Stress test: new modelling approach for component fatigue testing
The development of lightweight structures and components for electric vehicles has created a demand for more comprehensive and up to date test and measurement processes to evaluate component fatigue and service life. Nick Holt spoke with Lucia Barbu, research professor and project coordinator at Fatigue4light to get some insight into the challenges and solutions
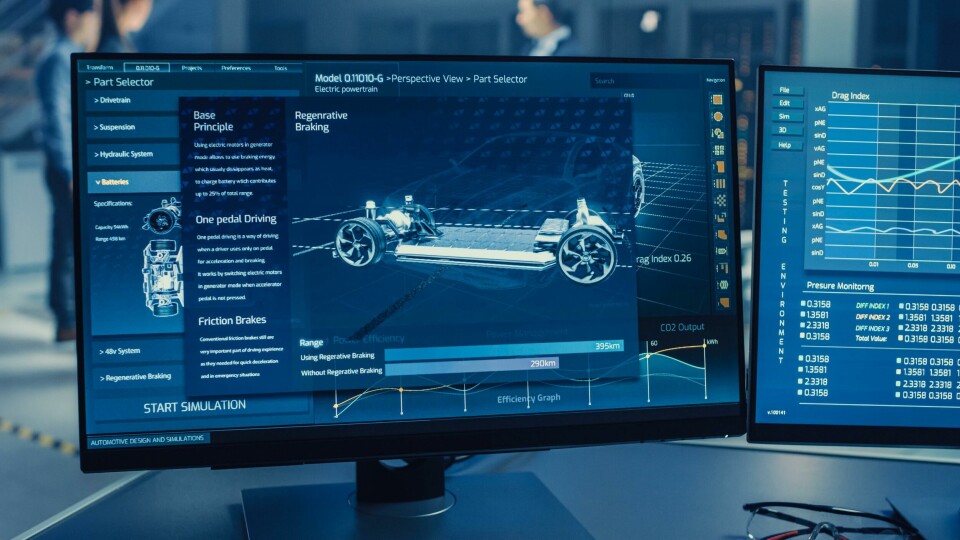
Launched in February this year, the aim of the Fatigue4light project is to support the production of new lightweight chassis components, designed for electric vehicle (EV) applications, through the development of new computer modelling for highly accurate fatigue prediction. This will include working with new high-strength, lightweight steels, alloys and hybrid materials and see the creation of new methodologies to reduce testing times for these materials.
Lucia Barbu notes that initially the focus of the project is on the fatigue behaviour of electric vehicle chassis parts, although the approach is easily extendible to other vehicle types. While here are fatigue modelling strategies are already in use, Barbu says that the modelling philosophy being explored by the Fatigue4light project is different to that currently being used across the automotive industry. “The established fatigue modelling strategy is quite simple, efficient and fast, it’s what designers and carmakers have needed so far”. The issue is that it has been developed and applied to conventional chassis parts and Barbu notes that the industry is in a phase of developing lightweight components specifically for EVs, which because of thinner thickness parts and different materials means that the way in which these components fail is more complex. “You’re starting to get failures that are quite difficult to predict, so we want to develop a modelling approach that can follow the failure process inside the numerical simulation.
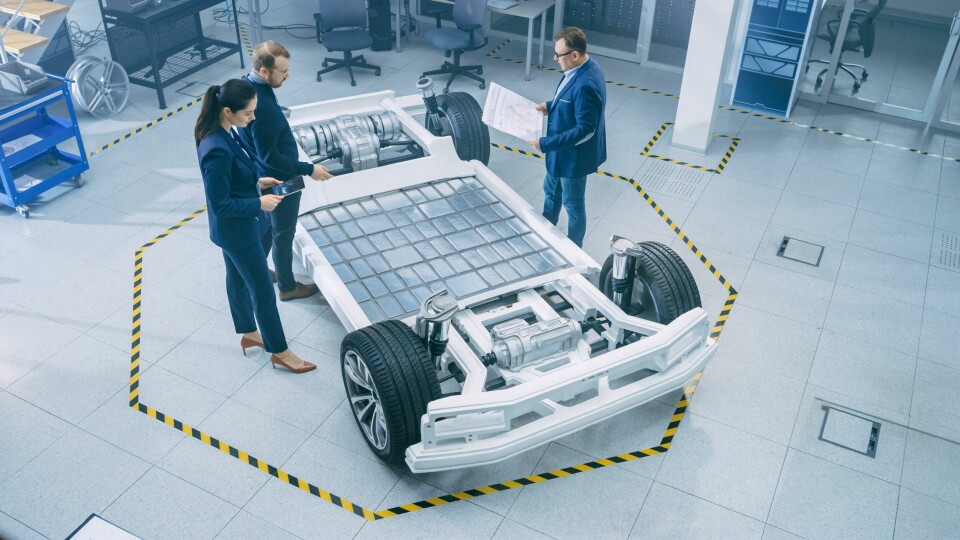
“Right now, the approach is to apply one cycle of loading, with elastic behaviour inside your model, for example, in the case of high cycle fatigue. So, in this case you are checking what the maximum stress level is with one type of load and then extrapolating, based on that level of maximum stress, the number of cycles you estimate that that part is going to be able to sustain until it fails. This might be, for example a small crack which appears in the material, inside your geometry. However, that small crack might not necessarily be the driver for a complete failure; it could be a crack in an area that is not that significant to the overall performance of the part. Maybe you have a material in a geometry that is able to sustain an additional one - two hundred thousand cycles after that first crack initiation. If you consider it failed at that initial estimation you are working with an over conservative approach”.
“We are exploring different modelling strategies, not only for fatigue where you model the whole cyclic behaviour and history of the samples, but also the influence of different manufacturing processes that are regularly used in the production of chassis components”
Lucia Barbu, Fatigue4light
Barbu says it’s more useful to have data that follows crack propagation, the interaction between different areas where there are stress concentrations inside the geometries, and how these stress concentrations (and eventual cracks) interact with each other, how they propagate inside different materials. “This approach to the modelling should offer the carmakers a better idea of the performance of different materials inside those chassis components”.
Modelling the effect of manufacturing processes
While the standard approach works on simple, established parts geometries, offering a good approximation, it’s much more difficult with more complex component geometries. “We are exploring different modelling strategies, not only for fatigue where you model the whole cyclic behaviour and history of the samples, but also the influence of different manufacturing processes that are regularly used in the production of chassis components.
“For example, with trimming or punching sheet metal parts the edge quality of the part is very important in relation the performance of the component as it undergoes many loading cycles. If you have even a slight imperfection in the edge quality, that’s going to act like a stress concentration initiator for the crack.
“We need to develop a modelling approach that is able to quantify any damage on the edges of parts that have been manufactured using these processes. We want to monitor the edge quality and input this information inside the fatigue modelling approach.”
The aim of combining these different data streams is to create an intelligent modelling process that will speed up the analysis and improve the accuracy of any fatigue prediction. Barbu explains: “We also need to have some new strategies from a computational point of view to save time. For example, if we are applying 100,000 cycles with a specific load density and we see some crack initiation in cycle 76,000, then the modelling can make ‘jumps’ until it very quickly reaches that specific number of cycles, then we simulate the loading cycles with smaller steps, monitoring the crack advance in a numerical simulation. This allows us to see how much it propagates with one loading cycle, and then we can make an estimation based on that advance rate and do additional controlled jumps. The number of cycle steps will depend a lot on the material, the loading level and the geometry of the parts.
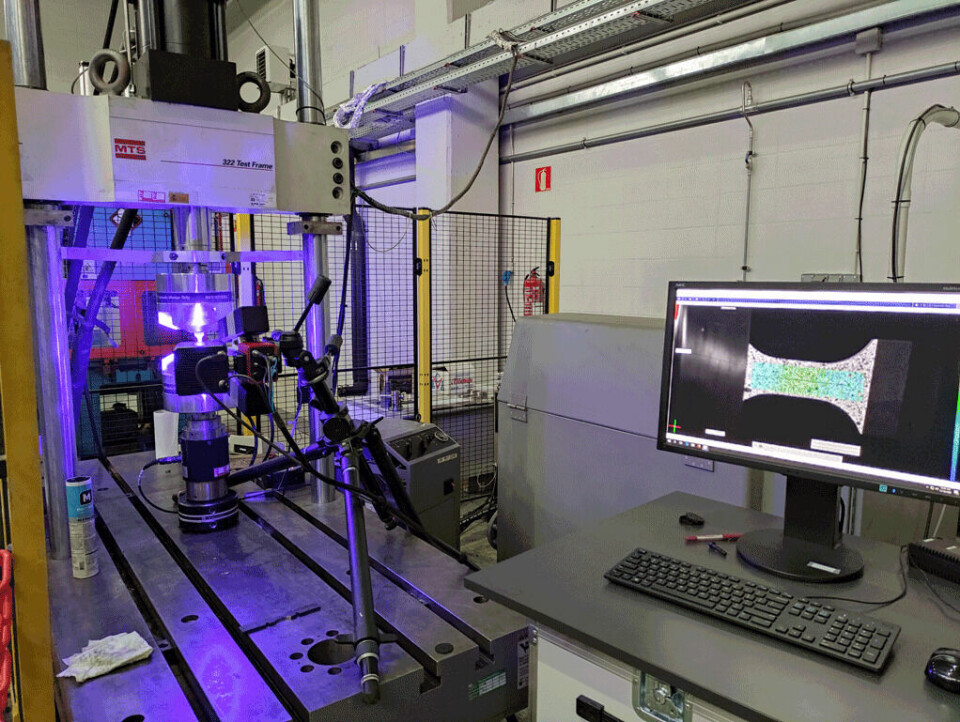
“That’s the kind of modelling philosophy that we are developing in this project. And it has generated a lot of interest from the carmakers. They want to explore this strategy and see if it works for them, if it’s easily adaptable to model specific parts”.
An important part of this development are the materials being used to reduce the vehicle weight. This includes being able to accurately evaluate both the performance and manufacturability of the materials being used individually or in combination.
“We have some partners, Eurecat and ArcelorMittal, who are developing fast fatigue testing methodologies and are working on the different properties of raw materials. They want to validate these fast experimental techniques. If the industry has faster test methodologies for fatigue, then they can explore different materials faster and the lead time for manufacturing the vehicle is reduced,” says Barbu.
Barbu notes that another key pillar of the project is sustainability: “We are studying the performance for new materials, but you cannot change a design now and introduce a new material unless it’s sustainable, for that you need a good end-of-life analysis”.
Expert partners sharing data
The project involves several partners from the automotive industry, including carmakers and tier suppliers, CRF, Stellantis, and Magnetto Wheels, who are lending their experience in key competences and providing invaluable data to support the development of the fatigue models. For example, ArcelorMittal is conducting tests and providing data on the effect of welding on different steel grades and combinations in vehicle structures.
Further down the line the project will investigate modelling fatigue and loading transitions where different materials interact as part of a multi-material body or component, but Barbu notes the project is following a step-by-step approach: “First we want to establish a fully characterised and validated, numerical simulation approach for the base materials being used (steel, aluminium alloys and hybrid metal-composites) and then we are going to work on simulating the performance of a component made of different materials which are bonded together and distributed in specific parts of the component “.