Connecting the network
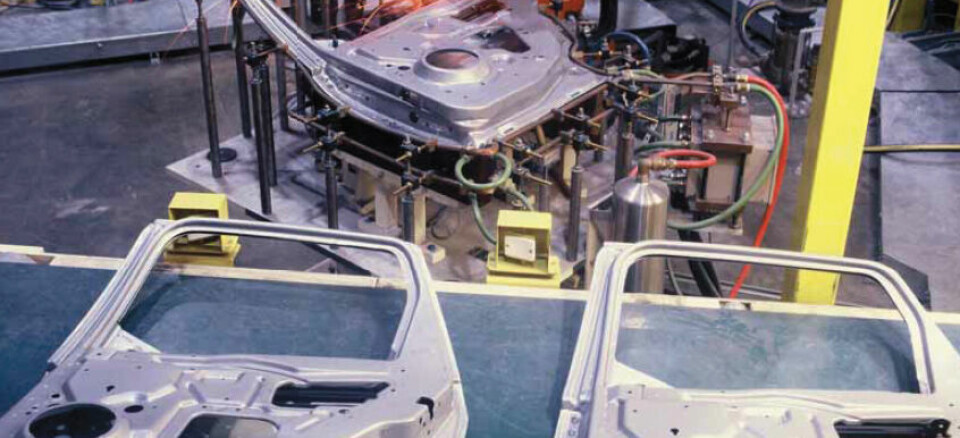
Communications systems are becoming increasingly standardised but there are still two distinct camps
One of the most fundamental factors shaping shop floor manufacturing operations in the automotive sector – and almost every type of organisation in both the discrete and process sectors – is also one that is invisible to the naked eye.
That is the increasing standardisation of the communications systems that link different items of manufacturing equipment – for instance robots and machining centres and the conveyors that transport components and assemblies between them. The underlying trend, however, is easily summarised – it is the increasing permeation of shopfloor networking by ethernet, or ethernet-based technologies, as the data link layer in automated systems. However, the plural indicates the complexities of the situation.
‘Standardised’ technologies, especially in the area of IT, can still take more than one form and the rate at which they converge is the result of politics in the broadest sense and the relative commercial success of their various embodiments. It is never the consequence of purely technological factors.
A matter of choice
In the case of shopfloor networking there are, in essence, two competing camps. One is based on the Profibus set of technologies, whose origins are European and which currently claims over 20 million ‘nodes’ in use across all industries worldwide. The other is based on the family of technologies promoted by the US-based Open DeviceNet Vendors Association (ODVA), which claims 1.5 million connections worldwide, but whose core EtherNet/ IP technology has had significant endorsement from the US automotive industry. Two years ago, for example, the US Council for Automotive Research (USCAR) formally agreed to endorse EtherNet/IP as the standard for shopfloor networking in vehicle assembly plants with specific initiative to accelerate its adoption by General Motors, Ford and what was then DaimlerChrysler.
Based in Detroit, ODVA Chief Executive Katherine Voss confirms that the process that was started two years ago will see the inauguration of performance-testing services of devices provided by ODVA members sometime this year. She explains that a basic compliance-testing service is already offered, but that the new service should relieve users of much of the pains of establishing device performance levels through ‘trial and error’. The service will obviously have use outside the automotive sector, adds Voss, but given that there is a huge base of relevant systems already installed in US vehiclemaking companies, the industry stands to benefit the most. The plural however, is again pertinent, because the ODVA in fact represents a number of different automation ‘solutions’ under the banner of their compliance with a broader Common Industrial Protocol (CIP).
The organisation started off in the mid-1990s promoting the DeviceNet networking standard, but has increasingly focused on EtherNet/IP. Voss states that the reality of industry today, particularly the automotive sector, is that several networking protocols are in use and that this situation is likely to remain the case for some time to come. “There are a lot of hybrid installations,” she confirms, but this is not necessarily a bad thing..
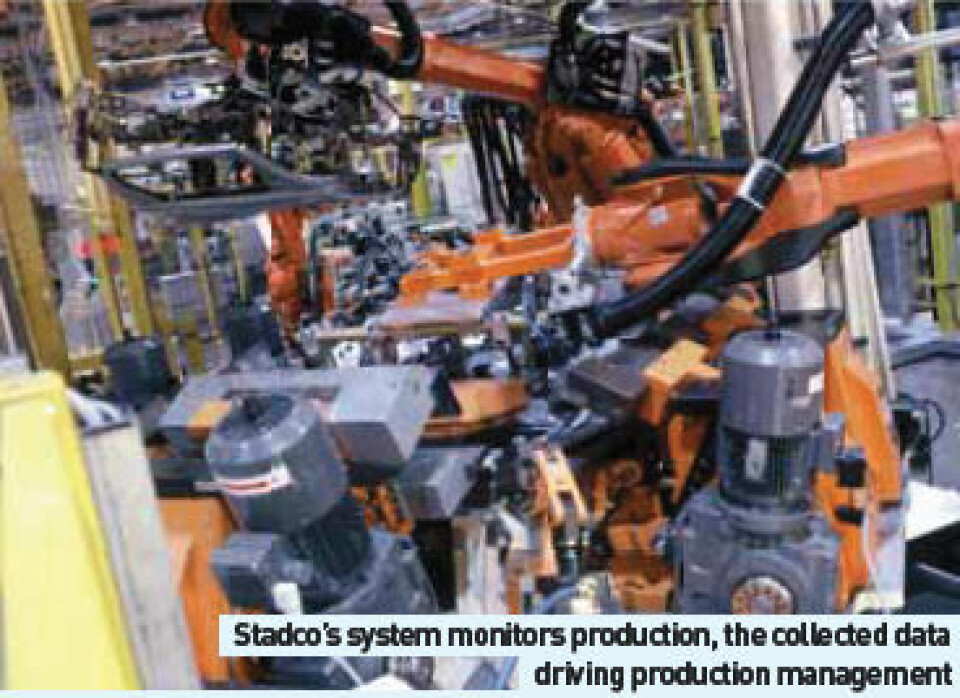
Different attributes for different networks
Different types of networking technology have particular attributes, she explains. DeviceNet, for example, enables devices with low power consumption to draw their power supplies directly off the network. But ultimately, she is in no doubt that a generalised migration to EtherNet/IP will take place. That is certainly what the ODVA is all about. “The entire industry is waiting for that day,” she states. But how is this situation viewed from the outside? Someone who monitors developments professionally is Jim Caie, Vice-President Consulting and leader of the automotive team with US-based analysts ARC Advisory Group. Prior to taking up this role, he was with General Motors for 36 years and his final post with the carmaker was as Director of Controls, Conveyors, Robotics and Welding, during which he led the development, validation and deployment of controls, networking, and robotic systems for all North American press and hydroforming projects. Caie confirms the trend towards ethernet-based technologies on the shopfloor, identifying as a key consequence that it is now “much easier to connect the automation world to the Windows world”. The significance of this development is not confined to the shopfloor, but also involves the way it facilitates the integration of shopfloor networks with a company’s surrounding offices and, in turn, allows that data to be accessed via the internet by other manufacturing and corporate networks.
He also recognises that in reality, automation (whether on the shopfloor or accessed remotely), is far from being that of seamless, ‘plug-in’ communications. “Integration is still an issue,” he confirms. “There are still a lot of problems.” Nevertheless, as someone who knows first-hand how things once were, he certainly does not deny that the situation has improved. “The technology suppliers have tried hard to base their products on standards,” he states. As a result, effective integration is, as he says, “nowhere near as hard as it used to be”.
Choosing one or the other
As for the two ‘flavours’ of ethernet represented by the ODVA and Profibus camps, he notes that while the differences between them are not fundamentally important, they are of such substance to force an automation user or system builder to choose one or the other. His experience bears out that perception. Caie says he had to tell a major German automation systems provider closely connected with the development of Profibus that it would have to supply sensors that conformed to the ODVA’s ‘device level’ DeviceNet specification if they wanted to continue doing business with GM. “They almost threw me out of their office!” he says, “But six months, later they came back with appropriate products.”
Indeed, Caie’s years at the point where technology and business imperatives coincided – and sometimes collided – mean that, perhaps unusually for an analyst, he is in a position to advise on the importance of management decision-making on the part of users, rather than that of the technologies provided by suppliers.
He is emphatic that there will be future advantages gained from the increasing prevalence of ethernet-based shopfloor networking, meaning that further uptake is inevitable. That said, many of theses improvements are of the ‘soft’ variety, with undoubted value that is still difficult to quantify. Training and recruitment are an example, as is ease of system support. As Caie points out, a convergence of the basic technologies underlying shopfloor and office networks means that the same skills and support staff will be relevant. For all these reasons, he is confident that as far as shopfloor networking is concerned, it will eventually be a case of “ethernet all the way”. Yet ease of integration does not come without its inherent dangers. Standardised systems are, by definition, similar in structure, making them that much easier to be compromised by hackers and viruses. The possibility is confirmed by David Robinson, UK Country Manager of American IT security specialist company Norman Data Defense Systems. Robinson’s views are clear: “Standardisation increases the risks,” he says. For instance, ethernet technology now routinely forms the ‘transport layer’, most obviously the physical cabling and connectors, on the majority of shopfloor networks, while the TCP/IP networking protocol is equally commonplace for actual communications. While the trend towards ethernet networks has obvious benefits in terms of lowered costs through standardisation – plus a relatively large pool of available network designers with the required skill set – the number of hackers familiar with ethernet systems is considerably larger than the number with in-depth knowledge of proprietary field bus protocols.

Opening the Windows
Another element is the fact that as PLCs increasingly come to resemble PCs, the Windows operating system is assuming the status of a de facto standard. Continuous enhancements to both the software and the devices that run it, notes Robinson, mean that Windows can now meet the demand for real-time capability that shopfloor operations require. Given that “a lot of malicious files are specifically written for Windows”, there could well be problems, unless the possible dangers are appreciated and preventive measures put in place.
Robinson says that the potential for system security breaches has become a reality for carmakers. In August 2005, ‘worms’ put 13 of DaimlerChrysler’s US manufacturing plants out of action for almost an hour while Microsoft Windows 2000 systems were patched. Downtimes lasted from five to 50 minutes because of the malicious code that exploited a hole in the Windows Plug and Play service, a common component that allows the operating system to detect new hardware on a Windows system. Robinson adds that he has personal and more recent experience of a UK company in the process sector that lost eight hours of production under similar circumstances. The blunt reality, he says, is that many manufacturing companies simply do not apply the same level of security to their shopfloor networks that they do to their office systems. “Ask them if they routinely update Windows or anti-virus systems on the shop floor,” he notes, “and the answer if often ‘no’.”
Exploiting the gateways
An important point to note, he adds, is that infection of a shopfloor network does not necessarily require deliberate intent by employees. There are two common routes that can allow shopfloor systems to be unwittingly compromised. The first is the integration of shopfloor networks with wider business software, most obviously an ERP system, which, in turn, is connected to the internet.
Any company that has such a ‘top-floor-to-shopfloor’ form of connectivity, he states, has a gateway that can exploited to introduce some form of ‘malware’. The second is the introduction of infected software to the network by a third party, a consultant or external software or hardware maintenance employee, literally carrying the problem through the door in their own laptop. Either way, states Robinson, it is a serious issue that does not get the attention it deserves. Yet with a few preventive measures, much of the potential hazard can be obviated.
Despite the possible hazards for less cautious users of the technology, it is evident that the emphasis in the use of shopfloor automation has shifted from the problems of integration between hardware and software elements to the effective exploitation of the increased capabilities. This, is according to John Boville, US automotive segment manager for PLC supplier Schneider Electric, who has been involved with the technology in both the UK and the US for more than two decades.
When he first started out, constructing shopfloor networks with components from different suppliers was a complex and difficult task. Now, on the back of a convergence in standards and the widespread adoption of ethernet, the whole issue is more straightforward, though according to Boville, an out-of-the-box compatibility between PLC hardware from different suppliers has still not been achieved. Instead, what he describes as a “degree of configuration” has to be carried out, though in practise this involves no more than the use of routines that can be easily carried out by a typical controls engineer employing nothing more complex than the in-built capabilities of the device. No customisation or specially-written software is required or at least not with modern devices that conform to the relevant standards.
Like David Robinson, Boville pinpoints the nowubiquitous presence of Windows in shopfloor devices like PLCs as a particularly important underlying factor. One consequence is that their programming routines are affected through commonplace techniques such as cut-and-paste, familiar to anyone who uses a PC. Boville adds that the situation might well be different if one attempts to integrate an older ‘legacy’ system into a more modern network. As a supplier of PLC technology, Boville is also keen to stress the opportunities, rather than the inherent dangers, of ‘wide area’ shopfloor communications devices. This ‘internet to ethernet’ capability is one of the attributes Schneider Electric emphasises in its products. For example, it stresses that the Modicon M340, introduced in 2007, can be accessed remotely either by modem or through a standard asynchronous digital subscriber line (ADSL) from any location. In practical terms, says Boville, this opens up the potential for remote monitoring and if necessary, fault remediation of networked equipment by the equipment suppliers themselves. He claims he is aware of at least one major US vehicle maker that benefits from this approach, though he declined to name the company.
In short, the integration of shopfloor manufacturing and company business networks to allow ready access to and transmission of data is now a relatively straightforward task. Yet many companies in the automotive sector still fail to make their systems work as efficiently as possible by generating useful information, says David Lloyd, IT Director of UK components supplier Stadco. With that in mind, the company has set up an example of just what can be achieved at its flagship plant in Shrewsbury, UK. Lloyd tells AMS it has integrated an Mfg/Pro ERP software system with automated data collection software provided by UK company Intouch. Explains Lloyd, “The system itself monitors what is being produced and the data is used to drive production management.”
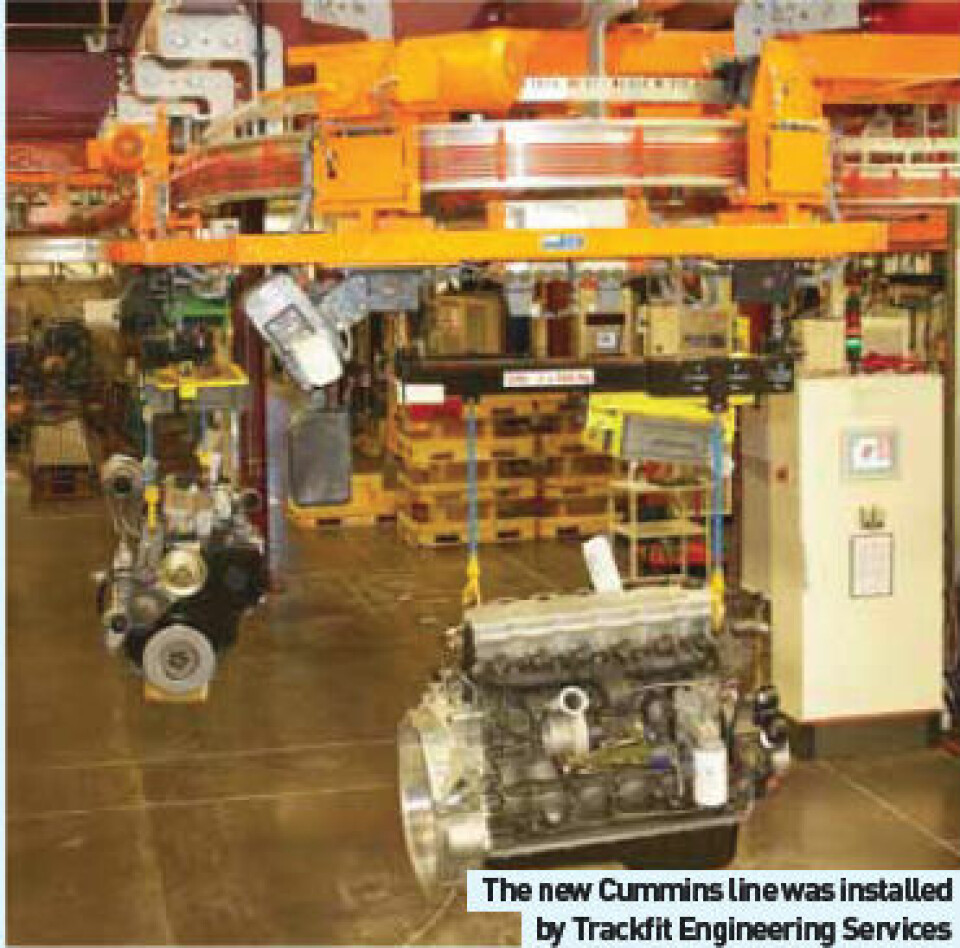
Benefits of integration
Lloyd says that one of the major benefits of integrating shopfloor and business systems in this way is to allow the generation of detailed equipment efficiency figures. “It also allows you to see where your bottlenecks are,” he adds. The system at Shrewsbury has been in operation for the past two years, but according to Karl Edwin, Managing Director of Intouch, the type of data being collected and the environment in which the system operates do not favour the use of standardised communication protocols. Instead, it relies on a relatively simple networking infrastructure with ‘dumb terminals’ at each shopfloor machine, linked into a central system server, no more than an industrial PC linked into the ERP system. The collected data is, as Edwin explains, “productionbased, rather than process-based” meaning it coallates relatively simple numerical data generated by counting operations, the number of parts or machine cycles, rather than variable process parameters, such as temperatures, voltages or pressures. But that does not make the operating environment any less ‘noisy’ in terms of electronic data collection.
As such, Ewin reveals that the basic network linking the shopfloor terminals to the PC relies on ‘RS485 connectivity’ for its hardware elements – cabling and connectors. The underlying communications protocol however, is entirely that of Intouch itself. Edwin explains that given the nature of the application, indeed of all the typical applications of the software, a proprietary solution is more robust and costeffective than one based on standards, which by implication are over-specified for the type of circumstances in which the Intouch system will normally be used. “We have looked at using various types of ethernet, but this puts up the price of the operator terminals,” he points out. Nevertheless, he does concede that as the data involved becomes more complex and process-based, then a move to ethernet would be unavoidable.
Controlling the carriers
In contrast, one major manufacturer for which standardised (Profibus) communications plays a major role is the UK division of diesel engine producer Cummins, having recently completed a major upgrade to assembly and pressure test procedures at its Darlington, Durham plant. Where engines had been transported through the plant using a combination of overhead chain conveyors, powered floor conveyors and automated guided vehicles, in 2006 the whole system was replaced by an electric monorail system (EMS) during a two-week shutdown.
The EMS comprises 600 metres of overhead monorail, 50 carriers, 14 switchpoints, three lift units, one rotate unit, 34 assembly stations and four pressure test stations. There are a number of networks in the system compliant with the Profibus specification. These provide communications to radio frequency identification (RFID) devices, operator panels, maintenance touch panels, carrier controllers and distributed I/O points. These networks are also used to interface between the Siemens S7-317DP PLCs which control the system. All the carriers have a Moby data tag attached, which stores an engine’s build attributes and determines its route through the system. At each of the assembly and test stations there is a read/write device which communicates the engine data and operational status back to one of the PLCs.
Driving the devices
There are three production pressure test lanes and one repair test lane. Each carrier has an onboard controller which constantly reads an encoded rail to determine its position in the system. Each carrier communicates status and command words bi-directionally with the relevant PLC, again via Profibus. Every assembly station is also fitted with an OP77A human-machine interface (HMI) panel that allows the operator to raise and lower engines to a suitable working position, to offload them to the floor or reload them into the system and to release an engine to the next station when work is complete.
Both offloading and reloading operations involve updating the RFID tag to reflect its new status. Profibus connectivity was a key factor in the selection of the OP77A devices. The whole system is an undoubted success, daily production rates in the first year increasing from 220 to 350 engines. The communications elements of the system were designed and installed by Cleveland Systems Engineering (CSE), a systems integration outfit. Tam Ashcroft, Managing Director, confirms that the specification of Profibus (or similar) compliance for the operation of the system and related hardware selection is increasingly typical of the automotive sector projects in which the company is involved.
In the Cummins application, Profibus is used to link devices such as the HMIs and RFIDs, and to connect these upwards to the PLCs. At the level above that, the higher-specification Profinet takes over to link the PLCs to Cummins’s manufacturing execution system (MES). At the level below a simpler, but still standardised communications specification, Actuator Sensor Interface (AS-I), is employed.
Installation times are reduced
For Ashcroft the benefits of using standardised communications in this way are overwhelming. “Installation times are hugely reduced from the familiarity you get with repeated use,” he says. When in use, he adds, fault-finding capabilities are also greatly enhanced, not least by the fact that a standards-based approach makes it much easier to customise the HMI screens to display fault locations. “Users tell us they can now often find faults in minutes,” he explains. As such, there is definitely a convergence in the use of standardised communications, he says, and on the basis of CSE’s work (which is currently limited to the UK and Europe), it is equally evident that, as Ashcroft tells AMS, “Profibus has won the race.”
The race, however, is not confined to Europe. Katherine Voss claims there is increasing interest and awareness of the importance of standardised networking in the Far East, although – as yet – there is no discernible trend towards its implementation. Part of that, she admits, is because the whole issue is complex and far-from-easy to communicate. “It is easy for the marketplace to get confused,” she notes.