Digital factories need forward thinking
Michael Nash talks to Bosch's Stefan Assmann about changes taking place on vehicle production lines
Stefan Assmann was previously a plant manager at Bosch’s gasoline and diesel systems components facility in the Czech Republic. He is now head of Bosch Connected Industry – a new unit created by the supplier in the hope of helping customers to take advantage of Industry 4.0 solutions. The supplier is currently gearing up to showcase a number of software packages and services at Hannover Messe, which is held in April 2018. Speaking to AMS, Assmann described these solutions, some of which are already being introduced at car manufacturing plants to increase product line efficiency and cost-effectiveness.
Do you think vehicle manufacturers need to do more to increase the efficiency of their plants?
Yes, though many big vehicle manufacturers have already launched appropriate activities. But I think the entire automotive industry must consider digitisation and connectivity as part of its core philosophy. Competition is harsh, and as alternative mobility concepts are being introduced to the market, the ability to adapt quickly to changing market needs is more important than ever.
The car is becoming more individual, digital and connected; it is not only supposed to get people and things from A to B, but it should also be an ‘intelligent actor’ itself. Such a modern product can only be developed in a modern manufacturing environment, and so both OEMs and their suppliers need to implement Industry 4.0 into their processes if they haven’t done so yet.
What type of technologies or processes would you recommend for vehicle manufacturers?
We see digitisation and connectivity as a holistic process, and are aiming to provide solutions that address real challenges. All our solutions are developed to support operators, maintenance staff, production supervisors and factory managers in their daily work.
One example is ‘Open Integration’, which is a harmonised framework of different processes, software systems and applications for production and logistics. It closes the gap in processes between suppliers, logistics, production and point of sale. Weak spots in the process landscape are eliminated without having to re-design processes and their infrastructure, and missing software components can be integrated into the existing landscape.
Open Integration bundles all programs and services with one single and secure login process. For operators, the time-intensive changeover between different services becomes obsolete. Depending on the customer's request, the tool can function as a simple access interface or it can visually standardise programs and consolidate data. Applications from other suppliers can also be integrated in addition to the individual Bosch solutions. This way, employees receive a comprehensive solution for convenient and fast access to their digital tools.
Is this already in use across the automotive industry?
We are currently implementing Open Integration at the facility of a well-known vehicle manufacturer. It will make several different processes on the shop floor, such as energy management, predictive maintenance and performance display, available within one framework by transforming the heterogeneous software landscape into one homogenous picture. This way, different users such as plant managers, floor managers, operators, and service technicians view exactly the information they need with a simple and intuitive look and feel.
Could you provide another example of a technology that may be useful for vehicle manufacturers looking to improve their production lines?
Maintenance work binds up resources – often unnecessarily. With our Maintenance Support System (MSS), long itineraries, diagnostics and coordination times are a thing of the past. The analysis and transmission of data in real-time make it possible to respond quickly and process maintenance orders efficiently, even without extensive and specialised knowledge. The MSS bundles all required information and makes it available to machine operators and maintenance technicians on mobile end devices such as tablets, smartphones and smart watches. This way, repair times can be reduced and machine availability can be increased.
So this could change the way workers on a vehicle production line perform maintenance?
As soon as a problem is identified, the responsible technician receives a corresponding message on a smartphone. Once at the machine, he or she can use the smartphone to call up the fault history from the MSS. If necessary, the technician can call up the digitised documentation as well as images and videos of the machine.
Could this have any other uses aside from production line maintenance?
Aside from error diagnostics, the MSS also simplifies the process for ordering spare parts. The technician checks the spare parts stock for the machine directly on the mobile device, and if the required part is in stock, he or she can reserve it and install it in a timely manner. Finally, the technician documents the operation as well as the restarting of the machine, and then closes the order on the smartphone.
Would vehicle manufacturers need to completely revise existing, more traditional car plants to house these technologies, or could they be introduced quite simply?
Provided a good Industry 4.0 strategy is in place, implementation is not as difficult as many manufacturers tend to think. Some of the older machines can be digitised with starter kits or connected with retrofit solutions, so there is no need to exchange the entire machinery park. But digitising and connecting entire factories necessitates a number of changes, especially for the employees. Their everyday work will definitely change for the better, as long as all members of staff are involved from an early stage to achieve a smooth transition.
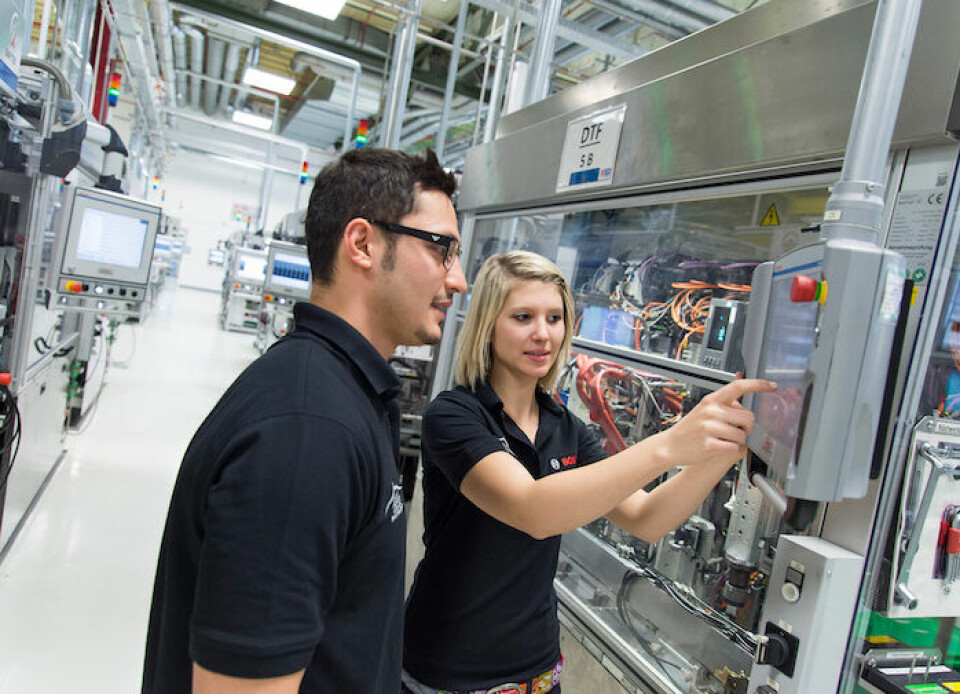
How can Bosch help carmakers digitise entire factories from scratch?
We see lean management as basis for process optimisation. Once the basics have been implemented, we design a connectivity strategy together with our clients. What make’s Bosch’s offer special is our pool of experts we have available for different industries. So if a vehicle manufacturer wants to start a project with us, we will work with our colleagues from Bosch’s automotive sector to develop the best possible solution.
Are there any drawbacks to investing in digitalisation and connectivity in manufacturing? For example, could it cause any problems in terms of uptime or safety?
Only a badly planned or implemented digitisation and connectivity process can lead to negative results. This is why we focus on consulting our clients from the very beginning and on preparing the transition process in detail. In the long run, digitisation and connectivity is sure to increase machine availability and security. A faulty part would never go unnoticed in a fully connected factory, and solutions for preventive or predictive maintenance make sure that machines are serviced and spare parts are replaced before a possible malfunction. The entire production process is less prone to errors, leading to increased product quality.
Do you see the car factory of the future as completely different to what it is now?
Not be completely different, but a lot things will change if everything and everyone is connected. For example, production modules could adapt autonomously to the parts that need processing and run their own diagnostics. Software tools will simplify the commissioning, integration, and configuration of all components. Operators will not need to have extensive programming knowledge, as smart devices would help them to adapt workflows and perform the required maintenance activities. Virtual real-time representations of machines and processes, as well as open standards would form the basis for horizontal and vertical integration, and thus for the seamless exchange of information. By connecting value streams and by combining the strengths of humans and machines, vehicle manufactures can react to the challenges of today and tomorrow.