Electric ovens – sustainable, efficient paintshop technology
Climate neutrality, increased costs and uncertainties with the natural gas supply are prompting car manufacturers to intensify their search for alternatives to gas-powered production plants. Dürr discusses how its electric paintshop ovens can significantly reduce CO2 emissions
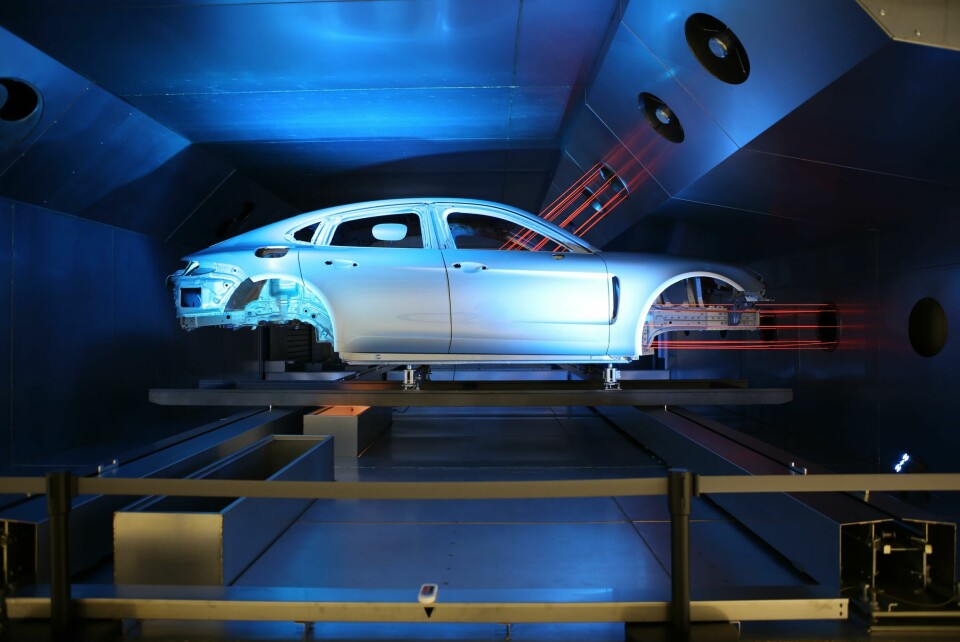
In response to these ongoing challenges around sustainability and rising energy costs, Dürr became the first supplier to electrify all the body ovens in its portfolio. The first reference project with green electricity – in use since 2018 in a paint shop in Scandinavia – proved that was is no change in the drying process quality, which remains at the highest level.
The biggest energy consumer in the painting process is body drying. And its share of the CO2 footprint is accordingly high. By switching from natural gas to a sustainable energy source, like green electricity, it is possible to reduce a conventional paintshop’s CO2 emission by about 40%, which is a big step towards climate-neutral production and greater supply security.
All Dürr ovens – from the traditional oven to the EcoSmartCure compact to the innovative EcoInCure with body drying from the inside – can operate with future energy sources. In addition to favoured green electricity, conversion to hydrogen and biogas is also possible. In developing these electrically powered ovens, Dürr can provide not only the electrification of new ovens but also in brownfield retrofits. The company says it offers individual assessments for existing plants to develop an optimal conversion concept so manufacturers can achieve short conversion times, and outstanding cost efficiency.
Reducing costs through energy efficiency
Further increases in fossil fuel prices are expected in the medium term, while the costs for regenerative plants are falling as the number of installed plants grows.
“We have developed a complete concept with several energy efficiency modules so that car manufacturers can already leverage environmentally friendly green electricity for cost-effective production,” explains Heiko Dieter, Product Manager at Dürr Systems AG. “With a state-of-the-art insulation concept, skidless conveyor technology, and our EcoSmart VEC oven control system, we are coming at this from many directions”.
Lowest exhaust air temperatures
The Oxi.X.RV air pollution control system works electrically according to the principle of regenerative thermal oxidation (RTO). Dürr offers a complete concept consisting of electrically heated ovens and electric exhaust air after treatment. Electric heating uses the RTO method, which decouples heating and air pollution control. Decentralised, compact individual units provide heat. The units have the additional benefit of streamlining the layout since large duct systems for supplying heat are no longer required. Highly efficient heat recovery means that manufacturers can use the energy in the exhaust airflow almost completely for heating fresh air. This reduces energy losses via the exhaust air to an unprecedentedly low level.
Needs-based control of the electrical supply
Another energy-efficient tool is the predictive EcoSmart VEC fresh and exhaust air control system. The intelligent software regulates the oven’s electricity consumption by tailoring the energy demand to the exact number of bodies in the oven and reducing consumption during operation at partial load. Switching to skidless conveyor technology like Dürr’s traverse technology also saves energy since the oven heats less material which needs to cool down later.
No change to the painting process with electric body drying
Dürr notes a sharp increase in the demand for electric ovens. “Currently, we have several projects in the pipeline. As the only paint shop supplier, we can offer a complete package for the electrification of dryers and air pollution control, combined with energy efficiency technologies for reducing operating costs”, says Heiko Dieter. “We are putting all this into practice with products from our portfolio. For our customers, switching to electric body drying is completely risk-free. With no change in the usual Dürr quality and no change in the drying conditions, the only change is in the energy source”.
Find out more about these technologies here