Boron, or boron-free? That is the question
Metalworking fluids containing boron have hit the headlines recently, mainly due to REACH legislation and labelling requirements, reports Umut Urkun of ExxonMobil Lubricants and Specialties.
As well as the health and safety implications of using metalworking fluids containing boron, some industries have started looking at alternative solutions for a different reason. In advanced manufacturing industries, including areas of the automotive sector, companies have started to look at different chemistries due the impact of cutting fluids containing boron on crack detection tests. There have been cases where the use of such fluids has been found to result in hidden flaws in a component during integrity testing.
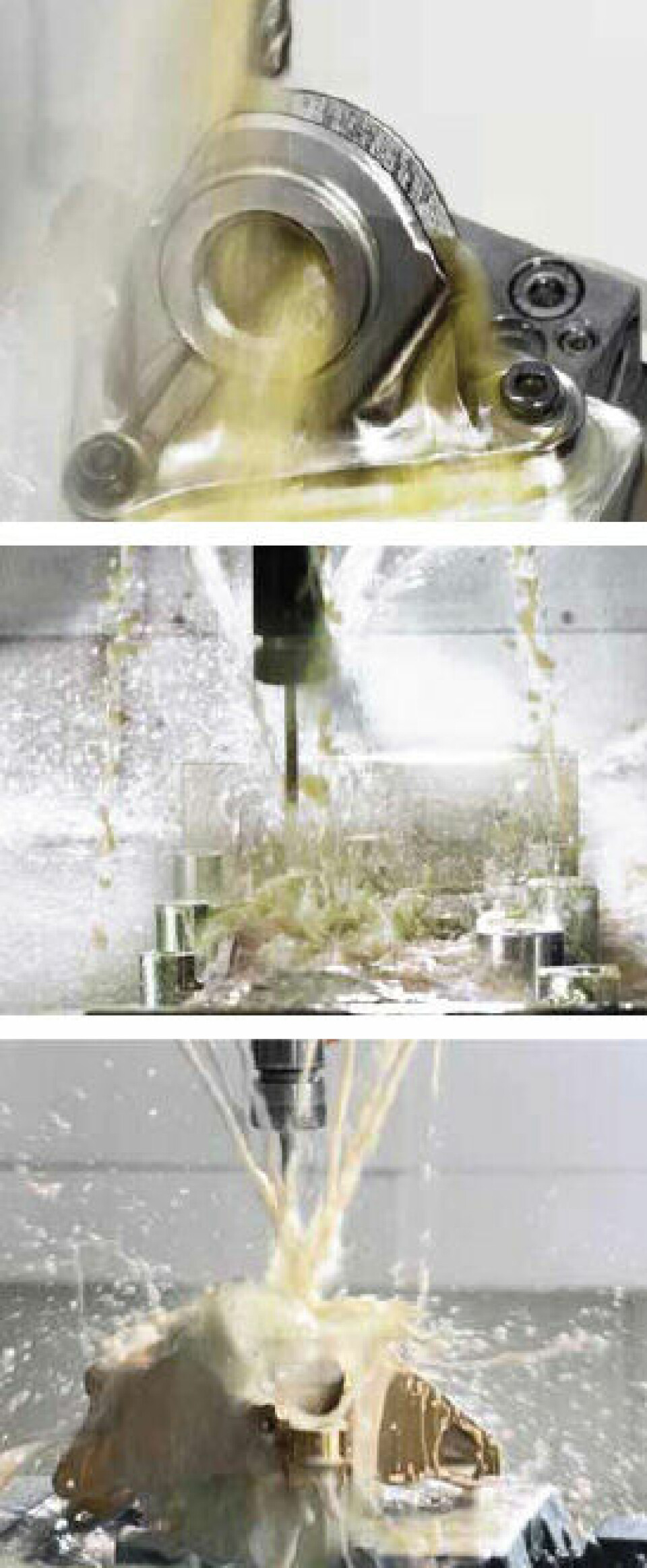
Boron metalworking fluids and alternative technologies
Boron has traditionally been used in water soluble metalworking fluids as it acts as an excellent corrosion inhibitor and helps to extend fluid life by slowing down the development of bacteria, with the chemical helping a fluid to be more inherently stable. Simply removing boron from a fluid is one option but it is not a viable solution in all cases due to tougher metals and more advanced, severe metalworking processes. From a health and safety perspective, the European Commission (EC), has highlighted that metalworking fluids containing boric acid with a concentration equal to or in excess of 5.5% must be classified and carry appropriate labelling. For fluids under the 5.5% limit, current legislation means that products do not need to be labelled as a hazardous substance.
Future formulations
The use of boron in metalworking fluids will continue into the foreseeable future due to the benefits it delivers in formulations, but the focus now for metalworking fluid companies is to develop products which have low levels of boron while maintaining the same degree of performance achieved by higher concentrate versions. ExxonMobil’s latest water soluble range of metalworking fluids, for example, are below the 5.5% threshold and still offer extended technical stability, helping to maintain a good charge life. However, with other factors outside of potential health and safety issues creating a market for boron-free metalworking formulations, leading companies in fluid development, such as ExxonMobil, have developed chemistries which still offer machine shop operators high performance products. New technologies included in the ExxonMobil range of Mobilcut fluids include phenoxyethanol and a lactic acid derivative. The boron-free Mobilcut 250 for example, which contains phenoxyethanol, is a high performance semi-synthetic fluid formulated to enhance performance when machining aluminium and aluminium alloys and where low staining potential is important on sensitive components. Containing high levels of lubricity agents, it provides high machining performance of carbon and alloy steels and yellow metals.