Parts of the process
Tenneco CTO Ben Patel talks to AMS about the company’s approach to perfecting process, sharing best practice and mastering materials
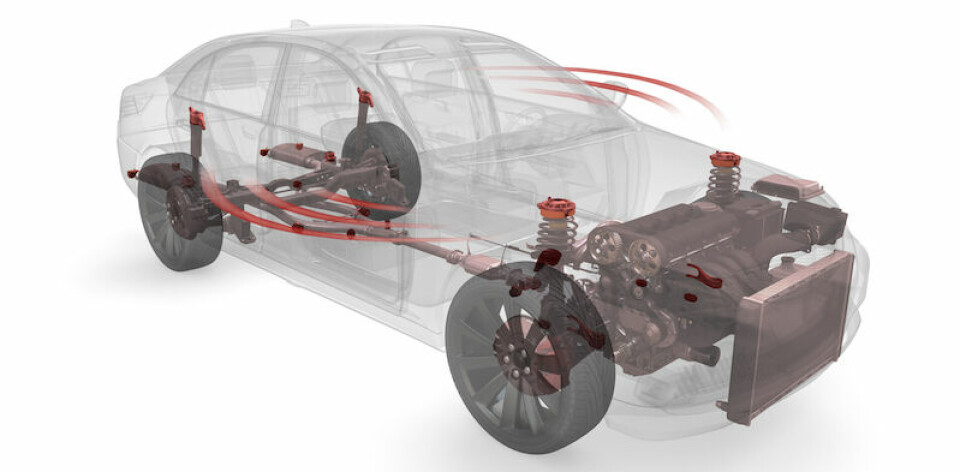
Spinning off from a multi-sector conglomerate enterprise in the 1990s, the Tenneco of today takes it manufacturing focus along two distinct component groups. The clean air line features exhaust systems, catalytic converters, DPFs and manifolds. The ride performance division covers suspension and damping technologies along with elastomer NVH solutions.
Based in Illinois, the company serves diverse markets from light vehicle, commercial truck, off-highway equipment and has seen significant growth in product lines and has expanded its global footprint over the last 15 years. In China, for example, Tenneco was among the first foreign automotive tier suppliers to establish operations there, supplementing the company’s existing engineering and manufacturing operations throughout the world.
Tenneco operates more than 90 manufacturing facilities worldwide with 31,000 employees. AMS met with company vice president and chief technical officer Ben Patel to discover how Tenneco ticks.
How would you characterise Tenneco’s manufacturing operations?Our core is high volume manufacturing of components for clean air, ride performance and underneath ride performance we have the elastomer business. All three are unique because the products are very distinct. What is common to all, however, is that it is fundamentally high volume. Around 70% of our business is on light vehicle platforms.
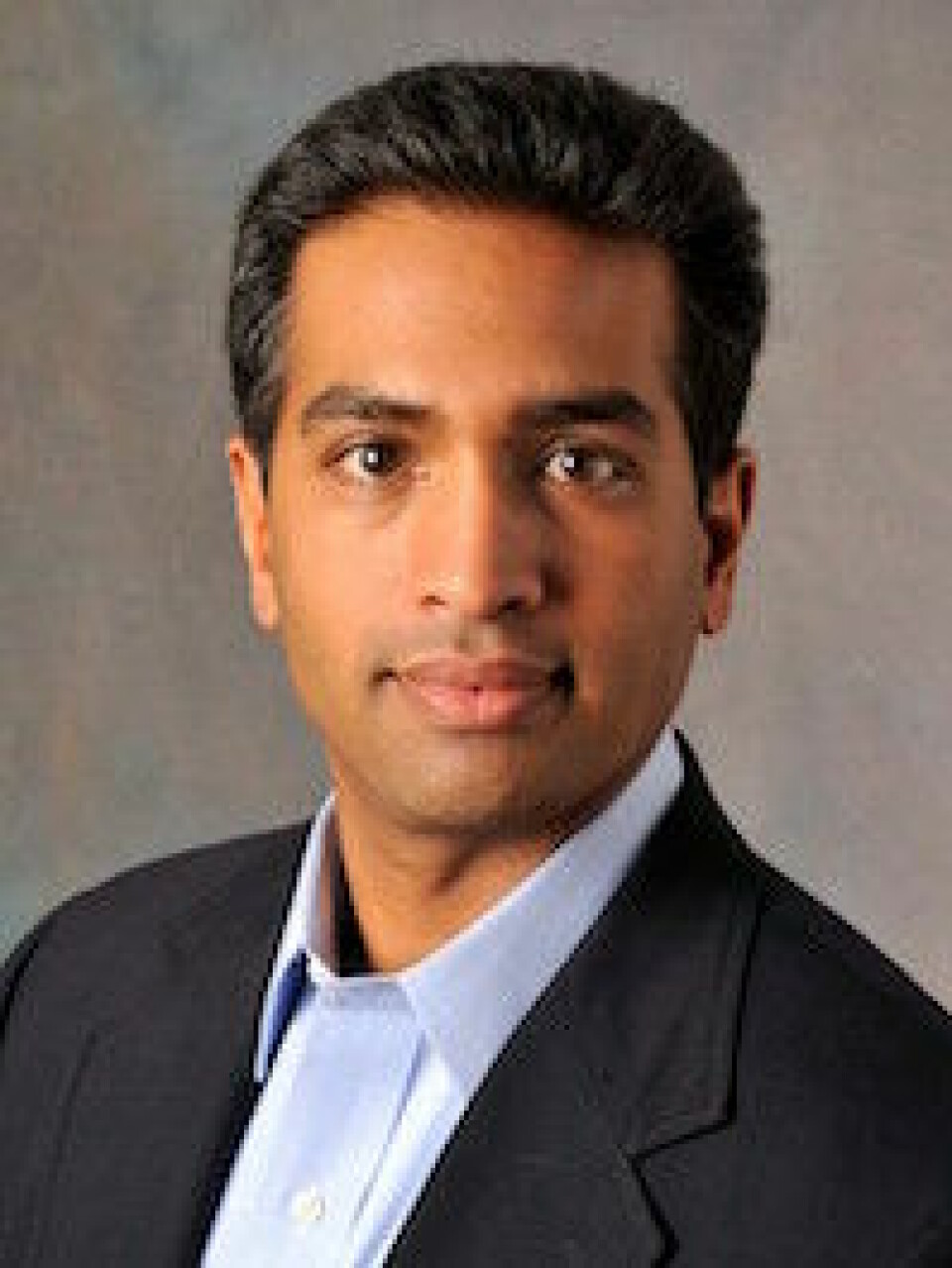
"As exhaust temperatures continue to come down it opens the envelope to a whole new range of materials" - Ben Patel, Tenneco
How does high volume shape your activities?Our approach is to look at how we take lowest cost designs, lowest complexity designs – things that at the end of the day make good sense for Tenneco but also good sense for our customer. We ask how we can standardise, whether it’s tooling or manufacturing process, or design. We can drive the highest efficiency in processes regardless of whether it’s a clean air, ride performance or elastomer component. What is constantly evolving in that process is, obviously, best practice. At Tenneco, under the leadership of Brian Kesseler – we have a new CEO this last two years – is a lot more best-practice sharing across the company. When something happening very effectively in one plant manufacturing environment, it is quickly determined whether or not that benefit has value – all along the product line within that business or in some case across the enterprise. We call that the Tenneco Business System – manufacturing is one of the four core elements.
How does the Tenneco Business System operate?There’s geographic distinctions, customer and platform distinctions and product line distinctions. In a best case scenario, something that leads to higher efficiency, quality or safety – any attribute that you would want across your geography and across your product line — the Tenneco Business System now allows that best practice system to be more effectively shared. That kind of lean approach, continuous improvements, that within our core DNA – but what is new, is Focus Factory.
Tell us about Focus FactoryIt’s a pilot cell. Within a plant that’s running the standard process or producing a given part, can you create a pilot environment that allows you to play with different positioning of equipment and experiment with different processing improvements — if it demonstrates desired efficiency that then becomes a pilot for what can be rolled out across the plant shop floor.
Is operator experience taken into account?Yes, we drill all the way down to the operator, who sometimes has the biggest impact both in providing feedback and the efficiency of the operation unit. We look at how to take the learning and promulgate it through the rest of the plant, that’s what Focus Factory is designed to do.
To what extent does automation feature?In general, standardization and a highly automated processes is what we strive for. We strive for common, robotised processes from plant to plant and region to region. There’s no substitute for human perspective but at the end of the day we want to drive the highest efficiency possible in order to have the lowest manufacturing cost. When a design lends itself to be fully automated that’s the ideal scenario, from both a quality and speed standpoint.
What role does data play for Tenneco? In clean air, traceability is very important from a catalysis standpoint. We need to be able to identify which substrate went into which can and into which part of which vehicle. From a compliance standpoint or even a warranty standpoint, that traceability is absolutely critical.We would say the exact same thing for ride performance – we’re no different from any other high volume manufacturing
Looking ahead, what challenges are you anticipating from OEM customers?Exhaust systems, for instance, are among the heaviest subsystems on the vehicle. So the expectation from the OEM on Tenneco as a supplier is that when they set a weight reduction target, we receive a large percentage of that.
How do you tackle that?We can attack that with a variety of different approaches. Thinner gauges in materials: we can go to more innovative designs that can shrink the amount of steel that needed. We can introduce new technologies, one we have is called smart sound – it’s basically active noise cancellation. We can take a muffler box, which is really a chamber for attenuating sound, and actively create sound waves that cancel out the sound waves made by the engine. This means I can shrink the muffler box so introducing that technology, one could argue, is a lightweighting innovation as it reduces the overall weight of the system.
Do material and joining innovations offer opportunities?Yes, I would say that material science is probably next big disruptive topic in this field. You can move to joining dissimilar materials, if the cost benefit is there – for example, moving to titanium in certain very niche applications in premium vehicles. Learning how to join steel and titanium is a research activity we have ongoing at Tenneco. People don’t realise that it’s not simple. The coefficient of thermal expansion is very different for those two materials. All of this falls under the umbrella of trying to drive lightweighting, which itself is driven by regulatory need to reduce CO2 emissions. When you think about Tenneco’s clean air component production, fundamentally, joining is the core competency of the business. So from an innovation standpoint we are always looking at joining methodologies. If we look at aerospace today – a tremendous amount of an aeroplane is glued together – so high temperature adhesives are eventually going to move their way into automotive.
Which processes could benefit?On the vehicle body there are already present but in the high temperature component like an exhaust system you can see a path to how that someday will become a core competency. As exhaust temperatures continue to come down and we continue to figure out how to harvest energy out of the exhaust (which again reduces heat) it opens the envelope to a whole new range of materials.You can imagine a world where the cold end of an exhaust system is made from something like a thermoplastic because you start to get down to the 150-160ºC range. In the world of plastics you really can talk about lightweight design. Maybe you have a hot end system that is still stainless steel, a heat exchanger in the middle to extract energy, maybe for cabin heating, and then the whole cold end of the system can be injection-moulded plastic. Everyone is focussed on powertrain right now – once we get through that, material science will be the next big thing.