Heavy-duty Daimler
Daimler adopts a people-centric approach to advance its commercial vehicle production operations in IndiaThe first thing Felix Homburg, vice-president, Operations and Manufacturing Engineering, Daimler Commercial Vehicles, pointed out at the start of our tour of the company's truck plant in Chennai, India, was a large noticeboard featuring various employee incentive schemes. 'Employee of the Month' and ‘Lean-O-Mania’ competitions are fairly common, but the importance of these should not be underestimated as India’s labour-centric automotive industry relies heavily on engaging with the workforce to consistently achieve the required levels of quality and productivity.
The vast assembly hall gives a good view across the two main production lines for heavy- and medium-duty trucks, and the open meeting section at the head of the lines is a good representation of the transparency of the plant’s operational communication structure. Here, regular shopfloor meetings are held with team and section leaders so that all are able to discuss operational developments and any issues with Homburg and other senior managers. This open forum offers greater access to management, which in turn fosters a much more collaborative ethos among the workforce, and this is important; Homburg noted that devolving responsibility to the teams goes a long way toward building confidence and greater engagement.
Creating a quality culture The scale of everything is big, from the size of the hall to the vehicles themselves, yet the whole operation proceeds with a calm, quiet efficiency. The main assembly and smaller subassembly areas are spotlessly clean, the company having placed a lot of importance on creating a pleasant, healthy working environment at the plant, both indoors and outdoors. This, Homburg explained, helps with engagement, improves efficiency and creates a quality culture.
Observing the assembly of the trucks coming down the line, the process seems deceptively simple. The ladder-style chassis have axles, suspension, powertrain and cabs installed at various stations along the line and it would at first appear that this open, simple vehicle architecture makes the assembly process more straightforward than with cars. However, several factors compound the complexity and create challenges when balancing the two assembly lines.
Firstly, there is a widely varying workload at certain stations according to the variant or model (notably the new 3143 CM truck, internally dubbed the ‘Thunderbolt’) due to different content levels depending on the vehicle and the market for which it is being built. Longer average takt times might seem preferable to help with balancing, but Homburg explained that in fact shorter takt times help to improve quality and, ultimately, productivity. Moreover, the size and weight of some of the parts adds to the challenge of installing them quickly and efficiently.
“Our production operations are very robust, so the great thing is we are very capable of building models for both the domestic and exports markets” – Felix Homburg, Daimler
Getting the basics right Given the high level of manual operations throughout the plant, Daimler has worked very hard to establish solid processes and procedures within all production operations. It has also seen a heavy reliance on self-developed Kaizens (improvement strategies) to optimise efficiency, quality and productivity. Lineside tyre mounting is one area where simple changes to the flow of the operation and some clever solutions to racking, tooling and delivery ergonomics have made a significant difference to the efficiency of the process. The tyres and rims are cumbersome and heavy, but simple carts that now deliver the tyres to the assembly line station (arranged in the correct orientation for twin-wheel axles) have made installation a much smoother operation. This is a solution that has been shared with Daimler’s global network.
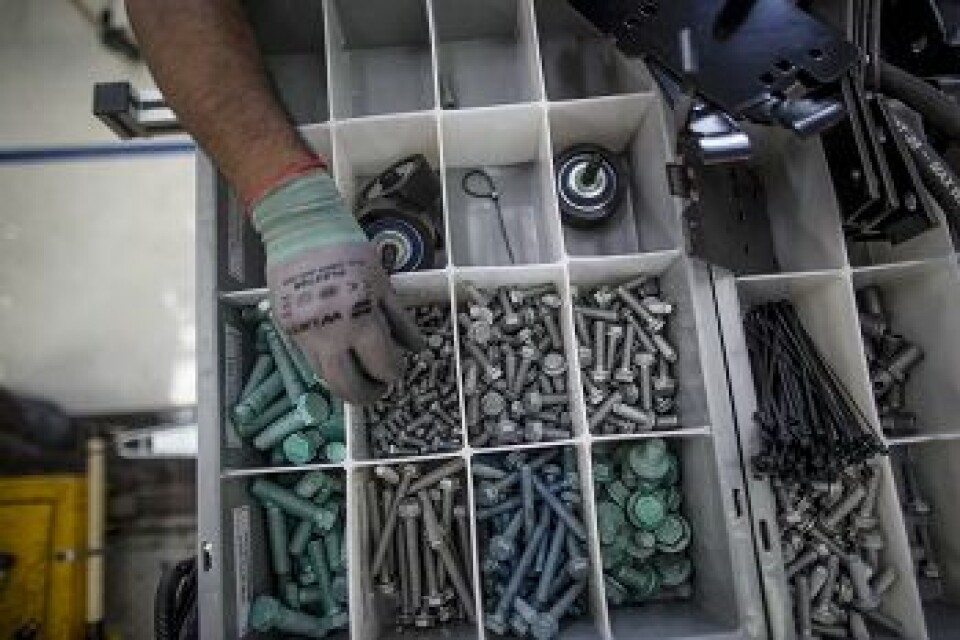
Kitting is used extensively to help error-proof the assembly process, with the parts cases and racking specially developed and designed by the line workers to sit on and around the vehicle as it moves down the line. The layout of the parts within the kits is described as ‘surgical’, with everything in a particular position.
Clearly a lot of development has gone into these kits but the speed at which these bespoke racks can be built and implemented is surprising. Special teams supplied with pre-formed tubing, connectors, brackets and fasteners can be called to the lineside to measure and construct anything of this type on the spot. It also allows any changes or adaptations to be made very quickly. As Homburg noted, this further encourages the workers to think about their particular job and come up with solutions to improve the process.
Working on expert projects As well as the myriad of small Kaizens that have been and continue to be implemented, there are also larger, longer-term programmes underway: ‘Expert Projects’ which are developed and executed over a three-month period. One such programme is to boost the efficiency of the cab subassembly line, looking at ways to improve the layout of parts and materials at the lineside and reduce the space required for this part of the operation. Although most of these developments require a low-tech solution, an automated guided vehicle is used to deliver cabs to the main line; this is an experiment which is part of a feasibility study to improve the delivery of the bulky cab units.
Production of Bharat Benz (9t-49t) and FUSO (9t-49t) trucks, plus engines and transmissions
Capacity of up to 70,000 units per year, depending on shift model
Site covers 400 acres and employs more than 3,000 personnel. It is houses the company headquarters and an integrated R&D centre, as well as a dedicated bus plant
Vehicles feature more than 85% local content from more than 300 suppliers
Engines and transmissions are both assembled at the plant and this is another area that has benefitted from the application of Kaizens. It is also the focus of another Expert Project, with the aim to improve the layout of components at the lineside. This would seem to be a serious challenge when observing the amount of parts needed for the engines and gearboxes, and the complexity of the build process, but Homburg is confident that big improvements can and will be made. The engine line produces both six- and four-cylinder engines, using a universal engine mount.
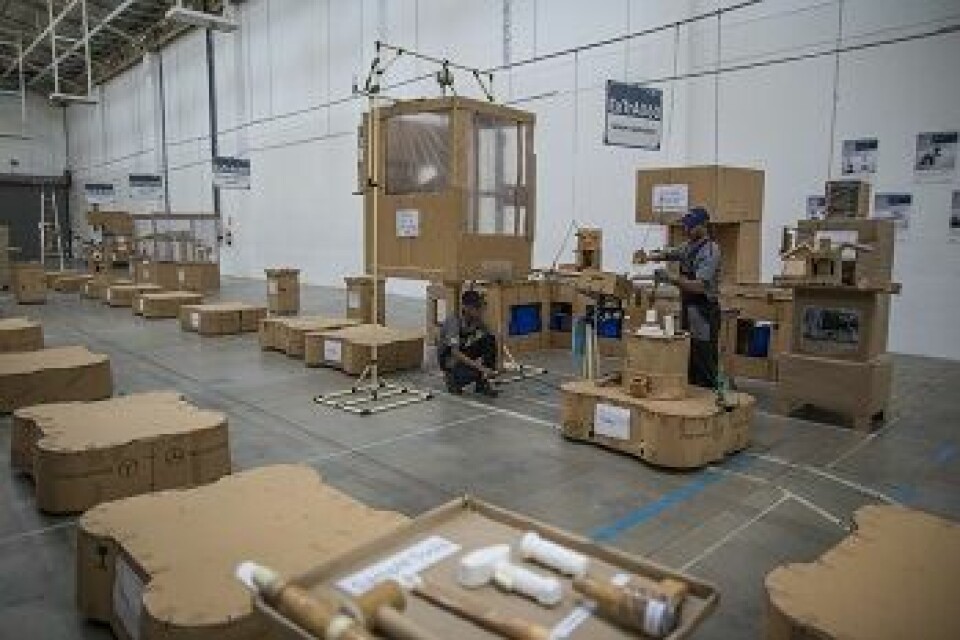
Simple solutions for complex builds The transmission line involves a complex process to build each gearbox, but also a very simple system that uses colour-coded golf balls to indicate when certain component sets need replenishing. Each worker has to focus on following an exact assembly procedure which includes preheating certain components to a preset temperature in order to enable the assembly of sections requiring an interference fit.
At the time of AMS' visit, the powertrain section was getting ready to add a new transmission line to expand capacity for export. In preparation for this, the operations team had built an exact replica of the planned line out of cardboard, complete with assembly stations, tooling, equipment and conveyors. The process was then worked through, timed and videoed, with everything from takt times to ergonomics examined in as much detail as possible to identify any problem areas and to optimise the layout for all sections of the new line.
With this impressive truck plant at Oragadam and a new bus production facility located next door, Daimler has demonstrated its clear intent to challenge for market share in India’s very competitive commercial vehicle sector. The plant is continuing to expand with new buildings under construction, although Homburg and his team would not reveal what additional operations they will house. What is very clear already is that the company has understood how to play to the strengths of India’s workforce, tapping into and developing problem-solving skills, and creating a greater sense of engagement. Interestingly, at a plant where everything is on a large scale, the smallest and simplest innovations are making the biggest difference.
Felix Homburg has been vice-president Operations and Manufacturing Engineering at Daimler India Commercial Vehicles since April 2015. Previously, he was managing director of Daimler’s former South African subsidiary, Atlantis Foundries near Cape Town, from 2011. A university graduate in Electrical Engineering, he started his career at Daimler in 2003 in the International Management Associate Program, subsequently completing various assignments with a manufacturing focus at Daimler Trucks plants in Woerth, Germany; Portland, Oregon; and Saltillo, Mexico.
AMS: During the tour of the plant, we saw a lot of small but very effective Kaizens being used across the production lines. Could you explain the approach to developing these improvement strategies?
Felix Homburg (FH): The manifestation of Indian Kaizens is brilliant, smart solutions that cost little or no money. When we look at Kaizens, it typically does not involve big budgets; somebody [on the production line] comes up with an idea and we build it ourselves. You saw the mobile teams during the tour that bring all the tools and pre-form tubes, etc [to the lineside] to build new carts. Problem-solving is very important to us, it’s a big part of our shopfloor management. We operate in a way that allows us to stop the line if there’s any issue as we want to produce quality the first time not ‘inspect’ quality into the product. So even a line stop is actually part of the problem-solving routine.
These building blocks allow us to get the workforce into a methodology of following the standard work instructions. This then lets them think about what really matters: where improvements might be made in their work area. We drive these improvements either through Kaizens or bigger projects – we call these ‘Expert Projects’ – and these might take up to three months to complete. To facilitate these improvements, we have a ‘lean team’ who are highly trained in this area. However, these projects are the responsibility of and run by the departmental head, who can call on the lean team members for support and help with methodology and structuring the work.
We also have steering committees where every quarter we review our yearly targets, looking at the steps needed and resources available and decide which big project to run. Currently, we are working on an end-to-end project with our axle supplier, for just-in-sequence for axles and the cab line project where we want to take bigger steps to take this operation to the next level of value-added versus non-value-added, to remove a large amount of ‘muda’ – waste – out of the assembly process. This is a system that fuels itself, so building cost efficiency, good training and, importantly, a great place to work, where people feel they can contribute.
AMS: What identified the cab line as the next big project for improvement? Had it become a bottleneck?
FH: It was more that the chassis line had progressed a lot in terms of line design and efficiency and the cab line, in relation to this, was falling behind, so we challenged the cab line team to make some big steps.
AMS: Does building additional variants for export increase the complexity of the production operation?
FH: You’ve seen that our production operations are very robust, so the great thing is we are very capable of building models for both the domestic and exports markets. We have established very solid fundamentals in our production. That’s why we look at an export vehicle basically as just another variant to build.
AMS: Earlier, you mentioned training. How is that delivered, do you send any staff to Germany?
FH: We don’t have to. We have a fully integrated training centre here. As well as the induction training for everyone, which is quite sophisticated, we have more specialist training for particular roles, which involves both theoretical and practical elements. This allows us to develop skills to the next level. One example of this would be automotive electricians, because with increasing regulation of emissions [in India] trucks are now featuring higher-level electronics, so the potential for problems with these complex systems increases and we need the skilled workers in place to deal with any issues.
AMS: When the plant opened, it was reported that vehicles built here would contain up to 85% local content. Has this figure increased?
FH: Yes it has increased, although we don’t publish the exact figures. It’s a high level but everything we can source locally improves our cost position. We knew when we began that to be competitive in this [Indian] market we needed to push the localised vehicle content above 85%.
AMS: Which parts do you still import?
FH: The more complex components – electronics, fuel systems, etc – that we haven’t yet found an Indian supplier to provide. We have worked hard to get over 300 suppliers working with us. Some are German tier-one suppliers based here but also we have many fully domestic suppliers that we have helped develop to deliver the quality we need.
AMS: Daimler has an R&D centre here. How does that link to your production operation?
FH: The first purpose of our R&D centre is to develop products for the Indian market. Our latest product, the 3143 CM truck for the mining and construction industry, which we internally call the Thunderbolt, was designed here. We [production] are involved in the design concepts at an early stage with both new products and updates.
“We have very good people here with strong problem-solving skills and our training and systems that we put in place make us very strong in this market” – Felix Homburg, Daimler
AMS: So there is now a much closer working relationship between design and manufacturing?
FH: Yes, and today it is vital. It’s very important to design a vehicle with assembly in mind, right from the beginning, because while it’s easy to make changes at the design stage it’s far more difficult to change things in manufacturing engineering. It should be designed in a way that reduces assembly time, manages the complexity, for example having one master [wiring] harness which can then be modified [for different variants]. Our R&D centre deals with every part of the truck, axles, frame etc.
AMS: You have recently opened a bus production facility on this site. How much commonality is there between the trucks and buses?
FH: We build the chassis for the front-wheel drive buses and the powertrains. We can then drive the chassis to the bus plant, where the bodies are fitted. It made a lot of sense to locate the bus plant on this site; as well as sharing certain parts it avoids having to drive the chassis a long distance for bodies to be fitted, which is common in some regions.
AMS: Has the all-new Thunderbolt had any impact on production operations?
FH: The Thunderbolt challenges our production because it is produced on the heavy-duty line and in some areas requires almost double the workload of an HDT [heavy-duty truck]. The challenge for our production team is to come up with very flexible solutions to balance the workload across the line. So while we may never completely eliminate spikes in the takt times for these models, we still focus on standardisation of operations as this is the only way to achieve consistency in quality.
We started production of the 3143 in May of 2015, so ramp-up and increasing demand is also affecting the balance of the line. We are very proud of this vehicle, our first Indian-designed model. We have very good people here with strong problem-solving skills and our training and systems that we put in place make us very strong in this market.
AMS: Having set up and run this plant, what is the biggest challenge – in manufacturing terms – that you face to build trucks in India?
FH: I think managing the high number of local suppliers which contribute more than 85% of our content is quite an achievement. The consistent levels of quality that we require do not always come easily; sometimes it needs support from our side. Right now, for example, we have a project with an important chassis supplier, working with them to understand our lean methodology. So the more capable they get, the more stable our production system gets.
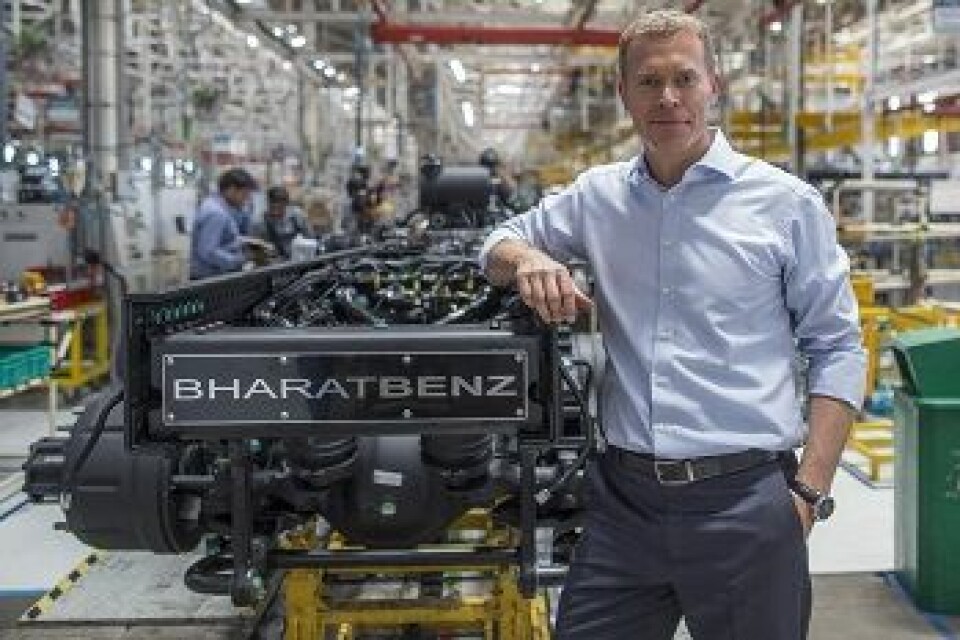