Paintshop 4.0
Nick Holt visits Eisenmann’s technology centre in Holzgerlingen, near Stuttgart, for a preview of the latest skidless paintshop technology prior to its installation at the Daimler plant at Kecskemét
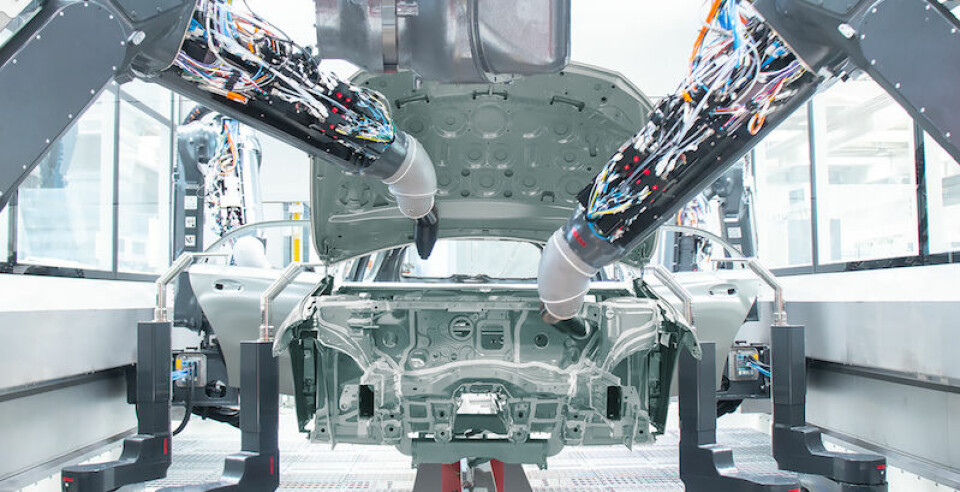
The skids used to convey vehicle bodies through the various coating and drying stages in the paintshop are seen as a limiting factor in increasing throughput and improving efficiency. These heavy (around 200kg) steel skids require frequent cleaning and are another structure, in addition to the vehicle body, that has to be heated and cooled, therefore requiring greater energy consumption. Eisenmann’s solution removes the need for skid with its modular floor-mounted VarioLoc rail system. This uses individual, autonomous electric motors to move each vehicle through the coating process and drying oven, avoiding the need for lubricated chain systems.
Jörg Robbin, Eisenmann’s vice-president of product development, automotive systems, explains the company’s aims when developing the VarioLoc system: “Flexibility is very important to us. It’s our priority, our guideline. We want to combine flexible hardware with intelligent software for the benefit of the customer. This is our understanding of industry 4.0 and also our priority in everything that we do.”
Simplifying the current form of the paintshop was the start point. “We really thought about streamlining the processes and how could we save energy,” he adds. “These skids, for example. We heat up the skid and after each process step we have to cool it down again, and that is unnecessary because we only need the painted car body in the drier. So, we have the opportunity here to leave out everything that you do not need. Everything that wastes money and that requires a lot of effort when it comes to maintenance.”
This system offers a high level of precision in term of positioning the vehicle at any point in the process. Each car body has its own controls; its own smart system via the VarioLoc that it is mounted to. A barcoded strip runs along the entire length of rail through the paintshop and this is said to allow the precise position of the body to be monitored and controlled. These smart systems extend from the pre-treatments to the drying and the company has redesigned this last stage with its smart oven.
Process engineer Jonas Eckhart explains some of the features of the new drying oven and how the VarioLoc system improves the efficiency of this process stage: “In the main part of the oven we have the big combustion chamber and a heat exchanger, and so we generate the hot air inside the wall [of the oven],” he begins. “The ventilators are implemented from the top, so all the parts we need – the ventilator, the burner, the filters – everything is installed inside the oven wall. That means we don’t need heating boxes and no additional [external] duct work.”
Eckhart notes that: “Every duct you have in a plant has pressure losses. That means if we have less duct work we can save, or we can reduce, the pressure losses. Also, every surface that we have in the oven has heat loss, and so if you have less surface [area] then we can also save energy. Another advantage is we can save a lot of space in the plant. A conventional oven needs a second platform, and here we don’t have this platform. We just have the oven and so we can save the space on top of the oven.”
Hitting the hot spot
The oven is divided into heat zones and the VarioLoc system allows very precise movement and positioning of the vehicle body as is passes through the oven.
“The car body is tracked through the oven and we have at least six [zones] in the oven that can be at different temperatures, this allows us to heat up the car body slowly,” explains Eckhart. “That makes the quality better. Also, we have a lot of different nozzle types and in every zone the nozzle configuration is different, so we can target and heat up the big heavy parts of the car body [A-pillar, B-pillar and the C-pillar] at the same speed that we can heat up the doors, for example, because the doors are very thin.“Our target is to heat up the whole car body in the same speed or in the same time, and not too fast. If we heat up the car body too fast, then the paint gets a lot of quality issues. Also, we know the position of the VarioLoc at all times and the car body type. Some producers have ten, 12 different car bodies [produced] in one plant, so we always know which car body is on top of the VarioLoc. We can also monitor the maintenance intervals for the system, for example the VarioLoc sends the information on a motor’s time and distance of operation so we can send it to the maintenance platform, if needed.”
Keeping control
To control all of these smart systems the company has developed its E-MES (Eisenmann Manufacturing Execution System). Daniel Hartmann, head of sales and marketing at ENISCO (Eisenmann Industrial Software Company) explains what the system does. “First of all, equipment monitoring,” he begins. “What is the status of the equipment, whether it’s in a paintshop, what’s the status of my VarioLocs, what’s the status of other conveyors, what’s the status of the process equipment like the smart oven? Do we have any problems with that?
“Building on this information, maintenance is an important issue. We support reactive maintenance, so if something breaks down we give the maintenance guys tools to solve the problem. We tell the workers exactly what tasks they are required to perform and provide them with all the tools necessary, such as the manuals, e-plans, drawings, instructions and the steps to complete the maintenance task.“The next step is predictive maintenance, which is something we are working on right now. We collect all [operational] data so if we have any incidents or failures this information is in our system. Also we see all the variable input parameters. How did we use this device? For example, a motor, how long was a motor driven and in what frequencies? All this information is saved in our system. Then, based on this data, we can do condition monitoring and predict failures”.
Hartmann notes that the system also provides material flow management and tracking, the latter being millimetre-exact thanks to the VarioLoc rail barcode. “We know exactly where the car body is [in any part of the process]. So, all the process values from the paintshop – for example, pH value, temperatures, currents – can be now tracked and linked to the individual car body.” He points out that this information allows any issue with any vehicle to be examined in detail and identified to an exact position in the process.
Quality management is big part of the software, according to Hartmann. The quality information is collected and stored in a central upper level system, so when E-MES is controlling the complete factory it offers a view across the bodyshop, paintshop, and the assembly line operation.
A technical partnership
Eisenmann was awarded the contract for the new paintshop at Kecskemét in 2016. According to Daimler’s Stefan Schubert, the companies then had two years to find viable technical solutions for the new plant. “We tested the solutions and we decided to use this new system,’ he recalls. “For us at Daimler it’s important when it comes to industry 4.0 to be a pioneer, to be leading the field. So, we need the enablers, the technology that provides us with the opportunity to really be leading the field.“There are several processes and technologies involved in this. We picked the VarioLoc [system] because it is a great example of the kind of technology that can be further developed.”
Schubert explains some of the priorities in the development process: “Its [level of] complexity is important. All our vehicles have to be moved on one surface. Maintenance is important. So, we need to keep the cleaning process, the maintenance process and everything that’s involved to a minimum. Innovation and energy conservation are very important to us… and as an OEM it also needs to be cost-efficient, of course.”
While the VarioLoc system is already being used in different applications with other manufacturers, the project at Kecskemét would be the first time it was used for all surface processes, and this posed number of challenges. Schubert highlights the attention that needed to be given to the process layout, standardisation and control technology, factory layout, equipment maintenance and worker safety. “For the process requirements it was really important to see that a skidless movement would be beneficial,” he says. “We had to take a look at each single process and make sure that we didn’t miss anything.
“The VarioLoc is a monorail system and has to be 100% stable. That means whenever we enter a workdeck we need to make sure that there is no side movement and we found a very smart solution to do that. Looking at body flexibility and under body design, the VarioLoc now makes it possible to mount all car bodies and we are convinced that we are now prepared when it comes to future car models.“We obviously wanted a very low failure rate, so maintenance needs to become much simpler. Now I no longer have this huge steel skid and that makes it easier to clean the whole process, and it’s also more eco-friendly.
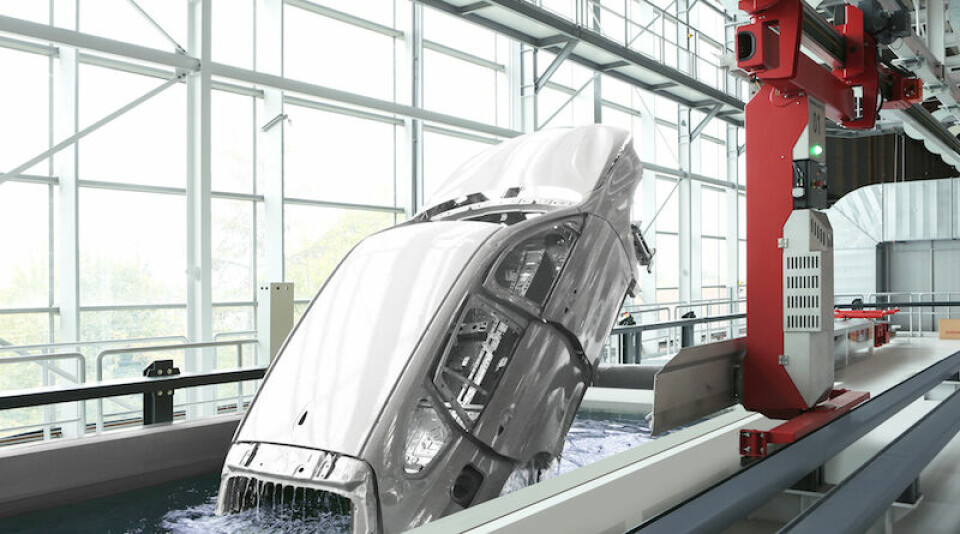
“And, of course, safety. We want our employees to work safely and the VarioLoc is very safe. However, it moves around at the centre of a workdeck and we need to train our employees in handling this system,” explains Schubert.
The building to house the paintshop didn’t require any significant changes to accommodate the VarioLoc system, according to Schubert, but the ability to add curves in the process flow and vehicle orientation and position had to be considered along with the potential need for an additional buffer zone. The layout of the system also had to consider the fact that the car bodies had to move from the paintshop to the assembly line and through all the different stages, including any buffer zones.
It’s interesting see how Eisenmann and Daimler worked together to ensure the VarioLoc system would meet all the requirements at the Kecskemét plant. There is always a strong focus on standardising and simplifying production processes, and system suppliers will present what they call ‘turnkey’ solutions, and to some extent they are, but this example highlights how these systems are developed and fine-tuned to meet the requirements of a specific customer or manufacturing site.
Skidless paintshop for electric vehicles
Since AMS visited the Holzgerlingen technology centre, Eisenmann has announced it is constructing a second skidless paintshop (utilising the VarioLoc system), this time for electric-vehicle start-up DEARCC in Shaoxing, in China’s eastern Zhejiang province.
Eisenmann says it was tasked with the project in the summer of 2018 and the first electric vehicles are expected to roll off the line from late 2019.
DEARCC will produce a new E-SUV model named ME7 at the Shaoxing factory. The new car is the first model under the high-end brand Enovate which was released by company in November 2018.Eisenmann notes it will be supplying a pre-treatment and electro coating zone equipped with E-Shuttle 200 conveyors plus spray booths, dryers, work decks and the ventilation and exhaust air purification systems. The paintshop will use the E-MES production control system.