Flexible friend at Magna Steyr
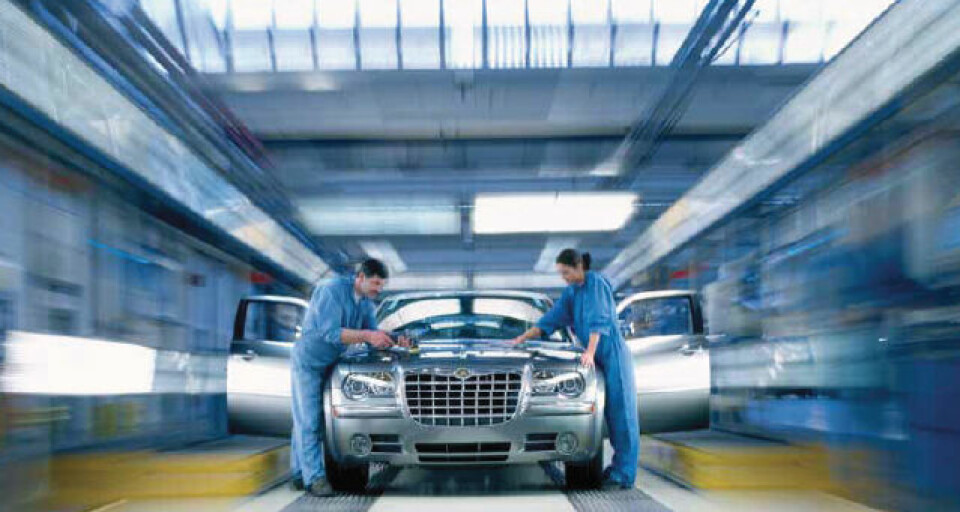
What is it about Magna Steyr that convinces OEMs to come to you to build their cars? Gerhard Stiegler, Vice-President of Operations does not hesitate with his answer. “Our flexibility, our range of services and our quality.”
It is a winning combination that has, since 1979, brought a steady stream of carmakers to Magna Steyr’s facility in Graz, Austria, looking for a partner capable of producing their vehicles. It was then that the company started production of the Mercedes G-Class, which in different guises has been a farm workhorse, army transport and luxury SUV. “The G-Class is a unique vehicle,” says Stiegler. “If it was designed today, it wouldn’t go into production, it is overengineered. One key difference from the G-Class and its competition is that it has a framed door, where most have an open closure, which is very difficult to get right.” While the G-Class remains, other products are destined to be leaving the Magna Steyr fold, but that capacity will be quickly taken up by new contracts, namely from Aston Martin (Rapide four-door saloon, late 2009), Peugeot (308 Coupe, 2010), BMW (MINI SAV, 2010) and Porsche (Boxster, Cayman, 2012). “The biggest thing on the horizon is the MINI SAV, the all-wheel and two-wheel drive versions, for two reasons. It is by far the highest volume model coming online, and secondly, it is a turnkey contract, we have full responsibility. Even if MINI themselves supply development work, as they do in their core competencies, design, handling, etc., they will do so on a contract basis. They are responsible for the results, but we have to give them a formal order; we give them the input and then we receive the output, which will be then integrated into our turnkey project.
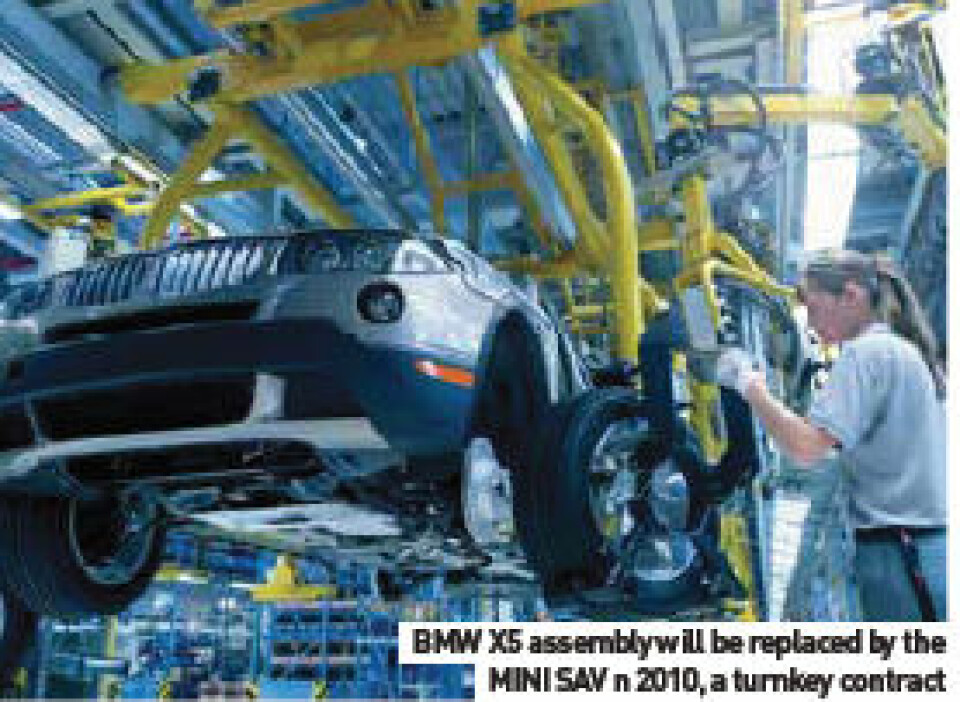
“MINI Plant Oxford is more or less full,” continues Stiegler. “They are approaching the plant’s maximum capacity of 260,000 units per year (237,700 units in 2007) and require the additional headroom to service the three current models. It is because of this that they were looking for an alternative and due to our long-term relationship with BMW and the success of the X3, another turnkey project, it was a natural choice. From an engineering, planning and manufacturing perspective, this is our biggest project. For us, the MINI is the successor of the X3. “We will use exactly the same line as the X3 to produce the MINI, which features Kuka robots and various Nothelfer equipment (on the BIW line, from the ThyssenKrupp group). The paintshop and final assembly line (trim, chassis, final) was supplied by Dürr. All of our equipment is supported by our in-house team.”
Lowering plant emissions
Magna Steyr is currently in the final phases of lowering plant emissions. “The plant is located in a largely residential area, and we’d had some complaints about emissions from the paintshop,” explains Stiegler. “We’ve addressed this and now the shop includes the latest technologies. It is completely closed, with all runoff and residues collected and treated in-house.”
With Magna Steyr losing X3 production to BMW’s Spartanburg, South Carolina facility, has the company considered building cars in the US, to take advantage of currency exchange rates? “There have been discussions on opening a manufacturing plant in the US, but not specifically to take advantage of the dollar,” says Stiegler. The overall scale of any new operation would be too large to be directly influenced by any currency fluctuations. The key advantage would be in supply, having US-specific models run off the line in-country, without the associated transport costs. “That’s not to say we don’t have any facilities in the US. We have a paintshop, outfitted by Haden Prism, which we took over when they went out of business, where we are currently painting panels and other parts for the Jeep Wrangler.”
The appeal of Magna Steyr is self-evident in the range of expertise the company brings to the table. “Companies come to us because we have experience in all areas of car production,” says Stiegler. “Concept, design, serial development, serial planning, launch, serial production, spare parts, we have covered each area for a number of different manufacturers and for a variety of model types.” In 2005, Magna International (parent company of Magna Steyr) purchased CTS Fahrzeug-Dachsysteme GmbH for €170m ($250m). Originally founded in 1996 in a joint venture between Porsche and Daimler-Benz, the company proved to be a key purchase, both in the fact that it was already supplying Magna Steyr with roofs for the Saab 9-3 Convertible, and opening up new avenues of business, namely production of the Porsche Boxster. Additionally, according to Stiegler, flexibility in production was a key consideration in Magna Steyr winning the Boxster and Cayman contract: “The line can scale production up or down in order to meet customer demand above and beyond production of the models at Zuffenhausen. Even before the purchase of CTS, Magna was already supplying convertible roofs (as well as some body panels) for the Boxster convertible.”
While Magna Steyr has recently finalized multiple new contracts, the rumour that KTM had chosen the company to produce the new X-Bow model is categorically false. “There is no KTM deal,” clarifies Stiegler. “They have decided to do it by themselves, in Graz. That said, we are still proud of the X-Bow, 80 per cent of the people building the car are coming out of this plant. “We have cooperation with the company, they outsource activities on a contract basis, and we take care of those activities. Examples are in purchasing, where they can take advantage of our purchasing power and the people we have here at the plant. There’s also a personal relationship, we talk from time to time, offering advice.”
Matching market conditions
The company, though, is undergoing a fundamental shift in response to market fluctuations. “We are currently downscaling,” says Stiegler. “In 2006, we produced a record number of units, about 250,000. In 2009, we expect to produce 150,000. This is a direct response to the market, as both BMW and Chrysler reduce volumes.” That said, the plant, which currently operates on two shifts, five days a week, is due to add a third shift by the third quarter this year.
Until the new models enter serial production, the Graz facility, which covers approximately 840,000m2 (0.84km2, 200 acres), continues to produce the aforementioned G-Class, Saab 9-3 Convertible and BMW X3, as well as a selection of Chrysler products destined for the European market.
The Chrysler assembly line
Magna Steyr has had an extended relationship with Chrysler. The Eurostar plant, so-named due to the ‘star’ logo of Chrysler and the plant’s location in Europe, was home to the then DaimlerChrysler assembly line building the PT Cruiser and Voyager MINI van. Purchased by Magna Steyr in 2002, the plant was completely refurbished in 2005 and has since been the home of the BMW X3, and will produce the MINI SAV after 2010. Helmut Wagner is Operations Leader for Jeep and Chrysler at Graz. “Here we build the Jeep Grand Cherokee and Commander SUVs, and the 300C (formerly 300M) saloon and estate models, the latter with both two- and four-wheel drive drivetrains.
“Takt times vary along the line, so we try to find the optimal mix. For example, if a Commander takes more time for an operation to be completed, we will try and load a following vehicle with less content. We try to balance the number of worker operations over an hour. But there is no blocking on the line; we have the ability to build any number of models in any combination.” The assembly line is broken into four different sections, Chassis 1, Trim 1, Chassis 2 and Trim 2. Parts are delivered JIT or JIS, as required. “We get a lot of parts delivered from the US, including most major body components, all arriving in cardboard boxes,” says Wagner. “In terms of the environment, these boxes are shredded by us and that material is then shipped out to third-party businesses for reuse. In regards to overall inventory, we have an average of two and a half days of stock for any given part, perhaps slightly more for some items.”
On Chassis 1, the carriers have been adapted to be able to carry any chassis, with just a quick alteration to the colour-coded support assembly. Once the body is loaded, the first order of business is attaching the wiring harnesses and removing the doors. These are transported to a kitting area via a dual (left- and right-side) conveyor system and brought back to the line just in sequence. “Parts are separated lineside into colour-coded bins. Some are delivered just-in-time, others are delivered boxed. To simplify operations, we keep as much as possible common between models and variants.”
“We have electrically-controlled tools for safety-critical torquing operations,” continues Wagner. “These are monitored for process completion, with each operation logged in the production control database. Combined with this, we have a labelling system that features part and product numbers. All parts and products are scanned, and then matched with the vehicle chassis.”
Glass application
One of the final operations on Chassis 1 is glass application. Lifting at the windscreen station is done automatically, with Kleinmichel robots applying the exact amount of adhesive as necessary. “We use Betaseal adhesive, brought in from the US. This was specified by Chrysler. The machine is set to initiate a self-cleaning function for the applicator nozzle after a preset number of operations, maintaining accurate applications and flow rates. Once prepared, the glass is manually installed using articulated arm lifters from Siemens. We chose to do a manual installation as it is a critical operation, plus there are too many glass elements (by model mix) to do automatically.”
According to Wagner, Chrysler specify vehicle parts and assembly processes, while Magna Steyr specify the equipment needed to fulfil the required processes. Once glass is installed, the chassis is raised approximately 3 metres by a Traglast lift onto an electrified monorail sourced from Siemens, where it joins the Trim 1 line. A key difference between the two line sections are the heightadjustable chassis carriers of Trim 1. Developed by DeMag, these allow each individual chassis to be raised or lowered between stations featuring lifters and robots by Nothelfer and Siemens. “The carriers are self-powered,” says Wagner. “Raising or lowering allows us to present the chassis at the most ergonomically-correct height. We switched from a chain-driven system to improve flexibility along the line. If an operation is finished early, the individual can choose to signal that the operation is completed, allowing the carrier to start any height change early for the next station. “The carriers offer great flexibility, but we had to learn how to use that, how they could be optimized. Within each station, the carriers are set to an average height, allowing all individuals to work comfortably on the vehicle, compensating for the various heights of the assigned workers. If a new worker is added, a new optimal height is calculated. It doesn’t make sense for the carrier to be moving up and down randomly within each station – aside from it being quite dangerous.”
In Chassis 2, the chassis is married to the powertrain assembly, comprising the front axle, powertrain (including engine dressing) and rear axle assemblies. “The rear axles are very different between models,” says Wagner, “they require a different process for each model. For example, in the case of the 300C, the rear axle assembly includes an independent rear axle, while for the Jeep models this is of a fixed type. All line personnel are required to know processes for all three models and all variants within that range.”
Concept cars can be said to serve two general purposes; to gauge the reception of a design before the decision is made to put it into production and to showcase the design cues and technology future models might incorporate. Much like the second group, concept vehicles produced by Magna Steyr are unlikely to ever go into production. Instead, they serve to demonstrate the company’s ideas, offering elegant – yet practical – solutions to perceived problems in current car design or construction. In 2005, Magna Steyr revealed the MILA Concept (Magna Innovation Lightweight Auto). Powered by compressed natural gas (CNG), the single- seat model featured a 1.6-litre four-cylinder engine, standard apart from the addition of CNG-specifi c injection valves. CNG was adopted to fuel the MILA due to its higher anti-knock qualities over standard LPG systems (butane or propane).
What is more, with a higher effi ciency than petrol-powered alternatives (up to 32 per cent over 25 per cent) and zero particulate emissions, the MILA qualifi ed for the Californian AT-PZEV or Advanced Technology Partial Zero Emission Vehicle Category Based on a rigid monocoque chassis, the 150bhp car could also perform, returning a 0 to 100km/h time of 6.9 seconds, and a top speed of over 200km/h. With a 76-litre capacity fuel tank, made from an aluminium liner wrapped in carbon fi bre, the MILA had a range of approximately 200km, making it a viable alternative for everyday transport. Magna Steyr followed the MILA Concept in 2007 with the MILA Future, a two-seat static concept designed to showcase the company’s convertible roof expertise. The car featured a twopart retractable hardtop that could be set to any of four different confi gurations; coupe, landaulet (with the rear window fully opened), roadster, and the so-called ‘copster’, a combination coupe and roadster. Based around a hydraulically-operated pivot hinge, the roof design was widely hailed as one of the best solutions to date for hardtop convertibles.
Most recently, Magna Steyr unveiled the MILA Alpin off-roader at the 2008 Geneva Motor Show, featuring a hybrid CNG-powered engine designed in-house that produces only 100g/km of CO2. Whether the vehicle was deliberately designed as a homage to the Hafl inger, manufactured by the company between 1959 and 1974, we will probably never know, but based on a modular chassis and able to climb 45° slopes, the technologies featured in the Alpin once again served to demonstrate the expertise of Magna Steyr’s engineers.
Experienced production line teams
Wagner goes on to explain that stations along the production line are manned by teams of two or three individuals, each with one leading person from the related area, trim or chassis, a highly-experienced individual who has undergone extensive training. New line workers are assigned to these teams to learn station processes. The final area of the production line is Trim 2, with operations such as interior fitting, filling operations and seat installation. “The seats are delivered lineside just-insequence, which is especially important as they are specific to each model variant. Of the three models, the Commander requires marginally more time, as it is a seven-seat model.” This is also where the dressed doors are brought back to the line for fitting, using manipulators, and the vehicle is prepared for final ups and testing.
A feature of Trim 2 is the lineside pre-heaters for plastic trim items, including wheel arches, to be added to higherspecification model versions. “Keeping the trim pieces at a raised temperature allows them to be almost custom-fitted to the car body. Heating them also helps to create a stronger bond.”
The second-largest university in Styria, Austria, Graz University of Technology was founded in 1811 by Archduke Johann. A public university, it offers approximately 9,000 places in a variety of fi elds, but most notable (in the case of Magna Steyr) are the Faculties of Mechanical Engineering and Electrical Engineering. “The university produces candidates of superior quality and we actively look to employ graduates in related fi elds,” says Gerhard Stiegler, Vice-President of Operations. “Having the university so close to us is a benefi t, in terms of the quality of graduates and the fact that the students are familiar with Graz and want to remain in the area after graduation. That said, these graduates are widely sought after by other companies in Austria, Germany and throughout Europe, which makes it diffi cult to secure the numbers we would like.” With a number of famous graduates, including Nikola Tesla, electrical engineer and inventor of the alternating current (AC) electrical supply system that is common throughout the world, Graz University of Technology is a coincidental, yet welcome, supplier of engineers at Magna Steyr’s Graz facility.
Covering all the bases
In addition to vehicle production, Magna Steyr offers impressive turnaround times for vehicle development. “We took the Audi TT from coupe to roadster in 15 months,” says Bernd Oberzaucher, Public Relations Manager for Vehicles and Powertrain. “Magna also designed the Fiat Stilo, taking a wholly new car from drawing board to production in the same time period.”
Magna offers its customers unrivalled flexibility when producing vehicles ‘on demand’. “The (Mercedes) M-Class production was a case of product peak shaving. Assembled on the same line as the Jeep Grand Cherokee, we provided 20,000 units per year for three years to service anticipated customer demand above planned capacity. Magna Steyr can offer flexible capacity with low-volume production, which also serves to introduce us to OEMs unfamiliar with the company.” Before the Voyager, 300C and Commander, The M-Class/ Grand Cherokee production was the first merger project for Daimler and Chrysler, realized by Magna Steyr’s Stiegler, Gerhard Wolf from Mercedes-Benz and Gary Cash from Chrysler.
In addition to vehicle design and production, Magna Steyr has developed complete systems for a range of global companies, including Bosch, Denso and Delphi. Says Oberzaucher: “There are only two items we have never developed; glass and tyres. This is because the marketplaces for these two products are already filled beyond capacity, and we don’t feel it necessary to be a small, introductory player in a large market.” Shared technology is another side to Magna Steyr. “We developed feed lines (fuel lines) for the Ariane rockets. The same technology is used in the hydrogen fuel system onboard the BMW H7. The car also features our liquid hydrogen storage system, maintaining the fuel at a constant –253°C.
“Under development now we have a system named ‘Intelligent Safety’, where cars colliding head-on are directed off to the side of each other rather then being subjected to a full frontal impact.” Why, when it clearly could, doesn’t Magna Steyr produce its own vehicles?
“There are two reasons we don’t make our own cars,” says Oberzaucher. “One is that we don’t have a distribution network. We wouldn’t want to sell vehicles through other manufacturers’ outlets and it is very expensive to set up and support your own dealer network. Another is that almost any new car that we sent to market would put us in direct competition with our current customers. We cannot put the relationships we have with our customers at risk by putting a competitor on the road.”