Production systems return competitive edge
Flexible production now lies at the heart of global automotive manufacturing. Using reprogrammable tooling in bodyshops, standardized equipment in paintshops and common build sequences in assembly, carmakers are seeking to integrate processes that allow production of multiple models in a single plant and on a single line.
In North America, more than most regions, it’s the difficult economic climate that has forced plants to consolidate, extracting maximum value from every manufacturing investment. To push costs even lower, carmakers have been further exploiting lean and flexible methods in combination with cross-plant standardisation. The economic crisis, though, has forced the collective hand of the automotive industry, requiring change to take place at greater speed, with the changes sometimes impacting entire companies. “Flexibility has led to efficiency and consolidation of plants and build process functions,” says Dr. Jay Baron, President and Director, Manufacturing Systems Group at the Center for Automotive Research (CAR), located in Ann Arbor, Michigan. “Ideally, flexible plants will operate at higher levels of capacity (near 100%) than less flexible plants.” The message is clear: Plants without the required flexibility needed to implement rapid model production changes will never reach 100% capacity.
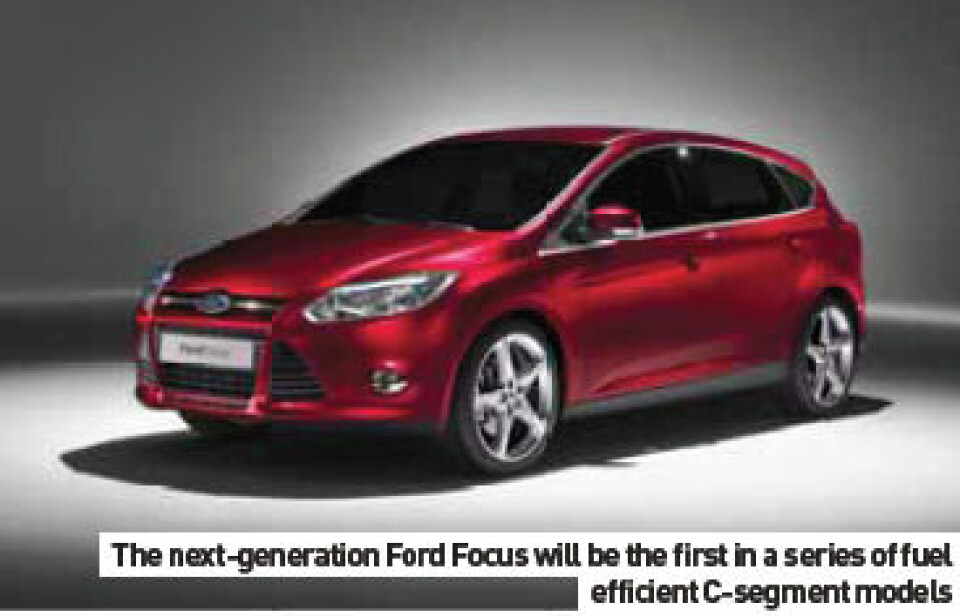
Virtual assembly
While automotive design departments have long benefited from using virtual tools, the systems are now used to develop universal best practices and improve production line ergonomics in order to assure workers can deliver consistently high quality products. Beyond design, virtual tools - computer design and software programs – are now used across all elements of product development. New vehicles are signed off by remote production engineers and the layout and implementation of line technology is optimised employing the same technology suite previously dedicated to vehicle design.
A further benefit is the falling cost of robotics. “For the Detroit Three (Ford, GM, Chrysler), robotic automation has become very low cost. Robots carry greater payload, are more repeatable and require less maintenance. Now they cost less than 50% of what they did 20 years ago,” says Baron.
Pushed by macro economic trends, federal and state funding, and the shifting tastes of the US consumer to smaller, more fuel efficient vehicles, carmakers are planning ways to take advantage of model line and plant consolidation. It goes without saying that reducing the number of platforms can drastically simplify integration of new automation at assembly plants. But more than this, standardisation is the darling of flexible operations, with repeatability across models cutting costs and improving finished vehicle quality.

Ford plans for global model
The 2011 Ford Focus is set to take the lead in Ford’s new global manufacturing strategy. In the United States, the model will be built at Michigan Assembly in Wayne, a plant being revitalized as part of Ford’s global manufacturing system.
Yet well before this, the car was a test model for virtual design and flexible manufacturing. Using the latest in remote communication technology, teams of engineers, manufacturing specialists and assembly plant workers gathered in North America, Europe and Asia with the goal of working together to remotely build a virtual next-generation Focus piece by piece, operation by operation, right down to its quality-driven paint finish. This more than a year before the model’s market debut. Simply put, the gathered experts were asked one question at each decision point: Yes or no? It was a major milestone in starting a global manufacturing operation slated to produce up to 10 different C-segment models on one highly-flexible platform. The new Focus is the first global product to come from Ford in a strategy championed by Alan Mulally, company president and CEO.
“It was an exciting moment,” says Bruce Hettle, Executive Director, Global Manufacturing. “We built the car partby- part from start to finish, from the first piece of sheet metal.” According to Hettle, deciding the make up of the team was one of the most important parts of the process. In addition to engineers and executives, members of the vehicle production teams at regional locations were included; the people who would later build the car on the shop floor. Building a virtual representation of the first nextgeneration Focus was an important step in proving the company’s global manufacturing capability. Plants around the world will now build globally-developed cars with processes, tools and technologies signed off by the people most familiar with the equipment. It’s a move that opens up significant opportunities for increased part commonality and cross-model build strategies. Additionally, Ford expects to benefit from improved economies of scale.
Lean machine: GMS propels the new GM
General Motors has invested heavily in its Global Manufacturing System (GMS), the cross-plant and crossregion equipment purchasing and integration strategy. The GM GMS now covers 100% of the company’s global plants and joint-venture partner operations. Like shared DNA, the GMS strategy serves to dictate manufacturing and even corporate culture across all GM facilities. Started in 1996, GMS started its journey into becoming GM's single global operating system under Gary Cowger, a former plant manager who retired from his position as group vice-president for global manufacturing at the end of 2009. Featuring built-in flexibility, GMS is a tool designed to respond to changing markets, but at the individual plant level.
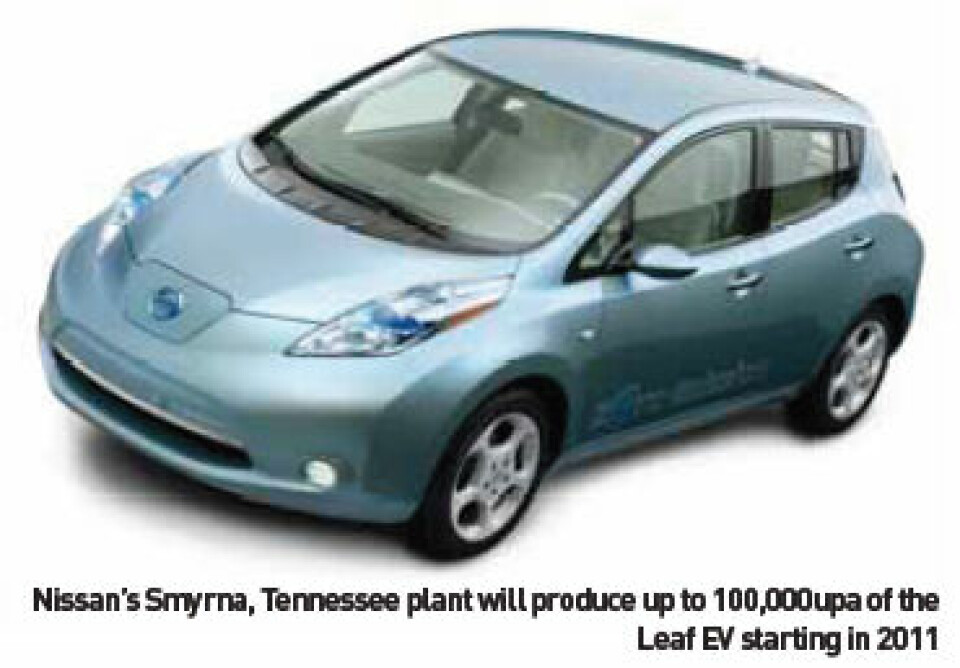
A system of continuous improvement keeps the system relevant; nothing is set in stone. Line operators are the heart of the structure, with each individual having the ability to influence how the system grows and adapts. Based on this input, workers can literally decide the fate of a process by pulling an andon cord - or even by entering an e-chat. “The nature of standardisation is that if we find a better way, we can change it. We keep raising the bar,” says Ken Knight, Executive Director of GMS. Knight was formerly plant manager at GM’s Oshawa Truck Assembly Center in Canada and Lansing Grand River Assembly in Michigan, a company-leading plant in the implementation of advanced technology. “It has transformed the assembly process and permeates the entire fabric of work,” he says about GMS. “It’s a basic way of life here; it is based on continuous improvement.”
Yet the GMS isn’t only an operating guide to leaner, flexible production. Instead, it acts as a blueprint, a competitive tool. It is suggested by GM management that GMS is an underlying reason as to how the carmaker consistently matches the quality gains achieved by its Asian and European competitors.
“You can walk into any GM facility or JV operation around the world and you would be able to read and understand the floor, thanks to GMS,” says Martin Apfel, GM Executive Director for Global Manufacturing Strategy and Planning in Detroit. Apfel moved to the company’s technical centre in 2005, after serving as director of GM Europe’s Opel plant in Bochum, Germany, producing the Opel/Vauxhall Astra and Zafira models.
Another key GMS feature is that within the structure of the system, there are dynamic and fluid elements. For example, as new plants come on stream after renovation or consolidation, feedback is captured and cascaded system wide.

The ability to monitor processes in real time has further enabled GM to run common and lean. “Through continuous improvement, minute-by-minute changes can be made throughout the system,” says Apfel, who continues: “The GMS is a best-practices sharing approach that supports teams globally.” The company also conducts internal process audits to monitor activities against the GMS in order to improve flexibility. “It’s a constant effort of calibrating the system.”
Apfel believes the system ultimately provides a competitive advantage, with operational reports shared throughout the responsible departments. As a result, GM can quickly shift model production within plants, within regions or globally, in response to changes in different markets. Apfel: “GM leverages its global scale by sharing best practices at all plants around the world. If someone in Korea comes up with a great idea it is shared and can be implemented here in the US.”
Other tools include a bill of process (BoP) to cover individual steps across each stage of the build process. A bill of equipment (BoE) is also tailored to different plant environments; within the system, even the level of automation is flexible. Apfel points out that plants in developing regions can convert to more manual operations as needed.
In the US, the standardization of these processes has led to GM being able to quickly spread model production among different plants in response to a fluctuating market. Within the plants, process and activity standardization, from die changes to paint application, has reduced takt times – with the same done across global plants. “Changeover times have been reduced by up to 50% over the last five or six years through GMS and our Global Flex Strategy,” says Apfel.
Flexibility through automation doesn’t always create permanent layoffs. Last autumn, for example, GM recalled 2,400 production workers to three plants, Fairfax Assembly (Kansas), Fort Wayne (Indiana) and Lansing Delta Township (Michigan). While these plants have become more flexible, a third shift (started in January this year) was required to extend operations over 24 hours. GM workers relocating to the Kansas plant were even offered a lucrative bonus to make the switch.
CAR’s Jay Baron observes that a reduced number of plants operating at higher utilization levels is far less costly than many plants operating at less than full capacity. As carmakers fully-exploit flexibility in preference to ramping up inefficient plants, there will be a fundamental shift towards multiple-model, single-line operations.
Ford’s flexible bodyshop
In April 2009, Ford announced plans to invest in retooling its Kentucky Truck Plant (Louisville) in order to produce the Ford Expedition and Lincoln Navigator. Following the changeover, which was completed in just seven weeks, the plant has been a study in efficiency, leading to further product and platform sharing between plants in order to further increase productivity and efficiency.
The plant makeover signalled Ford’s shift to leaner, more flexible manufacturing across its North American operations. Retooling included installing a flexible bodyshop; the plant will also produce the Ford F-Series Super Duty pickups alongside the Expedition and Navigator SUVs.
The changes in Kentucky were implemented through a $200 million, state-sourced incentive package. The new body shop was sourced from a former Ford assembly plant in Norfolk, Virginia, with additional components brought in from Michigan Truck, which has been retooled to produce the next-generation Focus and other smaller models.
Nissan flexes in Tennessee
Nissan has converted its Smyrna, Tennessee complex into a nimble, market-driven plant. The three-shift operation is capable of producing a variety of products; future production will include the Leaf EV. Smyrna Manufacturing is central to the company’s Nissan North America network, where car and truck lines meet. Nissan Maxima and Altima saloons, Altima coupe, Xterra and Pathfinder SUVs are all built at the facility. Daily production breakdown is cars over the first two shifts and trucks on the third.
“Trucks all run down the same line, cars down another. There are 19 different variations for Altima and Maxima models alone, including the hybrid Maxima,” says Randy Knight, Director of Altima/Maxima Trim-Chassis Lean Production at Smyrna. He joined Nissan in 1983 as a production technician in the paintshop.
Knight says that flexible production is at the core of Nissan’s production system. “It eliminates all waste. We wouldn’t be competitive without it. In the last 18 months, vehicle choices have become highly consumer driven. It gets more and more demanding, given market constraints.” Maintaining flexible production at Smyrna involves a high degree of complexity. To keep lines moving efficiently, Smyrna kits vehicle parts before they are shuttled to workstations in AGV carts. Knight points out that there is no wasted motion between kitting and a technician adding parts on the line.
Opened in 1983, the Smyrna plant can produce a maximum 550,000 units per annum, though Nissan estimates that it is currently producing about half that number. Production of the Leaf EV will start in 2011, which will improve capacity utilization, with between 50,000 and 100,000 units being built per year.
In addition to Smyrna, Nissan operates a full engine facility in Decherd, Tennessee, manufacturing V4, V6 and V8 engines, together with engine components and parts for distribution to markets across the globe. Rick Youngblood, Plant Manager and Director of Plant Operations, and David Sliger, Senior Manager of Maintenance, hold up to ten focus groups a year with team members, including shop technicians, to discuss the state of business – it’s an integral part of Nissan’s global production system.
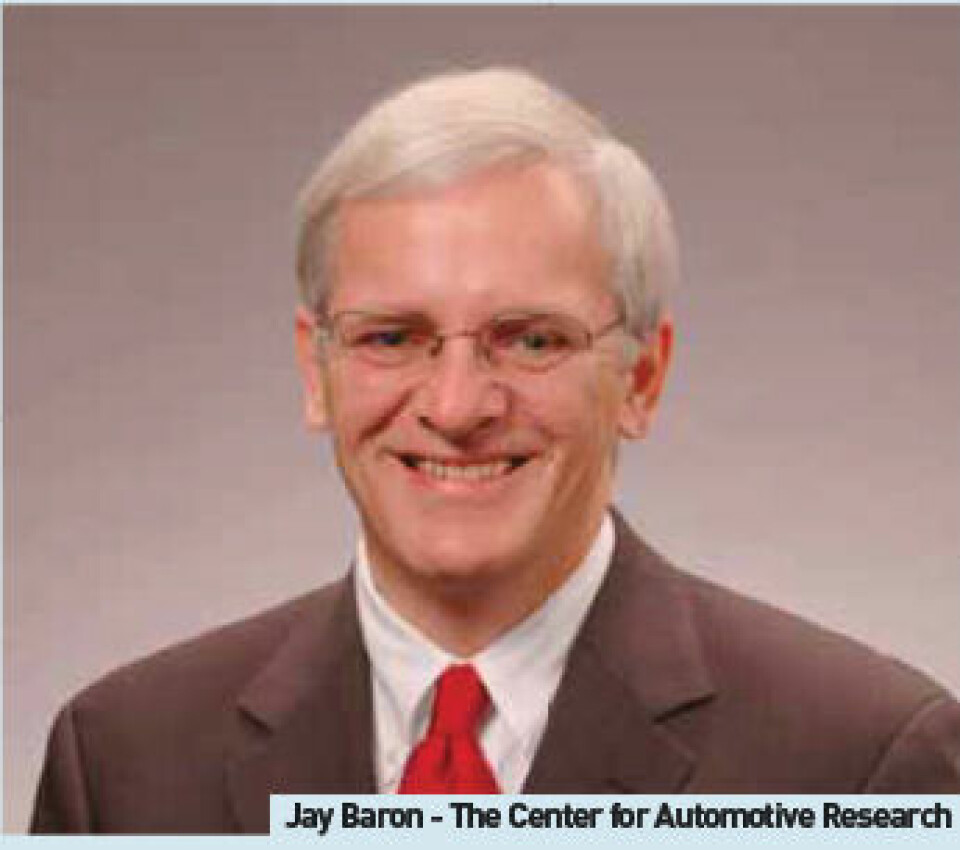
Two-way communication between plant management and line workers is a hallmark of the non-union Nissan plants, the reasoning being that in addition to flexible production you have to have flexible minds. Although the plant is currently underutilized, it is capable of producing 1.1 million engines and components annually for Nissan and Infiniti models, with exports going to Spain and Thailand. Being lean and agile has helped Nissan stay competitive in the US market, says Youngblood. “We shift gears very well and very quickly. We’ve created global databases, e-rooms and videoconferencing to share best practices.” He claims that by using the technology, ideas can be shared between grassroots and cross-functional teams, including line technicians.
It was a suggestion from a technician that led to efficiency improvements included in the new lean maintenance programme called Preventive Maintenance Optimization (PMO), says David Sliger. “That means maintenance employees don’t perform a task unless conditions require it.” “A major premise here is we will challenge everything,” says Youngblood. “Everyone staying in this business has that mentality.” Sliger and Youngblood, like many Nissan managers, credit employees for any success. “There’s no one more important than the person making the car. They’re true stakeholders,” says Youngblood.
Chrysler goes common
Chrysler believes the key to flexibility lies in standardisation. The newly-restructured group, now controlled by Fiat, is using its Flexible Manufacturing System (FMS) as a model for all plant upgrades and designs. The system features standard bills-of-process and a standard bodyshop design that is heavily reliant on modern robotics. In rolling out the FMS, the carmaker claims to have provided the template for future plant modernization, with the Sterling Heights Assembly Plant, Sterling Stamping (both in Michigan), and the Belvidere Assembly Plant (Illinois), having pioneered the strategy.
The common manufacturing systems used across all Chrysler plants support efficienct product design and overall manufacturing. Standardization covers common operational sequences, dimensional strategy and guidelines for machines and tooling. This is of particular importance in the bodyshop, considering the uniform reliance on robotics.
Japanese firms build on past success
Honda, which has long been a model for the US automotive industry, celebrated fifty years of manufacturing in the US in 2009. The company, though, is not resting on its laurels. Known for technical innovation, Honda maintains a practise of continuous innovation to remain ahead of the competition in terms of manufacturing.
Honda’s plant in Marysville, Ohio, was the company’s first North American manufacturing facility, but the last to come into line with Honda's Global Manufacturing System. The system, which started development in 2000, serves to set standard process guidelines at company plants worldwide. The system further serves to provide guidelines for increased flexibility, meaning that plants can build any model in a particular range. This makes it simple to adjust model mix or introduce new models at a given facility. The ultimate goal is to reduce the new product cycle from fortyeight to 30 months, while still cutting investment costs by as much as 50%.
Toyota, widely regarded as the originator of lean production, started slimming down manufacturing processes in favour of flexible production more than 30 years ago, based on the now legendary Toyota Production System. Many automakers have benefitted from studying Toyota’s lean and flexible production principles.
Increasing fl exibility and standardisation means more models can be produced on multiple platforms in the same facility, says Dr. Jay Baron, President and Director, Manufacturing Systems Group at the Center for Automotive Research. “It does add complexity pressure, but much of that is put on the supply chain,” he says, going on to point out that this is balanced by reduced engineering costs through platform fl exibility. The fl exibility that computer-based automation offers no longer comes at a cost premium. “Around 30 years ago you would pay more for a fl exible plant,” says Baron. “Now fl exible plants don’t necessarily cost more than less-fl exible equivalents.” Costs associated with fl exible automation are largely due to the investment needed for associated computer systems controlling manufacturing equipment (robots, material handling systems, inspection equipment, etc.), he explains. Only a few decades ago, running more fl exible plants might cost 50% more than non-fl exible plants. “In order to justify this added cost, you would have to recognize the value of fl exibility. If you had long product runs (between six and 10 years for some models), and high volumes that fi lled an entire plant (more than 250,000 vehicles per year), then you didn’t need to be fl exible.” The Detroit Three rely mostly on off-the-shelf technology. “Robots are cheaper now and commercial robots can be bought with fantastic performance,” says Baron. Robots that cost up to $75,000 can now be purchased for about $25,000, with even greater capability. Effi ciency gains in plants are being seen across all facility operations, from die-change times to improved takt times. Baron points out that some plants can now complete die changes in just a few minutes. Even in the 1990s, such operations could take several hours at less-effi cient stamping plants. “The speed relates to standardization of dies and fl exible lines. The dies, the set up procedures, the presses and the press conditions (maintenance) were all standardized so that the processes could be steadily improved for maximum effi ciency.” Quality has vastly improved as a result. Just 15 years ago, squeaks and rattles associated with NVH would become apparent after just a few years in most domestically-produced cars. “Now, the quality gap is closing and (US) domestic car quality is on a par with world-class quality,” he says. The productivity gap also is also closing, to the point where it is no longer a distinguishing factor between domestic and transplant carmakers. In 2007, the productivity gap, measured in hours-per-vehicle, was within 10% from best to worst vehicles made in the US across all manufacturers, explains Baron.
Toyota operates 13 manufacturing plants in North America, with new plants under construction in Mississippi and Ontario, Canada. The new Venza crossover is built at the Toyota Motors Manufacturing Kentucky (TMMK) complex using flexible and lean manufacturing strategies. Built exclusively for the North American market, all aspects of Venza’s engineering and design were designed to suit local car buyers. The TMMK complex represents a $5.3 billion investment and is considered Toyota’s flagship North American facility.
Flexible plants across the US
The following is a round up of current production activities at some featured plants.
General Motors
Fairfax Assembly in Fairfax, Kansas, builds the Buick LaCrosse and Chevrolet Malibu. The plant also built the Saturn Aura before GM started winding down that division. Fairfax was in the running to build the new Buick Regal, but this model was eventually awarded to GM’s Oshawa, Ontario plant, one of the company’s original flexible production plants. Malibu was transferred from the Orion, Michigan assembly plant, which closed in September 2009. This year, Orion is slated to be refitted in order to produced a range of high-volume small cars, possibly including the Chevrolet Spark or Aveo replacement.
Lansing Delta Township, located in Lansing, Michigan, has added production of the Chevrolet Traverse, formerly built at Spring Hill Assembly, Tennessee. An additional shift is scheduled to start at the Lansing plant in April 2010.
Ford
A third shift was started in April 2009 at Ford’s Louisville Truck Plant across the stamping, body and paint shops. A second trim line was also added. Approximately 450 Ford employees transferred to the plant, primarily from Louisville Assembly and the former Michigan Truck Plant. Total workforce is now about 4,000 employees.
Ford has outlined plans to invest $400 million in its Chicago manufacturing facilities to launch production of the new Ford Explorer SUV at its Chicago Assembly Plant. A second shift will add approximately 1,200 new jobs at the nearby Chicago Stamping Plant.
Nissan
Nissan’s 5.4m sq-ft complex in Smyrna, Tennessee builds the Nissan Maxima and Altima sedans, Altima coupe, Xterra and Frontier trucks and Pathfinder SUV on two flexible lines. Smyrna is a so-called ‘hybrid’ facility, as it is also scheduled to start production of the Nissan Leaf EV in 2011. At full capacity, Smyrna employs approximately 3,900 staff.
Honda
Honda Marysville builds the Accord Sedan and Coupe, Acura TL saloon and Acura RDX crossover. The East Liberty Auto Plant produces the Honda CR-V and Element SUVs and the Accord Crosstour, a new crossover vehicle launched in late 2009.
Toyota
Toyota Motor Manufacturing in Georgetown, Kentucky is Toyota’s largest manufacturing facility in North America, with a capacity of 500,000 vehicles and engines. Products include the Camry, Camry Hybrid, Avalon and Solara saloons, and V6 and four-cylinder engines and engine components. TMMK will produce the new Venza crossover, said to include about 70% domestic content. Anticipated output 70,000 units per year. Associated operations include die manufacturing, production of interior plastics and rubber components. The complex employs about 7,000 workers.