Lille and large - regional focus
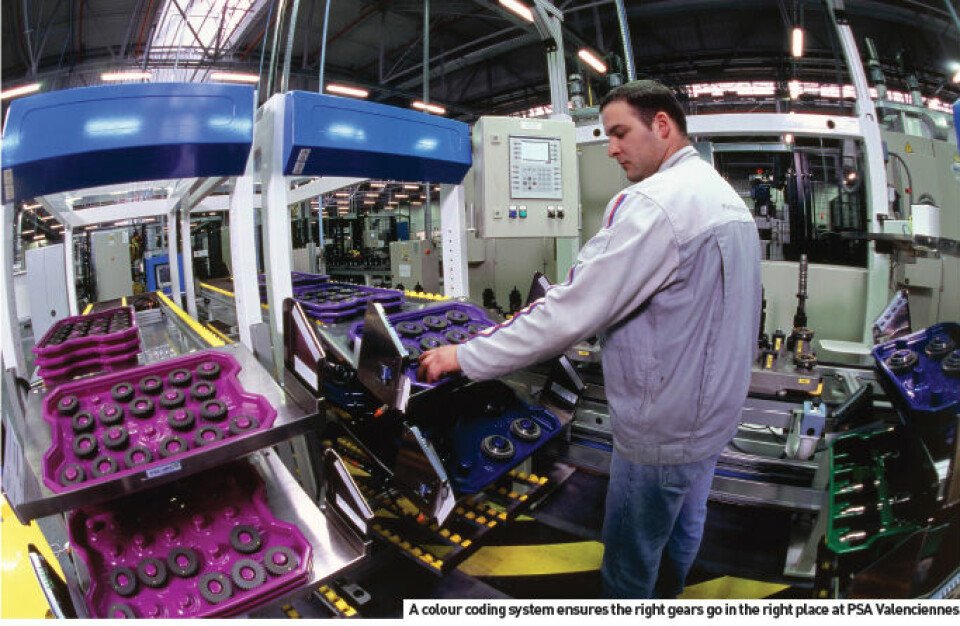
The northern French region of Nord-Pas-de-Calais is a prodigious centre of car production, with over 200 automotive companies supporting an annual build of 10 million. AMS looks at what some of the leading carmakers and Tier Ones are achieving there
The Nord-Pas-de-Calais region of France is claimed to be at the heart of one Europe’s largest manufacturing centres. It contains almost two thirds of the continent’s automakers and many component and equipment suppliers are located less than one day away. Each year, ten million passenger cars and commercial vehicles – equivalent to 80 per cent of the total production of North West Europe – are assembled within a 700 kilometre radius of Lille, the region’s main city. As the second-largest automotive region in France, and the third biggest in Europe overall, it is home to 200 companies that in 2006 manufactured 925,000 vehicles, 1.6 million gearboxes and 1.9 million engines With unemployment levels running at three per cent more than the rest of the country, labour costs in the region are claimed to be five per cent lower than the national average in France. In July 2007 the French government decided on its industrial strategy for the next 30 years by identifying 67 ‘Competitiveness Clusters’.
These projects, subsidised by the state to the tune of €1.5 billion over the next three years, had to meet certain requirements:
- To create new wealth with strong added-value and a skilled workforce
- To be a able to operate in global markets characterised by strong growth potential
- To be based on thorough partnerships between various stakeholders
- To define objectives and the means required for an efficient strategy of economic development and innovative research.
In Nord-Pas-de-Calais, the state has already established six such clusters, two of which have projects that will eventually be developed in the automotive sector.
PSA at Valenciennes
The showroom introduction in 2008 of the new Peugeot 308 will provide a boost to the PSA Peugeot Citroën plant at Valenciennes. It has produced 28 million gearboxes since it began operations in 1981 – equivalent to more than one unit every ten seconds – and the new model will be available with the Valenciennes-produced four-speed adaptive automatic gearbox, known as the AL4. The AL4 automatic gearbox was developed at a cost of €114m ($168m) between 1992 and 1997, in partnership with Renault, which supplies the torque converter unit and other components. It weighs just 70kg and is claimed to offer the same feeling as a manual while being “vastly superior” to traditional automatics.
It features an on-board electronic control unit that permanently analyses and ‘learns’ the driving style of the driver. Starting from September 1997, this cooperation between the two French manufacturers anticipates a growing market that has seen almost 1,300,000 AL4s made for PSA at Valenciennes. As yet the company is unable to say how the take-up of the AL4 by 308 customers may affect demand at the plant, where production stands at 1,100 a day, but the next generation is around the corner.
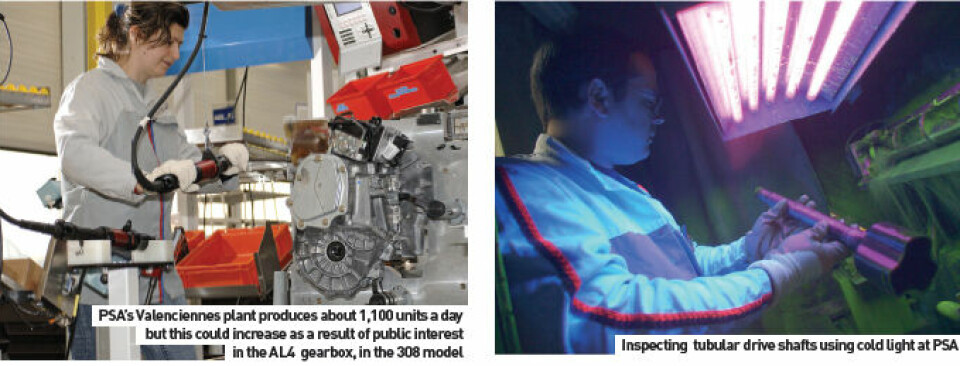
MCP manufacture
Produced at Valenciennes since 2006, a new six-speed automatic gearbox, built on a classical mechanical basis, has made its appearance on the Citroën C4 Picasso. This unit features Tiptronic control and an ability for the driver to switch from manual to automatic at will.
Known as the MCP (Mechanical Compact Piloted), the production of the Tiptronic unit at Valenciennes is currently running at 700 units per day but is expected to increase with new adaptations on other PSA cars, though demand will remain within the plant’s capacity of 8,750 MCPs a week. The Valenciennes site, which covers 89 hectares and has 2,420 employees, began the manufacture of MCP in 2006 as part of a project that represented an investment of €430m ($634m) and which generated 200 new jobs. The six-speed MCP employs a hydraulic gearshift mechanism supplied by Magneti Marelli, which manufactures a similar unit used by Audi for its R8. It has a self-contained electronic control unit that adapts itself to the driver, says Vincent Van Humbeeck, Project Manager at Valenciennes. It operates in both manual and automatic mode through floor-mounted or steering-wheel paddle controls. The gearbox is claimed to offer improved performance and a three per cent improvement in fuel consumption. Valenciennes’ first gearbox, a five-speed manual unit called the BE, remains in production, though it has undergone “much fine-tuning and is now a model of quality and precision,” says the company. Daily output currently stands at 5,600 units. Valenciennes also produces the middle range of gearboxes while, in eastern France, the PSA site at Metz manufactures small and large units.
Suppliers in step with assembly
There are 1,300 suppliers to the Valenciennes operation, 20 per cent of which are in the same region. Main components made from steel, cast iron or aluminium arrive in a rough state before being machined on site. This process is aided by robots, digital control and highspeed movement systems around the site, while a system called RECOR manages the movement of the parts, so that production is always in step with assembly needs. Heat-treated components are air cooled as part of an innovative approach that is more environmentally friendly, since it avoids the use of oil and water. Assembly takes places on semi-automatic lines but the ‘human element’ is still a key part of the production process, says the company, because each gearbox is manually tested and listened to by a specialised worker at the end of the line before being dispatched to the car plants.
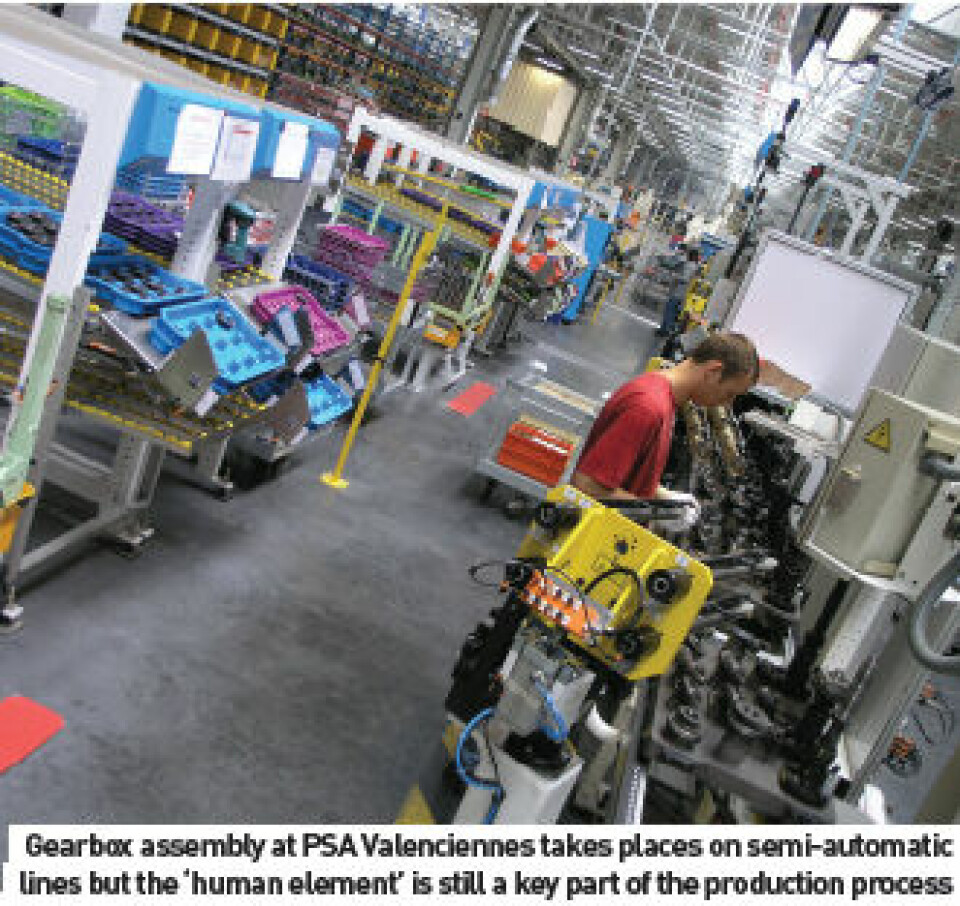
CRITT M2A
CRITT M2A claims to embody a unique partnership between state and private enterprise. Situated at Bruay la Buissiere, it is a publicly-owned research centre that operates as a private company and hires out its extensive testing facilities to automotive sub contractors.
The operation was established seven years ago and represents an investment of €15m ($22m), according to its Managing Director Jerome Bodelle. The building covers 6,200 square metres and is located on a four hectare site, carefully hidden from prying eyes. “It stems from the collaboration between the automotive industry suppliers (Avon, Bosal and Bridgestone, to name a few) and public bodies to provide access to research and development facilities in the areas of vibro-acoustics, engine mechanics and CAD for auto industry suppliers,” says Bodelle. “It means we a can offer subcontractors access to the advanced R&D necessary to take into account all the needs of the main manufacturers and to benefit from our wide range of testing facilities.” He said that CRITT M2A offers a central structure for performance optimisation, reductions in thermal engine pollution, sound emission analysis rooms, high performance calculations, modelling and simulation means, as well as human resource skills to operate these tools and benefit from the results. “The centre possesses the means for acoustic diagnostics and analysis for vehicle noise optimisation through a semianechoic chamber with a roller bench, while our vibration study equipment and our experienced engineers are also able to provide expert analyses.” Typically, the cost – ‘just for the keys to the room’ – of the use of an anechoic chamber with a roller bench is €2,000 ($2,950) a day. “Another key benefit of the operation is that it helps us retain automotive engineers in France,” added Bodelle.
Bridgestone
Bruno Capron takes no prisoners. The managing director responsible for manufacturing at the Bridgestone plant in Bethune is briefing journalists before a tour of the factory. “Taking photographs is not permitted and we will confiscate the camera or mobile phone belonging to the culprit.” Capron smiles as he says it, adding even more weight to the threat and convincing us that he probably will do what he says.
Sited as it is on Avenue George Washington provides a clue to the plant’s history. It was built by US company Firestone in 1961 and in 1972 was the first of its plants worldwide to produce a steel-belted radial tyre. That claim to fame was soon eclipsed in 1988 when the US icon was acquired by the Japanese giant and the sign outside changed to Bridgestone. However, the Firestone name lives on and half the tyres made still carry the ‘flaming torch’ symbol. In the good old Firestone days of the 1960s, capacity was a modest 4,000 tyres a day, but by 1987, thanks to a combination of investment, product rationalisation and extra shifts, this figure had grown to 20,000. Only three years after the Bridgestone takeover, the introduction of high and ultra-high performance, low-profile units at the Bethune plant – about 38 kilometres from Lille – paved the way for the start of OE supply to Audi in 1995. The following years saw supply to BMW, Toyota and Mercedes.
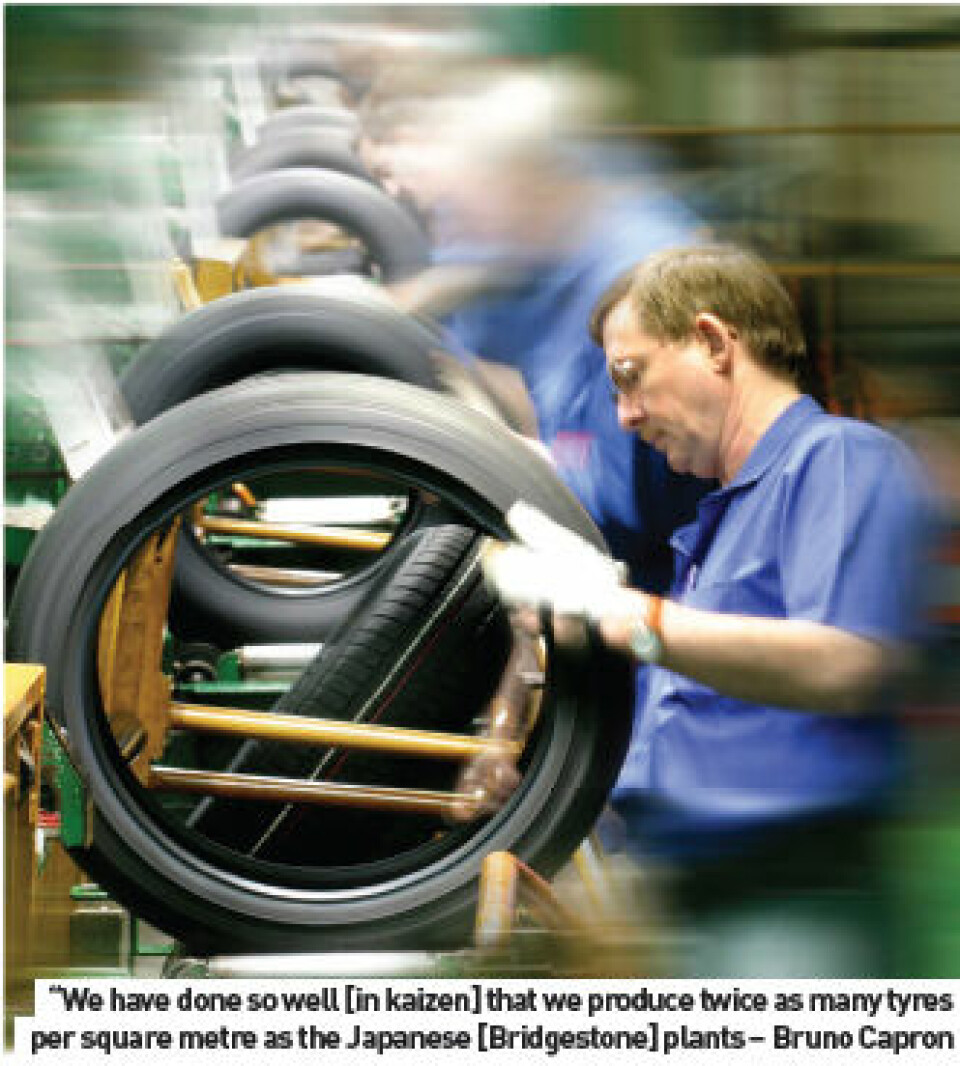
Competition breeds creativity
“This is the only Bridgestone plant in France in the middle of a Michelin ocean,” chuckles Capron, revelling in the thought of a being a small thorn in the side of the French giant’s Mr Bibendum. “We run for 347 days a year, producing 25,000 tyres in 60 different types and sizes a day. And because we are surrounded by Michelin, to remain competitive we have had to be innovative.” Capron is proud of the work Bridgestone has done with BMW in the area of run flats and the German carmaker now sources around 50 per cent of its requirement from Bethune for this fitment. “We’re now working with BMW on a second-generation run flat with more compliant sidewalls for better ride quality,” he adds. In 1988, the site started producing silica-based products for enhanced rolling-resistance. It has also brought in Japanese working practices, such as kaizen (continuous improvement) and there are monthly kaizen meetings involving between 50 and 100 employees that address all areas of activity and all levels of staff.
“At the end of each year, we actually have a ‘golden kaizen’ award for the group that has introduced the best improvements,” says Capron. “In fact, we have done so well in this area that we produce twice as many tyres per square metre as the Japanese plants.” Capron concedes, however, that some parts of the factory do look not permanently as clean as desired – “but this is because we work seven days a week and so regular maintenance and cleaning has to fit into the schedule.”
Labour intensive production
There are 1,450 workers at Bethune and in spite of the dramatic strides forward in the robotisation of vehicle manufacture, tyre production remains labour intensive. With the main components still put together by hand, Capron estimates that it takes six months for a worker to become fully trained and able to work on his own. “But to become really good and highly skilled may need as much as five years’ experience.” Visual inspection of the finished product remains a must – undertaken by the ‘Mk I Eyeball’, as the British Army would say. Operators have only 30 seconds to inspect a tyre. However, a complementary in-depth technical inspection is performed automatically on 100 per cent of the production as well. Currently, the scrap rate is 0.5 per cent, or more than 40,000 units a year.
“It’s easier to scrap tyres than to shut down a whole system to track down the fault,” admits Capron. One of his main tasks at the moment is to push OE levels back up. In 2001, OE accounted for more than 60 per cent of production, too much to operate smoothly but now this has dipped to just below 30 per cent. “My aim is to get back to 40 per cent OE. Ultra-high performance OE means perfection and that means stress, but this is the best benchmark for remaining among the topclass makers and ensures our plant’s survival. “We need another one, or even two, new plants in Europe to meet current demand.”
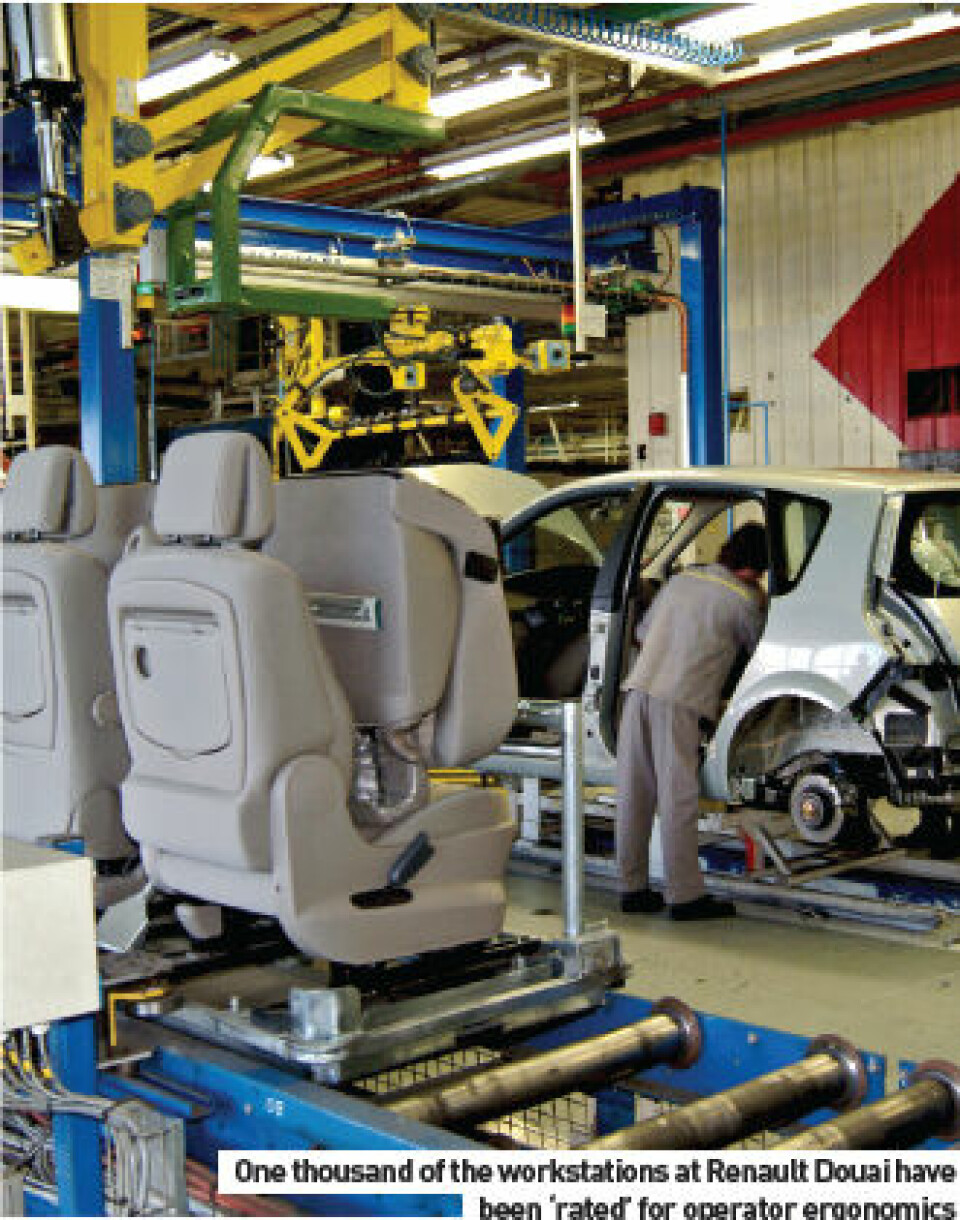
Bridgestone BIRD
More capacity will come from the new plant in Tatabanya in Hungary, which is expected to come on stream in 2008. This plant will inaugurate the new Bridgestone ‘BIRD’ production system, which should drag tyre manufacture into the 21st century. Short for Bridgestone Innovative and Rational Development, it is claimed to be the first tyre production system that automates the entire manufacturing sequence, from the processing of material to the inspection of the finished tyre. Also, in 2006, Bridgestone began construction of a new €200m ($295m) radial truck and bus tyre plant at Stargard Szczeciński, in north-western Poland, scheduled for completion in 2009. The 100-hectare site will have 750 employees and a capacity of 5,000 tyres a day by 2011. The company says that Stargard production will supplement output from Bridgestone’s existing Bilbao truck and bus tyre plant in Spain and help meet European demand for Bridgestone commercial vehicle tyres.
Renault at Douai
The Renault plant at Douai, which employs 6,000 workers, is one of the group’s largest factories worldwide, ranking second only to the nearby Arc International tableware company with its 8,900 employees.
But though size may count in the macho world of motors, a programme called ‘Feminisation’ at Douai has seen the number of women working at the Megane plant double during the past decade. Women now account for almost 10 per cent of the workforce and, in the past three years alone, the plant has taken on 250. Overall, from 2000 to 2005, Douai recruited an extra 1,500 staff, during a period up to 2004 when production reached a record 470,000 units, though output for last year was lower, at 327,832 units, a fall of 30 per cent. It is also a relatively young workforce with an average age of 44 and a recently-introduced crèche has been specially adapted to accommodate the children of employees working on one of the two, eight-hour shifts.

Safety and ergonomics
Creating a safer working environment is also key priority at Douai and the number of accidents (those serious enough to shut down the line) has fallen from 34 in 2003 to 17 last year – a figure the company claims is ten times better than the industry average. This, it says, has come about because out of 1,400 workstations at the plant, 1,000 have been ‘ergonomically rated’ and, where necessary, altered to make life easier for the operator. In 2004, there were 104 stations with a ‘high’ (bad) rating, together with a further 228 categorised as ‘medium’, while this year the plant expects that these figures will have fallen to 49 and 195, respectively. After safety, a commitment to quality comes a close second at Douai and Megane Scenic achieved first place in its segment for the JD Power 2006 survey in France, though it could manage only second in the US company’s survey of product quality in the UK.
French bastion
Douai was built in 1970s and like the many other companies in the region, Renault chose this location for the geographical advantages of easy road and rail access to Europe’s major car markets and its proximity to suppliers. Also, back in 1969, the French government, the then sole shareholder in the company, was seeking to, as the company archives put it: “slacken the grip of a harsh economic crisis that was ravaging a region that has been a traditional bastion of French industry”. Work started in 1970 and lasted five years. Douai’s first model was the Renault 5, which had been launched three years earlier. Its first full-scale production project was the Renault 14 in 1976.
The 1980s at Douai saw the launch of the Renault 9 and the Renault 11 – which ushered in just-in-time production at Douai. This was followed in 1986 by the 21 and the Renault 19 two years later, the introduction of which coincided with a major initiative designed to lift quality and probably helped the 19 model remain top of the German import chart throughout its life. To mark the tenth anniversary of his assassination in 1986, the plant was named after the chairman and CEO George Besse in 1996. Two years later the site celebrated the completion of its five millionth model.

C-Segment production
Douai produces four variants of the Mégane II family launched in 2002 – hatch, coupe-cabriolet and five and seven-seat versions of Scenic II. These models compete in the C-segment category, the largest sector in the European market. The millionth Mégane II rolled off the production line in September 2005. Rather confusingly, next to a Mégane displayed at the main entrance, is the latest Laguna; apparently placed there as an example of quality. As well as manufacturing Megane, the plant also produced stamped parts for other Renault operations. In October last year, Douai opened its doors for the first time to the general public. The theme of the twoday event was “quality manufacturing practice across the Mégane range” and featured a three-hour tour of all the manufacturing and assembly areas. Although the plant was not actually making cars during the open-day weekend, there were features and film shows running to recreate everyday conditions. This year there is no open day, probably because of cost cutbacks, according to insiders.
Environmental impact
In keeping with every major European manufacturer, the effect Renault has on the environment plays an increasing role in the way it manages things. At the end of 2006, Douai and 38 other Renault Group manufacturing, logistics and product sites were ISO 14001 certified. This certification marked a milestone in a programme that began a decade ago when Renault introduced a policy to reduce the environmental impact of its activity at every stage of a vehicle’s life cycle, according to Douai Communications Manager, Yann Dorison. “ISO 14001 certification is one of the specific criteria that applies to the “Renault eco²” signature launched in May 2007. The signature covers every stage of a vehicle’s lifecycle, from design to manufacturing, customer use and end of life. “The other criteria are carbon dioxide emissions of less than 140g/km, or the use of bio fuels, a 95 per cent re-usability at the end of vehicle life, and at least five per cent use of recycled plastics.”
A recent example at Douai of waste recycling is the recovery of excess wax used in the anti-corrosion process. Previously, the waste wax, which amounted to almost half the 1.5 litre slug injected into body cavities, was incinerated. However, since May 2007, the wax that is recovered (240 litres every day) has been recycled and mixed with the new wax prior to injection, so that 20 per cent of recycled wax is included in the final product. “The collection of wax drips will gradually be applied to the automated paint booths,” says Dorison.

Savings have also been achieved in the area of materials and mastic recycling: in the past five years, the quantities of mastic used at Douai have been reduced by 40 per cent, while 98 per cent of the recovered mastic is now recycled. In addition, in the paint shop recovered paint solvents are used to feed the cataphoresis and mastic ovens. Since 1993, four incinerators have been burning the solvents from cataphoresis baths, with the energy from this incineration used to heat the cataphoresis ovens to 120°C. The system operates as a loop: the solvents released in the ovens are incinerated in order to raise the temperature. A similar system is used for the mastic ovens and the heat exchange between the incinerators and the ovens reduces the quantity of waste and minimises the quantity of energy consumed by the latter. In 1998 solvent-based paints were replaced by hydrosoluble-based products, resulting in a significant fall in voluble organic compounds (VOC) from 6.5kg per vehicle to 2.9 kg in 2006.
“The Douai factory has invested €60m ($88.5m) to achieve this environmental progress and this initiative was followed in 2002 by the use of burst painting techniques for colours and primers,” says Dorison. “Burst techniques can be used to paint a complete series of vehicles with the same colours, without having to clean and purge the painting system between each vehicle, saving 2kg of solvent.” The results of these environmental initiatives at Douai over the past ten years are impressive: energy consumption has fallen by 30 per cent; VOCs have been reduced by 66 per cent; water consumption has been cut by 40 per cent and waste reduced by 50 per cent, half of which is recycled.
Toyotomi Europe
A company originally founded in Japan in 1960 to make parts for obsolete Toyota vehicles is one of the latest to set up shop in the Nord-Pas-de-Calais region. Toyotomi-Kiko was created in Anjo City to produce spare parts for Toyota vehicles no longer in production.
In September 2006 – just five years after Toyota started producing the Yaris in the Valenciennes region – it opened a 120,000 square metre site under the banner of Toyotomi Europe at the same Onnaing Business Park as Toyota. The investment in equipment and plant by Toyotomi Europe in northern France was €21m ($31m), €2.62m ($3.9m) of which was covered by local and state aid. However, the level of financial aid available for a region which has an unemployment rate that is three per cent above the national figure in France (10 per cent) was not the only consideration, according to Karl Martin, Area Development Project Manager for the Valenciennes area Chamber of Commerce and Industry.
The Toyotomi site is only short distance away from the Toyota plant and Toyota Motor Manufacturing Chairman Hiroshi Okuda points out the benefits of the location: “The Onnaing business park is only 60 kilometres away from downtown Lille [a Eurostar stop] and is very close [less than four miles] to the Belgian border. Also, Paris can be reached in just two hours, either by road or rail, and Brussels is only an hour away,” he continues. “After having carried out feasibility studies and analysed all proposals, we chose the Valenciennes area because of its high quality of infrastructure and the presence of high quality equipment manufacturers. “The operation is also close to other Toyota sites and to the main market for which the vehicle assembled at the plant was intended.”
Yaris supply
Two years ago rising demand for its Yaris series prompted Toyota to increase production by 11 per cent at the Valenciennes plant and create 1,000 new jobs as part of a €110m ($162m) investment. The move was designed to lift annual capacity by 11 per cent to 270,000 to meet increased sales fuelled by the introduction of the secondgeneration Yaris.
Toyotomi, in which Toyota in Japan has a 49 per cent stake, produces mainly accident parts for Yaris, such as rear quarter body panels, doors, floor sections, hoods and fenders. Its work force has grown from 65 in September in 2006 to 80 and it expects this figure to have increased to 120 within three years. Apart from Valenciennes, its also supplies parts to Toyota vehicles in the UK and Turkey, explains Manufacturing Manager Philippe Guckert. “Plants order the parts they want and typically they are delivered in three days’ time to Toyota’s logistics centre in Brussels. Raw materials are sourced through Toyota centrally to get the best price and production is organised around small batches of, say, five. “Toyota stops making parts for its vehicles after about five years after model launch and the company believes it’s more profitable to be able to increase the volume of new cars than to carry on making spares for old ones,” says Guckert. Usually, once Toyota sales in a particular region hit the million mark, executives at the parent company in Japan sit down and consider whether a Toyotomi operation is viable. The plant sells about 1,000 parts a day from 282 part numbers and the average order size is 155 units, but it can be just one, adds Guckert.
For body panel production there are four presses: one 1,800 tonne unit and three 800 tonne ones that come from Toyota. There are 340 dies available – Toyota in Japan stores some 20,000 – each weighing 20 tonnes but taking only ten minutes to change. But with each press representing an investment of at least €13m ($19m), instead of producing half-adozen panels at a time, wouldn’t it be more cost effective to stamp them out in larger quantities? “The problem is where to put them,” says Guckert, who adds that 30 per cent of the 20,000 square metres of floor space available is already devoted to storage. Toyotomi is proud of its safety record and each day at the plant starts with a five-minute safety meeting. “We share all the safety data from all over the Toyota world,” says Guckert.
Faurecia has 60,000 employees worldwide and had a ¤11.6 billion ($17 billion) turnover in 2006. Innovation is an important part of its success and, together with its stakeholder PSA Peugeot Citroën (71 per cent), it invented the diesel particulate filter.
It is a truly global operator: taking into account its six product lines, it is ranked eighth worldwide and number two in Europe. Its customers include all major vehicle manufacturers: 24.5 per cent of sales are accounted for by VW; 23.5 per cent by PSA Peugeot Citroën; 12.4 per cent by Renault-Nissan; 10 per cent by Ford and around seven per cent each by GM, Daimler and BMW.
It has 190 manufacturing sites around the world supported by 28 research and development centres.
As the world’s number one in the field of interior systems, sales last year of instrument panels (eight million units a year); door modules (0.5 million); door panels (25.6 million) and cockpits through a joint venture project with Siemens (3.6 million) generated revenues of ¤3.5 billion ($5.6 billion), or around a third of the company’s total turnover.
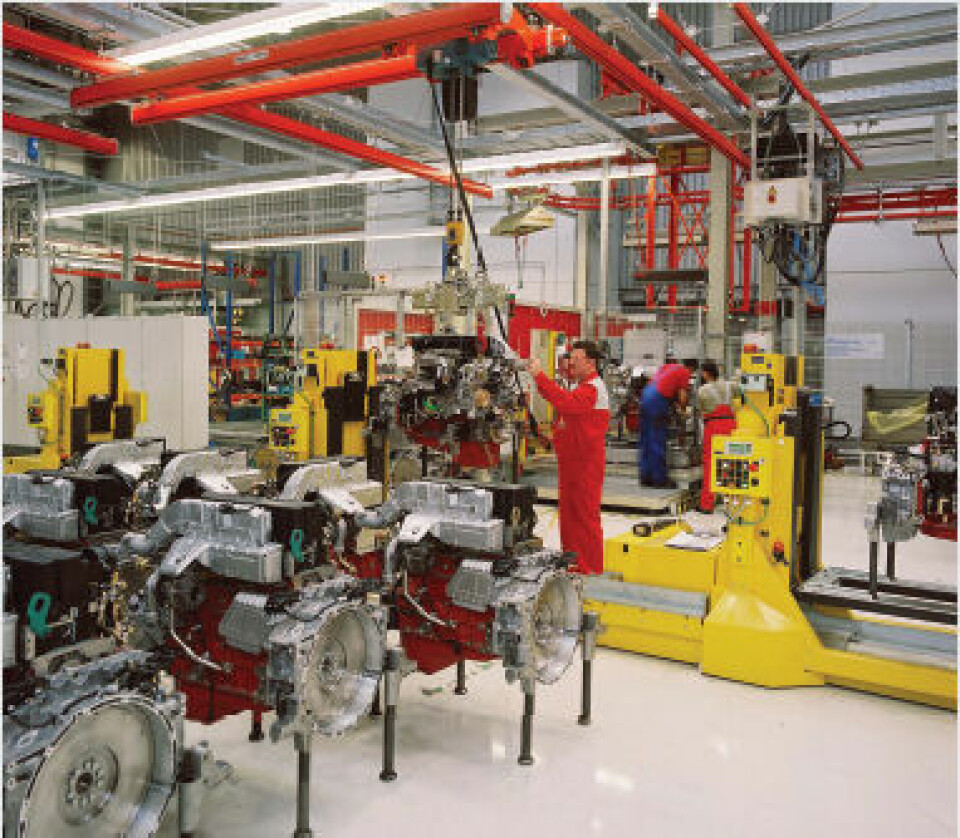
Faurecia
Faurecia is a key player in northern France and Europe is its largest market. The Tier One company has 95 sites and more than 38,000 employees in the western region of Europe. It is the number one supplier in the world for interior systems and number two in Europe for acoustic packages. For exhaust systems and front-end modules, it is number one in Europe and second worldwide while for seats it is second in Europe and third around the world. At the recent Frankfurt Motor Show, Faurecia was able to display the special ‘slim’ front seats it developed for the new Renault Laguna, along with an exhaust system that is 30 per cent lighter, alongside innovative instrument and door panels designed specifically for Renault’s latest contender in the D-segment.
The plant at Henin-Beaumont was created in 1969 and last year it achieved sales of €110m ($162m). With its 490 employees it delivers 144 instrument panels a day to the plant at Sevelnord for the Peugeot 807/Citroën C8 and Fiat Ulysse/Lancia Phedra vehicles; 350 and 1,500 instrument panels a day to Renault’s Douai plant for the Megane and Scenic models, respectively, along with four different painted parts for the Scenic, also at the rate of 1,500 a day. In addition, from January 2008, it will begin shipping 950 instrument panels a day to Renault’s site at Sandouville for the Laguna III. Gaëtan Houzet, the Deputy Plant Manager, explains that the Henin-Beaumont plant employs a wide range of technologies including thermo covering; ultrasonic welding; flaming; foaming and milling. There are also 17 injection machines ranging from 650 to 2,100 tonnes. “In the area of painting, we use soft, acrylic and hydro PU2K,” he says.
Deliveries of instrument panels to the Sevelnord plant started in June 2001 and are shipped in module form and assembled on site. Production of these for the Megane and Scenic began in July 2002 and March 2003, says Houzet. “Renault demands a very high standard of finish,” he stresses. “The original Laguna, for example, simply had an injected instrument panel but this has evolved into a more sophisticated one for which we use foaming to produce a much better finish. “For the instrument panel for the Laguna III, Renault stipulated that it wanted zero defects.” A spokesperson for Faurecia said that, following market consolidation, there are now only about ten major vehicle manufacturer groups remaining in the world. “We have a very close working relationship with them all.” Faurecia has only recently started to court Asia and the US and new business there has proved useful in the effort to help offset a slowdown in demand from European customers. “Until five years ago we were almost exclusively in Europe but now we have recently opened six new plants servicing contracts in North America with BMW (X5), Nissan and Volkswagen, together with the ‘Big Three’ indigenous automakers.
“In 2007 we started to supply front-end products to Chrysler for the Sebring in the US. Here, and in Asia too, we may open new plants as we win new business.” He added that Faurecia opened its first plant in China a couple of years ago and in India it has formed a joint venture project with a local company.
“Where we can, we source from low-cost countries although much production activity takes place near to the final customers because the fragile nature of a lot of our products means they don’t travel well,” he says. He added that the increase in the cost of raw materials – many of which are petroleum-based and are therefore linked to the price of oil – has put increasing pressure on companies such as Faurecia.
Demag cranes have several applications in the region at:
PSA in Valenciennes :
KBK enclosed track system in steel and aluminium plus several chain hoists
Bridgestone in Béthune :
KBK supension cranes, chain hoists and a heavy-duty EDKE model crane
Renault in Douai:
KBK enclosed track system and chain hoists, wheel blocks with drive systems, and one ZHPE semi portable crane of 15/15 tonnes on a 11.23 metre track
Toyotomi in Onnaing:
8 KBK enclosed track systems with DC model chain hoists
Toyota in Valenciennes
Several KBK enclosed track systems and one 10 tonne ZKKW process crane on a 27.225 metre track