Growing gains in South Korea
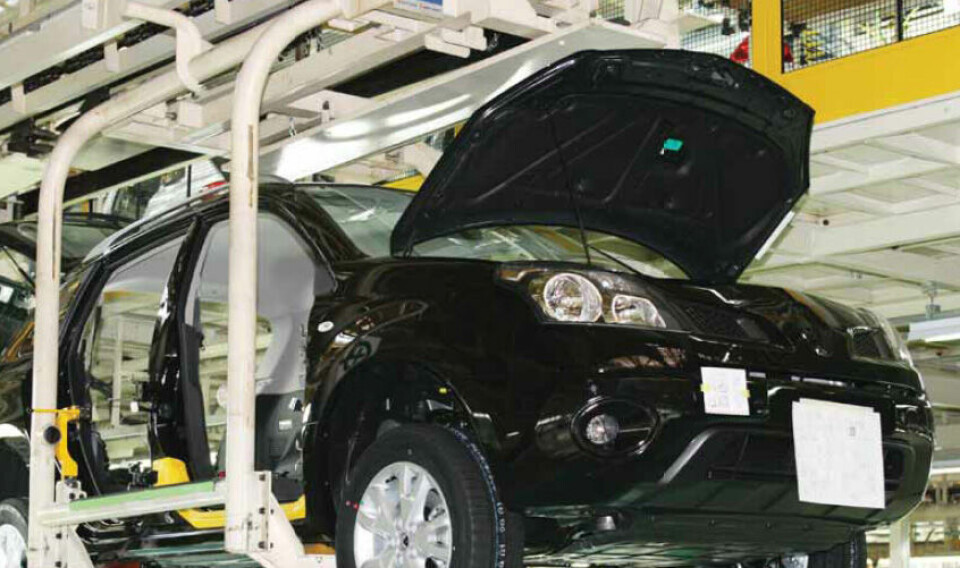
Production plants in South Korea are running at near capacity to meet global demand, but dealing with local unions is still proving problematic as the five in-country OEMs attempt to adjust production schedules. And considering the robust state of health of the South Korean automotive industry, it’s hard to believe that four out of five of the same companies have filed for bankruptcy over the past fifteen years.
So while the long-time number one, Hyundai Motor (HMC), has always managed to stay clear of trouble, its smaller rivals Kia Motors, the former Daewoo Motor (now GM Korea), Samsung Motors (now Renault Samsung) and SsangYong Motor have all at one time or another collapsed into administration. While HMC’s rivals are now all but unrecognisable from when they each started to claw their way out of receivership, so too is Korea’s largest car manufacturer compared to where it was even five years ago. It’s was almost a compliment when Toyota President Akio Toyoda stated that Hyundai-Kia is the one rival he watches more than any other.
Hyundai gained control of Kia in 1999, taking over from former minority partner Ford. Since then the company has steadily worked to integrate the firm into what is now the Hyundai Kia Automotive Group, where both companies set ambitious production and sales targets. HMC and Kia operate separate manufacturing plants in the home market but share platforms, powertrains and other major components where possible. In recent years Kia has even outsold the parent brand on occasion, but Hyundai looks set to remains the larger brand in the Korean market for the foreseeable future.

Hyundai Motor
HMC’s Ulsan complex comprises five plants which have a combined annual production capacity of 1.7 million passenger vehicles. The firm’s other main passenger vehicle plant, located at Asan, has an annual capacity of 300,000 vehicles per annum, mostly the Sonata saloon, a big seller in the Korean market.
In November 2011, HMC stated that it would look to revolutionise production at its home-market plants. The company would invest KRW300bn ($260m) to implement a new production initiative that would end the need for night shifts.
The firm plans to commence the proposed two-shift system from 2013. This will mean operating factories from an early daily start and ending production at midnight in place of the current operates day and overnight shifts. In order to put this plan in place, Hyundai must first finalise talks with its main labour union before moving away from night shifts, or else risk industrial action.
In fact, the move to end night shifts has been sought for many years by unionised labour working at Hyundai’s various plants. Workers claim that the long nights expose them to health risks, a claim supported by the South Korean government, which has placed pressure on Hyundai, Kia and other firms to phase out overnight production shifts. The country’s Ministry of Labour has produced data which claims to demonstrate that Korea’s automotive industry employees typically put in 2,400 working hours per year, which compares to 1,850 hours for Toyota workers in Japan and 2,080 for those employed by General Motors in the US. Hyundai claims that while it supports worker requests for better conditions, the cessation of night time car production will cut annual Korean output by an estimated 187,000 vehicles.
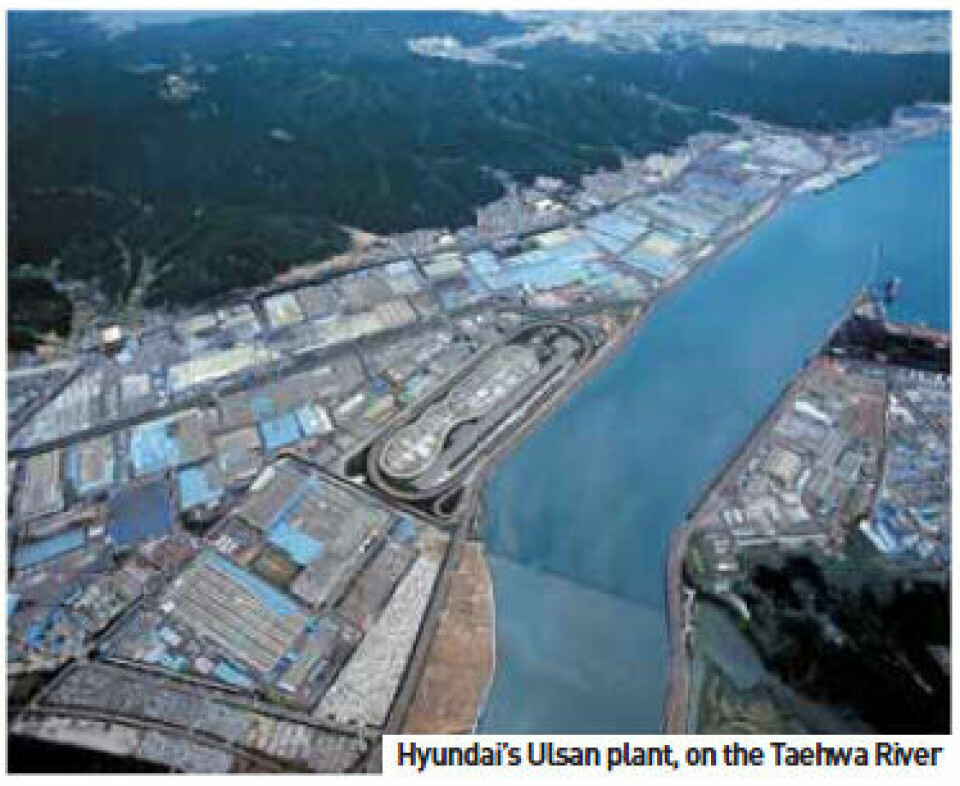
The company has suffered many crippling strikes in recent years and seems determined to head off future industrial disputes by taking the initiative of setting out a timeline for the end of overnight manufacturing. It is perhaps no coincidence that the recently-appointed leader of the main HMC union is set against such shifts. HMC and the union have committed themselves to talks on finding ways to make up the expected loss in production from 2013.
Kia Motors
The country’s second-biggest carmaker has also been talking production numbers, but in this case it is looking at expanding an existing plant. In December last year, the Seoul-based firm told the media and union leaders that it intends to raise the capacity of its Kwangju factory, located in south-eastern Korea, by 25% over 2012. This is largely in response to growing US sales of the Sportage SUV and Soul crossover.
Pending union agreement, Kia intends to invest KRW150bn ($133m) to increase annual capacity at Kwangju to 620,000 vehicles from the current 500,000 units. The company is concerned that unless it acts soon, it will not be able to take advantage of the steady recovery currently underway in the United States. Kwangju, one of four domestic plants, makes up around 18% of Kia’s global passenger vehicle manufacturing capacity. As this issue of AMS went to press, Kia had yet to release total 2011 sales figures, but through November the company saw a 19% year-on-year (YoY) rise in global sales. This is slightly more than 2.26m passenger cars, recreational and commercial vehicles. The increases were due in large part to double-digit YoY sales increases in Europe, North America and China. In Korea, and following on from a particularly strong 2010, the company recorded only a 2% YoY increase (to just under 450,000 vehicles). North America remains the company’s top market, followed by Europe and China, each of which saw sales above 400,000 vehicles in the Jan-Nov period.
GM Korea
This division of GM stated in early 2010 that it intended to invest the equivalent of $5 billion in new products and plant upgrades. Nearly a year later, that process is well underway. The first results can be seen in the form of the new Chevrolet Malibu saloon, which was launched in Korea in November 2011. The car will be marketed in 100 countries, compared to only 20 for the previous US-built model. The fi rst Chevrolet Malibu off the line in October 2010 at GM Korea’s Bupyeong plant. GM Korea’s Bupyeong plant is the first global facility to build the eighth-generation of the Malibu. US production commences later in Q1 2012, with a Chinese build to follow. Bupyeong makes both left- and right-hand drive cars, including a Holden-badged variant for New Zealand and Australia on the way.
What is now GM Korea will celebrate its tenth birthday as a division of General Motors later this year; the US company purchased the bankrupt Daewoo Motor in 2002. The renaming of GM DAT coincided with the introduction of the Chevrolet brand to Korea in 2010, as General Motors elected to axe the Daewoo name in favour of Chevrolet after research showed that younger buyers preferred foreignsounding brands. Since then, as more Chevrolet models have been launched or simply rebadged, sales and market share have risen to the point where GM Korea is now a serious challenger to Renault Samsung as the third largest local brand.

GM currently has 2,500 engineers at its Korean operations, with small car development a particular expertise. The ‘Gamma 2’ architecture that underpins the Chevrolet Spark was developed in Korea, while local engineers also took the lead on the platform development projects for the Chevrolet Cruze saloon and Orlando minivan. The firm works closely with other GM engineering centres in Melbourne, Michigan, Shanghai and Germany.
Four manufacturing plants turn out passenger vehicles and micro-vans, as well as gearboxes and petrol and diesel engines. According to GM Korea, three of these are at full capacity, with only the main Bupyeong plant having spare capacity. The division’s most recent total annual production is 900,000 vehicles a year, plus 1.5m engines and 1.4m transmissions. The majority of the company’s production is in the form of kits, which it ships to GM plants in various countries.
Next to come from GM’s Korean operations will be a third bodystyle for the Cruze. This small wagon is due to enter production at the Gunsan plant later in 2012, reportedly timed to coincide with a mid-life facelift for the existing saloon and hatchback. Then, following its expected global debut at the Paris motor show in September, a small Chevrolet crossover is scheduled to be built at Bupyeong alongside the Aveo/Sonic with which it will share a platform.
Renault Samsung Motors
Busan, a city in the south-eastern corner of Korea, is the location for the sole vehicle production plant of Renault Samsung Motors. The French parent company kept the Samsung brand name going after it agreed to purchase some of the assets of the bankrupt Samsung Motors in 2000, giving it a 70% stake (since raised to 80.1%) in the new firm. The company had been created by the Samsung Group in 1994 on the basis of a co-operation agreement with Nissan Motor, which largely consisted of building the Nissan Maxima saloon under license, which became the firstgeneration Samsung SM5.
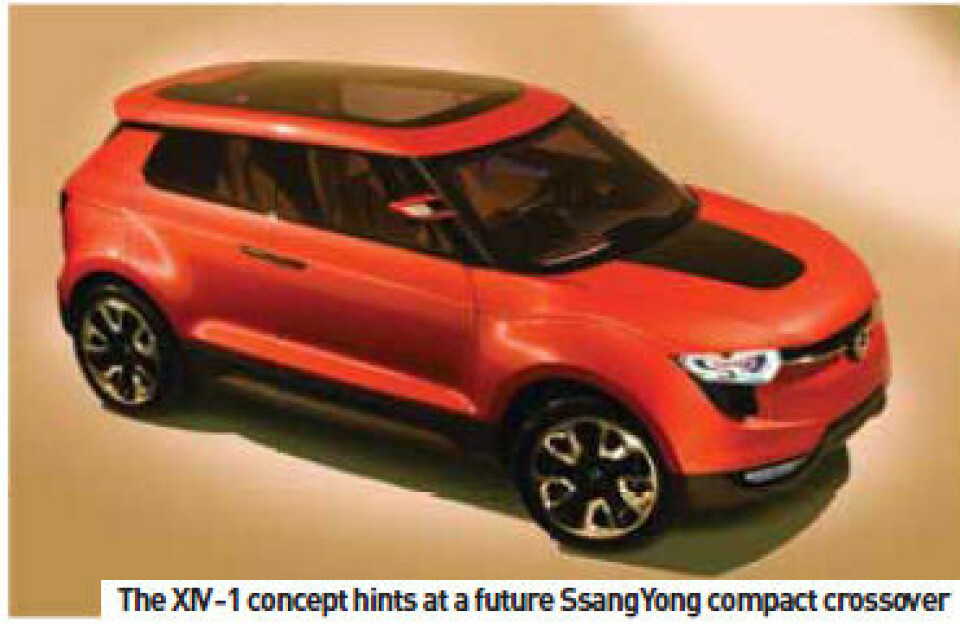
The Busan plant was famously troubled in its early years. Structural problems related to the plant having been constructed on a reconstituted plot of land located in the estuary of the Nakdong river left it sinking, albeit slowly - but sinking nonetheless. Much time and money has been invested on fixing the problems at Busan but the vast complex, which was built to deliver a hugely ambituous 500,000 cars per year, remains underutilised. This, despite the fact that Busan has tripled its output to 300,000 cars a year under Renault management. As an aside, when RSM was created in 2000, Samsung was only building 12,000 cars per year, which meant racking up enormous losses. Another RSM site is the Kihueng Renault Samsung Technical Center (RSTC), located near Seoul. At this engineering hub, prototypes undergo development while specialised test facilities (chassis, powertrain, emissions control, electronics, safety, etc.) also employ teams of Korean, Japanese and French engineers.
The most recently built RSM facility is the Design Center, located in Kihueng. This fully-integrated part of the Renault Design global network is referred to by the parent company as a design bridgehead for the Renault Group in Asia. The centre’s first and most visible product was the eMX Concept, which premiered at the 2009 Seoul motor show.
SsangYong Motor
Now controlled by India’s Mahindra & Mahindra, SsangYong Motor is steadily recovering from its economic collapse under former owner SAIC. The firm recently stated that it aims to lift its sales and revenues by one third between late 2011 and the end of 2013. To reach this target it plans to add new models, replacing outdated products, and return to overseas markets that were abandoned while it was in receivership.

SsangYong has one main plant, Pyongtaek, which builds its SUVs, crossovers, pick-ups, both of its luxury sedans and the Stavic/Rodius minivan. Pyongtaek has a stated annual capacity of 220,000 vehicles. For calendar 2011, the company was on course to build 121,000 vehicles; a figure of 160,000 units is targeted for 2013. As for revenues, the 2011 target of KRW3 trillion looked like being attained as the year ended, with a rise to KRW4tr set for calendar 2013. The firm also intends to launch four new vehicles by the end of 2016. The Pyongtaek site consists of the manufacturing plant and head office, as well as an R&D centre and a shipping office. The facilities extend over an area of 992,000m². A larger complex, Changwon Powertrain, covers 1,010,000m² and consists of two factories. Here, SsangYong builds 2.0- and 2.7-litre diesel engines, along with petrol units (2,300cc, 2,800cc, 3,200cc and 3,600cc) and various components for the four-wheel drive systems used in its core SUV model ranges.
Increasingly, SsangYong will be twinning its future model programmes with those of its parent company. One of the first is expected to be a production version of the XIV-1 concept, which had its global debut at the Frankfurt motor show in September 2011. This proposed model (‘Korando B’) would slot in below the existing Korando C (Korando in some markets) as a rival for the forthcoming small SUV which Chevrolet is due to launch in late 2012. The Mahindra-badged equivalent is said to be codenamed S101.
Expanding union power
The Pyongtaek plant of SsangYong Motor hit the headlines back in 2009 when a sit-in strike by workers turned violent. But this dispute was far from being an isolated event. Almost every Korean manufacturer has faced lengthy industrial action in recent years and the Korean Metal Workers’ Union (KMWU) remains a powerful force.
The KMWU’s most recent victory was having some 2,000 production workers and 500 white collar and maintenance workers at Renault Samsung’s Busan plant join its ranks. The union has claimed that with Renault having invested heavily to triple annual production to the present 300,000 cars, workers have faced intense pressure to raise their productivity levels.
The union’s local at RSM’s Busan plant has recently pressed for and obtained unilateral agreements on annual wage increases and goals concerning units-per-hour and hoursper- vehicle. The local, however, also insists that wage increases have not matched those at other auto assembly companies, setting the scene for another showdown later in 2012. Following the KMWU’s successful organizing of RSM’s Busan workers in August 2011, each of Korea’s vehicle manufacturers - Hyundai, Kia, GM Korea, SsangYong, Tata- Daewoo and Renault Samsung - is now affiliated to the KMWU.
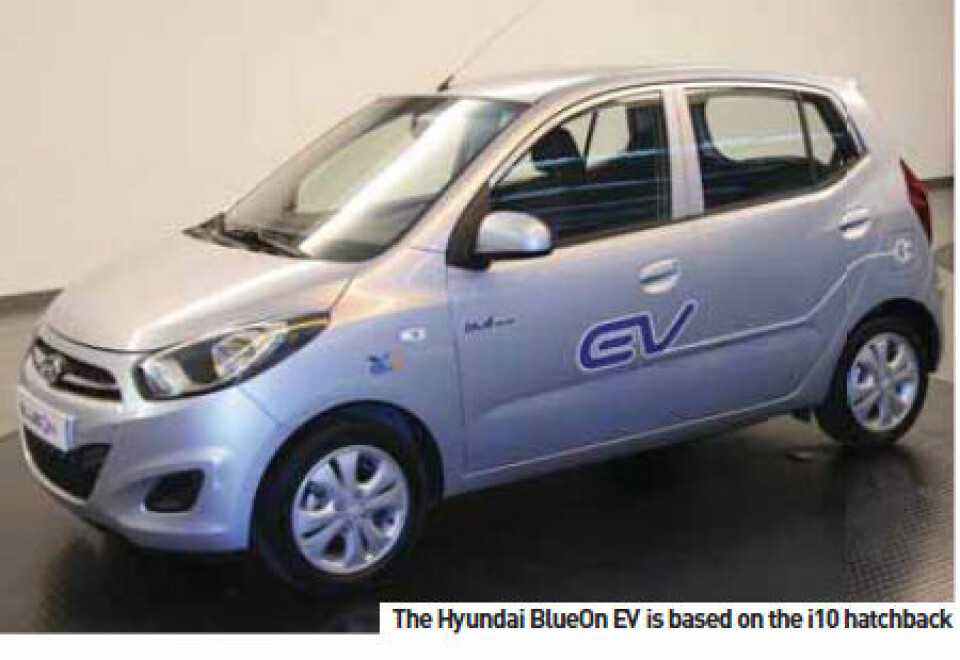
Tear gas and riot police
Industrial disputes at Korean vehicle manufacturing plants are by no means unusual but such disruptions have taken a new turn, with the government sending in riot police in cases where management and union talks have ended in stand-offs. One such example was the raid in May last year of a factory owned by powertrain component supplier Yoosung Enterprise following a prolonged illegal strike. Some 3,000 specially trained police officers were sent into the plant, which is located 90km southwest of Seoul. The facility, which makes piston rings, is a vital link in the supply chain of Hyundai and Kia and had been the cause of production stoppages for both manufacturers, which they stated had cost them in excess of KRW2 trillion. As Yoosung controls 80% of the country’s piston ring market, even after the strike had been going only a few days, production of Hyundai and Kia diesel-engined models began to be affected. Not only is Yoosung the source of approximately 70% of the piston rings used in Hyundai and Kia vehicles, the company also supplies the same components to GM Korea and SsangYong Motor, as well as camshafts to Renault Samsung.

The police raids came after the Korea Automobile Manufacturers’ Association called for rapid government action, stating that a prolonged walkout would seriously damage the global competitiveness of the country’s carmakers
Korean EV production nears 1m units per annum
In August 2011, a consortium made up of Korea’s main manufacturers signed a framework agreement with the national government’s Ministry of Knowledge and Economy to commence large-scale production of electric vehicles by 2014. Previously, the firms had been working to a deadline of 2017, but extra funding from the Seoul government provided a new incentive to bring forward the ambitious plans.
Hyundai Motor leads the group of 43 firms, the combined aim of which is to pool resources in the fields of motor and battery manufacturing, together with power converters and the building of a series of recharging stations. The large suppliers in the project include Hyundai Mobis, LG Chem and SK Innovation, while C&S Technology and Wise Automotive are from the list of Tier 2 companies involved with the project. Tertiary education facilities such as the Korea Electronics Technology Institute, Seoul National University, KAIST and Sungkyunkwan University are also represented.
The Government in Seoul has established the new agreement as part of its large-scale funding for various projects under a so-called ‘Green Car’ investment project. As well as directing the efforts of manufacturers towards making more plug-in vehicles, the ministry says its main aim is to encourage R&D activities that seek to improve the performance and affordability of locally-built EVs. The government says it would like to see one million electric vehicles being manufactured in Korea every year from 2010, of which 700,000 would be exported. That’s an ambitious goal, especially in the context of where the country’s OEMs are right now. In short, only Renault Samsung has set out plans for double-digit production, though both Hyundai and Kia are working on plans for mass production of plug-in cars.
Hyundai ramping up EV bid Korea’s first EV to enter series production, albeit on a small scale, is the Hyundai BlueOn. The company revealed what it termed a production-ready, zero emissions vehicle, the i10 Electric, at the Frankfurt motor show in September 2009. This battery-powered version of the i10 city car was then unveiled in production form exactly one year later as the Hyundai BlueOn.
Powered by a 49kW motor and a 16kWh (SK Innovationsupplied) battery, the BlueOn promises a driving range of 100 miles (160km). The vehicle accommodates dual recharging cycles: a 220V household current which is slower but potentially advantageous if recharging is done during off-peak hours when utility rates are lower; and a 380V industrial-strength current which promises quicker recharging speeds. According to Hyundai, under the quick cycle, the battery can be recharged to within 80% of its capacity in just 25 minutes. Under the normal cycle using a 220V household current a 100% charge can be reached within six hours.
Hyundai has already supplied an initial 30 cars to government agencies with 2,500 planned to be built by the end of 2012. Kia, meanwhile, is yet to fully reveal its own plans for production of EVs, although a plug-in version of the Ray minicar, which it launched in South Korea in December, is said to be under development.
Meanwhile, Renault Samsung might well have stolen a jump over its larger rivals by tapping into the Renault-Nissan Alliance’s EV expertise. A prototype of an EV version of the existing Samsung SM3 saloon was revealed by RSM in November 2010. As is the case with the related Renault Fluence Z.E., the battery pack is installed directly behind the rear seats rather than beneath the car’s floor, extending the rear of the electric model by 13cm. The company claims limited production is due to commence during 2012.
Of particular interest with the SM3 EV is that the vehicle features a quick-drop (250kg lithiumion) battery pack. The cell-switching concept has been chosen for the production model to ease concerns about charge times, according to RSM. The company claims that a robotised battery switch typically takes 90 seconds at specially designed switching stations. The SM3 EV is claimed to have a range of up to 160km (100 miles). In November 2011, RSM stated that its target for calendar 2012 production of the SM3 EV is 250 cars, with up to 13,000 to be built by 2015.