Collective thinking
Closer collaboration between product development and production teams could lead to significant improvements in vehicle manufacturing processes. Ford Otosan holds a unique position. Michael Nash reports
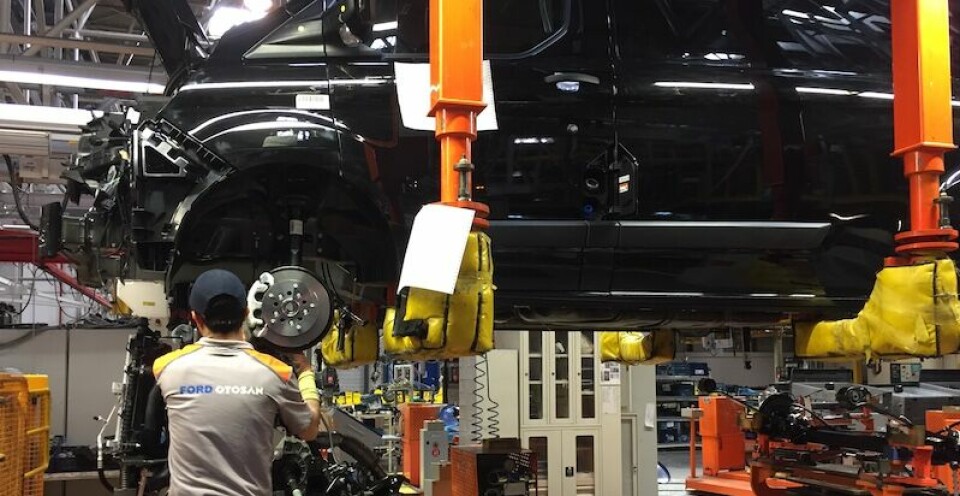
The scenery in Turkey is full of surprises. A quick car journey can lead to towering mountains, pristine beaches and lush forests, while historical ruins and ancient structures pepper the countryside. On the north-western side of the country, however, huge industrial factories sprawl for miles across the landscape, churning out everything from textiles to cars.
According to a recent Bloomberg article, Turkey’s economy grew more than China’s and India’s during 2017. It suggests that the country has rapidly recovered after a slump caused by a failed military coup in July 2016, and points to continuous strong demand throughout 2018. Total vehicle production increased by 13% compared to 2016, 80% of which was exported. One of the companies that took advantage of this growth was Ford Otosan.
Its Gölcük and Yeniköy plants are situated in the Kocaeli region, two and a half hours south-east of Istanbul. With annual capacities of 315,000 and 110,000 units respectively, they are separated only by a small river that is maintained by the OEM and runs into the Sea of Marmara. From here, the company operates a private port that ships its Transit, Custom and Courier light commercial vehicles (LCVs) all over the world.
Gölcük is the only global production base for Transit Customs, but it also houses the production of the Tourneo Custom. The plant covers an area of 1,600,000 sq.m, and includes a tool-and-die centre, a pressing facility, a bodyshop, a paintshop and assembly area. Central maintenance, production planning and quality assurance departments are based in separate buildings.
The Yeniköy plant is much smaller. It is where the Transit Courier and Tourneo Courier are made and, according to Ford Otosan, it is the only plant in Turkey where “all activities aimed at creating a complete production environment including construction, vehicle design from scratch, prototype manufacturing, and installation of production lines were carried out simultaneously.” As a result, it was constructed over the course of just 16 months.
Although they are situated in a small and rather dated-looking town, both plants are surprisingly modern and well equipped. The Yeniköy plant opened in 2014, making it the first automotive plant established in Turkey in 13 years. In contrast, Gölcük opened in 2001, but has since benefitted from several large investments. In August 2017, for example, the company spent $52m to expand its output by 12% and, since 2013, efficiency at the plant has increased by 23%.
AMS sat down with Cem Temel, head of the Gölcük and Yeniköy plants and assistant general manager for new projects at Ford Otosan, to discuss these improvements as well as plans for the future of LCV production in Turkey.
AMS: Its quite unusual for one person to be head of two plants as well as a separate ‘new projects’ unit. Can you explain the benefits of this?
Cem Temel: I took over as plant manager at Gölcük in 2012 and then four years later was asked to head up Yeniköy. So, now I am in charge of both and have two plant managers reporting to me. I’m also in charge of a ‘new project’ office, which was set up in 2016. 55 white-collar workers provide data on how to manufacture new models and how much it will cost from a very early phase of a model, even before clay work is done. They make evaluations of each part, give feedback to the product development team, and outline the specifications for the tools and facilities needed for the new programme. So the design, manufacturing and engineering all come under one umbrella, which gives us a considerable amount of flexibility and high information flow.
Which of these responsibilities takes up most of your time on a daily basis?
I’d say 25% of my time is being spent on current production projects and issues, while 75% of the time I’m focused on future manufacturing technologies and products. These technologies and products are split in to two groups: the short-term, which covers the next one to two years, and the long-term, which covers the next three to six years.
How do you prepare the plants for vehicles that may be introduced to your portfolio in the next three to six years?
The plants have a roadmap, which we have defined, and we start introducing production technologies and adopting certain principles as we follow the roadmap. We also carry out pilot manufacturing projects to verify whether or not it is practical to make new vehicles. These projects will often leverage innovative technologies to make sure the process is as efficient as possible, and this gives us a very good idea of how to adapt our plants to prepare for the future.
Could you outline the primary method that Ford Otosan has used at its sites in Turkey to improve production efficiency?
The first is having a firm base in automation. We wanted to increase the number of robots we use, but cost was a big challenge. We were getting quotations from European and US companies which were very high, so we prepared a so-called ‘grey model’, in which we decided to only buy robots from European countries. And then, with our in-house engineering, we designed automation cells. Between 2016 and 2018 we installed 150 TAR robots and we learnt how to program them, increasing our automation level in body construction from 60% to 92%.
What savings were achieved by programming the robots and designing the cells in-house?
We were able to reduce the cost of this kind of investment by up to 60%, which is huge. So now we have a principle in place to not invest in any more turnkey solutions. And the robots have also allowed us to increase efficiency and capacity by about 23% and 20% respectively between 2013 and 2018, which has saved us a lot of money.
What impact has this growing level of automation had on the number of people working at Ford Otosan?
We have actually kept all our employees who were previously working on the manual lines. But as the level of automation on production lines increases, people will have different jobs and will need different talents. We have a technical high school here with a training programme for all of our employees on the maintenance side. It includes a laboratory with a small production cell containing different tools, such as PLCs, sensors, software programmes and physical handling units. So the maintenance workers can get a really good idea of how increasing digitalisation in the factory will change their roles in the future.
Do you think there will be any employees left working on the production lines in the next five to ten years?
In the future, these workers might be spending around 70% of their time on production and 30% of their time on low-level maintenance. Both sides should interact and work together. We have 6,000 people working here and we can’t cut that number, its not possible. So the method is to use lean manufacturing principles, working in parallel with robots.
Are workers worried about losing their jobs to robots?
We have an incentive system whereby employees are paid if they identify improvements to production processes. They will receive 4% of the total saving or €800 ($933), but the improvement must be physical not theoretical. The employee must make the change and show us how it works. Many of these suggestions lead to an increase to automation levels, but if it gives us efficiency gains then the workers will be rewarded.
What kind of challenges come with increased automation?
One of the major challenges is the growing amount of data coming from production lines, and finding out how to use it positively. A while ago we decided to create a common communication platform to connect each PLC from thousands of different robots and machines. With this, our ‘big data’ journey started, but it failed because we found that the amount of data we collected during each millisecond was so enormous. So we started another phase of engineering and lowered the data requirements. We contracted local Turkish firms to help us and then we put together a team from Ford Otosan made up of the workers on maintenance and workers in IT. It took two years to define the system internally, and it is still a work in process.
What uses do you think this common platform will have?
We are now beginning to analyse the data that we are getting from all the machines, and have started some pilot projects using the data for predictive maintenance. These pilots have been going on for the past two years, but honestly, the technology isn’t ready yet. We’re testing the software here in our Gölcük paintshop and body construction along the actual production lines. If we see a big benefit we will decide to bring it in, but we haven’t had satisfactory gains yet.
Aside from predictive maintenance, can you use data from other areas of manufacturing to improve your plants?
Quality checks come in many different forms – weld data, paint raw materials, sheet metal quality and so on. These are often kept in excel spreadsheets or other people-orientated systems. We are preparing a digital vehicle identification number (VIN) platform for all quality data. If one of our operators enters a VIN, they will get all the quality data for each vehicle. It’s a huge project.
Is it so big because of the amount of data you need to put on the platform?Yes, because each vehicle is different from the other. We’re starting to put cameras in some production areas that the vehicle passes through. These are linked to a system that has a checklist for all the features that the vehicle should have, such as a painted bumper and a large electrical mirror. The system is trained to identify what is what, and if the features are all there, the vehicle can pass to the next stage. All of this type of data will be stored.
What does the term digitalisation mean to you?
Digitalisation it is not a new concept in the industry, but it will be for Ford Otosan. Here’s a confession: our production lines still use paper. We’re going to use digital screens instead, starting with a pilot project in December 2018. Each vehicle will be defined on tablets, and the operators will verify which part is going where on the screen. He or she can then also confirm the quality of each process with a signature.
Do you see any benefit in adopting more advanced digital tools in the manufacturing process, such as virtual reality?
Today, we have a computer screen on which product development sends data to be evaluated by the engineering team. But the engineers can’t see the real production environment, so we are currently scanning our entire plant with a high-resolution camera. Once we’ve done this, our engineers will be able to do everything in this digital plant, making sure it all works before spending money on pilot projects or implementation. The second stage will be to integrate component data to the digital plant, which we will be doing in February 2019. Then the third will be designing manufacturing facilities and testing production technologies in 3D. Once we have all this, we can make changes to both the plant and the vehicle to make sure that the production processes are as efficient as possible.
Are there any trends in the industry that could play a key role shaping Ford Otosan’s future?
From the product point of view, the entire industry is talking about electrification. There’s no doubt that it will come. Autonomous driving technology is also a hot topic and will probably first be introduced with large commercial vehicles that are operating on fixed routes. There will also be more personalised features in vehicles, which means high complexity from a manufacturing point of view. Many different parts will need to be fitted correctly to the vehicle. Lastly, customer satisfaction and quality is and will continue to be very important, so traceability is crucial.
How could vehicle electrification change plant layouts?
Nobody really knows what the share of electrified vehicles will be, but I think the ratio of them could go up to around 30% during the next few years, while 70% of vehicles will still only have internal combustion engines. One thing is clear: the demand for batteries will rise dramatically, and these will need to be assembled in the plants before being married to the vehicles, not shipped from somewhere else. This will have a big impact on plant layouts, but we are prepared for it already as Ford previously announced that all models will include electrification in some form, including the Transit. The underbody of vehicles will also be made differently to account for the heavy and bulky batteries.
Will autonomous driving have a similar impact?
We don’t yet have much involvement regarding the autonomous driving trend at the moment, but it will have a big impact on the way that electronics and software is built in to the vehicles. There will also be more severe quality checks during the manufacturing process, because these systems are safety critical and therefore must be completely robust.
What are your thoughts on multi-material vehicle designs and how could they change the manufacturing process?
If we are still considering electric vehicles, then weight needs to be reduced because of the heavy batteries. There will be boron composites, which are currently under development, while aluminium usage will also increase. We do use boron and aluminium today, but the ratio will climb. There will likely be a trade-off between weight, cost of the material and then efficiency of using it in production.
What will the greatest improvement to vehicle manufacturing be in the next ten years?
There will be a stronger relationship between product development and manufacturing. They currently have very different priorities, but they also want to achieve the same goals. There must be flexibility, and as they learn, they will understand each other and work effectively together. Also, they can both leverage the digital plant. Engineering will look at it to see what design parameters they have, and the manufacturing team will give them pointers on what is possible. This kind of relationship probably won’t surface until 2025 or beyond, but when it happens it will make me very happy.