In a state of flux: EV motor development
Electric motor development is key to improving the performance of EVs. AMS spoke to Paul Price, chief technology officer at electric motor developer IRP about optimising design for manufacture and developing better driving performance
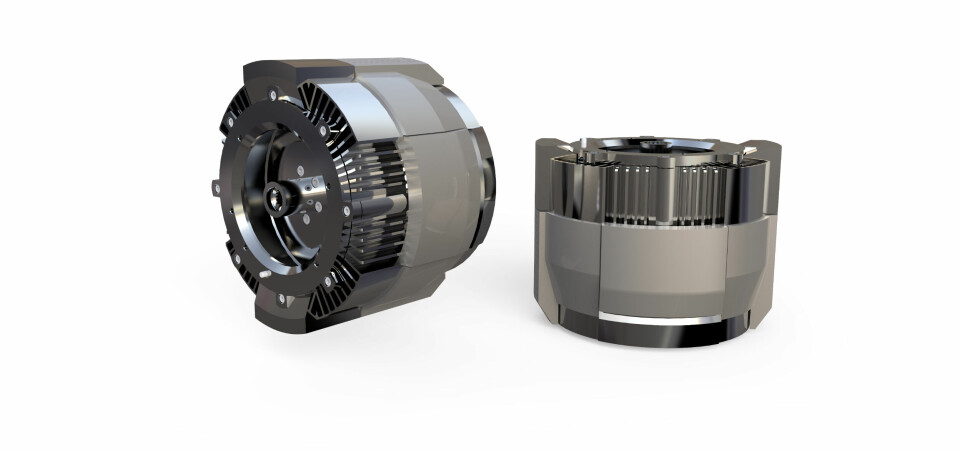
AMS: Could you offer some background about IRP?
Paul Price: Initially we were providing electric powertrain solutions for the aerospace industry. Around 2015/2016 we started to get enquires from the automotive industry and at that point we were self-funded with our own profits and revenues. We developed a two-wheeler application that was quite successful and this encouraged us to develop further in this sector.
What we realised was that to enter the automotive industry we needed outside investment, which we raised in two rounds and we have since invested a lot in IP and knowhow because a small company needs to have an edge in order to enter this market. One of the things we recognised was the OEMs and Tier 1s already had production lines ready for the new generation of EVs, so this was a potential barrier to motors requiring more sophisticated production lines. To fit these existing production operations, we have developed our technology and the topologies of the motors to be very flexible, removing the need for special materials or production processes, making it easier for the OEMs and Tier 1s to accept our technology. Also, we have developed a lot of IP knowhow with the software and hardware configurations.
Making a comparison to the internal combustion engine (ICE), this has a legacy of 100 years of development, while the EV industry is very young, without any legacy, so this needs to build up. A lot of new technologies and ideas will mature in the EV propulsion system in the next few years, but it will be more difficult. Internal combustion engines have a lot of moving parts and a lot of mechanical components, you can tune and adjust and modify each part of the powertrain separately and build improvements along the way, but an electric motor is a very simple device. It has one rotor and one stator, not many components, not a lot of materials, so you must be an excellent chef to produce an excellent meal from two or three ingredients.
”Once you have a stable production line that is not super sophisticated, not using any rare earth materials or any high-end components, it will be easy to make a micro production line wherever the customer requires. And transportation today is becoming more difficult and it will ease things on that side”
Paul Price, IRP
AMS: In terms of the electric motors, could you offer some context as to where you see the current level of EV motor types and technologies?
PP: It’s still in the early stages and it’s perhaps difficult see how a simple device like an electric motor will develop in the future, because it has few components and not a lot of material usage. So, the benefits will come from software, control algorithms, integration in the vehicle and also reduction in the cost. Efficiency will not be 100% but it will be relatively close to that. The motors can be small, will not have to dissipate a lot of heat and there the advantage will come from using just one motor per vehicle; this is a main cost driver, which is a barrier for the industry today.
AMS: Are EV motors going to be segmented in the same way that vehicles are or is it purely based on power output?
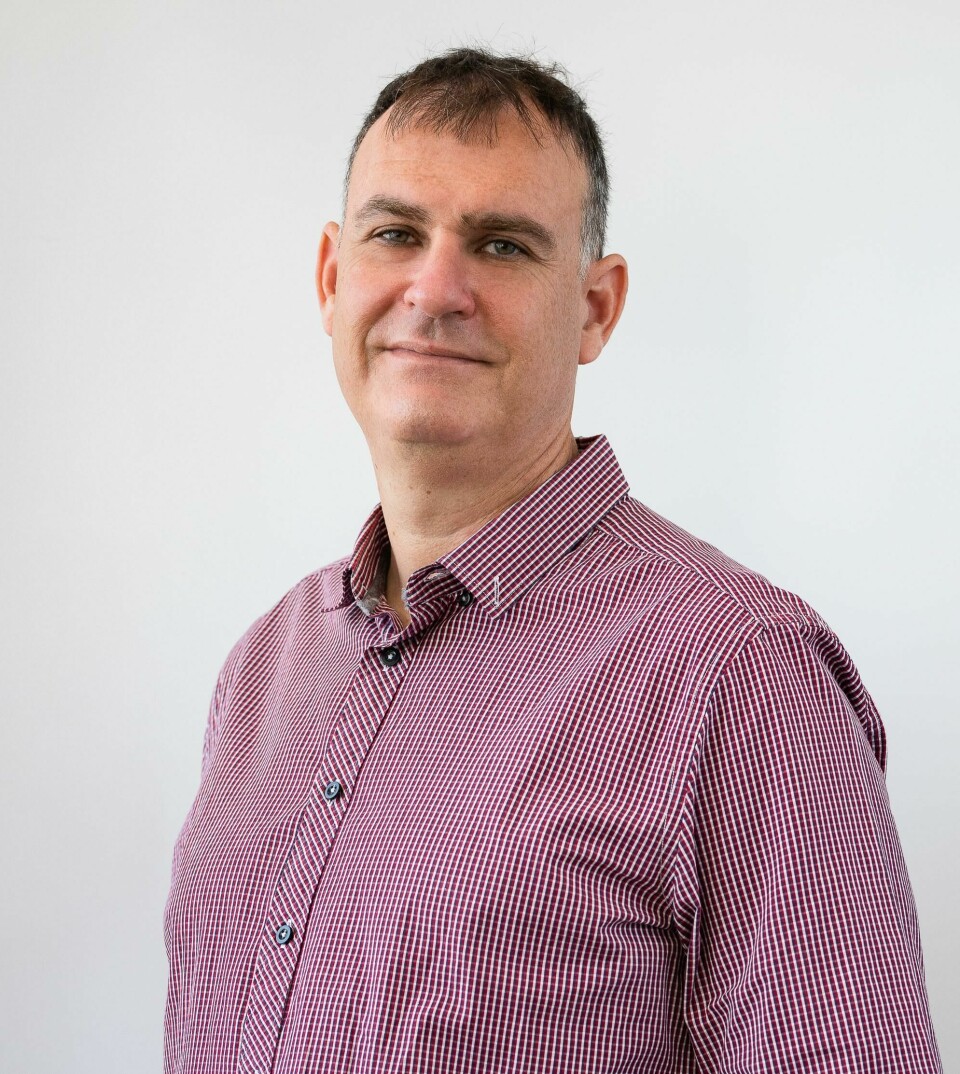
PP: This is an interesting question. Yes, it will start with power levels and this is the first requirement. But because there is no legacy, going back to my comparison with ICE powertrains, when you hear the sound of an internal combustion engine, you can immediately identify, for example, a classic V8 from General Motors. This is not yet the case in the EV sector, but it will come because the OEMs will have to differentiate themselves from others. They need to have their own characteristics, so it will vary with technology.
AMS: Do you see those differential characteristics coming from the software?
PP: Yes, the driving experience will be a major contributor to that. But let’s compare it to phones. Eventually, an EV car will be a phone with wheels, this is what everyone is aiming towards. You have iPhones and Android phones and you can distinguish differences there, so they are not the same. This applies to EVs, but the OEMs will have to find a way to distinguish themselves from others.
AMS: You have signed a contract to produce electric motors in India for the two and three-wheeler market. Could you offer some insight into this?
PP: We are producing brushless motors that don’t use rare earth material components. The use rare earth materials is becoming a burden on the EV industry in terms of cost, supply and in terms of stability of production, so the idea is to have a rare earth material free e-machine, and this will support the next stage of local production of e-machines.
Once you have a stable production line that is not super sophisticated, not using any rare earth materials or any high-end components, it will be easy to make a micro production line wherever the customer requires. And transportation today is becoming more difficult and it will ease things on that side.
I think this is also one of the reasons why [EV] has not had the market penetration that we see with cars, but it’s not the only issue.
The other issue we think is that you always compare it to a standard ICE two wheelers. So, the cheap electric two-wheelers don’t perform the same, they don’t have the same power, they cannot carry the same weight. The feeling is not that good. And this is something that we learnt quite early in the process, so we put a lot of effort in the development of the driving experience and we have had good feedback from the industry on how our controllers and motors feel in a two-wheeler and three-wheeler and, actually, every light vehicle, that feeling and driving experience is a major contributor. It doesn’t feel like a forklift, which is one of the most significant impacts on electric vehicles.
AMS: Is it a challenge to develop a magnet or a rare earth-free motor for automotive applications?
PP: Yes, it’s way more difficult for the automotive industry. Induction motors without any rare earth material component in them are widely used in industrial applications (air compressors, HVAC, etc) but this design of motor is too heavy compared to the power output. Also, these are mostly running at a constant speed, which in a vehicle cannot happen. It will need to vary the speed. So, efficiencies will be high and low, and this affects the battery range.
The other aspect is control and the driving experience. It will feel like driving a ventilator, which is not the way a car wants to drive. So, on the paper it is simple to make a non-rare-earth material motor, but once you apply the specification required for the automotive industry, it becomes much more difficult. And it has to be cheap, it cannot be super sophisticated, it has to fit into the standard production processes.
So, this is the most difficult part and it’s combining all the engineering areas – mechanical engineer, electromagnetic engineer, power electronics, analogue, digital and software.
AMS: We’re seeing a lot of the major vehicle makers have now set up their own electric motor assembly lines rather than outsourcing. What production challenges do you see for car makers in terms of making electric motors?
PP: First of all, quality control. With ICE vehicles if they change a model every couple of years, they know the process, but now with EVs it’s completely different and they have to introduce new processes. Also, there is a great deal of pressure to get new vehicles developed, manufactured and to market. There is competition from a lot of new companies who are entering the EV market.
AMS: In terms of the future development of motors, is this being done in parallel with the development of battery technologies?
PP: I would say that the investment in batteries and the motors are going in parallel. Not really close enough at present, but the OEMs and Tier 1s will mix them together. They know they have to do it and they will have to look at this on a system level where there will be a lot of development.
AMS: Where do you see the most potential for the development of the motors themselves, will it be in materials, production or will it all be focussed on software, motor and power control?
PP: There are some areas of development in the production of motors. So, today most of the motors are using windings but this is a cost driver and other methods of supplying the current or magnetic flux in the e-machine are being considered to lower this cost. But it cannot impact the performance of the motor.