GM announces $60m Series B investment in AI-powered battery materials trailblazer Mitra Chem
Mitra Chem uses AI to develop iron-based cathode materials for lithium-ion batteries in reduced time to market and may signal GMs exploration of alternative battery materials to thwart ongoing supply shortages.
The Silicon Valley-based company’s mission is to develop and commercialise iron-based cathode materials for lithium-ion batteries, to drive mass-market electrification for EVs and energy storage. Mitra Chem is the first lithium-ion battery materials manufacturer focused on shortening the lab-to-production timeline by over 90%, marking it out as a viable option for investment by the OEM.
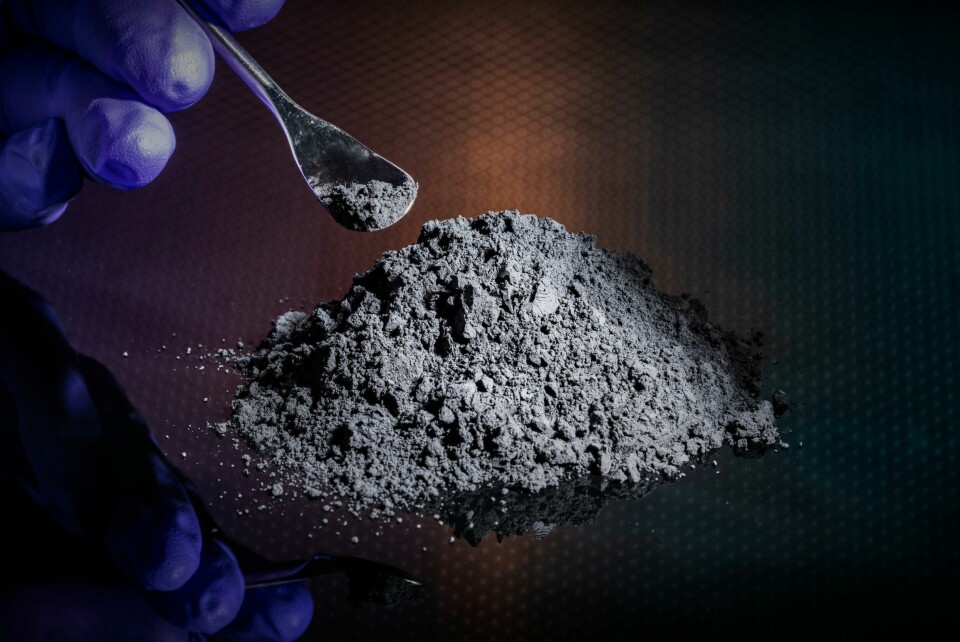
The Series B funding falls in line with GM’s electrification plan and attempts to secure more capacity in the battery supply chain and processing capacity for key components. Mitra Chem’s AI-powered platform and advanced research and development facility in Mountain View, California has the technological potential to accelerate GM’s aim to make EV batteries more affordable.
“This is a strategic investment that will further help reinforce GM’s efforts in EV batteries, accelerate our work on affordable battery chemistries like LMFP and support our efforts to build a US-focused battery supply chain.”
The start-ups AI-powered battery tech development processes are helping to drive substantially shortened learning cycles to achieve shorter time to market for new battery cell formulas, highlighting the company as a viable investment for GM as part of its goal towards “an all-electric future”; at the heart of which sits the Ultium battery platform, whose battery cells are currently composed of an advanced of nickel-manganese-cobalt-aluminium (NMCA) lithium chemistry.
The companies will work together to develop “advanced iron-based cathode active materials (CAM), like lithium manganese iron phosphate (LMFP), to power affordable and accessible EV batteries compatible with GM’s EV propulsion architecture, the Ultium Platform.”
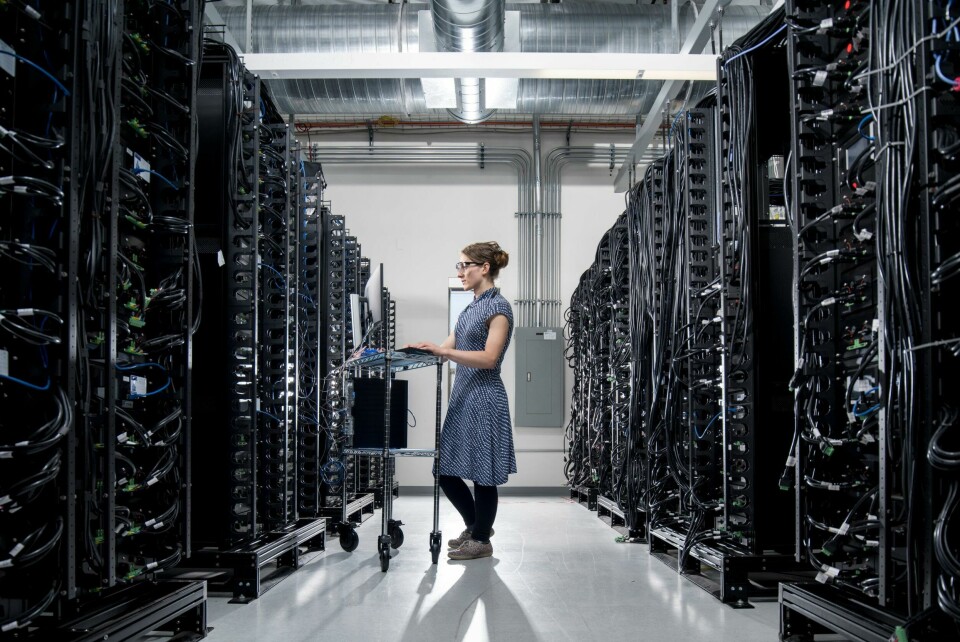
Gil Golan, GM vice president, Technology Acceleration and Commercialisation commented: “This is a strategic investment that will further help reinforce GM’s efforts in EV batteries, accelerate our work on affordable battery chemistries like LMFP and support our efforts to build a US-focused battery supply chain.
“GM is accelerating larger investments in critical subdomains of battery technology, like cell chemistry, components and advanced cell production processes. Mitra Chem’s labs, methods and talent will fit well with our own R&D team’s work.”
How GM’s investment in Mitra Chem could reimagine the Ultimum Battery platfom as well as battery production
As a company that works at the intersection of machine learning and battery technology development, Mitra Chem’s R&D facility operates through simulating, synthesising and testing thousands of cathode designs each month, ranging in size from grams to kilograms, according to GM. These AI-powered battery tech development processes are helping to drive substantially shortened learning cycles to achieve shorter time to market for new battery cell formulas, including in further development of GM’s Ultium battery platform. The Ultium platform’s battery cells are currently composed of an advanced lithium nickel-manganese-cobalt-aluminium (NMCA) chemistry.
“GM’s investment in Mitra Chem will not only help us develop affordable battery chemistries for use in GM vehicles, but also will fuel our mission to develop, deploy and commercialise U.S. made, iron-based cathode materials that can power EVs, grid-scale electrified energy storage and beyond.”
The OEM’s Series B investment into Mitra Chem could be seen as a signal of its exploring options into alternative chemical compositions for the future of its own battery technologies, since Mitra Chem’s iron-based cathode battery technologies represents a departure from conventional materials like nickel and cobalt, which are currently grappling with ongoing supply shortages.
Mitra Chem’s “atoms-to-tons acceleration platform” allows the company to utilise simulations and physics-informed machine learning models to speed up the processes of “formulation discovery, cathode synthesis optimisation, cell-lifetime evaluation and process scale-up.”
Its cloud platform, tailored specifically for battery cathode development, can accelerate the process of data collection and processing from various stages of synthesis, material characterisation, cell prototyping and standardised analysis and visualisation, and is sure to enable accelerated time to market for GM in the absence of alternative chemical explorations for its battery technologies.
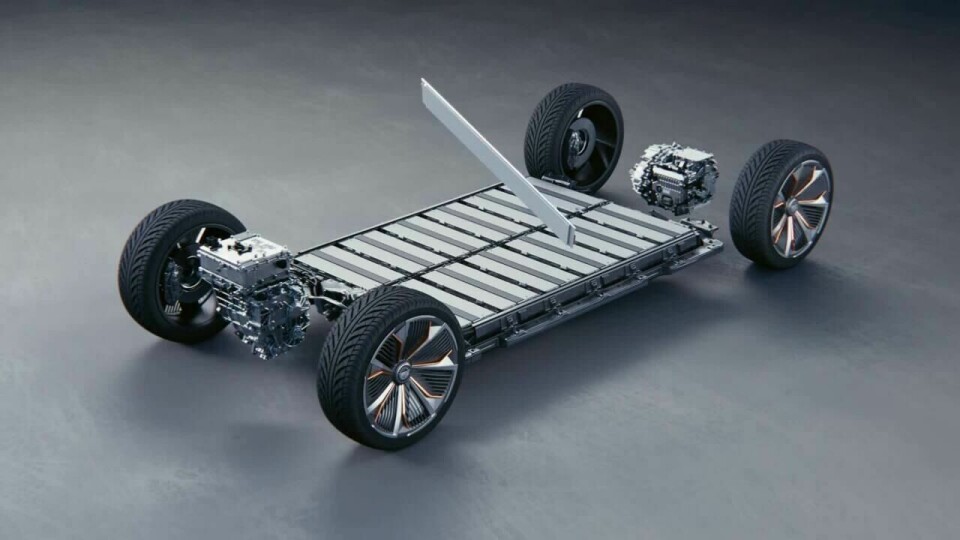
Mitra Chem CEO and Co-Founder Vivas Kumar commented: “GM’s investment in Mitra Chem will not only help us develop affordable battery chemistries for use in GM vehicles, but also will fuel our mission to develop, deploy and commercialise U.S. made, iron-based cathode materials that can power EVs, grid-scale electrified energy storage and beyond.”
Solving EV battery bottlenecks through innovation and collaboration
Shortages in key EV battery materials such as Nickel and Cobalt have caused bottlenecks across EV supply chains and manufacturing processes that have adversely impacted the EV market across the board. GM recently admitted that it continues to face delays in the ramp up of its EV models following automation supply issues for its battery module production.
Most recently, GM’s luxury SUV Cadillac Lyriq model was said to be the hardest hit, but its Brightdrop vans are also impacted by the production issues – both of which use GM’s new Ultium battery technology.
AMS’ sister publication, Automotive Logistics (AL), recently interviewed GM’s global purchasing chief, Jeff Morrison, who has recognised that new partnerships and collaborations with suppliers across chipmakers, battery materials and logistics providers have the potential to create more stable, resilient operations.
To navigate these risks, GM has invested in battery production and critical materials, partnering with companies “to secure cathodes, expand material processing capacity and establish lithium mines in the US,” while also seeking to expand “visibility and connectivity with upstream suppliers through supply chain mapping and advanced analytics.”
The article outlines that GM has identified a heightened risk in limited battery materials processing, “which is highly concentrated in Asia, with a limited number of suppliers for battery grade materials that go into key components like cathodes and anodes.”
This latest Series B investment by GM at $60m in Mitra Chem is evidence of the OEM’s strategy to develop resilience in the face of market, supply and manufacturing challenges, and a display that collaboration and innovation is central to developing flexibility in the face of disruption and uncertainty.