. In some parts of the developing world legislation is being considered for the first time.
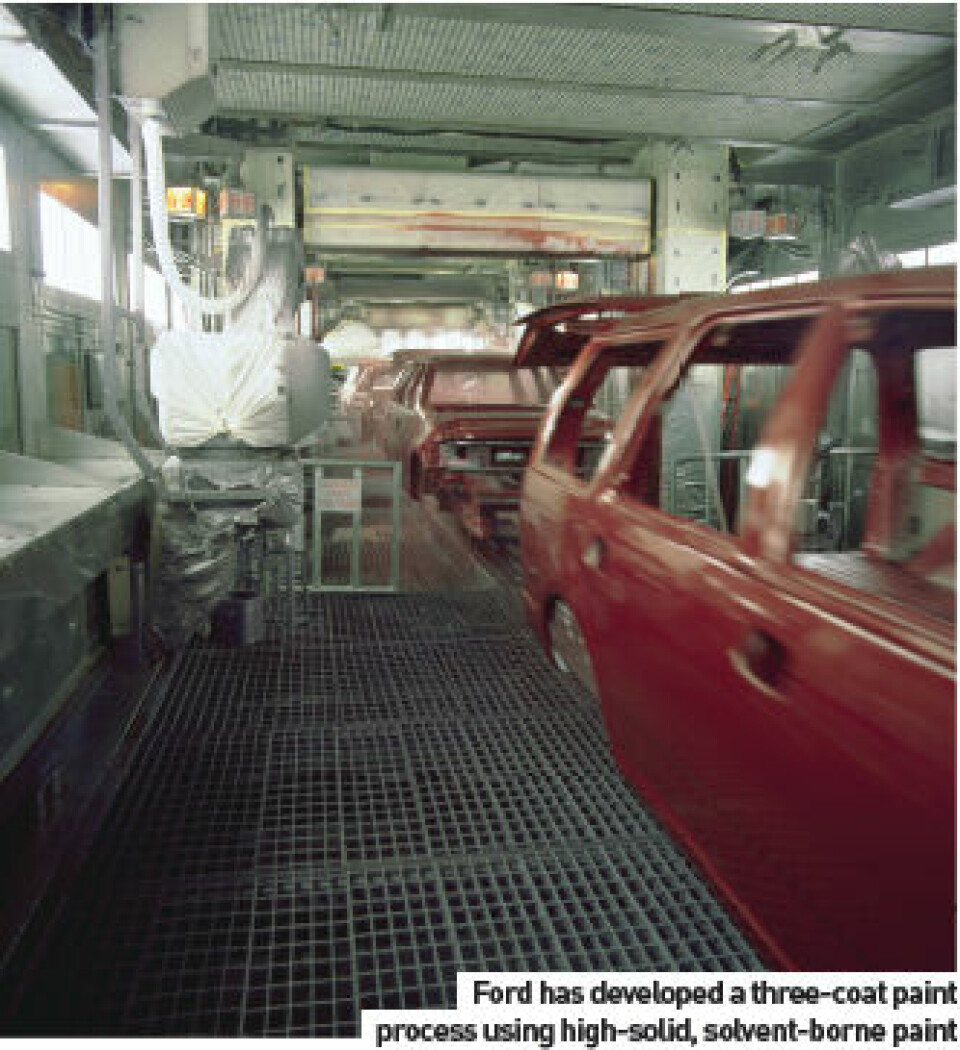
Damage limitation
The paint shop is the most environmentally damaging area of a car plant, accounting for 60 per cent of an assembly plant’s energy use and almost all VOC emissions. According to Tom Piskor at the CMM Group in Wisconsin, the environmental controls in a new paint shop would typically account for between 5 and 10 per cent of the total investment in the facility. The danger to the environment comes from volatile organic compounds (VOCs), which when released into the atmosphere react with sunlight to create ground level ozone. This can lead to respiratory problems. The type of controls vary depending on the location of the plant and the amount of VOCs produced.
“Before we put any abatement on the paint plant we try to reduce the VOCs in the process,” says Ed Piasecki, Director, Regional Operations and Abatement, GM Environmental Services. GM opts for high-solid coatings that produce little waste and an efficient electrostatic application that reduces the amount of paint used in the first place.
Other examples include BMW, which has introduced the Integrated Paint Process at the Mini plant in Oxford. The process eliminates the need for a primer coat application, which results in three layers of coating instead of BMW’s traditional paint application process that has four layers. Similarly, Ford has developed a three-coat paint process (instead of it traditional five-layer process). It chose a highsolid, solvent-borne paint, that it says produces fewer VOC emissions than current waterborne and solvent-borne paints. Powder coatings are also being used extensively in the automotive industry. They can be solvent- and therefore VOC-free, and they have the added advantage that any paint that does not stick to the vehicle can be fully recovered and reused, unlike liquid waste, which has to be separated from water and taken to landfill.
New European legislation
The introduction of new legislation in Europe has resulted in significant investment in paint shops. New legislation came into force in October 2007, but as recently as 2003, around 50 per cent of European paint shops would not have been compliant.
In Europe there are two directives related to the licensing of paint shops – one from 1996 and one from 1999. The 1996 directive (IPPC-Dir, Council Directive 96/61/ EC of 24 September 1996 concerning integrated pollution prevention and control) sets single standards across the European Union for environmental permits, the requirements of licensing processes and the content of the licensing. The directive does not set any fixed emissions limit values, rather it requires that plants are built and operated according to best available technologies (BAT). Dr Michael Mrowietz, head of environment and workplace safety at Volkswagen, says that there has been a huge amount of discussion about what actually constitutes the best-available technology. This discussion between the environmental authorities of member states and affected industries has been coordinated by the IPTS (Institute for Prospective Technological Studies) in Seville, Spain, and it has been up to them to conclude exactly what BAT constitutes in a BAT Reference Paper (BREF). The conclusions relating to paint shops were agreed last year and will be published shortly. To comply with the directive, manufacturers had until October 2007 to make sure their paint shops were using best available technologies. The second directive that is relevant to paint shops is the so-called Solvent Directive (SED – Solvent Emission Directive, Council Directive 1999/13/EC of 11 March 1999 on the limitation of emissions of volatile organic compounds due to the use of organic solvents in certain activities and installations). Among other things, this sets out specific emissions limits.
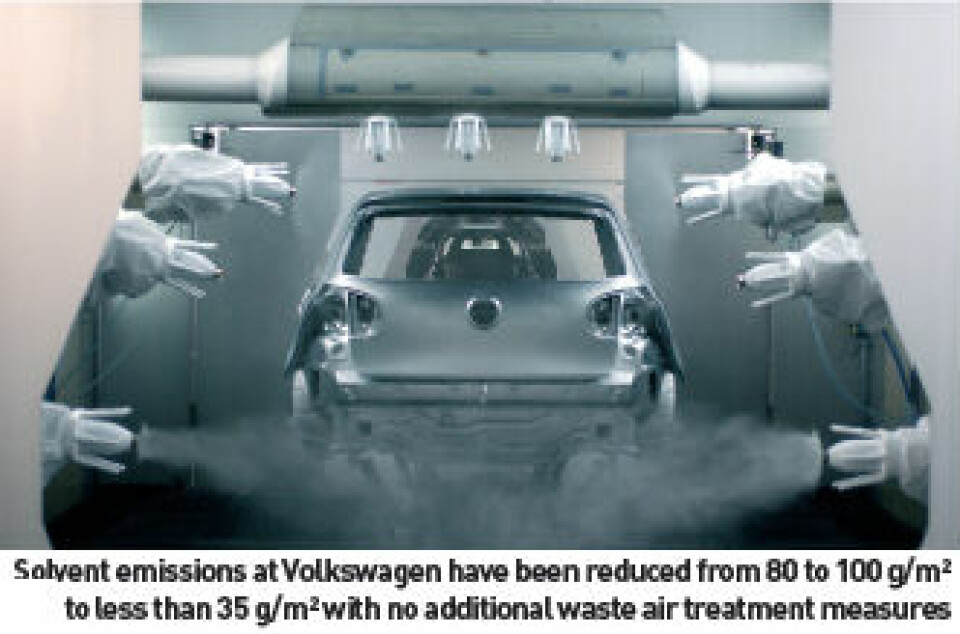
For automotive paint shops, permitted solvent emissions are relative to the size of the vehicle body. They are expressed in grams of solvent per square metre of vehicle surface. For plants that were established before 1999, permitted solvent emissions are 60 g/m². For new plants and those built after 1999 that value is reduced to 45 g/ m². This level also had to be met by October 2007. “In relation to BATs, however, these limit values are minimum requirements. When BATs are used in paint shops, much lower values are achievable and, therefore, need to be reached ( between 10 and 35 g/m²),” says Mrowietz. The member states of the European Union have incorporated these requirements into national law so there is now a common minimum standard for the licensing of paint shops. In Germany there were already strict licensing requirements and specific emissions limits before the introduction of the IPPC directive. Since the beginning of the 1990s all paint shops have had to emit less than 35 g/ m² VOCs. Germany, along with Sweden and Austria, had led the sector for many years. The current European Union legislation brings the other member states up to speed, explains Mrowietz.
Regulation outside Europe
Air pollution in the US is controlled by the Clean Air Act, which is enforced by the US Environmental Protection Agency (EPA). The EPA decides whether an area is an ‘attainment area’, which has clean air status, or a ‘nonattainment area’, which does not. A non-attainment area would be California, for example, and here there are limits on the actual volume of VOCs that can be released into the atmosphere.
In Japan the same rules apply as in Europe but in China solvent emissions are still receiving attention from environmental authorities. The main air pollution problems there are caused by nitrogen oxide and sulphur dioxide emissions from the old coal power stations and heavy industry. “We believe that there will be changes here in the next five years, and that emissions legislation on VOCs will be developed,” says Mrowietz.
He goes on to explain: “A global comparison is difficult because emissions limit values, where they are applied, are defined in different ways. Also, we only feel familiar with the legislation in those countries in which we have plants. Generally speaking, however, Europe, the US and Japan have the strictest limits. Then come countries in South America, the Middle East and Russia, which have less strict requirements. Finally, there are those countries that have no requirements whatsoever, such as India.”

Switch to waterborne paints in Europe
European legislation allows the limits to be met by either keeping existing solvent-based paint lines and technology andinstalling secondary emission reduction measures, or by investing in new paint systems with a lower solvent content. This may be cheaper in the long-run as the investment and running cost of the additional emission reduction measures can be saved. In Europe most companies have adopted the second route. This does not mean they escape having to use abatement systems. Waterborne paints can still produce VOCs that cannot be released into the atmosphere.
Volkswagen’s Mrowietz explains that German manufacturers adjusted to the more stringent thresholds in the 1990s: “Volkswagen and many other vehicle manufacturers decided not to reduce solvent emissions by retrofitting existing plants with additional waste-air treatment facilities. This decision was based on the fact that downstream treatment facilities will never bring added value, but will always increase operating costs.” The strategy that ultimately proved successful for Volkswagen consisted of developing paint systems further. Today, the solvent for filler coats and base coats is predominantly water. These water-based paints only contain between 5 and 15 per cent organic solvents, compared with between 40 and 80 per cent previously. As a result, solvent emissions at Volkswagen have been reduced from 80 to 100 g/m² to less than 35 g/m² with no additional waste air treatment measures. “Compared with the alternative, which involves conventional paint plus additional treatment of the compartment waste air, this is clearly the more cost-effective solution,” says Mrowietz. “The present data for our plants operating with what is known internally as the ‘5a’ painting process are in the range of 20 to 30 g/m².”
Energy costs and system choice
The CMM Group’s Tom Piskor explains that there are three main types of abatement systems, all of which essentially set off a chemical reaction and convert hydrocarbons and oxygen into carbon dioxide and water vapour. The three system types are:
• A catalyst
• A thermal process, also known as a thermal oxidizer or afterburner
• The collection of VOCs on a concentrator such as a platinum or rhodium, which is then reduced with a catalyst.
“The choice of system depends on air volumes and concentration levels,” says Piskor. Rises in natural gas prices have led to manufacturers changing from thermal processes to catalytic processes, as they can convert VOCs to carbon dioxide and water at lower temperatures than thermal oxidizers. Typical temperature ranges are 400°F to 600°F for catalytic oxidizers and 1,000°F to 1,800°F for thermal oxidizers.
Where thermal oxidizers are preferred, gas use can be lowered by using regenerative rather than recuperative thermal oxidizers (RTOs). According to the CMM Group, regenerative thermal oxidizers use an oxidation technology with two or more ceramic heat-transfer beds that act as smaller heat exchangers and a retention chamber where the organics are oxidized. It can often recover 90 to 95 per cent of the heat generated. A recuperative thermal oxidizer uses an oxidation technology (thermal or catalytic) with a conventional type of heat exchanger to heat incoming air with air from the oxidation process. Recuperative systems can recover 50 to 75 per cent of the heat generated by oxidation. Another important technology uses concentrators. The VOCs are concentrated on a rotating wheel impregnated with an adsorbent. The wheel is then regenerated by passing through a stream of warm, low volume desorption gas that produces a concentrated stream that can be more efficiently destroyed by an oxidizer.
Oxidizers and VOCs
Thermal oxidizers and catalytic oxidizers generally destroy around 95 per cent of VOCs. Many can achieve 99 per cent. GM uses concentrators that concentrate the VOCs ten times before they are sent for incineration. GM’s Piasecki describes the incineration process as very efficient thermally. Heat from that process is recovered to minimise natural gas use. These systems are on paint ovens and clear coat spray booths at GM. GM’s colour coat is water-based and does not need abatement.

Systems at GM vary depending on the age of the facility. In the US there are three types of regulation, explains Piasecki. Existing paint plants have to use reasonably available control technology (RACT). New paint shops have to meet limits. If a paint shop is in an attainment area then they have to use best available control technology (BACT). If it is in a non-attainment area then it can work towards the lowest achievable emission rate (LAER). “In the US the regulation is technology-forcing. In other areas of the world the regulation might consider the ambient impact on a specific area,” says Piasecki.
This is a high technology business area that is constantly innovating to reduce purchase and operating costs. Ford’s much talked about fumes-to-fuel project attaches a co-generation unit to the process so that excess heat can be converted into electricity. Other manufacturers have looked at the system but, according to GM, the technology has some way to go before it is commercially viable. The issue with co-generation is scale. A lot of electricity needs to be produced to offset the cost of the equipment.
“In recent years, the level of automation in paint shops has increased because of cost and/ or quality reasons; as a result (in Europe at least), painting by hand is rare,” explains Mrowietz. To ensure a safe paint process, painting is always carried out in a closed environment under clean room conditions. “A top-down laminar flow of fresh air at a constant flow velocity is pumped into the spraying compartments so that the overspray and solvents quickly flow downward and are removed for treatment. The air is not re-circulated so that fresh, treated, ambient air continually enters the compartments.”
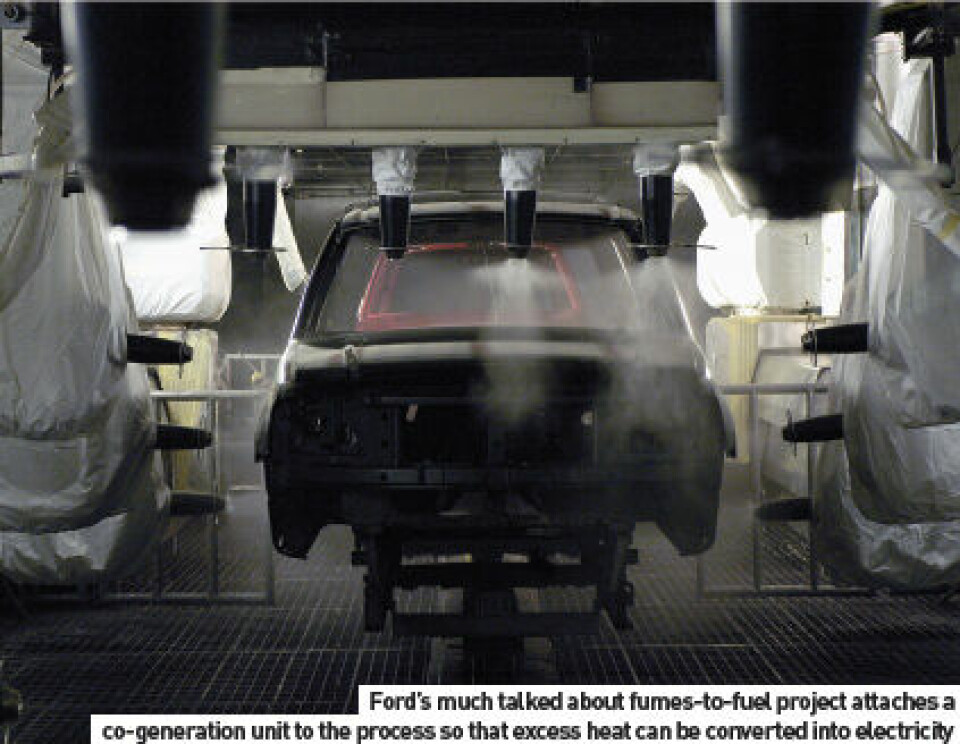
Future legislation
At the moment, a second round of legislation appears to be under preparation in Europe. This round relates to the amendment of existing directives, particularly the IPPCDir, which is being scrutinised in terms of its effectiveness in meeting EU air quality targets. It remains to be seen whether this process will result in new specifications for paint shops. Mrowietz argues that the existing measures have tackled industrial solvent emissions successfully and that now that the majority of VOC emissions that are generated by the use of solventcontaining products are in the residential and commercial sector. “We are of the opinion that the effects of ongoing measures in this sector should first be assessed before attention again returns to paint shops,” he concludes.