Colonised by China

The underdeveloped but populous countries of South-East Asia could be rich pickings for Chinese OEMs
The Chinese are now mounting their most serious attack yet on the domination of Japanese brands in South-East Asia, after Geely was announced in May as the new foreign partner of Malaysia’s struggling Proton Cars, beating France’s PSA Group. Geely, which also owns Volvo, joins a list of Chinese vehicle-makers targeting the region. For example, SAIC is expanding its Thai operations and the SAIC-General Motors brand Wuling, which this year is launching a car designed for Indonesia, has built a new factory there. The other Chinese OEM to watch is commercial-vehicle specialist Foton, which has opened a plant in the Philippines.
South-East Asia has long been a catch that Western and even Korean vehicle-makers have so far failed to land, albeit with a few exceptions. That any continue to try when some of the leading car brands, notably GM, have failed here is down to the obvious growth potential of the region. South-East Asia is under-represented in vehicle ownership compared to its population, which at just under 650m is around 9% of the global total. The most populous country in the region, Indonesia, records car ownership of 69 per 1,000 people, compared to 588 in Japan. Malaysia has the highest figure in the region, at 361, with Thailand at 206, the Philippines at 30 and Vietnam at 23.
Like most underdeveloped markets, the expansion of vehicle sales here is somewhat up and down, but right now its countries are mostly aligned in their expansion. In the first three months of 2017, car sales in the six main countries of Thailand, the Philippines, Indonesia, Malaysia, Singapore and Vietnam grew 11% to 826,545, according to Japan’s Nikkei, with the Philippines up 20% and Thailand finally growing again with an increase of 16%. Production in the region in Q1 was up 3% to just over 1m vehicles.
Differing stories for Malaysia’s makersThe ambitious Chinese companies want to get in at the bottom to take advantage of future growth in the region. Announcing its purchase of 49.9% of Proton from current owner DRB-Hicom, Geely said it was looking to “build Proton into the most competitive brand in Malaysia and a leading brand in South-East Asia”. Geely has proved that it can turn around foreign brands before, with its successful purchase of Sweden’s Volvo. Reports in the Malaysian press suggest that it is no less ambitious here, aiming to build 500,000 Proton cars in the country within five years.
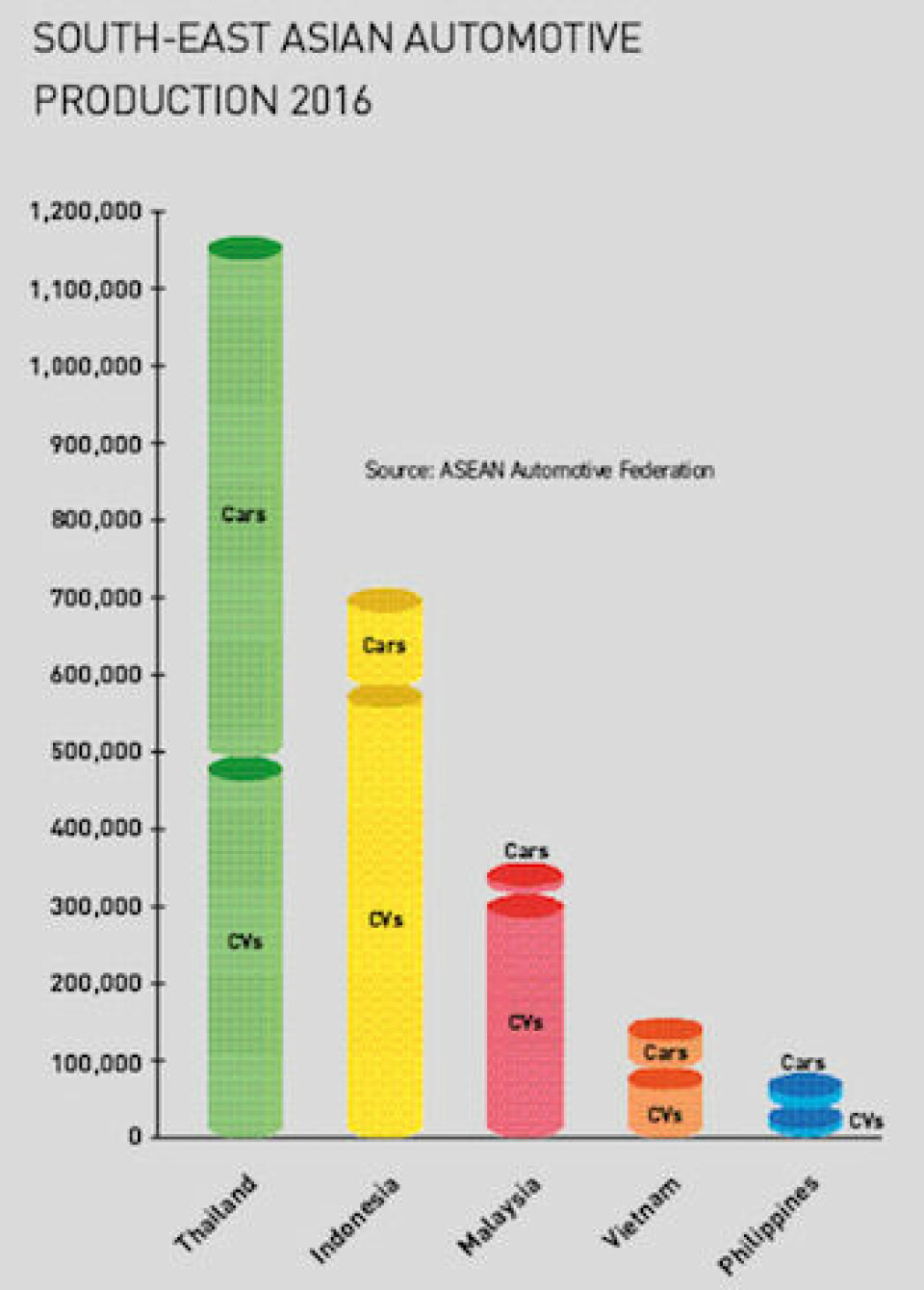
However, Geely faces an uphill battle. Proton is one of two national car brands in Malaysia, and by far the least successful. Established in 1983 with technical support from Mitsubishi, Proton has fallen far from its heyday in 1993, when it had a market share of 74%. In 2016, the loss-making brand’s share of the Malaysian vehicle market was just 12% on sales of 72,290, according to data from global sales aggregator bestsellingcarsblog.com.
By contrast, the share of Toyota-backed Perodua, which specialises in smaller cars, was 36%. “Proton may need to spend years to regain the brand reputation it once had here,” Jessada Thongpak, senior analyst, ASEAN vehicle production forecast, at IHS Markit told AMS.
Proton also struggles to make sales elsewhere. For example, it sold just 589 cars in neighbouring Indonesia, down from 2,263 in 2012, according to local vehicle-maker association Gaikindo. It means that Proton’s two factories are running below half their capacity; Shah Alam, in the suburbs of Kuala Lumpur, has space to build 50,000 and Tanjung Malim, 100km north of the capital, has capacity for 150,000. Within the Geely partnership, Shah Alam will be sold off for redevelopment while Tanjung Malim will become the focus of production.
Meanwhile, business is booming at Proton’s rival, Perodua, which last year opened a new engine facility along with partner Daihatsu (a full subsidiary of Toyota) at its Sendayan transmission factory. Perodua, which is 25% owned by Daihatsu, has two assembly plants in Rawang, Selengor. Its bestselling car is the B-segment Axia, a rebadged version of the Daihatsu Ayla/Toyota Agya which sells well in neighbouring Indonesia.
Proton will be hoping that its partnership with Geely will give it a similar boost as it gains access to the Chinese OEM’s increasingly sophisticated technology. Geely has said that it will share its Boyue SUV platform with the goal of developing Proton’s first-ever SUV. It might also choose to address Proton’s lack of a pick-up truck, one of South-East Asia’s most popular vehicle types.
Japanese OEMs still dominating IndonesiaIn Indonesia, the big Chinese hope lies with minivan specialist Wuling, the hugely successful partnership between SAIC and GM, which started production in July at a new plant in Cikarang, west of Jakarta. The company has developed a new seven/eight-seat small minivan called the Confero S which targets the country’s bestselling segment and is being launched this autumn. Wuling said it has invested $700m in the new facility and intends to use it as a base to export to other South-East Asian countries.
Wuling needed to bring out a new vehicle built for the market to have any hope of competing with the dominant brands of Toyota, Daihatsu and Honda. The three took 73% of the market in 2016 “mainly because they are among the only ones to design and produce vehicles specifically dedicated to the Indonesian market,” according to Matt Gasnier, owner of bestsellingcarsblog.com. Indonesia is virtually a closed market to any but Japanese brands, which last year took a 98% share, building this proportion of the 1.2m cars produced in the country, according to Gaikindo.
The pressure forced GM to shut its Bekasi factory in 2015 and pushed out Ford in 2016. In addition, the volume for Hyundai-Kia has slumped, with Hyundai’s production of passenger cars from kits down to just 510 last year from over 5,000 in 2011. Only the German premium brands are holding on, with BMW and Mercedes building around 2,000 cars each last year from imported kits. The market leader, Toyota, continues to grow in confidence, adding a new engine plant at its Karawang assembly facility in 2016, with capacity to make just over 200,0000 1.3-litre and 1.5-litre petrol engines per year. It is the first Toyota plant outside Japan to include onsite smelting.
Production boom in the PhilippinesThe Philippines are another South-East Asian target for Chinese manufacturers as automotive production and sales show strong growth. Last year, sales rose 25% to 404,051, according to bestsellingcarsblog.com, with Toyota taking 39% and Mitsubishi in second place with 13%. These gains are reflected in the still nascent automotive production, which rose 32% in Q1 this year to 33,404 units.
Foton is the Chinese OEM which is making the biggest push, having opened a 1.2-billion peso ($23.6m) plant north of Manila in 2016 to produce light- and heavy-duty commercial vehicles from kits, plus an SUV. The production capacity of the single line is reportedly 12,000 units, with room for expansion. Last year, Foton sold 4,081 vehicles in the Philippines, making it the 12th largest automaker in the country.
Along with Vietnam, the Philippines are one of the few South-East Asian countries which are not dominated by Japanese manufacturers. Last year, for example, Hyundai was the third biggest-selling brand, with a share of 7.4%, just edging out Ford, which has seen a lot of success with its pick-up-based Everest SUV. This persuaded Hyundai to set up a factory in the Philippines, just south of the capital in Santa Rosa, Laguna Province. The plant started operations in March this year, building the Eon B-segment small hatchback and E350 van from kits, with a capacity of 40,000 vehicles, according to local media.
Thai and Vietnamese markets open upChina’s most successful push into South-East Asia right now is in Thailand, where automotive giant SAIC is building a second factory to produce its MG brand for local sales and exports. Last year, its sales in Thailand – the region’s second-biggest market after Indonesia, with sales of around 750,000 – stood at 8,319, giving the company a market share of 1.1% and making it the 12th biggest manufacturer. That this still makes SAIC the biggest OEM from China in South-East Asia gives an indication of the scale of the challenge facing the Chinese.
However, SAIC is reportedly spending 30 billion baht ($879m) on the new plant south-east of Bangkok with its local joint venture partner, and this will eventually allow it to switch from kit assembly of cars like the MG 3 B-segment hatchback and C-segment GS SUV to full production. The plan is to target not only local sales but also right-hand-drive export markets such as Indonesia and the UK. Thailand exports around half of its automotive production, which in 2016 came to just under 2m vehicles, up 2% on the year before. SAIC’s strategy could work “but it will take time”, IHS’s Thongpak said to AMS, noting that the company’s strategy is to price its cars below the Japanese vehicles.
Toyota is the number-one vehicle-maker in Thailand, with a market share of 32% in 2016, followed by Isuzu with 19%. Both manufacturers hold their positions thanks to their dominant one-tonne pick-ups, the Toyota Hilux and Isuzu D-Max, which vie for the position of bestselling vehicle in the country.
Of the non-Japanese, Ford is the biggest player, in seventh place last year, and this is also thanks to its locally built pick-up, the Ranger. This pick-up and the Everest SUV based on the same platform have kept the OEM’s sales alive in Thailand and the wider region during a slump in demand for its locally built Ecosport small SUV and cars like the Focus and Fiesta. Last year, Ford added production of the Ranger to its Rayong plant in Thailand, which was previously making only cars. Production of the pick-up continues at Ford’s joint-venture facility, AutoAlliance Thailand (AAT).
Ford has also been successful with the Ranger in Vietnam, where it has a joint-venture plant to build vehicles from kits. In the first four months of 2017, the Ranger was the bestselling passenger vehicle in the country, making it the only non-Japanese vehicle to top the charts in any of the major South-East Asian countries. With trucks included, the country’s biggest player is Thaco-Kia, which assembles Kia cars in a plant at the Chu Lai industrial park in Quang Nam Province. It also builds light- to heavy-duty trucks, taking 26% of the market last year, as well as making cars with Mazda. On the truck side, Thaco collaborates with China’s Foton, building its Auman range of heavy-duty trucks.
Last year, the Vietnamese vehicle market climbed past 300,000 for the first time after increasing 24% on the year before. This growth comes on the back of a 43% rise in 2014 and a 55% jump in 2015.
Motorcycle production in South-East Asia is massively weighted towards Indonesia, which saw sales fall 9.5% to 5.93m last year, according to the Indonesian Motorcycle Industry Association. That is a long way from the country’s 8m high in 2011. Other markets brought better news for local producers, dominated again by the Japanese. Production rose 31% in the Philippines to more than 1m; 9.5% to 3.1m in the second-biggest market, Vietnam; and 4% in Malaysia to 395,938.
Thailand’s motorcycle production was static at 1.8m but its ability to attract premium brands such as Truimph and Ducati was given another boost earlier this year when US manufacturer Harley Davidson announced that it would open a plant in the country to build for local and regional sales. Trade deals in the region mean that it will avoid stiff import taxes and cut delivery times. The new plant, based in the Rayong district which is home to the likes of Ford, Suzuki and Ducati, will assemble motorcycles from kits. As for Ducati, its production in Thailand fell 22% to 8,761, or just 15% of its total.
As vehicle production across South-East Asia moves from mainly completely knocked down assembly into full production, substantial changes in the supply base can be expected, writes Ian Henry. Indonesia and the Philippines especially should see significant investment in new parts manufacturing facilities as local content rises. In Thailand, where full vehicle manufacturing operations – especially Japanese – are more developed, there is already a wider network comprising companies such as Denso, Aisin and other major Japanese suppliers. It is likely that Thai operations will play a prominent role in leading the development of new factories in emerging markets in the region, such as Vietnam and Cambodia.
IndonesiaDenso is using its Thai factory as the lead plant for its expansion in Indonesia, which centres on a $88m investment in Cikarang, east of Jakarta. The company will expand an existing facility for the production of compressors and clutches for air conditioning systems. The plant already employs 1,900 people and turns out 4m parts a year for Toyota, Daihatsu, Suzuki, Mitsubishi, Isuzu, Honda, Ford and GM, supplying both their Indonesian plants and sites across the region.
MalaysiaThe components sector here faces a significant challenge after the sale of Proton to Geely in May, which will very probably result in the Chinese OEM’s suppliers winning business in Malaysia. The impact has not yet been felt, but in the meantime the Malaysian government’s Matrade (Malaysian External Trade Development Corporation) has urged Malaysian component suppliers to look overseas for opportunities, especially in Indonesia.
Malaysia has established capabilities in shock absorbers, weather-stripping, brake pads, wheel rims, transmission components, head-up displays, alarms, sensors, lighting electronics and air-conditioning parts – areas in which the government believes the country should be able to develop its exports. The government has facilitated meetings between 25 Malaysian companies with 44 potential partners in Japan in a co-ordinated search for alliances. Malaysia’s component exports to Japan grew by more than 25% between 2014 and 2016 and the government is keen to widen its domestic industry’s horizons.
ThailandThe automotive components business in Thailand is well-established and larger than in other South-East Asian markets, reflecting the full production – notably of pick-up trucks – in the country by the likes of Mazda, Mitsubishi and Isuzu. In addition, Honda has established key component production operations here to supply in-car entertainment and electronics components and systems worldwide.
More recently, Mazda announced that it would expand engine production in Thailand to 100,000 units a year by 2018; this should lead to opportunities for both local suppliers and the transplant operations of Japanese suppliers. Mazda’s imminent growth should offer opportunities for companies like Daisin, a producer of aluminium parts. Originally founded as a local partner of Japanese brakes company Nissan Kogyo, this is now a wholly Thai-owned operation which supplies Toyota with parking brakes for the Fortuner SUV, as well as brakes to the local operations of Honda and Mitsubishi.
The PhilippinesVehicle production in the Philippines is poised to rise to 500,000 units a year by 2020, more than trebling the country’s 2010 production volume of 168,000 units, and the Philippines Parts Maker Association (PPMA) sees this a major opportunity for the country’s fledgling components industry. Until recently, parts production in the Philippines has focused on relatively low value-added components, with a rising level of high-value component imports.
The PPMA sees the imminent rise in vehicle production as likely to involve significant investment in the country by overseas suppliers, through joint ventures or technical licence agreements. Initially, the PPMA expects local suppliers to find their best opportunities in metal parts such as brackets, body stiffeners and latches, plus manufacturing tools, dies, moulds and fixtures for vehicle plants in the country.
VietnamThe country has a small vehicle assembly footprint and a correspondingly limited components sector. In addition, the Vietnamese automotive industry is about to experience significant change as the Association of Southeast Asian Nations (ASEAN) drops tariffs for intra-ASEAN trade. Vietnam will lose its 50% import duty on vehicle imports and this will likely place a question mark over the viability of Vietnamese vehicle production, certainly without some form of support for the industry.
The Japanese companies already in Vietnam currently source around 33% of the components they need in the country, a localisation level well below the 66% achieved in China and 55% in Thailand. The official aim is for the Vietnamese automotive industry to achieve 35-40% localisation by 2020, rising to 60% by 2025 and 65% by 2035. Vietnam has a strong network of parts suppliers for motorcycles but whether this is a sufficient base from which to develop a wider supply base is another matter. There are currently fewer than 60 component suppliers in the country, highlighting the challenge facing vehicle-makers which have been charged with increased localisation. The main locally produced components are wiring harnesses, fully assembled seats (made from mainly imported parts), batteries and simple injection mouldings.
There is a pressing need for the sector to modernise and achieve global standards in production, quality and cost. Although this is not going to be a quick process, some progress has already been made on a small scale. For example, Tap Hop Co is now a tier-two supplier to Toyota, while Thanh Cong, which makes automotive fabrics, has established a close relationship with Hyundai.