Hot on the press
The need for lightweight, high-strength steel parts has been given a boost with increased production of electric vehicles. AMS reports on a new hot stamping process designed to meet this demand
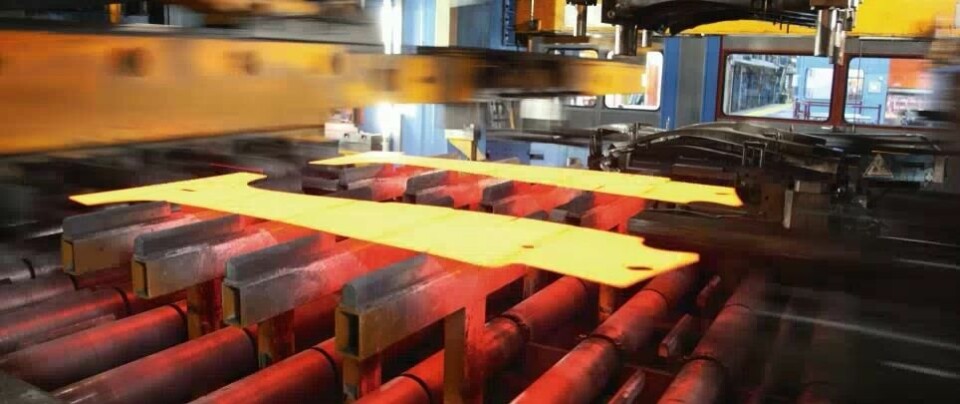
Pressed steel parts manufacturer Gestamp has developed what it says is its fourth-generation hot stamping process. The company has been producing hot-stamped parts for a number of years, supplying complete door rings for the American market and parts for door inners, which are said to reduce the weight of the inner doors by 20%. The latest application for hot-stamped parts are the battery boxes for electric vehicles, and these have presented both OEMs and tier suppliers with a set of new challenges.
Ignacio Martín González, general director of body-in-white (BIW) R&D, explains how the new Multi-Step hot stamping technology at the company’s Bielefeld plant in Germany will advance the production of high-strength steel parts: “This fourth-generation technology allows us to achieve several goals; we can reduce the weight and the cost of the parts. Also we can increase the performance. This is exactly what the EV market is expecting from us.
“We can see there’s a move from steel to a multi-material mix gradually coming into electrical vehicles and this is mainly driven by the battery boxes.”
Speeding up the process
While hot stamping allows pressed parts to be formed from very high-strength steels, one disadvantage has been the slower speed of the process, with the required heating and cooling of the steel and the subsequent need for laser trimming of the harden parts, compared to cold forming. González notes that the new Multi-Step technology would overcome these issues. “We will have a high-speed hot stamping process that now operates at the same speed as cold stamping, and that eliminates the laser cutting operation,” he explains. “It also enables us to create more complex geometries that until today we were not able to do.
“With this technology we load the parts much faster than in conventional hot stamping. To do this we are using double loading, twin robots, and loading eight parts at the same time. We are also using a new type of furnace, and can now feed the part into a computer-controlled tool at the same speed as in the cold stamping operation.
“The tool reduces the material’s temperature from 900°C to 500°C in 0.2 seconds and this allows us to form the part in each station and to harden the material to exactly the same hardness grade that conventional hot stamping produces, but without the need for any laser cutting operation. So, this new technology produces, in this case, two parts per stamping operation in a ready-to-be-assembled state. We were able to produce the same part with three times more productivity than before”.
Developing this technology, Gestamp designed the process simulation and performed the validation on its G-Labs car model. They also designed the lines that now being used serial production. The company says that using this hot stamping process means it has the capability to produce all the safety structure-related parts of the car, for both combustion engine and electrically powered cars.
“It’s important to understand the thermomechanical development,” says González. “What we do in this technology is not stamping as in hot stamping in one shot with the part. We are cutting the part, transferring, making a [drop operation], and then cooling the part in different stations. And for this process we’ve developed a [forming] simulation.
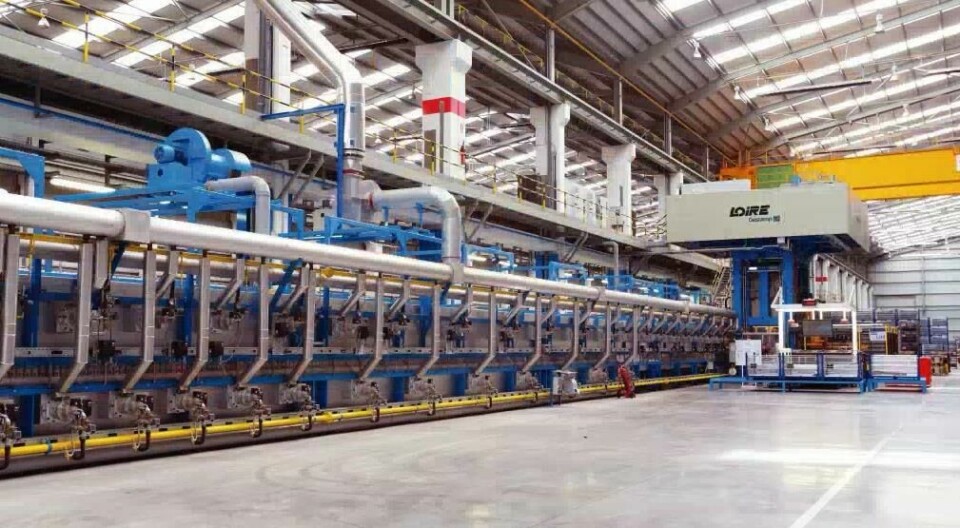
Hot stamping, weight saving
“The big advantage is in the weight saving that we can create with this type of product. For example, a typical [car] body, which is on the market today, has at least 11% hot-stamped content. We redesigned this body in our G-Lab cars to a body where we applied all the Multi-Step formed parts. The result is we can reduce the full body weight by 7%, which offers a 3% CO2 saving over the lifetime of the car. This representation of CO2 reduction over a lifetime cycle of the car covers diesel and gasoline cars, as well as on electric vehicles”.
One of the biggest challenges has been creating a suitably strong but lightweight structure for the battery box on EVs. This has to meet a number of strict criteria for crash resistance and weather proofing, as well as being an integral part of the vehicle’s structure. The EV BIWs have to be manufactured in high volumes, cost effectively and offer flexible platforms for multi-model applications.
González explains how Gestamp has approached this challenge: “The battery box design is slightly different, depending on the type of car. A small city car might have a small battery box, weighing 390kg. A city segment car’s battery box may be over 400kg. And the big SUV sized car can have a battery box up to 650kg.
“We can see there’s a move from steel, to a multi-material mix gradually coming into electrical vehicles and this is mainly driven by the battery boxes.”Ignacio Martín González, Gestamp
“This weight in the lower gravity part of the vehicle completely changes the crash structure. In our model of the cars that we are developing, we are using these [new hot-stamped] technologies. For example, for our all-new small city car the battery box is a non-structured part. That means the battery box is smaller than the body of the car and it’s surrounded by a hot-stamped frame produced using the Multi-Step process. So, we have the battery box protected with a new style of steel inside.
“The result of this holistic approach is that we can validate the battery box inside the car with all the hot-stamped parts, and we are able with our own [G-Lab] cars to validate the full system and how it works. So, we’re not a single part provider, we are a solution provider for the complete functionality of an electrical vehicle inclusive of the battery box”.
Simulating crash structure performance
To highlight the crash protection levels required for EV battery box structures, Gestamp has created a 3D crash simulation that demonstrates the deformation of the vehicle (and battery box) structure in a variety of crash scenarios, at different speeds and angles. The detailed simulation replicates the crash-esistant properties of the different steel grades used in the BIW, allowing engineers to see how and where certain materials perform best, optimising the structural design and validating its performance.
The shift to electrically powered vehicles continues to throw up new challenges for both OEMs and tier suppliers, the latter being called upon to deliver not just components but complete engineering solutions. As Gestamp’s Multi-Step hot-forming process demonstrates, there is now a big focus on developing new manufacturing solutions to build the next generation of vehicles.