Waste not, want not
How GM and Michelin are achieving the goal of zero waste-to-landfill, what is required to set up the internal processes, and whether there is any money to be made from programmes such as these
At the Flint South plant of General Motors in Michigan, around 15 machining centres are used to manufacture engine parts. In doing so, these machines inevitably generate significant amounts of steel or aluminium swarf. There was a time that nothing could be done with this leftover material; it would be sent to landfill, together with the filter media used to separate it from the coolant fluid that had removed the swarf from the machining location.
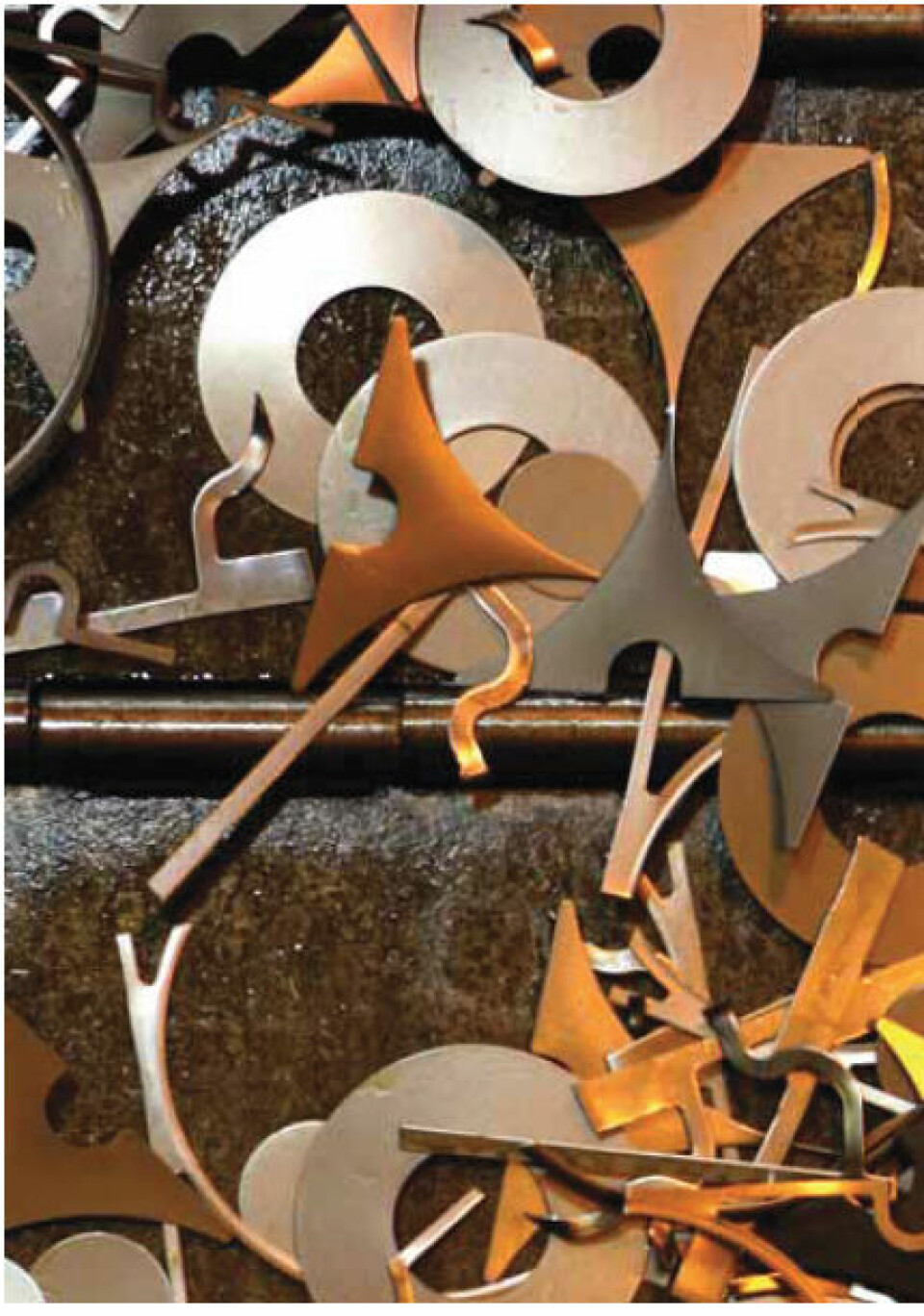
Now, Flint South has put a zero-waste-to-landfill policy into operation that includes these metallic leftovers and used filters, as well as all other effluents and residues. In doing so, the plant has succeeded in solving the what is described as the most difficult challenge that an operation of this kind is likely to encounter in achieving a zero-waste goal.
This is the assessment made by Glenn Rowe and Chuck Sorrick, co-founders of Crystal Filtration, located in Rochester Hills, MI, and its subsidiary company, Waste Free. Both companies combine services to GM that have enabled the carmaker to crack this particularly tough nut. Rowe and Sorrick have been in the filtration business for more than 20 years, but the specific process that now operates at Flint South is one they developed during the last decade. The filter media is generally a large roll of plastic material, 2.3 metres in width and up to 250 metres in length. The precise composition of the rolls varies according to requirements, primarily dictated by the size of the swarf particles. The material itself is most likely to be either monolithic polypropylene or a 50/50 mix of polypropylene and polyethylene, though in some instances the mix is polypropylene and cellulose.
According to Rowe and Sorrick, the average lifetime for one of these rolls is a week, although depending on usage they can last the better part of a month before they need changing. That part of the process is conventional enough; the innovation is in what occurs after replacement. Used rolls clogged with swarf and some residual coolant are taken to the Waste Free plant, where the first task is to drain off any free coolant. The filters are then sorted according to whether they contain ferrous or non-ferrous material, the latter invariably aluminium. If the swarf is aluminium, the rolls are brushed to remove loose metal. Accounting for as much as 10% of the total content, this is sent for recycling. This is done with aluminium-laden filters as the retrieved material can be sold for a profit, unlike ferrous metals. The rolls are then subjected to a process of shredding, heat treatment and compression, which results in pellets composed of compacted filter material and swarf fragments. Pellets containing aluminium are used to make cement, while others are sent to a partner company where the metal content is fully-recovered for appropriate reuse, with some possibly being used to make new GM vehicles. Either way, none of the material involved ends up in a landfill. The process, though, is not entirely new. Crystal Filtration has been dealing with swarf and filters from Flint South for the last five years and has recently started to handle similar materials from GM’s Toledo transmission plant. It has, though, been enhanced with the construction of the current Waste Free facility in 2008, at an investment of around $700,000.

Even for this single process the relevant figures are considerable. The total weight of material received at Waste Free from the Flint South and Toledo plants between January 2009 and July this year was almost 163,000kg (360,000lbs), though monthly figures can vary. Currently, deliveries range between 13,000 and 27,000kg (30,000 and 60,000lbs) per month. Of the total received to date, approximately 60% (by weight) is ferrous metal and 20% aluminium, 15% is mixed plastic and 5% moisture. There is also some minimal capture of free oil, about 1,400 litres (300 gallons) over an 18-month period, with captured fluid sent to General Oil, GM’s designated handler of waste oil.
The process has a number of interesting ramifications, concerning both waste recycling and the automotive industry in general. One of these is a possibly significant innovation; with long experience in the filtration business, Rowe and Sorrick say: “You can never get all the metal out of the filters and so you need a process that uses it.” A considerable time had been dedicated to developing uses for metal-plastic mixes in an attempt to circumvent the persistence of metal fragments in the mix, the particles causing myriad problems. Glenn Rowe: “Putting metal into plastic is like putting information on the internet – you never know where it will end up.”
For the automotive industry, it serves to demonstrate that there are no insurmountable barriers to achieving zero-waste-to-landfill. Both Ford and Chrysler have looked at the process, the latter going so far as to carry out a formal process audit. The company is currently on track to introduce the process for relevant waste streams at four of its US plants by the close of 2010.
Meeting internal targets
For GM, zero-waste-to-landfill is already a well-established policy. According to John Bradburn, Design and Environment Programme Manager based at the OEM’s Warren Technical Center, the carmaker is well on track to achieve a target of 50% of its worldwide plants recording zero-waste-to-landfill by the end of this year – a strategic goal set in 2007. He reports that by the end of July, fully 69 of its sites were already operating to this level of environmental efficiency, with a handful more only marginally short of that initial objective. The official 50% target figure, he explains, could be met with the addition of just another three plants, bringing the total to 72, keeping in mind that the target is not stationary, with plants opening and closing. It should be noted that Flint South achieved zero-waste-to-landfill in 2005, officially the first GM plant to do so. Bradburn confirms the global nature of the policy and provides some interesting figures on regional achievement rates. The respective percentages for GM plants that have already achieved zero-waste-to-landfill (by continent) are: North America, 47%, Asia-Pacific, 57% and Europe, 65%. The one region lagging behind is Latin America, which Bradburn attributes to the lack of appropriate support infrastructure.
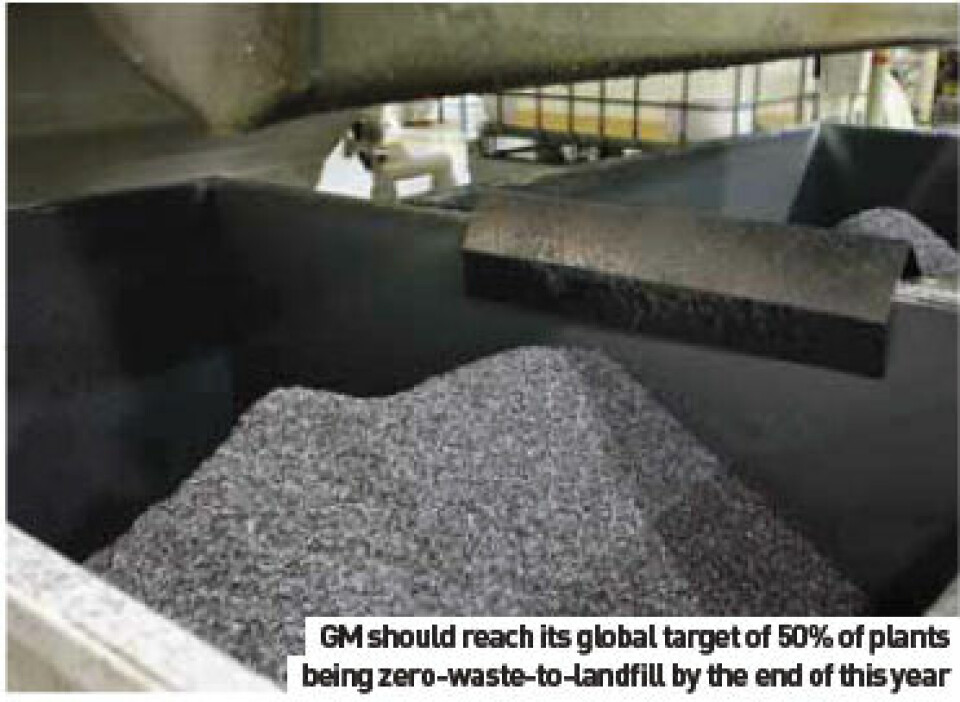
The motivation for the policy is not primarily financial, though without providing figures Bradburn says that it is possible to identify specific savings – sometimes ones that are “significant”. The initiatives, though, are largely financially neutral, a policy that pays for itself. “There have not been any significant cost increases,” he confirms. Bradburn says that there is more to the policy than dealing with process waste, even if that is where the biggest challenges are encountered. For instance, one idea has seen marked parts packaged and sold as aftermarket equipment; parts which would have otherwise gone to scrap. “It is a very good alternative,” he notes.
Modification of processes so that previous waste streams are reduced - or eliminated – is another tactic employed by the carmaker. Bradburn says that a move away from barium-based welding wire has resulted in a marked decrease in the generation of slag and dust. But while some measures may be specific to particular plants because of the procedures carried out there, the successful implementation of this kind of policy is about the application of broad, generic principles. For international companies like GM, a successful scheme is one that can be rolled out on an international basis, with lessons learned in one location being applied elsewhere. As Bradburn says, “We can leverage our global manufacturing base.”
He indicates that the the successful implementation of a zero-waste-to-landfill strategy depends on people and procedures rather than technology. With regards to the first of these, one of the necessary preconditions is the broadbased enthusiasm and participation of employees. Providing there is effective communication of the objectives involved, Bradburn indicates this is relatively straightforward. “It is something everyone can relate to,” he explains. What follows is the “communication of best practices and their application based on experience.” The second is related to how qualityrelated initiatives are implemented and monitored. “It did not require any major change in out culture or procedures,” he says. “It is now part of our systems and metrics.” The relevant global figures for the company appear impressive. Bradburn says that on a worldwide basis, he expects that over the current year GM will redirect around two millions tonnes of material that would otherwise have gone to landfill. He adds that this represents some 90% of all relevant material, taking into account the fact that a lot of plants that may be not yet have attained the zero mark, yet still recycle a considerable amount of waste. Nevertheless, Bradburn makes it clear that application improves with experience. “If we started out all over again, we could do it much quicker,” he says.
Recycling tire components
Much of what Bradburn reports is echoed in Ballymena, UK (located in Northern Ireland), at a manufacturing facility operated by French tyre producer Michelin, where 900 employees are involved in the production of large truck tyres. More relevantly, it is a site at which Michelin is planning to complete implementation of a zero-wasteto- landfill strategy, covering both process waste from manufacturing operations and also general waste from non manufacturing activities including the cafeteria and offices. Michelin’s Paul Kinkead confirms it is a highly-successful strategy, the site achieving its process target in 2008, only three years after initiating the project. Although the recycling of general factory waste is still not quite 100%, as of mid- 2010, it was finding non-landfill outlets for 96% of all materials.
Kinkead has been environmental manager at Ballymena since 2007, and headed up the final push to achieve zero process waste to landfill. Interestingly, and despite its UK location, the achievement has made Ballymena the company’s benchmark North American site in terms of environmental achievement, the plant being part of the company’s North American group. “We are two to three years ahead of the sites that are actually in North America,” he confirms.
Accordng to Kinkead, the formal initiative did not start from scratch. Even in 2005, the plant was already recycling 29% of its process waste, but this was all ‘Grade A’ rubber. Materials going to landfill comprised lower ‘B’ and ‘C’ grade rubber, plus various powders, composites and what Kinkead describes as “metallic tissue”. This represented around 1,400 tonnes of material each year, to which another 680 tonnes of general waste was added.

A cost-neutral initiative
By the time Kinkead took over, the initial figure of 29% had been increased to 62% and the basic project principles were firmly established. Kinkead says this was to see all the materials involved not as waste but as “assets to be realised.” In other words, all material has the potential to be used productively elsewhere and all Michelin had to do was find appropriate customers. “We had to find economic outlets,” he confirms. “We are still running a business.”
Kinkead says that consistent application of this principle has ensured that the whole initiative has been self-financing. He stresses, though, that this does not mean that every single waste stream can be recycled profitably. Taken in isolation some will make a loss, but by proper balancing of assets and liabilities, the overall operation can be – and in the case of the Ballymena plant certainly is – cost neutral. But, in turn, this means that one of the essential underpinnings of a successful recycling initiative will be relevant business acumen. “You have got to know the spot market price for the materials,” Kinkead explains. “Frankly, you have got to become something of a commodities trader.” This means that in the current market, an offer of less than £80 ($140) per tonne for shredded tyres wouldn’t get very far. As such, all relevant sources of information need to be identified and utilised. In his own case, he says he makes use of an on-line marketplace called the Environment Exchange and is also part of the government-sponsored Producer Responsibility scheme.
As far as the internal organisation of the project is concerned Kinkead, like Bradburn, argues that workforce participation and the implementation of appropriate procedures are the key elements. He also confirms that the overall approach is similar to that used in initiatives aimed at such areas as quality management. In Kinkead’s case, the connection is quite explicit; he is also quality assurance systems manager at Ballymena and industrial hygiene manager for Michelin across the whole of the UK. Kinkead goes on to say that some of the necessary procedures, most obviously the sorting of waste rubber on the shopfloor, were already established when the initiative started. It is also pertinent that, quite separately from the recycling initiative, the Ballymena site has also been the location for an intensive campaign of continuous improvement built around the classical principles of targetsetting and teamworking. This means that everyone at the site is familiar with the concept of identifying and then achieving quantifiable process improvement goals.
People power
There have been some specific personnel changes implemented in order to support the recycling project. Paul Kinkead says that he was particularly impressed by the role of an ‘area waste coordinator’ that he saw at Michelin’s plant in Lexington, South Carolina. The individual in question was a ‘waged employee’ who in addition to their normal duties, had responsibilities related to materials recycling. The same model has been adopted at Ballymena, though with the additional reinforcement of some of the roles involved being made full-time. There are now seven such ‘environmental champions’ at the plant, reports Kinkead, three of which are full-time.
One of those staff is entirely dedicated to dealing with the recycling of just one particular waste stream, a ‘metallic tissue’ comprising a sandwich of brass cables between two layers of rubber used to reinforce tyres. Kinkead remarks that this was one of the materials that still had to be dealt with by the recycling programme when he took over and that it was probably the most difficult single task. Operations at Ballymena produce some 300 tonnes per year of triangular off-cuts from the original material rolls, enough to ensure that the individual involved can spend all their time in its collection, packing and labelling before it is shipped out of the plant.
Kinkead adds that this is also one of the waste streams that does not produce any profit when assessed in isolation. Sending it to landfill would only cost the company £75 per tonne, whereas recycling it actually costs £100 per tonne. But, as he stresses, such a situation is unavoidable if zerowaste- to-landfill is to be achieved, paid for by the real profits generated by other materials. The overall project has involved no substantial capital outlay, other than the creation of a small marshalling yard and on a day-to-day basis, it pays for itself. That is a fact from which he draws a tenet of fundamental importance about the whole project: “It is a myth that recycling is expensive.”
Academic analysis
Another certainty is that recycling and the ‘greening’ of manufacturing operations is now high on the agenda of every major automotive manufacturer. It is, in fact, of “strategic” importance. That is the verdict of Breno Nunes, a teaching fellow at Aston University in Birmingham, UK. Joint author (with colleague Professor David Bennett) of a comprehensive study of current trends in the global automotive industry, including a comparative analysis of the activities of three of the biggest companies, GM, Toyota and Volkswagen, Nunes says that companies have now recognised the connection between the environment and general efficiencies of their manufacturing processes. As such, cost-cutting dovetails neatly with more altruistic motives as a major driver of environmental process improvement campaigns.
Nevertheless, the practical details of how such campaigns are actually planned and implemented are subject to variations in external local factors, such as the transport infrastructure, and company culture. With regards to the first, he points out that relevant planning in Europe can usually take account of the availability of economically-viable railway freight transport whereas that is frequently not the case in the US. As for the second, he says that of the three companies covered in the study, “Toyota seems to be ahead”.
Ultimately, Nunes argues that the environmental footprint of the automotive industry is predominantly determined by its products and not its processes. “The biggest challenge will be to lower the environmental impact of the products themselves,” he confirms. Accordingly, he cautions that unlike internal production operations, the situation is beyond the control of individual manufacturers as it depends on “cultural behaviour, legislation and the actions of competitors”. That said, the evidence still points to the environmental enhancement of internal manufacturing processes as being worth the effort