Tomorrow's automotive world
What will vehicle manufacturing look like in a few decades' time, and how will production be controlled?
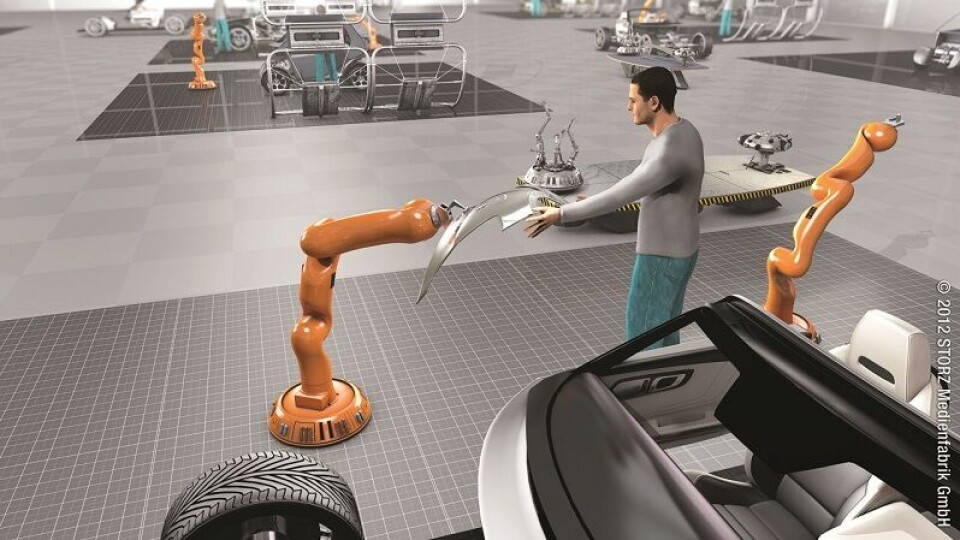
An initiative called ARENA2036, which is being carried out by the Fraunhofer IPA in Stuttgart, Germany, aims to explore and shape three areas in the design and manufacture of automobiles as they develop over the next couple of decades. One of them will concern lightweight vehicle construction but the other two will focus less on the physical nature of future vehicles and more on how digital information will be used in their design and manufacture – respectively addressing digital prototyping and, by means of a 'research factory', the production methodologies that can most effectively exploit developing data and communications technologies.
On that last count, the project will aim to move beyond the confines of both existing production methodologies – defined by their reliance on strictly sequential procedures involving a fixed chain of production – and existing approaches for analysing them, which focus too narrowly on single pieces of equipment. Instead, it will aim to establish a new manufacturing paradigm that will enable flexible routing of car assemblies between different stations on a production line.
Implementing Industry 4.0 That brief outline presented above comes from one of the researchers involved, team leader Thomas Dietz. But, as he explains, doing so will involve the practical implementation of the concept of Industry 4.0 – a term that has come into use over the past few years to indicate an approach to manufacturing in which communications technologies, whether across a shopfloor at a local level or the Internet at a wider – even global scale – are used to maximise manufacturing efficiencies.
“It is about exploiting the capabilities of networking in production,” says Dietz. The key break the concept makes with previous practice, he states, is that “in the past, the interfaces and relationships between different parts of the production system have been explicitly engineered". The devices have been “hardwired” so that “how one device communicates with another is specified exactly".
The ARENA 20326 initiative by the Fraunhofer IPA, the largest applied research organisation in Europe, has actually been underway now for over two years, and by the spring of 2017 it is intended that it should be operating in a purpose-built 7,000 sq.m facility co-located with the University of Stuttgart, Germany; construction costs alone are expected to be in the region of €30m ($33m).
The initiative is targeted specifically at the automotive industry, although only one vehicle-maker is currently formally involved: Daimler. However, other companies participating in the project include Bosch, Kuka and BASF.
According to Dietz, a fundamental principle of the Industry 4.0 approach involves the replacement of manufacturing processes “that have been implemented in hardware with new ones implemented in software". This means constructing manufacturing installations that can be easily reprogrammed to make new products, rather than being “rigidly dedicated” to a fixed product range. He gives one simple example that is already beginning to appear in industry: the replacement of dedicated parts-feeding hardware with robots equipped with vision systems that can be reprogrammed for the bin-picking of specific items from a collection of varied parts.
Right now, the research into future manufacturing at Stuttgart comprises several smaller-scale projects, including investigations into 'agile' door assembly and mating with the car body and robotic 'pre-consignment' of sets of relatively simple parts such as nuts and bolts. The latter, Dietz explains, involves using a robot to retrieve parts from storage according to immediate assembly requirements, like “shopping in a supermarket” – the justification being that, as product variability inevitably increases, lineside storage of all the types of parts that might be needed, even over a single shift, becomes more impractical.
Automating integration capabilityAnother project that Dietz describes with a similar everyday analogy involves pioneering a 'yellow pages' approach to automation. He says this means enabling individual pieces of equipment to register themselves automatically on a network and signal their availability and capability to the other pieces of kit involved. In effect, equipment will have an autonomous integration capability “even if the control infrastructure is heterogeneous". Such a scenario, he says, is “pure Industry 4.0”.
This is not technology for its own sake. The underlying business objective, Dietz explains, is to facilitate the reconfiguration and re-use of equipment so that levels of automation can be ramped up and down according to demand, and also that capital investment can be amortised if necessary over different model ranges. Interestingly, he adds that the work at Stuttgart has already resulted in the production of an app that uses a questionnaire approach to quantify the 'agility' of existing equipment – in other words, its ease of reconfiguration.
Dietz explains that agility in this context involves two sets of metrics. One denotes the ability of a production system “to react to external scenarios". This could involve, most obviously, the need to respond to a sudden change in demand, though more fundamentally it might mean having to relocate a complete facility because the market for the products it makes undergoes a geographical shift. The other, though, relates to the actual production equipment involved – how mobile it may be, for example.
In turn, that strategic objective is being driven by the prospect of a major shift in the degree of variability that automotive production lines will have to provide. Indeed, the industry is faced with the prospect of a “new dimension of variability”.
Preparing for product variabilityDietz says that the current emphasis on product variability according to customer choice will increasingly be supplemented by two other, rather more fundamental trends. These are: the increasing use of new materials such as carbon fibre in car construction and the greater uptake of new drivetrain systems – electric, hybrid, even hydrogen – alongside petrol and diesel engines.
What that will mean is increasing uncertainty about even the basic type of vehicle that carmakers will have to produce. A further complication is that different types of drivetrain make quite distinct demands for their own assembly and test procedures. The requirement for a pressurised fuel storage tank in a hydrogen-powered vehicle, for instance, has no analogue in the world of petrol or diesel vehicles. Hence the need for production lines with an inherent capability for reconfiguration according to demand.
However, as Dietz observes, it is not the high degree of technology and material variability in the cars themselves that will be the key factor – it is simply that over the next decade carmarkers cannot be sure how demand for different types of vehicle will shift. “It is the volatility of the market,” he confirms. If a car company were to start development of a new car model now, he observes, it really would be very difficult to predict with any certainty what the relative demands would be for such model variants, say, six years ahead.
In consequence, manufacturing equipment currently on the market needs considerable further development if it is to be capable of operating in ways appropriate to that environment. Dietz says that it has to have standardised, modular interfaces for both its hardware and software elements, and also needs to become much more “intelligent”. By the latter, though, he does not simply mean that it should have more processing power. Again, Dietz describes what he means using an analogy from everyday production situations.
Creating cyber-physical systems Take the example of a robot. Currently, such machines still have to be programmed “at a very low level on a movement-by-movement” basis. What is required, though, is that they should become “cyber-physical systems able to offer services in production". In practical terms, Dietz explains, that means they should have an integral capability to work out how to perform a designated task and to program the appropriate actions into themselves. As Dietz points out, if a human is asked to perform a particular task on a shopfloor they do not need to have every movement of their hands and arms stipulated – nor, in the future, should a robot. He adds that work to make such capabilities a reality is already a major preoccupation of robotics research.
"What if functionality could be taken out of the robot system and instead centralised on a cloud server?" – Thomas Dietz, Fraunhofer
Dietz adds that the ARENA2036 initiative is picking up on development work carried out by Fraunhofer on cloud robotics, which he says is very much focused on developing robotics systems appropriate for an Industry 4.0 environment. He explains that such installations today typically have a significant local hardware overhead in the work cell. For instance, even in a relatively simple application such as bin-picking this is likely to include a sensor system, an imaging system and the basic robot controller that will in itself be the equivalent of a high-end PC.
However, says Dietz, that type of set-up has “significant disadvantages” – not least the initial capital outlay and ongoing maintenance costs with an associated need for appropriately qualified staff. What, he asks, if all that functionality “could be taken out of the robot system and instead centralised on a cloud server?” The answer, Dietz seems confident, is that that the aforementioned drawbacks could be significantly curtailed.
Though the concept of Industry 4.0 can sound unspecific – it is not, for instance, based on published technical standards – it is nevertheless about the application of real technologies in actual manufacturing environments. As such, like any other set of shopfloor procedures it poses demands for appropriate training.
Helping to tackle those demands is the aim of a new mechatronics training rig from Bosch Rexroth that is described by UK technical training manager Dave Stirling as specifically aimed at satisfying Industry 4.0 requirements. The rig is billed as a “three-station, floor-mounted production system” which, in effect, allows the user to simulate three distinct processes common to any manufacturing shopfloor: part selection, the manufacturing process and return to storage.
Using it involves processing two blocks of material – one metal, one plastic – which are manipulated with the aid of an integral conveyor belt, a two-axis robot and a hydraulic or pneumatic press. An analogous process on an automotive production line, Stirling suggests, might be the insertion of the valve guides into a cylinder head. But the relevance to Industry 4.0 of the rig does not lie in the procedures it simulates. Instead, Stirling states, it derives from the system's use of the latest industry-standard electronics – for instance its range of sensors, including both optical and radio frequency identification devices – and their effective networking.
Moreover, though the off-the-shelf system makes extensive use of Bosch Rexroth's own technology, this is counter-balanced by two other factors. One is that the hardware is not completely Bosch Rexroth's own – the safety system, for instance, is from German supplier Sick. The other is that the whole system complies with what Stirling describes as its "open core" approach, which facilitates the integration of Bosch Rexroth's own programmable logic controllers (PLCs) with wider IT architectures from other suppliers.
Crucially, he says, the integration allows the PLCs to be programmed via a 'front end' which may come from another supplier and hence use a different programming language that creates its own distinctive look and feel. The training can thus mimic the interfaces which operators will use in real production environments.
Audi uses virtual reality technology for the 'virtual prototyping' of new vehicle manufacturing processes. The company has been using the IC.IDO system from ESI at its plants in Ingolstadt and Neckarsulm, Germany, since 2009, in what it calls a 'cave automatic virtual environment' (CAVE).Audi reports that it uses the system to carry out investigations in its 'pre-series centre' into the feasibility of producing future vehicles. Projected assembly procedures are simulated by virtually handling components in the 3D environment of the CAVE. The company states that the software’s collision recognition capability in combination with the haptic feedback from the controller allows it to test the feasibility of the assembly procedures involved and their associated process safety before the first prototypes are built.
The information the system generates is used primarily to carry out investigations of models that are to be produced at a specific plant, but where data is relevant for several plants it is disseminated accordingly. Either way Audi says that the objective is to plan the assembly process in advance so that assembly employees can implement it intuitively and without any additional information.
Audi confirms that the use of virtual methods enables conceptual problems to be identified and resolved at an early stage in the development process. Besides shortening development times this allows it to be certain what tools will be required, avoiding the costs of any subsequent tool modifications. Moreover the number of physical pre-series vehicles required for ensuring optimal assembly can also be reduced.
For the future Audi says it aims to use virtual methods to simulate the assembly of flexible components with the first intended application involving cable sets and hoses for cooling systems. In the longer term it also wants to represent the behaviour of door trim and seals during assembly on the basis of their respective properties.
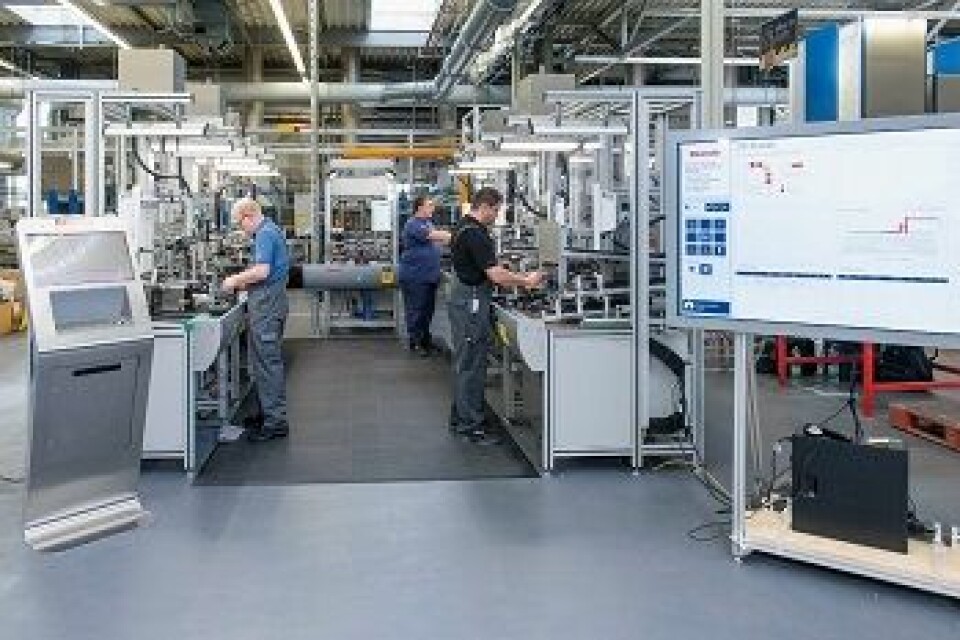
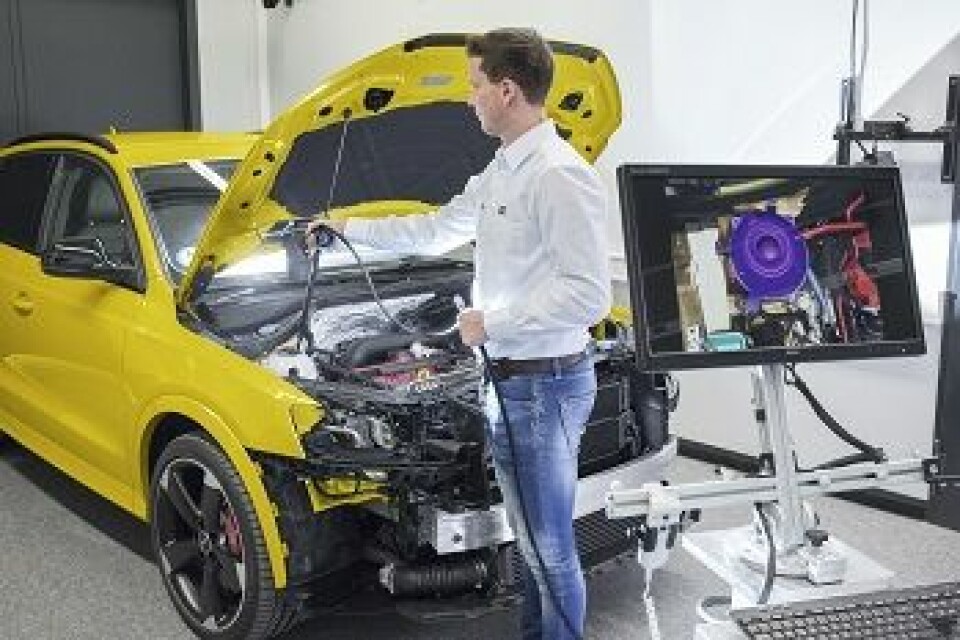