Preparing for take-off
- AvtoVAZ
- Togliatti: Past, present and future
- Manufacturing operations
- The Kalina Robot Garden
- Paintshop
- Ecological protection
- Plastics manufacturing
- The future: Outsourcing and production
- General Motors
- Hyundai and Kia
- Renault-Nissan Alliance
- Ford
- PSA Peugeot Citroën and Mitsubishi Motors
- Sollers: Fiat, Chrysler and SsangYong
- Toyota
- Volkswagen Group
- Conclusion
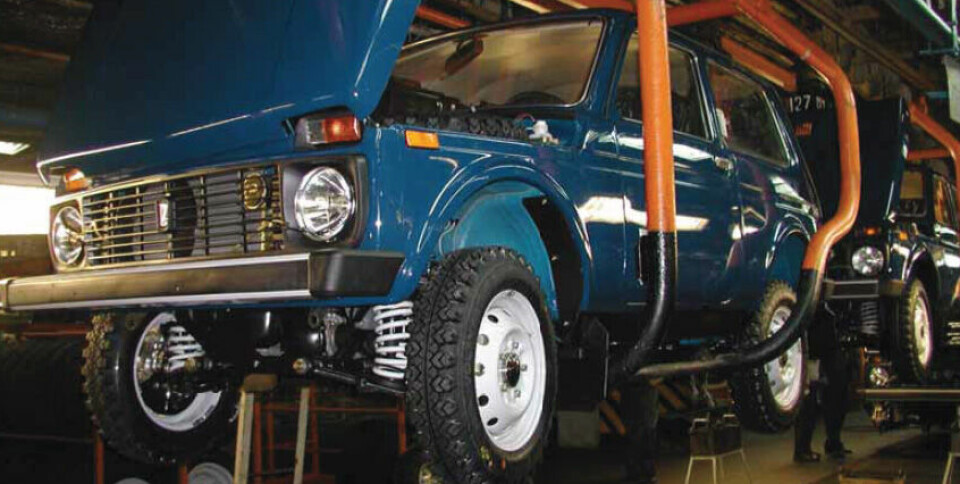
Like the Russian economy, the country’s car industry has been on a white-knuckle ride of late. The canceling of consumer lending eighteen months ago immediately led to one of the steepest declines experienced by any of the world’s car markets. Yet those who thought Russia would remain in the doldrums have been proved wrong. The combination of an easing credit market and a generous vehicle scrappage incentive scheme has pushed the automotive market up by 55% over the first three quarters of 2010.
With the return of new car buyers to the market, the scramble is on to service the increased demand, although high import taxes mean foreign manufacturers will struggle to deliver cars unless they have CKD or SKD operations in-country. This means those with Russian assembly plants look set to reap the benefit of their investment. A growing number of Chinese carmakers are also hoping to cash in on the next growth phase of this traditionally volatile market. However, even with a variety of cheap models on offer, consumers still appear to prefer the better-known Western or home-grown brands. Chery, the best performer of Chinese carmakers, sold only 7,217 cars between January and September, sufficient for only 25th position across all brands. Geely, one of the few Chinese manufacturers to experiment with local assembly (via a contract with TagAZ) as a way to circumvent Russia’s 25% import tax, has so far not had much to celebrate. With fewer than 1,300 cars sold this year through September, the carmaker has been outsold by its Volvo subsidiary by a factor of five.
Beyond the size of the market, what has tempted the Chinese companies to try their luck with older, lower-cost models in Russia is the country’s more relaxed approach to exhaust emissions and crash-test regulations when compared to the European Union.
If Russian consumers are uneasy about taking a chance on an unfamiliar foreign brand, no matter now cheap the car in question, that is certainly not the case when it comes to Russian brands. GAZ Group has temporarily scaled back car production in order to concentrate on its LCV and truck divisions – with great success. Further, with its extensive dealer network and strong branding, Uz-Daewoo, an Uzbekistan-based group, is also riding the crest of a sales wave, with more cars sold so far this year than either Nissan or Volkswagen. Yet for all this, there is no getting away from one fact: in 2010, the most improved and successful company in the Russian car market is the state-owned monolith, AvtoVAZ, maker of the well-known Lada range of vehicles.
Lada Priora family (since 2007)
Lada Kalina family (since 2004)
Lada Samara family (since 1984, restyling: 1998-2004, modernization: 2006)
Lada 4X4 (formerly ‘Niva’) family (since 1977, restyling: 1993, modernization: 2009-2010)
Lada 2105/2107 family (since 1979/1982 respectively, modernization: 2006-2008).
Even after extensive redundancies, the plant still employs 71,300 workers, with the company quoting an average age of 40 years; under-30s comprise almost one third of the facility’s total employees. Add to that service personnel, sales staff and the supplier network, and AvtoVAZ claims that more than two million people depend on the company for their income.
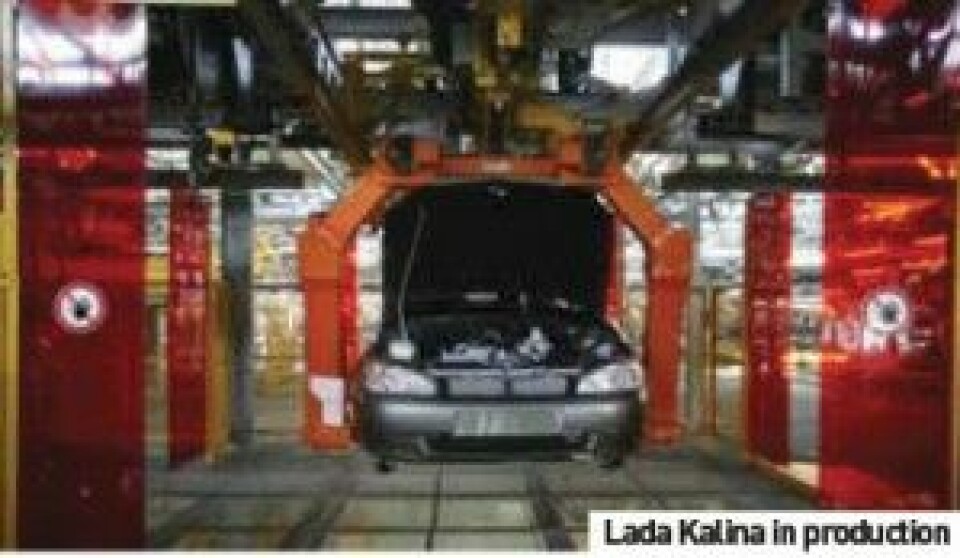
AvtoVAZ
AvtoVAZ, in which Renault has a 25% stake, recently announced that it is planning to produce just under 700,000 vehicles in 2010 versus the previous forecast of 465,000. This followed a statement by prime minister Vladimir Putin to the effect that the government would extend its car scrappage scheme for buyers of Russian-assembled cars into 2011 with an additional RUB14 billion ($453m). Further, AvtoVAZ reported a first-half net profit of RUB3.1bn ($100m), compared to its net loss of RUB19.6bn in the first half of 2009. The company says it has also benefited from the interest-free loans provided by its biggest shareholder, the state-owned Russian Technologies.
Russian Technologies agreed to subscribe a €730m issue of new shares for AvtoVAZ in July 2010, which raised its stake in the company to 36.5%. Renault, declining to participate in the share offering, instead agreed to supply its partner with technology and expertise valued at €240m. Commenting on the company’s thoughts concerning AvtoVAZ, Patrick Pélata, Renault’s COO, recently told the UK’s Financial Times: “They are doing much, much better, very fast”.
At the heart of what was once a giant automotive manufacturing group is the enormous - but these days vastly slimmed down - Togliatti plant. With technology from the Renault-Nissan Alliance and, inevitably, more cash injections from Russian Technologies, the Lada brand could soon be looking at a far brighter future than might have been the case twelve months ago. Key to that plan is a huge rise in productivity and the sheer quantity of vehicles to be churned out at Togliatti.
Togliatti: Past, present and future
Since it opened in the 1960s, originally with expertise and technology supplied by Fiat, the Togliatti works has built over 25 million vehicles.
AvtoVAZ Togliatti
• 16 buildings (four major and 12 additional facilities)
• total area of 416,812m2
• production area of 209,510m2
Major (vehicle) production:
• cast iron – manufacturing capacity is 112,960 tons per year: 104 cast items from grey, high-duty and special irons, including cylinder blocks, crankshafts, camshafts, housing castings and valve seats
• aluminium – manufacturing capacity is 38,340 tons per year: 141 cast items, including cylinder heads, pistons, housing castings
• forging – manufacturing capacity is 103,500 tons per year:
240 items comprising forging dies, forgings and end products, including conrods, gears, steering knuckles, semi-axles and suspension springs
• metal powder – manufacturing capacity is 1,115 tons per year: 84 items, from 0.9 to 4.5kg
AvtoVAZ boasts that tax assignments from the Lada works make up more than 40% of the budget of the city of Togliatti, as well as 20% of the Samara region’s income and, incredibly, 1% of the Russian Federal budget. The vast Togliatti complex extends over more than 600 hectares; total combined length of the assembly lines is 300km. The main line, which itself is 1.5km long, receives components from 270 vendor companies. Currently, 15 different Lada models or variants are produced on the plant’s five assembly lines.
Manufacturing operations
The first die, an inner door panel for a VAZ 2101, was manufactured in February 1970. Now, stamping operations at Togliatti produce close to one million vehicle kits for delivery to the Lada assembly line, off-site assembly plants, AvtoVAZ subsidiaries and the spare parts aftermarket. Approximately 5,000 people are engaged in stamping, processing more than 1,500 tons of rolled metal every day to produce 3,000 items. About 6,000 people represent about 157 professions and specializations involved in metallurgical production for AvtoVAZ, or as the company puts it, many ‘family dynasties of metallurgists’.
SA Komatsu-supplied high-speed automatic stamping line installed at Togliatti in late 2009, becoming fully-operational in mid-2010. According to AvtoVAZ, this includes loading devices with installations for washing and greasing of work pieces. The stamping force is 2,000 tons with prototype pad and there are four single-action presses with forces of 1,000 tons. The line design and structure allows stamping of two parts simultaneously (e.g., right and left wings), providing benefits for logistics processes, storage and transportation.
2011-2012
R90 with Renault engine, Samara saloon production ends, Priora facelift
2013 Low-cost sedan (Renault Logan-based), F90 light commercial
2014-2015 BM-Hatch (Renault engines), 4WD replacement, C-SUV
2016-2017 C-saloon, Priora replacement, B-Crossover
The Kalina Robot Garden
Facility workers gave the Lada Kalina bodyshop its nickname based on a literal translation from the German ‘Robotgarten’. Some 350 Kuka robots are concentrated in this workshop, with transport manipulators supplying parts for welding to the programmed point of space and time, guaranteeing a precise coupling. To ensure finished body geometry, bodies are selected at end of each shift for testing with CMM (control measuring machine) equipment.
Paintshop
The paintshop is equipped by Eisenmann, while chemical management is handled through a partnership with Slovenian company PPG Helios. For the Kalina small car series, the painting procedure starts with the carbody being attached to an immersible skid, together with its opening elements – doors, bonnet, boot lid – while a fixing band is installed. The body is then cleaned before being moving to a preliminary degreasing booth where it is treated with pressure-fed alkaline solutions.
After drying, the body undergoes surface preparation before primer application. This takes places via a series of 26 shuttles. Thus, the processes of degreasing, bonderization, passivation and rinsing in the preparation area are performed over several stages. As corrosion resistance is particularly important for cars on Russia’s heavily-gritted roads, a dense microcrystalline film structure is also applied to Lada car bodies.
After pretreatment, the body is then dipped into an E-coat solution. The process employs 13 vario-shuttles. AvtoVAZ states that the two-component primer considerably improves the resistance of the body coating to corrosion and mechanical damage. After the E-coat is dry, an underbody sealant is applied, followed by welding seam sealing and the laying of noise-reduction matting. Flanges and welded joints are fully protected by polyvinylchloride polymer sealant, while the underbody noise-reduction is a plastisol sealant. After the underbody sealants have dried, a second primer application takes place. Depending on final vehicle colour, light or dark primer is applied.
Following drying and dry grinding of the second primer, the body moves to the spray booths, in which a base coat and protective lacquer are applied by 26 robots on two automatic lines. Further anti-corrosion treatment then follows (salt tolerance of 1,000 hours is the Lada standard), after which the painted body travels to the assembly line.
Ecological protection
The Kalina paint complex features afterburners said to prevent harmful fumes, paint residue and solvents from escaping into the atmosphere, while hydro filters treat all waste water in the basement at a depth of up to six metres. The use of lead, tin and strontium chromate have now been phased out.
Plastics manufacturing
The plastic articles production (PPI) unit, established in 1995, employs more than 1,100 people but where relevant, uese specialist robotic equipment supplied by Eisenmann. The majority of workers are engaged in pressure casting, blow moulding, hot shaping or painting of plastic parts. PPI manufactures parts including front and rear bumpers, instrument panels and door linings. The PPI quality management system is certified to ISO 9001 2000.
The future: Outsourcing and production
AvtoVAZ says it intends to retain development of nine of a planned 30 modules for its future vehicle manufacturing operations, with the remainder gradually outsourced to Tier 1 companies. The modules that will continue to be produced in-house are: engines and exhausts, gearboxes, front and rear axles, suspension, bumpers and mouldings, integrated steering and communications systems, instrument panels, bodyworks, underbody and superstructure. A major programme of restructuring and production modernization is also currently underway at Togliatti. Heavily influenced by AvtoVAZ’s partnership with Renault (with input from Nissan), one of the main goals is to lift production from the current theoretical 922,000 cars and SUVs per annum to a planned 1.23m by 2020. While the majority of these will be Ladas, that total will also include the assembly of Renault and Nissan vehicles. In all, nine models are planned, each of which will be on what AvtoVAZ terms a ‘unified’ platform.
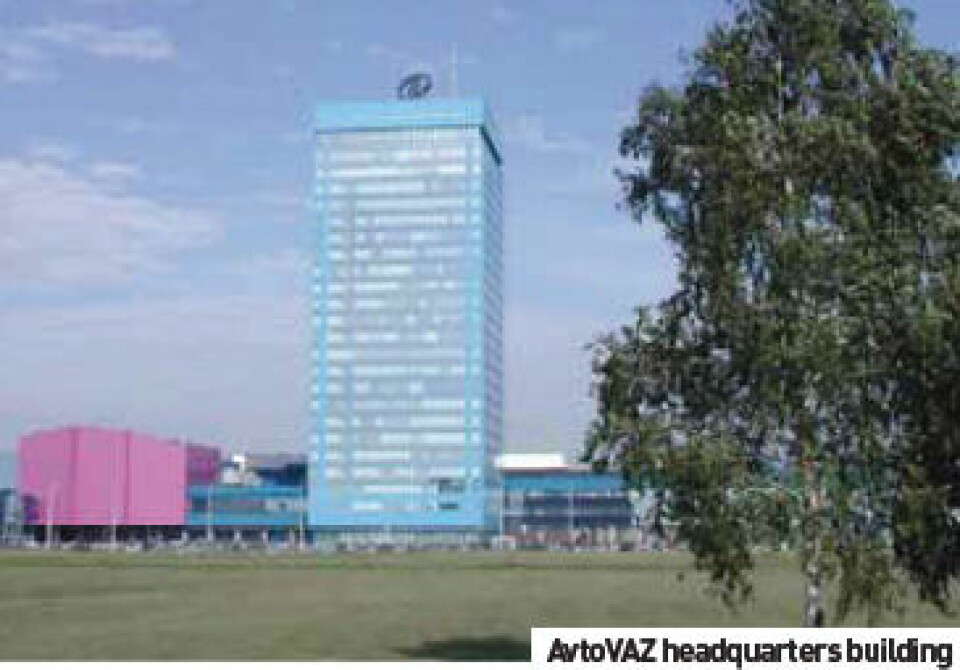
General Motors
As was the case in 2009, Chevrolet remains Russia’s most popular foreign brand. Much of the success of General Motors’ local operations comes from the AvtoVAZbuilt Chevy Niva 4WD, backed up by the Cruze saloon, manufactured at GM’s own Shushary plant, outside St. Petersburg. The cheaper, Daewoo-based Chevrolet Lacetti also factors into the equation, but is an import from Uzbekistan. The Opel brand also enjoys some success, with over 25,000 vehicles sold this year through September, versus close to 80,000 Chevy cars and SUVs.
Looking ahead, GM is reported to be considering the expansion of its Shushary plant, near St Petersburg. The most likely new product would be the next-generation Aveo, unveiled recently in near-production form at the Paris Motor Show. The contract assembler AvtoTOR, which produces vehicles from kits for GM and several other OEMs, should also begin assembly of the next-generation Chevrolet Epica saloon at its facility in the enclave of Kaliningrad from 2012. One year later, GM should start making the Chevrolet Captiva SUV replacement at Shushary.
Hyundai and Kia
If Kia Motors’ Russian operations continue to grow at the current rate, Chevrolet may soon lose its place as top foreign brand in the market. Kia’s rise throughout 2010 has been spectacular, with sales up 63% in the first nine months. Company sales through September stood at almost 78,000 cars and SUVs, versus almost 81,000 for GM brands. Most of Kia’s success can be attributed to three models, the Rio, Cee’d and Sportage.
With such strong sales, it is little wonder that Kia is reportedly looking to expand its ties with troubled local partner IzhAvto. The Russian carmaker’s assembly plant in the city of Izhevsk has a capacity of 220,000upa, but it currently stands idle while the company restructures some RUB14.5 billion ($498m) of debt with the Russian state lender Sberbank. The partners are optimistic that a deal can be reached, with a tentative plan to build 60,000 Kia cars and 15,000 Hyundai LCVs reportedly agreed in principle. Hyundai will not have to wait for an agreement to be reached with IzhAvto, however, as its own local plant - Hyundai Motor Manufacturing Russia - is set to come on stream in January. The $400m complex, which the Korean group claims is the first full manufacturing facility to be set up by a foreign maker in Russia, is a truly ambitious project. Hyundai has chosen the new Solais saloon as the first product for the St Petersburg plant, insisting that in-built quality systems will ensure a problem-free launch and rampup. Based on the recently-launched Accent, the Solaris has been modified for local conditions with features such as reinforced suspension and a 60ah battery. Hyundai intends to build 85,000 units of the Solaris in 2011.
Renault-Nissan Alliance
The Alliance has an extremely aggressive strategy for Russia, stating that, including Lada sales, it is looking to capture 40% of the market by 2015. While Lada is currently the sales leader, Renault ranks only fourth behind Chevrolet and Kia, with Hyundai, Ford, Toyota and Daewoo all ahead of Nissan. Nevertheless, with three production sites in Russia, the partnership will have an overall production capability of 1.3m cars in 2012; the Moscow Renault plant (capacity 160,000 cars per year), the Nissan plant in St Petersburg (50,000) and the AvtoVAZ production facility in Togliatti (1.1 million). Renault and AvtoVAZ are now implementing the Alliance production system at Togliatti, together with a joint production line for the production of cars based on the B0 (Logan) platform. Each of the three brands will produce models on this line.
Renault’s own Avtoframos plant in suburban Moscow continues to produce the Logan and Sandero, building slightly more than 51,000 units in 2009. The successor models are due to be made there from 2013. Like Renault, Nissan was hit hard by the collapse of the local market in 2009, but has since staged a steady comeback. The (imported) Qashqai crossover is its most successful model, with just over 13,000 units sold in the first three quarters of 2010.
The next model for the St Petersburg plant, currently building the X-Trail SUV and Teana saloon, will be the Murano, assembly of which will start in January 2011. While volumes will be small, the addition of this larger crossover is a vote of confidence in the plant. In terms of future products, it would not be surprising to see the next Qashqai built at St Petersburg from 2012, while the Teana and Murano are due for replacement in 2013; a new X-Trail is expected a year later.
Ford
Despite having set up its local manufacturing operations some years ahead of its various rivals, Ford continues to struggle against the likes of Hyundai-Kia and General Motors. That may change with the launch of the thirdgeneration Focus in the second half of 2011. The current saloon bodystyle has proved popular with Russian buyers, though the opposite is true of the larger Mondeo, also assembled at the firm’s Vsevolozhsk (St Petersburg) plant. As large sedans such as the Mondeo have fallen out of favour with buyers, Ford is unlikely to assemble the replacement model at Vsevolozhsk and may even discontinue the current car before then. In its place would logically go a Focus derivative such as the Kuga crossover, or possibly a low-price small car such as Ford of India’s wildly successful Figo, though that model sits on a now elderly architecture. Instead, Ford may choose to launch a low-cost variant of the Fiesta sedan, aping its Brazilian market strategy – low-price small sedans are also the biggest sellers there.
PSA Peugeot Citroën and Mitsubishi Motors
One of the most recent examples of the ever-expanding alliance between PSA and Mitsubishi Motors (MMC) was the summer opening of a €470m assembly plant at Kaluga, 180km south-west of Moscow. The complex, funding for which was split 70/30%, PSA and MMC, has an annual capacity of 160,000 cars and SUVs, although this is not due to be reached until March 2012.
The first Mitsubishi to be built at Kaluga was the Outlander XL, SKD assembly of which got underway in September, closely followed by its Peugeot 4007 and Citroën C-Crosser derivatives. The partners expect to make a combined 25,000 vehicles in 2010. The Citroën C4 will enter production at Kaluga in 2011, following the start of Peugeot 308 assembly in April 2010. Following on from this, the next model to enter production may be the related 3008 model.
The Lancer replacement is expected to be the first Mitsubishi car to be made at Kaluga (2013) but the ASX, a small crossover, could still be added in 2011 or 2012. Future Peugeot and Citroën variants of the ASX have been confirmed for 2012, but PSA is yet to state where these would be assembled. One scenario could see production of all three vehicles at MMC’s NedCar factory in Holland.
Sollers: Fiat, Chrysler and SsangYong
For the size of its global footprint, Fiat Group has an astonishingly small presence in Russia. This, though, is likely to change in the near future, following the establishment of a 50/50 joint-venture between the Turin-based OEM and Russia’s OJSC Sollers (formerly Severstal-Avto). This ambitious plan calls for the eventual assembly of 500,000 Fiat Group and Chrysler Group cars and SUVs at Sollers’ Naberezhnye Chelny plant in the Russian republic of Tatarstan. The first model, Fiat’s Linea saloon, started rolling off the line in August.
While the joint-venture betwwen Sollers and SUV and luxury car manufacturer SsangYong could continue, this is dependent on a succesful buyout by India’s Mahindra & Mahindra.
Toyota
According to statements attributed to the head of Toyota Motor Russia, Takeshi Isogaya, the company plans to significantly accelerate its Russian business activities, which could include construction of a second assembly plant. The Camry is the only model made by Toyota’s existing St Petersburg facility and sales have been disappointing. Still, while fewer than 15,000 units are expected to be built and sold in Russia this year, that is almost double the number of 2009. The St Petersburg has sufficient capacity for 200,000upa, with the original production target for the Camry set at 50,000 units.
The RAV4 (replacement codename 120X) and Corolla sell almost as well as the Camry, so each could be in the running for any future plant. Another likely product would be the Etios (800L), a small saloon and hatchback range for emerging markets, production of which has just started in India.
Volkswagen Group
Like Toyota, the Volkswagen Group has thus far struggled to become a major player in Russia but, equally, it seems determined to improve its recent performance. An assembly plant in the city of Kaluga, with a capacity of 150,000upa, produces the group’s best selling local model, the Škoda Octavia. This facility, which began life as an SKD operation, has also started production of the Polo Sedan, with output expected to reach 30,000upa in 2011.
Ironically, the Volkswagen Group has been in talks with GAZ with a view to taking over one of its manufacturing operations. The Russian OEM has a modern plant in the city of Nizhy Novgorod with a capacity of 100,000upa that has made fewer than 3,000 Volga Siber saloons in 2010. Clearly, subcontracting the facility to VW makes enormous sense.
Conclusion
As the ambitious plans of these manufacturers show, vehicle manufacturing in Russia appears set for a new phase of solid growth. This year, total vehicle sales should come in at around the 1.5m units, roughly the same level as that of a medium sized mature market such as Canada. As recently as 2008, analysts were predicting an annual Russian new vehicle market approaching four million units, but that is now unlikely before 2014. Having seen production and sales collapse only 18 months ago, manufacturers are reluctant to make new production predictions, yet as the ongoing investments show, this is not a market that any major OEM can afford to ignore.