Smart savings in paintshop energy
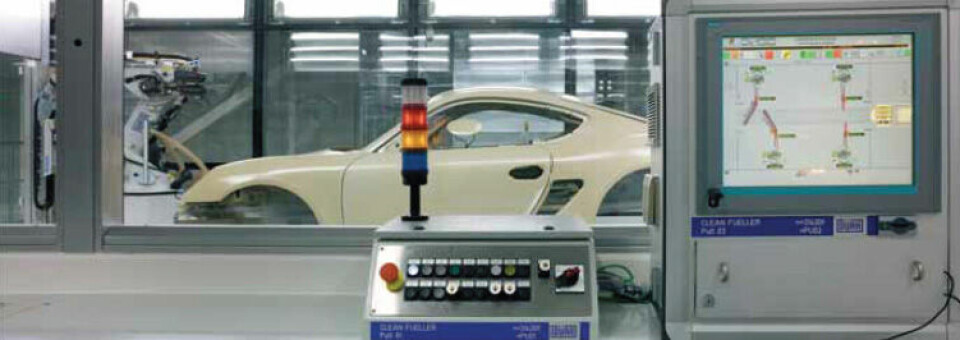
Ulrich Schrickel of Siemens explains how modern technologies and solutions can improve energy efficiency in the paintshop
In terms of energy used in a car plant, the paint shop is undisputedly the biggest consumer, accounting for 45%–70% of the energy required for the entire production process. Plants typically run six days a week, around the clock. Painted car bodies have to be dried and subsequently cooled. To guarantee the highest standard of quality, high volumes of supply air, exhaust air and recirculating air have to be transported in the spray booths. It is not uncommon for over 100 motors or more to be in operation, consuming up to 4 megawatts (MW) for operation of the fans alone. “Added to this are drive systems for conveyors and robots. The electrical power needed to operate a paint shop can quickly add up to between 8 and 10 MW ”, explains Ulrich Schrickel, Key Account Manager Paint Shop Automation in the Siemens Industry Automation Division.
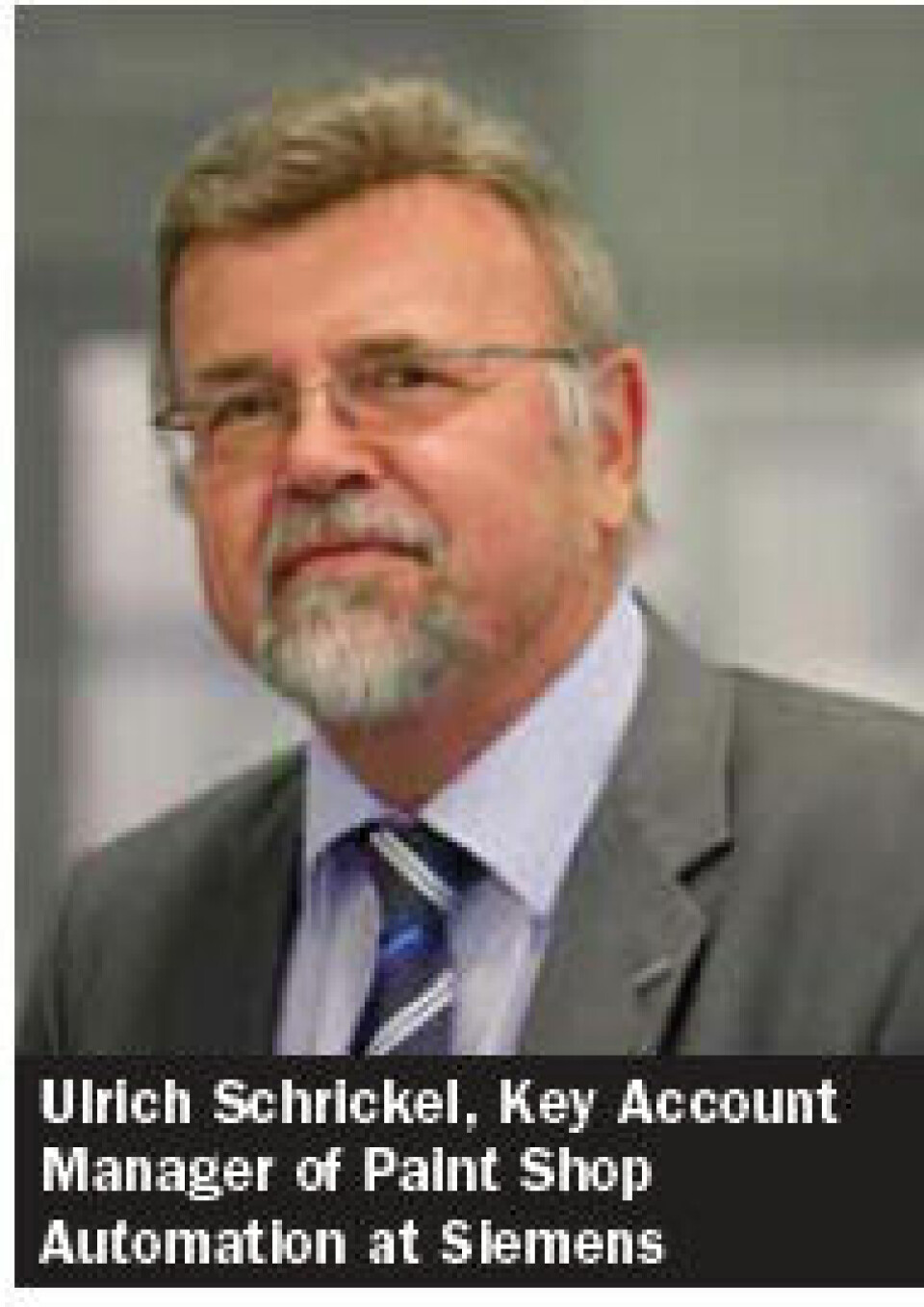
Electrical drives account for two-thirds of the electrical energy expended in a paint shop. Over the lifetime of an electric motor, 90% of its total cost is power consumption. Even if they are somewhat more expensive than conventional components at the investment phase, more efficient motors offer a fast payback. Even changing over from motors in the lowest EFF2 or IE1 efficiency category to high-efficiency EFF1 or IE2 motors can mean an efficiency gain of up to ten percentage points, depending on output. High-efficiency IEC motors are a key element of the environmental portfolio offered by Siemens, which already supplies its motors in the high-efficiency (IE2) and premium efficiency (IE3) categories right across the supply range from 750 Watts to 375 kW. The use of energy-efficient motors can also help drive down energy consumption by up to 40%. The savings gained by exchanging 100 motors in a paint shop can quickly mount up over the year to a significant five-figure euro sum. The additional cost involved in the purchase of energyefficient motors rather than less efficient models is recouped within one to two years. The work involved in exchanging Siemens components is minimal, as the motors offered in the various efficiency categories are designed to the same dimensions. This means that no adjustments to the machine design are required when upgrading to a more efficient alternative.
Savings potential lies dormant everywhere
The demand-driven operation of electric drives in conjunction with speed-controlled Sinamics frequency converters offers further scope for saving. Particularly in continuous flow machines such as pumps, fans and compressors, the energy consumption of motors rises by the power of three with increasing speed; doubling the speed results in eight times the consumption. Generally speaking, motors run at full speed, while the delivered quantity of the required medium is reduced using a throttle. A far more efficient approach is to use variable speed drives controlled by frequency converters. By applying a suitable increase in power, the airflow of a fan can be kept constant, for instance, even as the filter gradually becomes clogged with dirt particles. The frequency converters adjust the speed of the motor to meet the changing need, resulting in energy savings of up to 70%. “This opens up additional scope for savings in other systems, such as the pumps used to transport the paint and for the dip tanks”, says Schrickel. There are many ways to achieve energy recovery in automotive paint shops, one of which is the use of intelligent conveyor technology. The car bodies are transported on a variety of skids through the painting process, during which they are continuously moved and rotated. As soon as the skid is lowered, energy is released which is literally burnt away in braking resistors. A smart transport system ensures that the car bodies are transported with the most efficient use of energy. A key module of the system: the new generation of Sinamics frequency converters from Siemens with energy recovery. These absorb the braking energy generated by the skids and feed it into the grid. This type of relatively easily implemented solution can be used to achieve additional savings even in state-of-the-art paint shops, by deploying this same technology in hoists and lifting devices. Another example in which efficiency is enhanced by targeted innovation is the introduction of individual anode control (IAC) in the field of dip painting. By using small and efficient converters, energy is saved by optimizing the paint thickness though individual anode control. The patented system is able to reduce the energy requirement from the grid by 25 to 30%.
Putting machines to sleep
Machines go on consuming energy not only during production but also through break periods. Short break periods and even weekends together account for an amazing 60% of total consumption, because generally machines remain switched on. The smart energy management profile PROFIenergy offers a solution here by reducing idle consumption to around 20% of normal operation. The standardised energy efficiency profile was developed in close cooperation with the Automation Initiative of German Domestic Automobile Manufacturers (AIDA), and permits the coordinated and central deactivation of individual loads or whole areas of a production plant such as painting robots or conveyor systems. Load peaks can also be absorbed by switching off loads that are not required, or by switching to the sleep mode. Siemens has already developed a series of products such as controls or motor starters which support the PROFIenergy profile.
From cost factor to success factor
Other areas in which manufacturers can make savings can be determined by performing a detailed analysis and visualisation of energy flows. Schrickel explains: “After all, if you are looking to save energy you need to know exactly how much energy is being used and where. The only way to do this effectively is with an integral energy management process which is able to identify, evaluate and exploit savings potential.” Siemens offers a comprehensive energy optimisation package for paint shops. Using smart software applications for energy management such as B.Data, the industry supplier supports manufacturers in their bid to optimise production processes. Components such as compact, high-performance Sentron PAC multifunctional power monitoring devices, which keep continuous and reliable track of all consumption data and forward it to the higher-level control system, allow users to gain a detailed picture of their power consumption and take targeted action to optimize it. The B.Data software is precisely tailored to ensure implementation of the latest energy management systems standard, ISO 50001. The software tracks the progress of all energy and material flows, such as water, power, pressure or steam, both in production and in all ancillary processes. Individual consumption rates can be traced to the relevant originator and documented. Based on specific key performance indicators (KPIs), B.Data supplies a solid foundation for decisions on the best way of optimizing energy and energy savings of 5%-10% can be achieved without any further investment.
Paint shop automation – a question of integration
Siemens has for many years applied a concept that ensures the consistency and compatibility of every component: Totally Integrated Automation (TIA). This integral approach not only offers scope for more response flexibility and optimized capacity utilization, but also creates a basis for ensuring optimum painting quality. In practice, this means ensuring the efficient coordination of systems such as visualization, identification, wireless communication and safety. Measures put in place by Siemens include mobile HMI devices capable of replacing a whole array of stationary display units. RFID systems from the Simatic Ident portfolio ensure seamless identification. The tags used are easily able to cope with the extreme high temperatures occurring inside the paint shop and allow the no-contact identification of every car body. Scalance components can be used to create wireless networks in production that reliably control the transport of skids through the paint shop, including all rotary movements, by industrial WLAN. And Simatic Safety Integrated provides solutions designed to safeguard every aspect of the process, without the need for additional wiring.
But it is not just in production that Siemens may claim an almost unique position as a global partner to the automotive industry. Schrickel sums up Siemens’ unique position: “We are the only supplier capable of providing this kind of comprehensive portfolio for improved energy efficiency in car manufacturing around the globe.”