Choosing the perfect plot
Vehicle manufacturers must consider a wide variety of factors when choosing new sites. MAN and Ford reveal the criteria each company considered before starting construction, with a wholly-new production model
By the middle of this year, truck and bus manufacturer MAN will likely employ as many as 650 people at its newest European production site, located in Niepolomice, near Kracow, Poland. The facility, which was opened two and a half years ago, produces heavy trucks with a gross vehicle weight over 16 tonnes. When operating at maximum output, the plant produces up to 15,000 vehicles a year. A key driver behind the decision to locate the plant in Poland was the close proximity of the site to the relevant markets. This was highlighted at the plant opening, when MAN Group’s Director of Production, Lars Wrebo, said: "We are assuming that above all the markets, Eastern Europe and the CIS will be growing at above-average rates. We want to share in this growth."
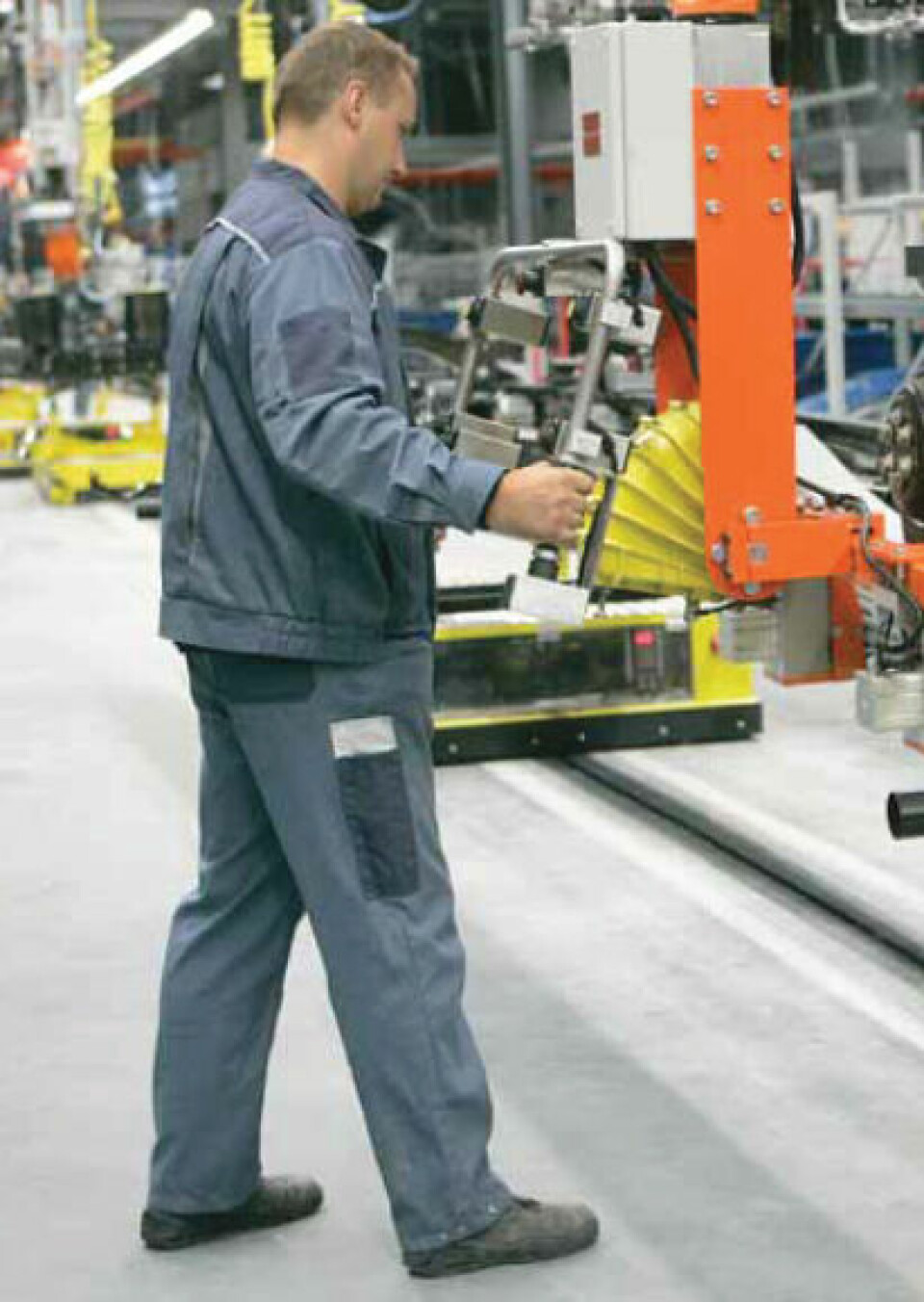
The plant is the third that the German-based series truckmaker now operates in Poland, the company also building low-floor buses in Starachowice and city buses in Poznan. As such, the location of the Niepolomice plant ties in with both the company’s strategic sales policy and the existing logistics infrastructure. At the time, the company’s country presence meant that one out of every two national logistics providers would be basing its business on supporting MAN vehicle production. But besides market access, proximity to the company’s domestic base was also a factor in the equation, since axles, cabs and engines are supplied directly from manufacturing plants in Germany and Austria.
Despite this, the company has made it clear that the decision to site new facility in Kracow, or even Poland, was far from automatic. Instead, the final location choice was the result of an exhaustive evaluation project in which factors such as the infrastructure, costs, availability of qualified labour and the legal and industrial framework were all subject to scrutiny. In this instance the decisive factor was, according to the company, “finding the right balance between logistics costs and personnel costs.” On that basis, Kracow proved to be the ‘geographical optimum’. Still, an automotive manufacturing plant is not something that can be uprooted and re-established in a different location with any ease, not only because there are specific problems physically transporting production equipment from one place to another; reliable logistics networks and trained employees are far less easy to relocate. Which means that getting the location decision right in the first place becomes of critical importance.
According to a spokesman for the company’s Strategy Department, based in Germany, the criteria surrounding site evaluation are linked to a pre-defined assessment procedure. “They are weighted according to their relevance for the project and then the weighted criteria are scored for each option. The sum of the scores will then be put together in a ranking to identify the best option.”
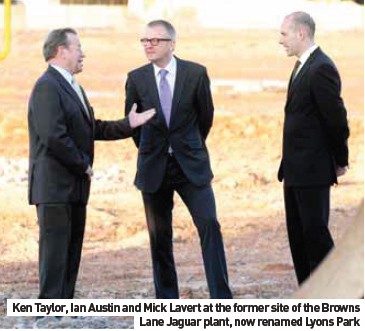
Nevertheless, despite operating internationally, the company does not have a series of fixed policies when looking to set up remote manufacturing operations away from its home base. Instead, the decision is contingent on a number of factors. “There is no general policy covering an assembly or production site abroad. Such decisions are always dependent on what is necessary to achieve sales and profit targets in a specific region,” says a company spokesperson. “For example, some markets require local value creation in order to be eligible to participate in public tendering. Another reason for local production could be high import tariffs which can be avoided if production or assembly were done locally.”
Country experience makes the difference
In the case of Niepolomice, the decision to locate the new truck plant there was relatively easy. “MAN has been market leader for trucks in Poland for many years, so it was a fairly natural, logical progression, when in 2005 we decided to located a new production site in the country. Effectively, Eastern Europe, and especially Poland, had been an area driving European growth for the previous couple of years.” Previous experience in Poland, both in terms of the country being a major market and manufacturing base (with the two other sites in Poznan and Starachovice), were both driving factors behind the decision to locate the new truck assembly operations in-country. Put bluntly, familiarity with a particular country, reaching beyond any logistics infrastructure to encompass knowledge of local laws, language and population, will always serve as a positive influence in a company’s decision-making process when looking to make a repeat investment; not withstanding the economic success of any previous installations.
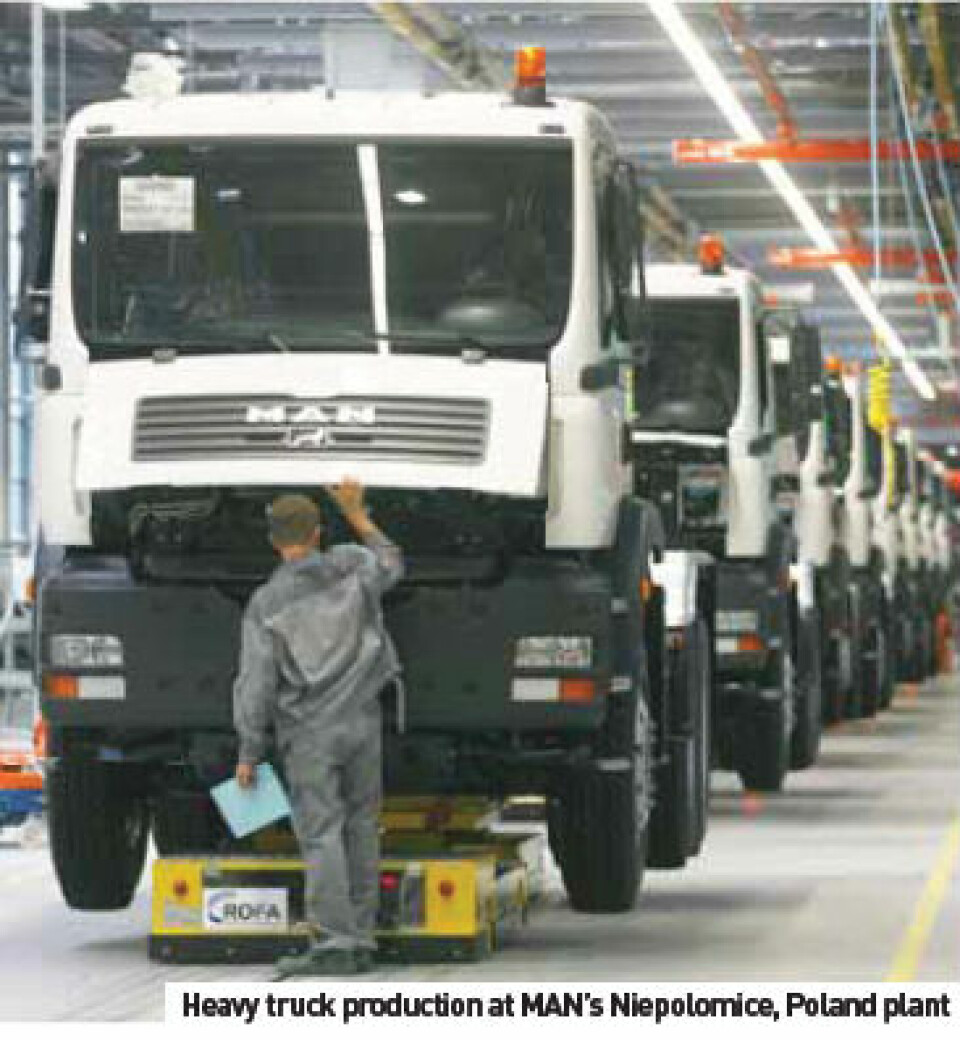
For MAN’s Niepolomice plant, the ‘people’ factor was of integral importance. “We were looking to make use of the existing skills of our colleagues in Poland wherever possible,” says a MAN representative. For instance, the factory manager now at Niepolomice had previously managed Polish bus production facilities. But the logistical tie-in also added weight to the argument. The Niepolomice factory is an assembly site, meaning that materials, components and sub-assemblies must be shipped in from either supporting MAN facilities or supplier locations. For instance, in the case of the products made at Niepolomice, the wiring harnesses for the trucks come from a Polish source, whereas engines are manufactured at the MAN facility in Nuremburg, Germany.
Once those broad strategic decisions have been taken, the more tactical question of whether a plant should be situated on an undeveloped ‘greenfield’ site or a previously-developed ‘brownfield’ location is again not a matter of pre-defined policy but of particular circumstances. “It is a decision based on the assessment of investment risk, i.e. how far the expected benefit from starting up a new site will outweigh the cost of potential failure,” the company explains. “In some cases, expanding an existing site may provide an advantage by enabling us to serve the market faster. There is no general company policy about it, as it all depends on the local conditions.”
A brief run through of other recent MAN development projects illustrates the point. Niepolomice was a greenfield development, but the company confirms that its two bus factories in Poland were both brownfield projects.
Something that appears to have helped with the development of the Niepolomice project is the sheer speed with which it was possible to carry out the whole project. Production operations actually started only two years after submission of the relevant proposals to the Polish authorities. “It’s true that the execution of this project has been rather swift,” the company confirms, adding that it had the full support from the local authorities in Niepolomice and Kracow from the start of the project. This was, “a crucial factor in the projects’s success”. Another plus is that the factory is located in a designated ‘industrial zone’. As such, it is using land in an area where the local authorities are actively seeking to promote relevant investment.
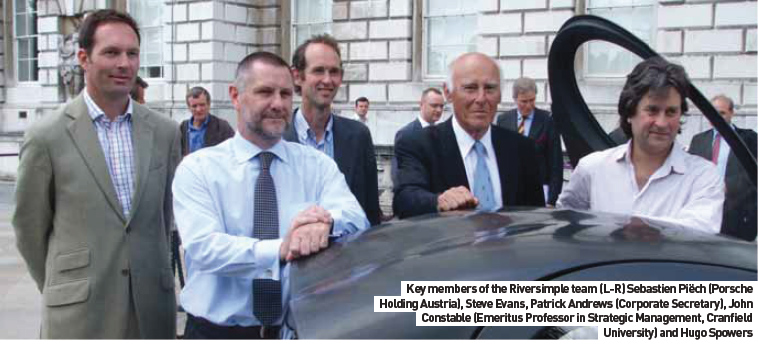
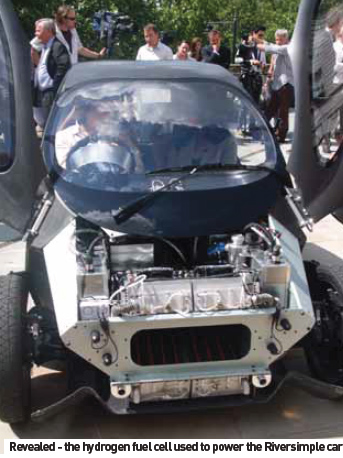
Several hundred miles away in the UK, Steve Holland, Head of Asset Management for Advantage West Midlands (AWM) is directly involved in the business of getting automotive companies to set up new facilities in his region. Located in what continues to be home to the vast majority of UK-based carmaking operations, Holland unsurprisingly says that the automotive sector as a ‘huge’ element in AWM’s portfolio. In line with the experience of MAN in Poland, Holland confirms that no single element is of paramount importance when it comes to persuading companies to invest in the region. Instead, various factors come into play, with each individual issue carrying more or less weight in the final decision according to the specific requirements of the companies involved. “It depends on the nature of the business,” Holland observes, though he indicates that as far as AWM is concerned, the fact that the area is synonymous with automotive production and offers a deep base of relevant skills is a major factor in its ability to attract related inward investment. As Holland notes, if prospective investors feel that they will not be able to find the right sort of people, then they are not going to proceed whatever other inducements might be on the table.
In this context the actual physical nature of a site – greenfield or brownfield - is of secondary importance. Holland says that the general policy of AWM is to encourage the re-use of brownfield sites, but he also admits that if a would-be investor was bringing a significantly large investment to the area, with the a large number of direct and indirect jobs that the project would develop, then it would not be an issue if they stipulated a requirement for a greenfield site.
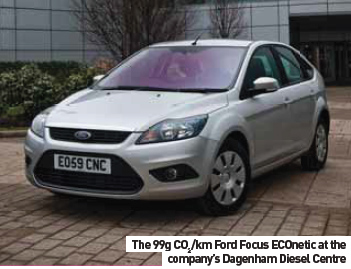
A degree of pragmatism is therefore the order of the day. This is directly illustrated when examining a major on-going site redevelopment project where AWM is working closely with a private sector company. In this particular case, the location is the former Jaguar manufacturing site at Browns Lane in Coventry, UK. Now renamed Lyons Park, the site is being prepared for a new manufacturing location, in a partnership between AWM and property development company Goodman. Holland explains that Goodman acquired the site at peak market value, the overall value of the site dropping as the country (and other global economies) was caught up in the recent market downturn. AWM stepped in to buy 24 acres of the approximately 60-acre site for £9.8m, on condition that the money was used to fund the necessary site redevelopment work. While not specifically intended for a business related to automotive manufacturing, the site will clearly prove attractive to automotive companies owing to its location within the heart of the UK motor industry.
On another front, Holland says that AWM is involved in discussions with Indian automotive manufacturer Tata about possibly siting a proposed European technical centre in the region. Should that be the case, he says, the concentration of relevant academic expertise in the area is an obvious positive for any proposal.
New manufacturing models
What both the operations of MAN in Poland and AWM in the UK have in common is an assumption about the basic business model within the automotive industry. This is one in which the industry comprises a small number of major vehicle builders with a logistical chain of materials and component suppliers that may stretch from their own factory – most obviously the operations of ‘co-located’ suppliers – to almost anywhere else in the world. But is that model bound to last? Is it the only one that is possible for the automotive industry?
“Consumers are increasingly concerned about the CO2 embedded in the products they buy, which includes the processes and facilities used to make them.” This, from Andy Taylor, Director of Sustainability for Ford Europe. It is an insight that underpins everything he does in his role. Taylor, who is based Ford’s engine production facility at Dagenham, UK, says that the company has been ramping up the sustainability of its products and production processes since the 1990s, a commitment fi rst driven by then company CEO Bill Ford. He points out that the company published its fi rst ‘corporate citizenship’ report in 2000, a document that sought to relate everything the company did to a broad awareness of social responsibility, though in fact it had been issuing more narrowly focussed environmental impact reports for several years previously. A decade on, Taylor says the concept is embedded in the company, across all relevant departments. Ford, he says, is a ‘function-led’ organisation and the various operational areas within the company enjoy the freedom to act on their own initiative. As a consequence Taylor’s own role now has an increased external focus. For instance, he says that his current focus is working with BP to formulate environmentally-benign engine oils. But the overall environmental effi ciency of the company’s manufacturing plants and the associated operations remain a primary concern. Dagenham, for instance, has taken the lead in making cutting fl uids and lubricants more environmentally friendly. A fundamental element of the strategy has involved decreasing variation in the composition of the fl uids, not so that they are interchangeable in use, but that mixing them together after use does not cause cross-contamination and waste, making recycling and re-use a possible alternative. The result, states Taylor, is an 80% reduction in the consumption of cutting and cleaning fl uids at the plant. Dagenham is the Ford facility that pioneered the use of wind energy. The Dagenham Diesel Centre has been powered by two 121m wind turbines producing a combined total of 6.7m kW/hours of electricity per year since 2004. The facility has been self-suffi cient in electricity since when the turbines went operational, with any excess shared between other site operations. Taylor notes that the retrofi tting of the turbines at a well-established site probably helped in their acceptance. While the inclusion of such structures at a Greenfi eld site might have generated opposition, the sleek towers and blades provoked no such problems in Dagenham. “We didn’t know what the reaction would be, but we only had one negative comment,” reports Taylor. Subsequently two further turbines have been installed at the company’s plant at Genk, Belgium, and plans are now in hand for a third turbine to go into operation at Dagenham next year.
Someone who would answer ‘no’ to both those questions is Steve Evans, Professor of Lifecycle Engineering at Cranfield University in the UK. He would say so not so much from his academic vantage point, as from his role in one of the most innovative vehicle development initiatives currently underway. The project is being conducted by Riversimple, based in Ludlow, UK, and involves the development of a two-seat citycar using carbon composite body materials and an electric motor powered by a hydrogen fuel cell. This would, the company states, enable the car to achieve the equivalent of 300 miles per gallon.
The innovative nature of the project goes beyond the powerplant and materials. The concept also aims to pioneer new models of payment, customer use and manufacturing. Regarding the former, the intended procedure would be vehicle leasing rather than payment for use. On the latter, the plan is to employ distributed manufacturing, with production taking place in small factories close to the intended vehicle point of use. Production volumes at these sites could average 5,000 units per year. While individual plants might produce standardised vehicles, the fact that there could be more than just one or two factories would allow a much larger degree of product variation. The whole concept is arguably a methodology for achieving mass customisation.
Evans says that this approach to manufacturing is derived from the materials and technologies that the vehicles will use, pointing out that composites manufacture is “labour intensive, rather than capital intensive”. As a consequence, low volumes can still translate to economic viability because the infrastructure will not require the output of a volume production facility to be amortised over a given period. The enthusiasm Evans, who is a member of the Riversimle board, shows for the concept is not born out of any hostility to the established business model. It makes perfect sense to have factories making 100,000 vehicles a year, he observes, if the cars have a conventional construction of steel frame with attached panels. But he adds, “you have to have 100,000 people a year who want to buy the cars.” In other words, the combination of the materials used in the vehicles and the type of production processes they entail enforce a need for high-volume manufacturing in necessarily large, centralised facilities. As Evans observes, the situation is implicit in “the technological sources and business model”.
Moreover, no degree of managerial skill or procedural efficiency can alter this basic fact. The automotive industry, Evans adds, is already “the best in the world” at high-volume, automated manufacturing. No other type of manufacturing can equal the efficiency and effectiveness of its processes. Therefore, only a radically different way of doing not just some things, but everything, can fundamentally alter this situation and establish a completely new paradigm. This is what Riversimple aims to do. At present only a single vehicle exists, which Evans describes not as a prototype but a ‘technology demonstrator’, while the company is currently raising funding to build 60 vehicles to test its ‘service-based’ sales strategy. The first element of that is now in place, the company having signed an agreement with the City of Leicester, in the UK, which will see 30 of its vehicles being used in a pilot scheme from Spring 2012. Whether this intiative will succeed will ultimately depend on the market, a point that has not escaped Evans: “The main driver is not legislation, but customer behaviour.” But he is confident that the beginnings of appropriate market demand are now discernible, a wave that could ripple back up the delivery chain and actually begin to shape both how and where cars are made.