Energy revolution
As a result of shrinking markets, automotive manufacturers are looking at new, innovative techniques to reduce production costs. As part of this drive, attention has been focused on new ways of developing and supplying the energy needed to power production plants, while also reducing carbon emissions. Such investigations have brought forward some revolutionary technologies that could mark the start of a fundamental change in the way plant energy is both generated and used.
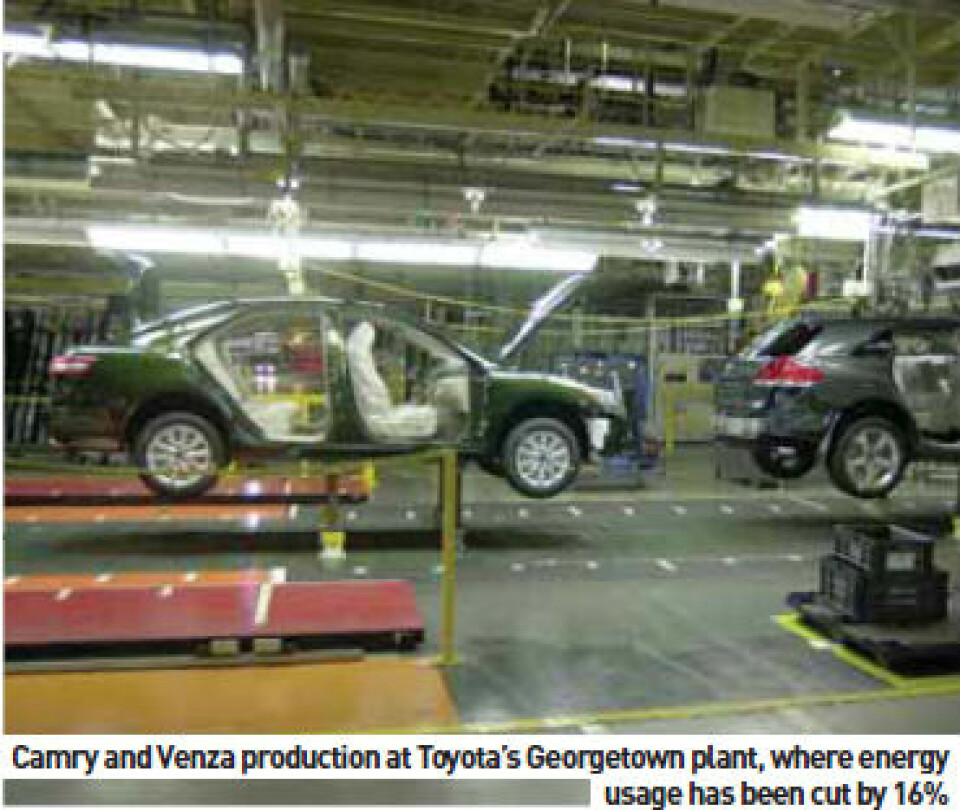
Toyota, now firmly fixed in the minds of most consumers as a ‘green’ company thanks to the publicity generated by its Prius hybrid, is one of the leading players when it comes to developing alternative energy sources for vehicle production plants. In addition to the company’s showcase plant in Japan that assembles the Prius, the company’s 30 North American manufacturing, design and logistics facilities are gearing up to meet the ambitious targets outlined in the firm’s latest five-year Environmental Action Plan (EAP).
Toyota’s North American manufacturing facilities consume in excess of $147m of energy annually, resulting in 1.1 million tonnes of CO2 emissions. Thanks to a programme that constantly looks for new ways to reduce energy costs and lower greenhouse gas emissions, the company was recently able to report that improvements in energy usage at its US plants have now reduced CO2 output by 150,000 tonnes (base year FY2002), resulting in annual savings of $18m.
Taking the just-in-time concept used in parts delivery and applying it to energy consumption has reaped huge rewards for Toyota, the philosophy having been modified to mean using energy only when it is needed. For example, as the US economy nose-dived in late 2008 and into 2009, Toyota took the decision to idle production lines at some plants but at the same time, took the opportunity to identify and implement fixed energy reductions. As production levels began to rise again from late 2009, the cost savings began to add up. Even the smallest examples of implementing several kaizens have been able to show impressive results for Toyota. At its facility in Long Beach, California, lowering temperatures and reducing the speed of the conveyor used in the electro-deposition curing process cut natural gas consumption by 12.5%. At the same facility, reducing the amount of time between equipment start-up and the commencement of production has saved over 1,600 therms a year. Cutting the number of agitators used as part of the coating process has also resulted in considerable savings – over 172,000 kilowatt hours (kWh).
Savings on a larger scale have also been achieved at ,Toyota’s Georgetown, Kentucky plant, home to production of the Camry, Avalon and Venza models. The company decided to run a competition in order to incentivise the workforce into finding ways of lowering power generation costs. While the overall winner was the plastics shop, absolute energy consumption for the entire plant over a defined period was cut by 16% year-on-year.
Activities that contributed to the cost and emissions savings at Georgetown were in some cases as simple as fans and lights being turned off when not needed. Other examples included converting high-pressure sodium lighting for car parks, roadways and footpaths to more compact fluorescents – this process alone reduced energy consumption by more than 711,000 kWh, with an annual CO2 reduction of 10,200 tonnes. Lastly, a heat recovery system in one of the paint shops now feeds steam back into the main plant steam system, a move that allows the main boilers to be shut off between the first and second shift changeovers.
Toyota’s powertrain facility at Huntsville, Alabama, the first plant in the company to install a photovoltaic system, is scheduled to receive yet more panels to increase potential energy generation. A 5kW solar panel already produces enough energy to light four bays (over 16,000 sq ft) of floor space, equivalent to eighty 60-watt light bulbs, the company claims.
A parts centre in Ontario is also contributing to energy savings for Toyota’s North American operations via the harvesting of solar energy. Its 2.3MW system is now said to be the second-largest rooftop array on the continent. When fully operational, it is expected to produce more than 3.7m kWh annually, providing 58% of the plant’s electricity requirements. The system of 10,400 panels covers a surface area of 242,000 sq ft.
Honda’s ‘Green Factory’ Initiative
Honda, Toyota’s main rival in the production of hybrid cars, has also been an innovator in terms of lowering energy usage and emissions at its plants. Each year sees the firm publish a set of fresh goals and, just as importantly, previous results, as part of its ongoing ‘Green Factory’ initiative. The Green Factory programme is divided into two elements: the conservation of energy and the quest for zero emissions. Each of these is in turn broken down by three components: new energy sources and resource (water) conservation; plus water reduction (by-products), reduced CO2 and SOC emissions and mitigation of air and water pollution.

For fiscal year 2009, the company set as a target an ambitious 27% cut in energy usage for its five main Japanese plants (Saitama, Tochigi, Hamamatsu, Suzuka and Kumamoto), which was almost attained (26.2%) using 1991 levels as the baseline. Combined introduced energy totalled 10,000TJ, while solar power generation levels reached 250MWh during the same period.
Carbon dioxide emissions attributable to energy used in vehicle production by the five Honda plants totalled 427,000 tons in fiscal 2009, against a target of 494,000 tons. Whilst admitting that the reduction was partly due to decreased production related to the global recession, various other factors came into play, including the introduction of highefficiency compressors and the installation of solar panels on factory roofs to provide power for air conditioning. Also in FY2009, a new 12kW power generation system at the Tochigi facility came on stream, producing 66m kWh of electricity using both solar energy and natural gas co-generation, together with other alternative energy sources. Honda states that its total amount of power produced by alternative means reached approximately 9% of requirements – unchanged from FY 2008.
Hyundai Total Energy Management System
While many OEMs have suffered dramatic declines in sales over the past year, Hyundai was conspicuous for the gains made at the expense of its Asian rivals. Its focus on wringing ever-lower production costs from its factories moved up a gear last year too, as it sought to follow the global leaders by adhering to its own Total Energy Management System (TEMS).
TEMS was set up to oversee usage and cost of electricity, LNG and other energy sources for Hyundai’s Korean plants. So far it has been rolled out at the Asan and Jeonju facilities, with particular emphasis on painting, forging and moulding activities – the three largest users of electricity in the carmaking process.
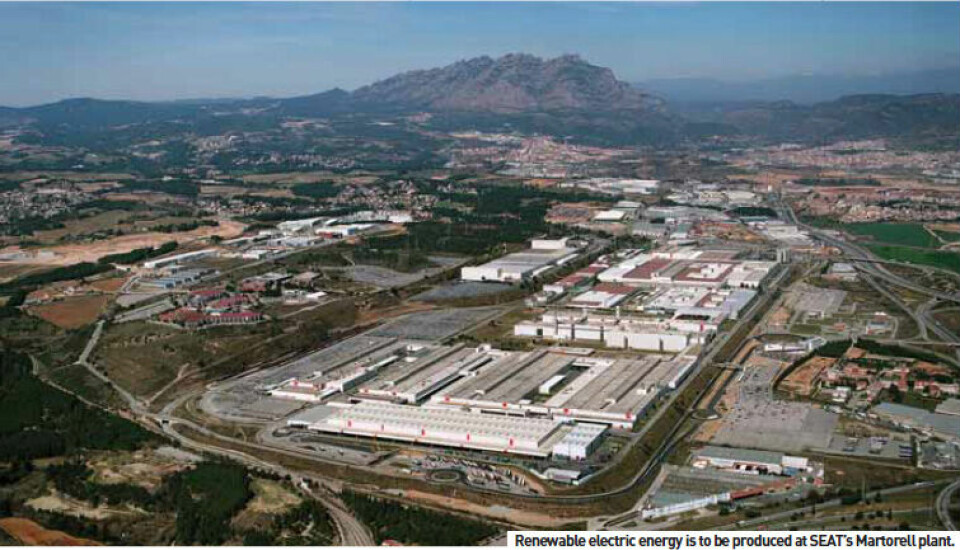
Hyundai now employs heat recovery devices at the two plants monitored by TEMS. These have been installed to collect high temperature waste heat generated during the painting process to produce steam. The installation has, the company claims, slashed energy usage for steam production by 50%.
Smelting activities have also benefited under the energy management programme. For the furnaces at material plants, Hyundai switched from parallel resonance to serial resonance in order to increase energy efficiency. A system that recycles waste heat from cooling towers for use in manufacturing processes and for heating has also been installed. As the first such system to be put in place at a Korean vehicle plant, it has reduced CO2 emissions by a claimed 4,000 tons per annum.
Hyundai has found further savings from lighting at its TEMS plants. Metal lamps (430 watt hours) have now been replaced by electrode-less lamps (150Wh) and highefficiency fluorescent lighting (54Wh bulbs), further cutting annual CO2 emissions by a stated 6,000 tons. Specifically at Asan, Hyundai has changed the electro-coat paint to adjust the rectifier voltage, while the installation of a crusher in the furnace at the material factory has shortened smelting times.
Hyundai says its overall goal is to maintain a balance between the input and output of its vehicle production activities. In 2008, the most recent year for which figures are available, the input at Hyundai business sites in Korea totalled 298,000 tons of raw materials, 30.4m GJ in energy consumption, 12.5m tons of water and 2,250 tons of chemical substances. Output included 1,700m finished vehicles, as well as 2,100m engines. Resultant by-products were 1,500m CO2-equivalent tons of greenhouse gases, 650 tons of air pollutants, 180 tons of water pollutants, and 344,000 tons of waste material.

New wind turbines at Ford of Europe’s Genk Plant
Two giant wind turbines, each 150 metres high, recently began turning at Ford of Europe’s Genk plant in Belgium, generating a combined four megawatts of ‘green’ electricity. Ford, which has partnered with local energy company Electrabel, says each unit’s 2MW output produces enough energy to power 2,500 homes.
“It’s part of our ongoing effort to implement a broad portfolio of environmental initiatives across our European plants that are aimed at further reducing the CO2 footprint from our manufacturing operations,” explains Wolfgang Schneider, Vice-President, Governmental and Environmental Affairs, Ford of Europe.
The company claims the wind turbines will deliver a significant portion of the power required at the Genk plant, where Ford produces the Mondeo sedan, hatchback and wagon, as well as the S-MAX and Galaxy minivans. The initiative at Genk follows that of 2004, when Ford of Europe’s Dagenham (UK) Diesel Centre became the world’s first automotive plant to meet all its electricity needs from two on-site wind turbines – with a third is due to go into service later this year. The extra power generation will mean that despite the installation of a new 1.4/1.6-litre Duratorq TDCi engine production line, the plant will remain 100% self-sufficient in terms of its energy. Supplied by Ecotrcity, the three blade-design turbine will add a further 2MW of electricity generation.
Also in the UK, Ford’s Dunton Technical Centre is another group facility now fully powered by renewable energy. Home to approximately 3,000 engineers, electricity at the 270-acre site is supplied from fully-renewable sources by GDF. The French utility sources power from a combination of hydro, wind and waste generation. Ford estimates that using this green energy saves in excess of 35,000 tons of CO2. Like Toyota’s Huntsville, Alabama facility, solar energy has been helping to power Ford’s Bridgend, Wales engine plant, thanks to an interlinked system of roof-mounted solar/ photovoltaic panels.
Ford has also started to use renewable energy at several of its German production facilities. The electricity needed for production facilities at the Niehl Plant (Cologne), a technical centre in Merkenich, and Ford of Europe’s head office, also in Cologne-Niehl, is generated by three hydro-electric power plants located in Norway and Sweden. Further, the Merkenich Technical Centre is heated by steam sourced from the German provider RheinEnergie. This would otherwise be wasted energy as it is a by-product of a co-generation power plant. Steam reaches the centre’s boiler house via a 2.6km pipeline.
“Such developments demonstrate the substantial progress we are making and our commitment to further improving our environmental performance,” explains Wolfgang Schneider. “We are building on that progress and continuing to look at ways to further reduce the carbon footprint of our manufacturing and office locations across Europe, parallel to the carbon footprint of our products.” According to Ford of Europe, the alternative energy programmes that feed its various green initiatives in Niehl and Merkenich reduce the division’s annual CO2 emissions by some 190,000 tonnes.
New flower species absorb factory emissions
While the generation of ‘green’ energy may address the environmental issues surrounding power used in the production process, Toyota has gone one step further by introducing an unusual solution to reducing emissions greenhouse gases outside its plants: two geneticallyengineered species of flowers, created to absorb greenhouse gases at the Prius manufacturing plant.
Derivatives of cherry sage and gardenia, the new species are specifically engineered to absorb nitrogen oxides, removing heat from the atmosphere. Planted around the Tsutsumi factory, home to Prius production, each absorbs nitrogen oxides, while removing heat from the surrounding atmosphere. This is said to reduce surface temperatures around the factory grounds, leading to reductions in the amount of energy used to cool the plant. The leaves of Toyota’s flowers are said by the company to possess unique characteristics that allow them to absorb harmful gases. In the case of the gardenia, the leaves naturally emit a cooling water vapour into the surrounding air.
The shrubs are part of a wider plan to reduce the environmental impact of its manufacturing activities. Toyota states that since 1990, it has reduced the CO2 emissions of its Tsutsumi plant by 55%. Techniques used to achieve this reduction include the fitting electricitygenerating solar panels on the plant roof, while special photocatalytic paint has been applied to exterior walls in order to absorb harmful airborne gases such as NOx and sulfur oxides (SOx).
Another cost-saving solution visible outside the Tsutsumi plant is the specially engineered lawn. Designed to grow more slowly than conventional grass, it only requires mowing once a year; previously, the lawns had to be cut three times a year. Additionally, 2008 saw Toyota plant 50,000 trees, this to offset the factory’s CO2 emissions.
The interior of the Prius plant also serves to showcase a series of energy-saving initiatives. Solar tubes beam reflected sunlight into rooms that were once illuminated by electric bulbs, while motion-sensitive lights in toilets are automatically switched off when unoccupied. After consulting with employees, the company decided it could raise the level at which the office air-conditioning system would feel comfortable, eventually settling on 28oC. Following on from this, staff are excused from wearing ties and short-sleeved shirts have become the norm.
SEAT installs 13m kWh of annual electricity capacity
The start of 2009 also saw the launch of ‘SEAT al Sol’, a project designed to bring clean electricity to the Volkswagen Group subsidiary’s Martorell factory, located near Barcelona. With a higher-than-average number of sunlight hours in comparison to most other automotive production plants, the plant (and surrounding region) has been selected as part of an ambitious collaboration with GA-Solar, a specialist division of the GESTAMP Corporation.
As part of SEAT al Sol, renewable electric energy is to be both produced and consumed on-site. This will be done via a system of integrated photovoltaics situated on the workshops, as well as a dedicated part of the factory grounds; an area covering 320,000m2. The partners are currently in the process of installing more than 10Mw of photovoltaic panels, with the system anticipated to be fullyoperational by the end of the year. With the capacity to generate an annual average of 13m kWh, SEAT estimates that this is equivalent to the average amount of electricity consumed by 3,000 households over a typical twelvemonth period. In using solar energy to generate the plant’s electricity, SEAT further estimates that annual CO2 output will be reduced by an average of 6,200 tonnes.
The partners’ investment in SEAT al Sol, which will eventually have an output of 4MW of grid-connected power, is €17m. Once this first phase of the project is up and running, the solar power plant at Martorell will, SEAT claims, be the second-largest building-integrated photovoltaic facility (in terms of clean electricity production) in Spain, and one of the largest in Europe. With the Spanish carmaker SEAT working hard to muscle in on a crowded space where seemingly every OEM is shouting ever louder about its eco-credential, the SEAT al Sol project demonstrates a commitment beyond producing cars with lower emissions. The initiative is, the company states, about lowering environmental impact during all phases of production and development, through to the recycling of its products.