Dual-purpose laser
In laser technology, the distinction between diode and fibre methods is clear – but automotive manufacturers are likely to need both types on their production lines
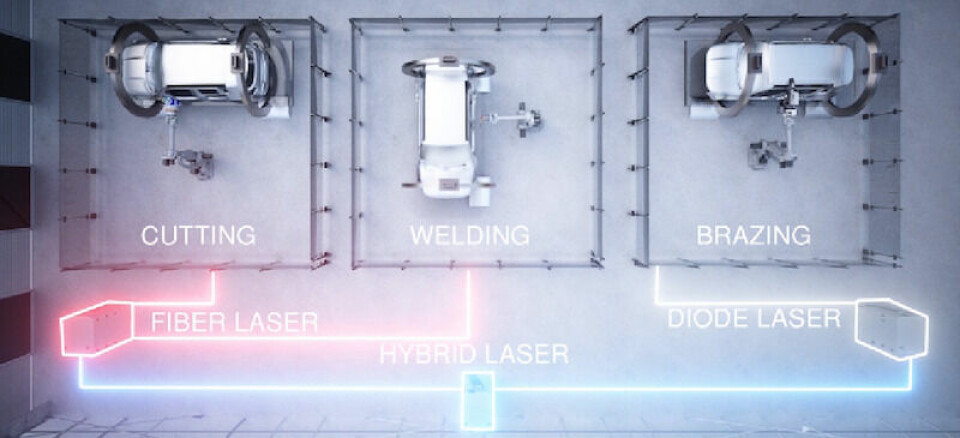
Lasers are now a commonplace tool on factory floors and are universal in volume car manufacturing environments. They fall into two categories – diode and fibre, a distinction exemplified by both the way the beams are generated and in their respective application areas. In the case of the former, the beam is fed directly from the diode where it is created to its point of use. In the case of the latter, the diode is coupled with an optical fibre to produce a beam with different characteristics. Essentially a diode beam is more diffuse and therefore suitable for applications such as brazing, while a fibre beam is more intense and therefore more appropriate for actually cutting metals.
Both types are, therefore, valid tools for particular applications – neither is better or worse than the other, just more or less appropriate for a given task – and as such manufacturers are likely to need examples of both types on their production lines. But the need for two types of beam requires two different sets of equipment to produce them, or at least it did until now. Italian company Comau, which is owned by Fiat, has just launched a new product, developed in a 23-month project with compatriot company Prima Electro, that it claims abolishes that previous requirement for multiple sets of equipment to generate the different types of beam.
[sam_ad id=17 codes='true']
Manipulating lightThe product – known as LHYTE – solves the problem of producing two different beams from the same source in a neat way that exploits the obvious and basic fact that a laser beam is a light beam and can therefore be manipulated by an optical system. Inside the external cabinet of the system the diode and yterrbium-doped fibre elements are located separately from each other rather than being conjoined, as they would be in a conventional fibre machine.
Therefore when a diode-type beam is required, the internal system deflects the initial beam away from the fibre elements so that that is what is delivered to the point of use. When a fibre-type beam is required, the beam produced by the diode is not intercepted in that way but instead is allowed to hit the fibre and excite it so that the beam is altered accordingly before it is delivered.
Giovanni Di Stefano, head of materials and process technologies for Comau, confirms the essential details of the new system. “There is always a diode laser inside a fibre laser,” he states. “So what we have done is separate them and put between them our innovation, which is a spectral combiner.” This technique, he says, constitutes the key know-how embodied in the system.
The first factor involved in that core capability, Di Stefano continues, is “mechanical precision” to ensure exact alignment within the system of the laser beam. The second relates to the fact that the two diode sources inside the system produce different wavelengths of light – 950nm and 920nm respectively – though each is rated at 3.0kW of power. In turn that means that the mirrors that form a key part of the system have to be reflective at one wavelength and transparent at another in order for the system to work as intended.
According to Di Stefano, the system is built around several different types of components. “We have a special sliding unit on which two mirrors are assembled – a standard mirror and a dichroic mirror that is able to transmit the laser beam at 920nm and reflect it at 950nm,” he confirms.
“Additional mirrors are assembled along with a beam splitter mirror able both to transmit the laser beam and reflect it. There are also the necessary electronic components for checking and supervision of the internal optical chambers and the temperature and flow of chilling water, for instance.”
The result is a high degree of variability in the respective beam output characteristics. In diode mode the maximum output power is 6kW with a beam quality of 66mm mrad. In fibre mode the corresponding figures are 4kW and 4mm mrad. The wavelength range in both cases, however, is 920-1070nm.
Close monitoringDi Stefano makes the point that in order to operate effectively the machine is fitted with an unusually high number of sensors. Each unit contains, he says, “50 embedded sensors,” including 24 thermal devices and 11 power sensors. “The different parameters that we need to control are the chilling flows, voltage, electric currents and the temperature,” he explains. “In particular we need to monitor the temperature of the water chiller, the chiller’s heat exchanger, both the diode and fibre modulus, the cold-plate and the water chiller’s flows into the optical chain.” He adds, though, that the volume of data this multiplicity of sensors collects makes the system highly conformant with the demands made by the ‘Industry 4.0’ concept. To that end the system is also compliant with the Profibus, Profinet, EtherNET/IP and DeviceNT fieldbus communication protocols.
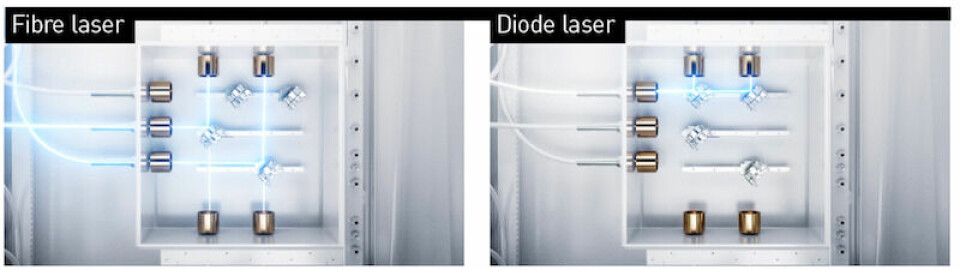
Unsurprisingly Di Stefano is confident that the system is highly innovative and contains a number of unique capabilities that Comau has sought to protect. “We have patented the optical chain of the spectral combiner, the method of realising it and the concept that permits the change from diode to fibre,” he confirms. Moreover, these new capabilities have been achieved through the use of existing technologies. “Our team has developed the design of the spectral combiner, but this has been realised by assembling different standard units,” he states, adding that the main technical challenges involved included the need to create a compact product despite the inherent complexity of a hybrid system incorporating a special component, such as the spectral combiner requiring highly precise optical alignment.
Economy in operationNevertheless Di Stefano also confirms that the key advantages the system can provide are concerned with the economics of its operation rather than purely technical performance parameters. For a start, he points out, any company needing both types of beam for its operations now only needs to buy one source and not two – a ratio that in practice will most likely mean two machines rather than four for a company implementing both techniques that simply cannot afford unplanned downtime and therefore needs duplicate capacity on-site. In addition, he indicates, this degree of economy will also manifest itself in use as a reduction in maintenance costs through the commonality of parts the two beam sources share.
In actual operation, though, the watchword is ‘flexibility’ since all conceivable types of laser application can be driven from a single source - “cutting, brazing, welding – even marking”. The units themselves are also neat and compact in size and appearance, measuring just 960x990x2050mm including their chiller, and can operate in an ambient temperature range of 10-42°C.