Inside track
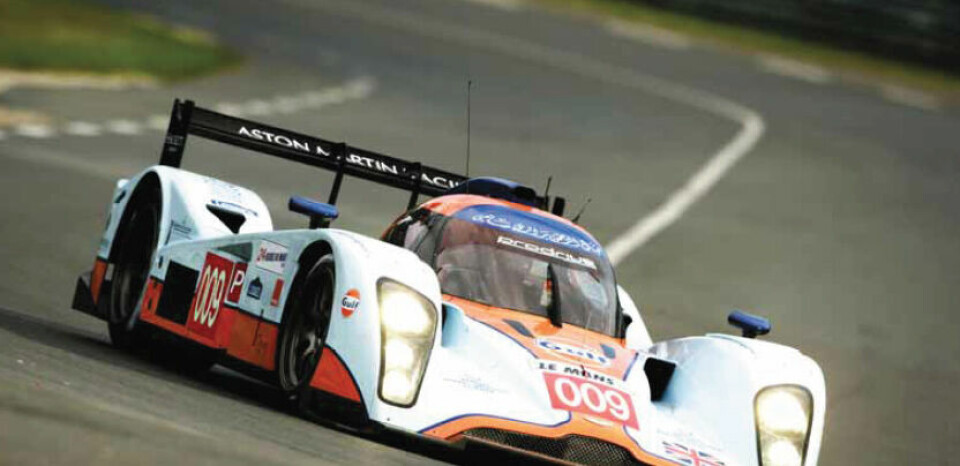
The motorsport industry believes that materials and powertrains developed on the track lead to better, more advanced production cars. AMS visits one of the world’s most famous motorsport technology companies to see if such claims are true
Prodrive, perhaps most famous for having been the long-time partner of the Subaru World Rally Championship team, is located within the UK’s high-tech motorsport technology cluster. Though the recent recession caused Subaru to cancel its racing programme in late 2008, Prodrive maintains strong links with the Japanese carmaker, while developing new OEM alliances as capital flows back into motorsport. Tony Butcher, Prodrive’s Managing Director and Head of Automotive Technology, has developed his industry expertise through working at the top level of motorsport, including working withe with the former Benetton Formula 1 operation, which went on to be the current Renault F1 team.
Butcher’s days of F1 involvement may be behind him, but his vehicle design and manufacturing experience have proved invaluable as Prodrive continues to spearhead motorsport technology transfer programmes in partnership with some of the world’s major OEMs. “When I joined Prodrive 11 years ago, we were basically an assembler of racing cars,” Butcher states. “But then our strategy changed and we began to in-source and invest in machine tools.”
Pressed as to why the company decided to bring so many specialist motorsport parts makers onboard, Butcher identifies quality as the number one reason, closely followed by speed of response and price. The last of these, he points out, is critical, as a busy supplier will always charge premium pricing. For obvious reasons, Prodrive is extremely reluctant to name the OEMs with which it is working on precision technology, but a tour around the company’s impressive facilities reveals hints of the possible identities of some of those clients.
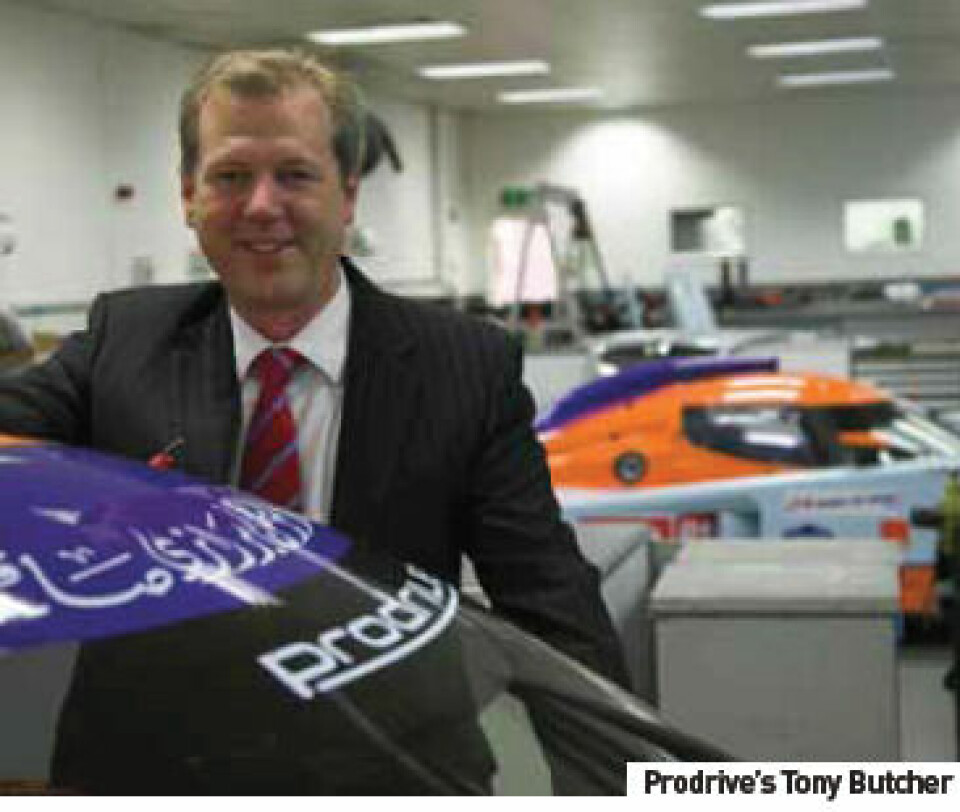
Motorsport technology reduces vehicle weight
The Aston Martin Le Mans programme has its headquarters in a dedicated complex within the Prodrive compound. In addition to this, the site houses various machine shops and other cordoned-off ‘skunk works’ buildings. In other areas, craftsmen work with metals and carbon fibre, surrounded by various racing car and low-volume production vehicle components, the often beautiful results of their labours. Tony Butcher believes that specialist motorsport concerns such as Prodrive have much to offer the world’s vehicle manufacturers. “There are many challenges facing both motorsport and volume manufacturing. For example, we need to keep improving engine efficiency and reducing overall weight. If you think about it, a racing engine is about the most efficient engine there is, the disciplines and principles are similar. If you take the case of an Aston Martin V12, the standard engine is about 160kg, but our race engine weighs close to 100kg,” Butcher reveals.
It isn’t just engines that provide such a contrast when comparing the weight of vehicle components, as Butcher explains: “If you pick up one of the racing Aston’s doors, it’s a fairly lightweight part. But try to do the same with a production car’s door and you’ll probably struggle, due to the glass, the wiring, window motors. When it comes to advanced, lighter materials, motorsport is leading the way.” Getting the weight out of vehicles is bordering on an obsession for vehicle manufacturers, but this often comes at a high cost, as engineers turn to advanced materials to achieve the desired results. Does Butcher see more use of carbon fibre, a material long familiar to motorsport specialist firms? “To understand what’s happening - and what’s ahead - you have to look at this as a material science. Right now, carbon fibre is a material that’s setting the world on fire and people are constantly amazed by its combination of strength and low weight. But there is so much more to come; already the military is working with nano-carbonfibre, experimenting with body armour.”
From its headquarters in Banbury, UK, Prodrive oversees subsidiaries as far afi eld as Australia and China. The company was established in 1984 by David Richards, a fomer rally co-driver who is still company chairman and has since run the Benetton and British American Tobacco Formula 1 teams. In 2007, Richards lead a private consortium which bought Aston Martin from Ford.
Today, company subsidiaries run Ford Australia’s hugely successful V8 Supercar team and the related Ford Performance Vehicles division. Back in the UK, Prodrive has run European touring car teams for several manufacturers, including Ford and BMW, while decades of rallying expertise are currently centred on building and maintaining Subaru customer cars. A return to top-level rallying is expected to take place in 2011, but the identity of the manufacturer remains a closely-guarded secret.
Prodrive has won the World Rally Championship six times in partnership with Subaru, fi ve British Touring Car titles with Alfa Romeo, BMW and Ford, as well as three best-in-class wins with Ferrari and Aston Martin. The Aston Martin Le Mans effort is currently run out of bespoke premises within the Banbury complex.
Any return to Formula 1 racing has for the moment been ruled out after an attempt in 2009 to buy the Renault team proved unsuccessful.
In addition to its motorsports activities, Prodrive has a growing business in developing low-volume vehicles for various OEMs, while also developing advanced technology applications for road cars.
Carbon fibre might well be seen as a miracle material for getting the weight out of cars and trucks but what about cost, the material’s major drawback? “Carbon used to be such a labour-intensive, manual manufacturing operation,” Butcher explains. “But we are already producing lightweight panels for two road car manufacturers (agreed confidentiality means they must remain unnamed) and the speed of response, working to an agreed budget, that comes directly from motorsport.”
Carbon body panels and interior trim is an interesting case. Referring to various highly-lacquered carbon fibre pieces that are prominently displayed on some vehicles as ‘automotive bling’, Prodrive’s MD believes this does a disservice to the material.
“The material’s strength is longitudinal; that’s why it’s arranged in weaves. If you look at a carbon panel that’s very shiny, it probably won’t be too strong as all that gloss means it’s heavily coated in resin. Rather than go down that route, we instead developed a process that uses lots of carbon and very little resin. That way, we get the strength.” Prodrive has been very successful at selling this specialist construction technology to OEMs, as many manufacturers have learned the hard way that great-looking but cheap panels will tend to contain chopped-off fibres, translating to part fragility. As Tony Butcher puts it, “you get what you pay for”.
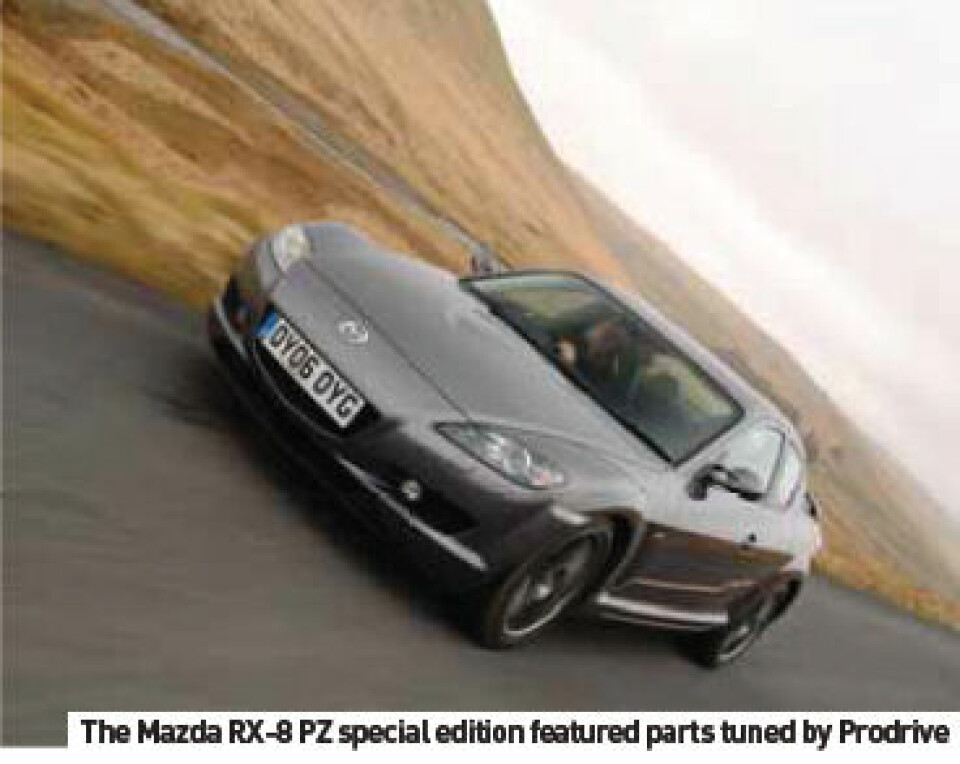
EVs: Back to the future
One area where OEMs are increasingly looking to reduce component weight is in the next generation of electric vehicles (EVs). Yet as Butcher points out, this is only one in a series of challenges.
“(EVs) have a huge range problem, plus batteries run down rapidly in very cold weather.” This aside, Prodrive’s MD admits that some OEMs will eventually find success with these cars. He also believes that we are only just at the start of a long development process in this area and that huge changes to vehicle design might be coming.
“Electric drive has a number of benefits. Put a hub motor on each wheel and it’s possible to control those wheels individually. So why not turn them at different angles for easier parking? You can also give the vehicle a much smaller turning circle than we are used to seeing with today’s cars. We built a front-engined, rear-drive EV in 2000 for a research project, but we know there are several OEMs close to bringing an EV to market based on that same thinking.”
Consultant role
Prodrive is looking to remain a successful advisor and supplier to vehicle manufacturers. There continues to be no desire within the company to take on companies such as Magna Steyr for projects like the Aston Martin Rapide. In 2008, Prodrive built a record 108 vehicles, but most of these were motorsport-based cars. Tony Butcher puts it simply: “You need a car factory for such projects and that is not something we choose to have. We do have a flexible facility in Warwick that can build a small number of road cars, but around the 1,000-vehicle mark is our sweetspot.”
While series vehicle production is ruled out, another rapidly-growing side of the business is very much taking off. Like the production and supply of formerly exotic composites, the design of automated manual transmissions (AMT) is an area where Prodrive sees enormous growth potential. India, perhaps surprisingly, is one of the regions driving the demand for engineering expertise.
“Many emerging market manufacturers have significant prior investment in good manual transmission facilities and cannot justify the additional investment required to produce planetary autos,” advises Simon Leleu, Prodrive’s team leader for transmission and driveline systems. “With our technology, these existing lines can manufacture a mix of both AMT and manual transmissions, opening up profitable new opportunities to meet growing market demand.” Early on in the almost two-decade relationship with Subaru, Prodrive engineering works developed an AMT for the Japanese firm’s rally cars, created by automating a manual racing gearbox. Such technology can now be brought to market using relatively low cost production applications. “We have worked with OEMs in India on everything from the smallest motorcycles, up to the largest trucks and buses.” says Tony Butcher. He continues: “Car drivers generally want to save fuel, yet many drive in a style that strains the transmission – they simply change up way too early. The same problem can be found with those driving heavier vehicles. Automatic gearboxes could be the answer, but not in such a cost-conscious market.”
The deterioration in the appearance of visible carbon composite components is a problem that most OEMs dealing with the material have had to confront. With most applications being on high-cost vehicles, owners tend to be particularly unsympathetic when they notice parts of their car looking decidedly worn out. Prodrive has now perfected a system for dealing with this problem, increasing the cosmetic durability of carbon components and also reducing part cost. The fi rm’s process delivers an exceptional surface fi nish that it claims is at least equivalent to the best lacquered fi nishes. “It’s highly unsatisfactory if a large panel, like a diffuser, has to be replaced after a few thousand miles due to cosmetic deterioration when the part is, functionally, still serviceable,” Gary White, Prodrive’s Composites Engineering Manager points out. “We now have a finish which is so good that we can dispense with the lacquer entirely, returning multiple benefits; piece part cost reduction, better durability in service and improved consistency of appearance.”
Composite parts had required a lacquer coat on the finished surface, though the protective layer was susceptible to stone-chipping, which in turn resulted in unsightly white blotches. Prodrive analysed the production process for carbon composite parts, listing all the steps that would affect the appearance of the finished product. It was discovered that the relationship between the part and mould was critical.
As composite layers (plies) are added to a mould, air bubbles may become trapped, preventing not only secure adhesion between the plies but the seating of the outermost layer against the mould surface. With Prodrive’s solution, temperature is critical, as is the precise application of pressure and the duration of the manufacturing process. “We have established a set of process conditions that give the best possible consolidation of the outer layer against the mould surface,” says White. “We also pay particular attention to the mould surface fi ish, developing an appropriate ‘prepreg’ (curable mix of fi bres and resin) specification with our supplier.”
Gary White notes that the new process is being supplied to what must remain an unnamed supercar manufacturer. He adds: “All their quality processes were based on a lacquered fi nish. The issues you control with an unlacquered surface are completely different. For instance, spray finishes can suffer from runs and fish eyes; nonsprayed finishes can suffer from pinholes. We wrote new quality standards for them to reflect this, and they were delighted; they not only received top quality parts from us but developed their supplier quality standards for the future.”
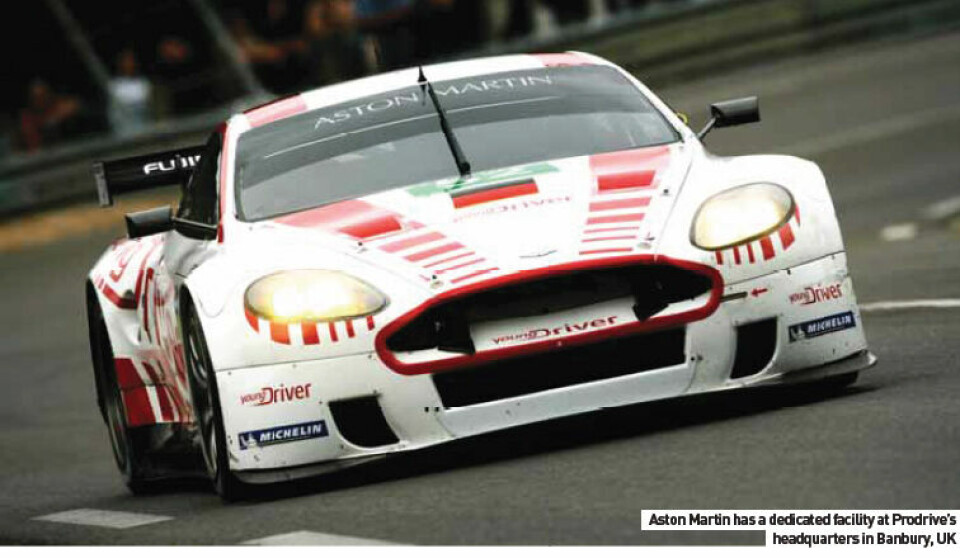
“On some HGVs, you can now programme the software to make sympathetic changes to protect the transmission. So if the driver naturally wants to put the truck into a high gear to save fuel, the system will prevent that happening too early and prevent damage to the drivetrain. Ultimately, you also save fuel.” Another example of direct technology transfer from motorsport to production vehicles is ATD or Active Torque Differentials. Where a traditional stability system will always default to applying the brakes if an electronically-controlled throttle reduction fails to rebalance an unstable vehicle, ATD uses an entirely different logic. The thinking behind it comes from time spent racing.
“Where a Tier 1 specialist supplier acts one way, we go the other, we apply what we would do for a rally car. We work with front-wheel drive, rear-wheel drive, four-wheel and even six-wheel drive systems,” Butcher explains. Following on from the latter, Prodrive was asked to develop a drive system for the oversized six-wheel drive vehicles used in large quarries. In such a heavily-loaded truck, a locked differential is needed for maximum, steady low-speed traction up and down loosesurface inclines. The problems come when the vehicle needs to turn.
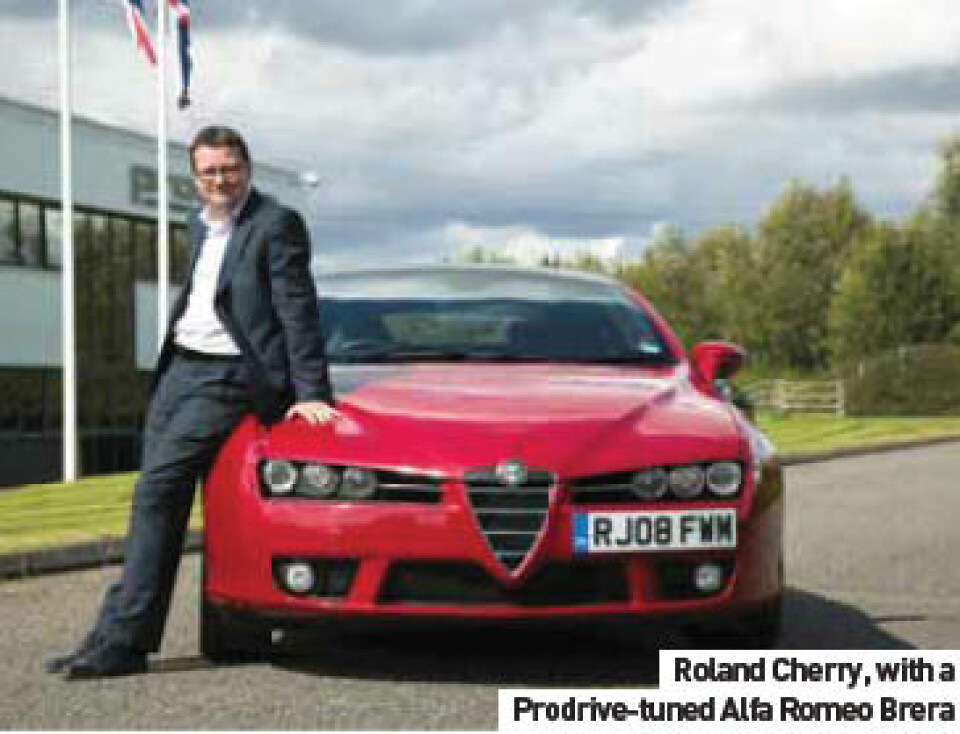
In these trucks, the skill of the operator is paramount. Even a slight bend can prove hazardous, as the outside rear wheel must turn faster than the inside wheels. To turn, the locked differentials are quickly and momentarily disengaged when the driver performs a crash gear change, causing a lot of strain on the transmission. One system Prodrive developed uses ATD to help these vehicles safely negotiate a corner, while at the same time dramatically lowering the strain on both driver and vehicle. As Tony Butcher points out, removing the brutal, manual gear change means lower fuel consumption, more precise control of the truck plus several other benefits. “If you eliminate a crash gear change, you’re preventing damage to not only the transmission, but also the tyres. In these vehicles, if you get a gear change wrong, you can take a chunk of rubber out of tyres that cost about £1,500 each. You don’t always find the answer in a logical way, but the ATD system we developed on the track demonstrates how lessons learned from motorsport can be used to solve a production vehicle problem.”
Working with carmakers
Roland Cherry, Prodrive’s Director of Special Vehicle Operations, heads the company’s low-volume, modified vehicle programmes. The division performs work for several OEM manufacturers, and recently handled tuning of the Alfa Romeo Brera and Mazda RX-8 for UK roads. “When we take on a project with a national importer, such as the Brera S, it can often mark the start of a relationship with the parent company. In the case of Alfa, they understand what we’re about, our sports and racing heritage,” says Cherry. Vehicle development programmes usually start with adjustments to a car’s ride and handling, explains Cherry. “Delivering on a promise to a manufacturer means making the car handle properly on UK roads. We can’t always change the geometry of the suspension system, so it’s a matter of various carefully-targeted adjustments. That’s where our experience on the track really pays off.”
Perhaps Ford Performance Vehicles’ (FPV) most famous driver (in a non-professional sense) is Mark Webber, currently driving for the Red Bull F1 team. The Prodrive subsidiary, based in the southern Australian state of Victoria, has its own racing arm, Ford Performance Racing, which builds track versions of Ford Australia’s V8 Falcon saloon. Having started life as Tickford, the name behind projects including Aston Martin’s Le Mans attempt in the 1980s, the company was acquired by Prodrive in 2002. Today, FPV works closely with Ford to improve the power, handling, braking, safety technology and styling of the Falcon-derived cars that it makes at its purpose-built manufacturing facility - the only one of its kind in Australia. Located close to Ford’s own plant in the Melbourne suburb of Campbellfi eld, FPV carries out such operations as tuning the Boss 315 V8 that it imports from a Ford powertrain plant in North America. As well as the big Falcon-derived sedans, FPV now also makes two Falcon Ute (pickup) variants, the Pursuit and Super Pursuit. The Prodrive subsidiary modifi ed Ford’s turbocharged inline six-cylinder engine, while this was followed by the F6X, a high-performance variant of the Territory, an Australian-made Ford SUV.
As for why a large OEM would turn to a company such as Prodrive, Cherry’s reply is revealing. “What we can offer these companies is speed. Here, there is none of the inertia that bedevils so many large vehicle manufacturers. The major reason why we don’t see more sports models from some carmakers is simply the time it takes to develop them.” Despite ending the formal relationship with Subaru in 2008, Prodrive still supplies performance parts to the company. “We have worked with (Subaru) on a number of programmes, like the efficiency of turbochargers, ways to minimise lag, but sometimes you find that you can bring an added dimension to what a manufacturer like Subaru might be looking to achieve in other ways,” says Cherry. “You can offer them assistance with developing vehicles for the specific needs and desires of vehicle buyers in various countries, setting up the ride and handling compromise, for example.” Whether or not Prodrive is credited with the work done on a particular car always depends on the vehicle manufacturer in question. With some, such as Subaru or Mazda, the relationship has been highly publicised. But why do some OEMs prefer to keep the identity of their development partner a secret?
“We are always in the process of talking to manufacturers about new vehicles and how we can improve them. Some companies want to leverage the Prodrive connection, while others prefer a more quiet approach. Generally speaking, when we work with an importer such as Mazda in the UK, there’s a lot of publicity, but if we go inside a large OEM and work with the engineers, they tend to shy away from discussing that collaboration,” Cherry reveals.
In the case of the RX-8, Prodrive worked with Mazda on a programme based out of Rotterdam, in the Netherlands. The goal was to tune 800 limited edition cars to give them a track-car feel, whilst maintaining the car’s ride quality; no small task. The car’s rotary engine was not modified. The RX-8 PZ project involved taking Mazda’s standard suspension components and making detailed modifications in order to lower the car’s centre of gravity. Spring rates were increased, giving improved agility, along with a flatter cornering ability and reduced rates of pitch. Bespoke alloy wheels and a rear wing to reduce lift were added, while the exhaust was tuned with a new silencer.