Always on the move in conveyors
As a means of moving goods around production plants – whether isolated components or vehicle assemblies – conveyor systems remain a reliable, robust and proven option. Some basic attributes also remain constant, irrespective of the complexity of the system involved.
That brief list is provided by Andrew Minturn, product manager for assembly technologies in the UK, for Bosch- Rexroth. Though Minturn does not identify any materials handling issues that are particular to the sector, he includes it in a list of those that are looking for greater variety in the configurations they can achieve through the use of standard elements in pursuit of lean manufacturing strategies. There is, he notes, likely to be an increased requirement for U-shapes rather than straight lines.
As far as Bosch is concerned, the company laid the foundations for that strategy as far back as the early 1980s when it adopted a lightweight, all-aluminium fabrication approach for the basic structures of its conveyor systems. But, as Minturn notes, “ensuring the longevity” of such systems for the future is bound to require flexibility in their initial configurations and ease of reconfigurability to meet changing product specifications without the need for major substantial new investment.
Small but strong
Meanwhile a seemingly consistent trait of the materials handling industry is that despite the key role its products can play in the operations of major companies – even vehicle OEMs – they themselves may be quite small. CI Logistics, for instance, based in Leicester, is a US-owned UK operation that employs just 31 people in the design, manufacture and installation of conveyors and associated materials handling systems for clients that include several well-known automotive names – Honda and JCB, for instance.
According to sales manager for the company Adrian Pryce the business gets round this limitation through the effective use of sub-contract services – particularly for installation work. Though it does some carry out some assembly work of its own, its focus is on system engineering – in other words design – and sales. On the former count, Pryce says that a particular attribute of the company is its willingness to step outside of any boundaries that might be set by the use only of standard components. “We believe our bespoke engineering strength is unique in the UK,” he states.
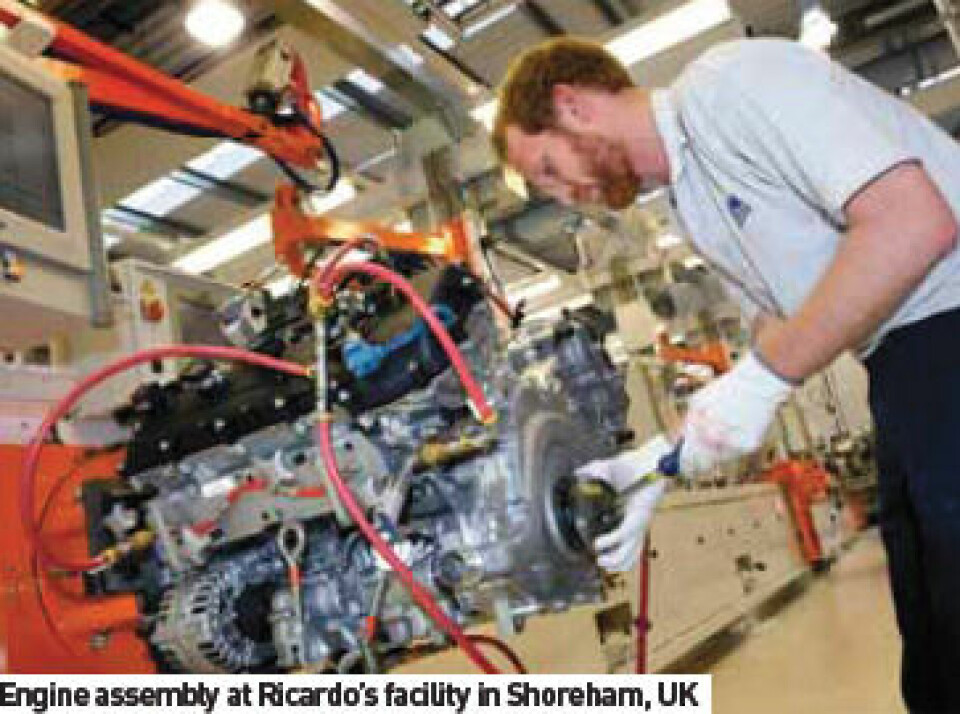
For this reason, Pryce stresses the importance of the initial phase of contact between CI and its clients. Getting things right at this stage – ensuring that requirements are accurately specified and that the consequent design accurately satisfies them – is crucial. Interestingly, though, he indicates that the automotive sector can exhibit slightly contradictory traits in this respect – that in one direction it moves in favour of optimal solutions being arrived at, but in another it can act to compromise that possibility.
One positive factor is the industry’s competence in specifying exactly what it wants in performance terms from suppliers such as CI. “You will always get a very specific request-for-quote,” says Pryce. Interestingly, though, he also adds that such documents usually also make a point of requiring logistics providers to ensure that any proposed solution is the best available. “If there anything better, they want to know,” he states. The point might seem obvious, but is has not always been the case. “There was a time when they were over-specific,” he explains.
Time is of the essensce
One the other hand the more demanding aspect of supplying such systems to the automotive industry is the relatively short timescales that may be involved, sometimes for producing the initial quotation document and quite often for actually carrying out the installation itself. On the latter count, Pryce points to the fact that the work often has to be shoehorned into holiday shutdown periods.
That was not the case, though, with the system CI supplied to JCB – an overhead chain-driven conveyor some 250 metres in length for the powder coating line at the JCB Heavy Products factory in Uttoxeter, Staffordshire, UK.
As Rob Cauldron, senior paint application engineer at the plant confirms, the factory only opened four years ago. Cauldron was involved with the line right from the initial planning stage. JCB itself, he confirms, specified the line in great detail. All of its major attributes – its overhead nature, the need for manual loading of parts, loading capacities, throughput rates – were stipulated and the resulting document circulated to a list of preferred contractors. CI came in as a sub-contractor to the outfit that won the main contract.
Cauldron says that the nature of the parts – generally small and lightweight such brackets and doors – meant that reconfigurability was not an issue. Quite the opposite in fact – the line was specified and designed on the assumption that no major changes would be required for at least ten years. Whatever flexibility may be required in the meantime – in terms of new product parts with different sizes and geometries – can be dealt with through the inherent adaptability of manual loading procedures and the straightforward expedient of altering the speed of the line if necessary.
Conveyors for container convenience
The use of conveyors isn’t confined to production areas, they can also have a role in the receipt of parts into a factory and the return of empty packaging to the suppliers. That latter role, for instance, figures large in a major system in North America installed by Bastian Solutions of Indianapolis. The client for the project was the logistics subsidiary of a major vehicle builder, which takes responsibility for the delivery and return of containers to and from the automotive manufacturer’s assembly line. The project involved the installation of three distinct handling systems in a purpose-built facility connected directly to an existing assembly plant via an above-ground tunnel through which several electric ‘tugger trains’ run.
The systems comprise, respectively: a small parts picking system that receives containers measuring a maximum of 43”
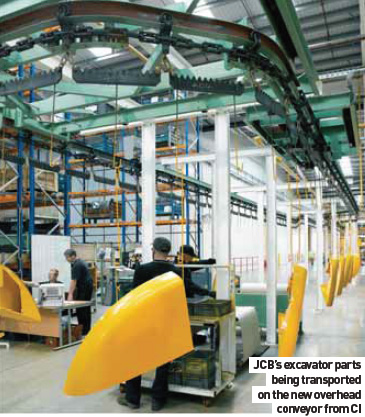
long by 23” wide, carrying parts that are sorted and then despatched to the plant; the corresponding small container sorting system which receives the empty containers back from the plant and sorts them prior to their return to the appropriate external supplier; and a large container sorting system for the similar handling of containers measuring a minimum of 48” long by 45” wide that had previously been delivered direct to the lineside.
Senior project engineer with Bastian, Blain Cook, who took a lead role in both the planning and installation phases, says that though the small and large container sorting systems both aim to perform exactly the same task, the difference in size of the containers involved means they have to employ different types of hardware for doing so. Those handled by the large container sorting system can be extremely heavy – the maximum weight of the largest empty container is 231lbs.
The weight factor was a major reason why, for the large container system, it became necessary to design a customer un-loader to remove the containers from the train. The initial system specification called for lift assists with rigidmast end tooling to transfer the containers from the trains to the conveyor. But that concept was eventually deemed insufficient on both throughput and ergonomic grounds. Instead preference was given to an alternative involving un-loaders that operate in a similar manner to a forklift truck.
The empty containers are then transferred to a heavy duty chain driven conveyor where they are automatically sorted, by means of optical scanning of barcodes on their surfaces into one of 36 track lines, each of which is reserved for containers from a particular external supplier. They are then removed from the conveyor by integral lift devices and loaded onto forklift trucks which deliver them to waiting lorries to be returned for re-use. Meanwhile the small container sorting line operates in a similar but not entirely identical fashion – a major difference being that the smaller size of the containers enables them to be both loaded onto and unloaded off the conveyor manually.
Again, though, subsequent sorting is automated – though in this instance not by supplier but by container size. Cook says that as the containers pass an array of lights, their size is detected simply by the extent to which they block the light path to corresponding receptors so that they are redirected by a simple mechanical pusher into one of three lanes at the end of the system. At that point the personnel operating the system simply read the relevant supplier’s name on an external label, remove the containers and place them on an appropriate pallet on the floor beside the conveyor, which is then again taken to a waiting lorry by forklift truck.
The two systems together therefore exhibit some interesting traits. Perhaps the most evident is the way that they are configured according to container size and weight to use different levels of associated identification and handling methodologies – fully automated at one extreme, purely visual and manual at the other – to achieve identical objectives.
Another is the scale of the supplier relationships they can handle. Though in each instance only around half a dozen container sizes are involved, the number of actual external suppliers is much greater. The precise figures are not given but can be to some extent inferred from Cook’s indication that the figure of 36 end-points for containers on the large container system is matched by 64 locations for pallets by the side of the small container line.
Rapid pay-back
As far as the basic physical means of transporting and buffering the containers in between their arrival from the production line and their retrieval by the forklift trucks is concerned, Cook is emphatic that conveyor systems offered the optimal solution. “I suppose a rack and crane system would also have worked, but it would simply not have been economical,” he states. “Conveyors really were the only really efficient option.”
As it is Cook reports that the system has not only proved itself in practice but also, though he does not cite actual figures, succeeded in meeting a payback period of “between one to two years”. In large part this derives from the minimal staffing the system requires and here Cook does provide some details. On a per shift basis, he states, the small container sorting line requires “two to three” people for its operation and its large counterpart “six to seven” – the adjacent small parts picking system, by the way, operates with “six to seven” personnel.
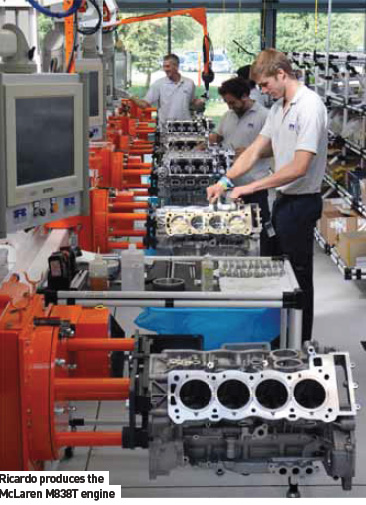
Promoting performance
But the notion that conveyors are by their nature suited only to high-volume environments is not the case. One UK installation – opened only last year to build engines for a high-performance sports car in volumes of just a few thousand a year – at most relies on a very clever mix of seemingly low-tech materials handling with associated high-tech quality control systems to meet the most exacting standards for end-product reliability and performance. This is the assembly line for the M838T engines for the McLaren MP4-12C sports car, located at the technical centre of consultants Ricardo in Shoreham, Sussex. The facility is unusual, as production manager Tim Soar admits, because it represents the first time that Ricardo – an organisation with a long track record in engine design and associated manufacturing consultancy – has actually also itself become an engine manufacturer. One advantage of this situation, Soar adds, is that design of the engine and production facility were carried out in parallel – quite literally under the same roof – by Ricardo. In consequence some aspects of the engines were created to support manufacturing quality – a small area of machined surface on the exterior, for instance, is there to enable an in-line metrology routine.
The assembly operations take place in a cleanroom environment with three distinct areas of activity – to one side a cylinder head assembly line with six stations, in the middle a single continuous main assembly line of ten stations with two parallel straight sections and loops at either end; and on the other side of the room a testbed for completed engines. Each area is equipped with an unpowered conveyor line supplied by Exmac Automation of Droitwich Spa along which – at least in the first two instances – assemblies are manually pushed on platens before being locked into place for assembly procedures to take place. Workpieces are moved between the areas on trolleys that are, again, manually propelled. That approach is, Soar confirms, the result of a deliberate policy to keep material handling and transport systems as simple as possible in line with the overall ‘single piece flow’ lean manufacturing philosophy.
Quality control in command
The process starts with the manual loading of cylinder heads onto their assembly line at the side of the room after which they are moved through all six stations on the line in a period of 62 minutes. At each location, completion of the relevant procedures – manual assembly in the first five cases followed by automated testing – is corroborated by an automated quality control system which alone has the authority to release the locking system to allow the platens to be pushed to the next station and then finally be loaded onto the trolley for transport to the middle of the room. In the central assembly area the engine blocks are loaded and then at successive stations undergo all the required assembly operations to produce an engine ready for ‘live’ testing. In fact, the only element of non-manual handling involved is that the assemblies can be rotated on the platens by means of handheld electric drills that are inserted into a connection point on the side of the platen.
After that the completed engines are pushed across to the final test BIPO test cell for live running to check factors such as emissions levels. Here, two short lengths of completely passive conveyors actually play an interesting role. Soar explains that the platens with engines ready for test are placed on a short length of inclined conveyor, down which they slide under gravity in a queue, at the end of which they are loaded into the test cell. Hence the conveyors act as both buffer store – four engines at a time – and sequencing mechanism.
But then, in a neat touch, of which Soar is obviously rather proud, engines that have gone through testing are placed for cooling on an adjacent conveyor inclined in the opposite direction so that when an engine reaches the bottom of that slope, the various attachments required for the test procedure can be removed from it and be fixed to the next available engine in the queue for testing. With a bit of imagination, it seems, even a straightforward length of conveyor can be made to act as a rather clever piece of kit.