Troubled times
New global politics and difficulties at home threaten the production and export hubs of Japan and Korea
Threats from the US to tear up free-trade agreements and impose tariffs on imported vehicles is causing fear in the export-dependent manufacturing strongholds of Japan and Korea. The two countries already face difficulties within their established (and costly) manufacturing bases, but the threat from the belligerent, protectionist President Donald Trump to put up barriers to one of their biggest markets adds a new element of concern as they try to fill capacity in factories which have already been weakened by their policy of expanding production overseas.
Japan in particular has been targeted by Trump, who complained in January it “wasn’t fair” that American manufacturers struggle to sell cars into the country while American consumers buy so many from Japan, contributing to the latter’s trade surplus with the US. Although exports have diminished over the years as OEMs such as Toyota, Honda and Nissan have localised production in the US, the country is still Japan’s top market for vehicle exports. The Japanese vehicle-makers’ trade association, JAMA, reported that 384,094 vehicles were exported to the US in Q1 2017, compared to 213,106 to Europe, the country’s second-largest export market.
Trump’s comments were, as usual, wide of the mark. Japanese cars shipped to the US attract a 2.4% import tax while American cars come into Japan duty free. They simply don’t do well in Japan’s highly specialist and hybrid-heavy car market. According to the figures for April, Jeep was the biggest US brand, taking 20th place with sales of 3,112 for the year, up 17%; Chrysler was 36th; Cadillac was 40th; and Ford pulled out of Japan altogether in 2016. Toyota was typically dominant, taking 30% of the market with just over half a million cars sold in the first four months of the year, according to global sales aggregator bestsellingcarsblog.com. Combined with its minicar brand, Daihatsu, and premium brand, Lexus, that share was above 40%.
Nevertheless, the US threat to Japan’s export market is real. “Every Japanese OEM is preparing for the worst scenario,” AMS was told by Masatoshi Nishimoto, manager of Japan/Korea vehicle production forecasts for analyst company IHS Markit. The US accounts for around a third of Japan’s automotive exports, which in turn accounted for half of Japan’s 9.2m domestic production in 2016.
Compounding the problem for both Japanese and Korean manufacturers is that Trump wants to renegotiate the North American Free Trade Agreement (NAFTA), which could see costs rise in Mexico. Nissan, Honda, Mazda, Toyota and Kia all have plants in the country, with Toyota due to complete another in 2019.
“We expect Japanese OEMs are preparing to transfer vehicle production from Mexico to the US in the worst scenario,” Nishimoto said. That will force them to address lack of capacity in the US, which in turn could impact their strategy of soaking up excess capacity in Japan by exporting higher-value models to richer markets such as the US. IHS predicts that Japanese light-vehicle production (under six tonnes gross vehicle weight) will fall below 8.5m units from 9.0m units now. Exports to the US dropped 5.8% in Q1 this year, but total vehicle exports remain static at 1.1m, with the US decline balanced by a 13% increase to Europe.
“If… they do things to us that make it impossible to sell cars in Japan, and yet they sell cars into us and they come in like by the hundreds of thousands on the biggest ships I’ve ever seen, we have to all talk about that. It’s not fair” – Donald Trump, US president
Car production in Japan has been falling over the years as more production has moved overseas; a total car volume of 7.8m last year was well down on its 9.9m peak in 1990. However, production in Q1 rose by 6.4%, compared to a 1% drop in 2016, helped in part by a buoyant market at home, which stood at 1.6m in Q1, up 7%. Toyota saw sales climb 12% in the first four months, with second-placed Suzuki up 8%. Dominant though Toyota is, the OEM reported profits that were down 28% in the 2017 financial year, partly due to the age-old problem of the strong yen, which hinders Japan’s export policy.
Nissan works on Mitsubishi reformOne of the big questions when Nissan took a controlling (34%) stake in fellow Japanese manufacturer Mitsubishi late last year for 237 billion yen ($2.1 billion) was whether it was going to shut Mitsubishi’s Mizushima plant, one of two factories it has in Japan. Mizushima currently employs 3,334 personnel and has an annual capacity of 355,000 units.
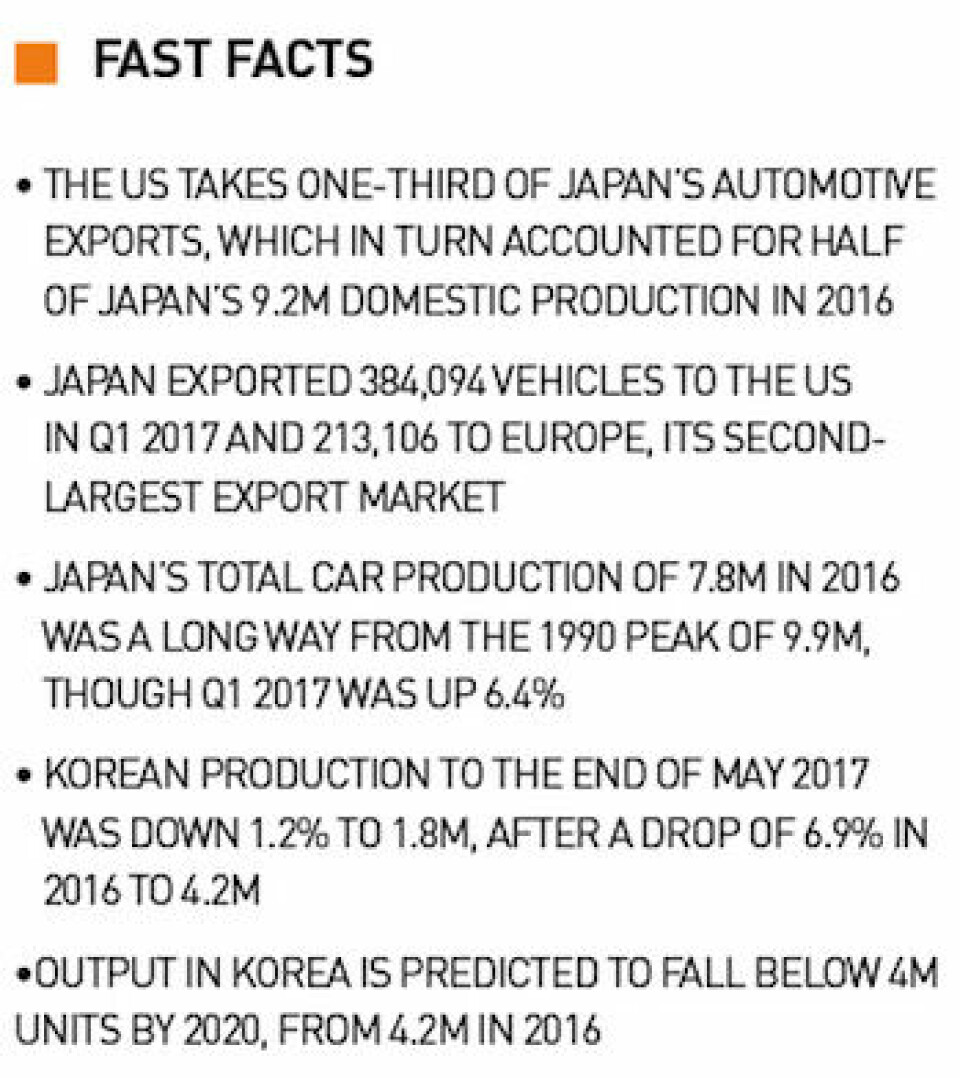
Renault-Nissan Alliance chairman Carlos Ghosn has held a fearsome reputation as a cost-cutter since shutting down five factories soon after his arrival in 1999, but in a statement released in April, Mitsubishi indicated that the plant will remain open to build its replacement for the RVR SUV, also known as the ASX or Outlander Sport outside Japan. Meanwhile, the 234,000-unit Okazaki plant will build Mitsubishi’s new Eclipse Sport SUV, which will sit below the RVR, thus securing its own future.
Nissan has already begun a lengthy reform of the struggling Mitsubishi, which was crippled by the recent scandal in which it admitted cheating on fuel-economy tests in Japan. Nissan is also starting to integrate the two companies. “Obviously we are working hard to understand what synergies we can complete,” Trevor Mann, Mitsubishi’s new chief operating officer, told AMS earlier this year. He noted that the two vehicle-makers are already shipping cars together, and in combination with joint purchasing will achieve around $250m of synergies next year.
Mann is looking at what else can be shared, including technology, platforms and even production. This will take time, however. “For a full convergence, you just need to look at Nissan and Renault to see how long some of these things can take,” he commented. “That being said, we’ve got the benefit of 20/20 hindsight to understand what went wrong, and why did it take so long and how can we do it quicker?”
For now, Mitsubishi remains in the doldrums. Production in Japan from January to April was down 13% to just over 200,000, with exports down 21%, and this was the 12th monthly decrease in domestic output since April 2016. However, one bright area was the revival of minicar cars sales, up 88% in April, as the OEM shook off the effects of the fuel-economy scandal, which mostly affected these models.
Production is laboured in KoreaKorea’s car production is being buffeted by strong global headwinds, a result partly of its dominant export strategy. Production to the end of May was down 1.2% to 1.8m. This figure would have been worse except for a bounce-back in May, according to the local manufacturers’ association, KAMA. Of that total, 1.1m units were exported. So far the year has been a little better than 2016, when production fell 6.9% to 4.2m.
As with Japan, Trump has attacked Korea’s trade surplus with the US, which is largely due to car imports, and criticised a free-trade deal that finally came into effect in 2016. Any change to that could leave Korean vehicle-makers vulnerable, including the OEM that makes what is currently the US’s top-selling passenger car – Renault-Samsung, which builds the Nissan Rogue SUV to supplement American production.

As for the leading automotive manufacturer in the country, Hyundai-Kia has continued its expansion aboard with the announcement of a new Kia factory to supplement Hyundai’s 650,000-unit capacity in India, while at home it has had to wrestle with the industrial unrest that affects all vehicle-makers here, largely centred on pay rises.“Lower productivity due to strong labour unions and stagnant domestic demand will mean Korean OEMs will find it difficult to maintain the domestic production levels,” said IHS Markit’s Nishimoto. He predicts that local production will fall to below 4m units by 2020 from 4.2m last year. Hyundai’s strategy is to focus more on high-margin vehicles such as SUVs and to shift production of smaller cars to Mexico, Nishimoto believes.
At the same time, GM Korea, formerly Daewoo, is suffering because of the OEM’s decision to pull out of Europe. Korea was GM’s development centre for small cars, but Nishimoto believes that this role will gradually shift to China and the company’s partner there, SAIC. GM Korea saw its local sales fall 31% in May as demand collapsed for its Spark small car, leaving it in danger of losing its third place in the local market to Renault Samsung.
The manufacture of motorcycles in Japan has been sinking for years as companies localise production, particularly of smaller models. Production fell from a peak of 7.4m in 1981 to 560,536 last year. However, that 2016 figure was actually up 16% on the year before and Q1 this year was up 13% on the same period in 2016 at 188,073 units, according to figures from Japanese vehicle trade association, JAMA.
Three-quarters of the motorcycles built in Japan were exported in 2016, with half (just over 200,000) going to Europe, up 18% on the year before. In Q1 this year, exports were down 3.6%, with a 21% fall in North American exports offset by an 11% rise in Europe (Germany being the biggest market). The bulk of exported bikes are over 250cc in size.
The decline of Japanese sales, particularly of smaller bikes, is down to “chronic shortage of motorcycle parking bays in urban areas, higher vehicle prices stemming from mandatory compliance with new emissions regulations and shrinking model line-up”, according to JAMA.
Broadly speaking, Japanese part-makers supply the Japanese vehicle plants; these companies have also followed their customers overseas to supply their plants in Europe, North America and across Asia, writes Ian Henry. Domestically, however, there have been more cutbacks than investments in new Japanese facilities in recent years; in parallel, some mid-sized Japanese tier-ones have formed alliances with or been bought by foreign companies. One notable example has been the acquisition of lighting supplier Ichikoh by Valeo, which has helped the latter to strengthen its business globally with Nissan and Toyota especially. Ichikoh’s recent expansion into South-East Asia will help Valeo to widen its geographic footprint there as well.
However, the biggest development of recent months came in June, when safety-system supplier Takata filed for bankruptcy and said it would sell most of its assets and operations to Key Safety Systems, an American company owned by Ningbo Joyson Electronic Corporation of China. The leading global supplier of seatbelts, airbags and child seats was brought down by an airbag fault which led to fatalities and extensive vehicle recalls. Key Safety, which will pay 175 billion yen ($1.5 billion) for the business, pledged to keep Takata’s 46,000 workers and not to close any of its domestic manufacturing facilities. However, the Japanese company has 56 plants in 20 countries and it remains to be seen if any changes will happen there.
Other Japanese suppliers have been looking abroad for growth opportunities due to the slowdown in their domestic market. For example, JTEKT, one of the leading steering systems companies, has acquired a 51% stake in Indian company Sona. Some, such as Denso, have expanded overseas by establishing new factories. Denso opened a new plant in Thailand in mid-2016 and this is now being used as a base from which to spearhead expansion into Cambodia, where Denso has opened a satellite facility in the Phnom Penh Special Economic Zone. This factory will make oil coolers under the guidance of Denso’s Thai plant, which is also acting as the lead for new sites in Vietnam and Indonesia.
Korea to grow emerging technologySimilar trends are evident in Korea. For example, Valeo has established a 50:50 joint venture with the Pyeong Hwa group called Valeo-Kapec, which will produce torque converters for both automatic and continuously variable transmissions in three Korean factories, in Daegu, Waegwan and Seongju. Parts will be made for Samsung models, using Renault-Nissan platforms and Renault-developed components until now produced by Valeo in Europe.
While global tier-one suppliers look for JVs in Korea, some Korean companies are expanding outside the country. For example, new Hyundai Mobis plants are coming on stream in Mexico, the Czech Republic and China.
However, the major Korean suppliers are continuing to grow their domestic business, especially in new and emerging technology areas. In March 2017, Hyundai Mobis announced that it had started mass production of its first self-developed integrated body unit, comprising the body control module, smart key system, tyre pressure monitoring and parking assistance system. The company also opened its first vehicle proving ground at a cost of 300 billion won ($254.8m), which is seen as essential for moving into autonomous vehicle technology. Mando, too, has been endorsed by the Korean government to develop autonomous vehicles as the country seeks to build a strong presence in this growing sector; fostering competition between two leading suppliers is a tactic to achieve this aim.
Meanwhile, Hyundai-WIA, a transmissions and powertrain components supplier, has ended its joint venture in turbochargers with Japanese company IHI and will now develop and produce its own turbochargers, having become confident enough in its skills and capabilities to continue without an international partner.
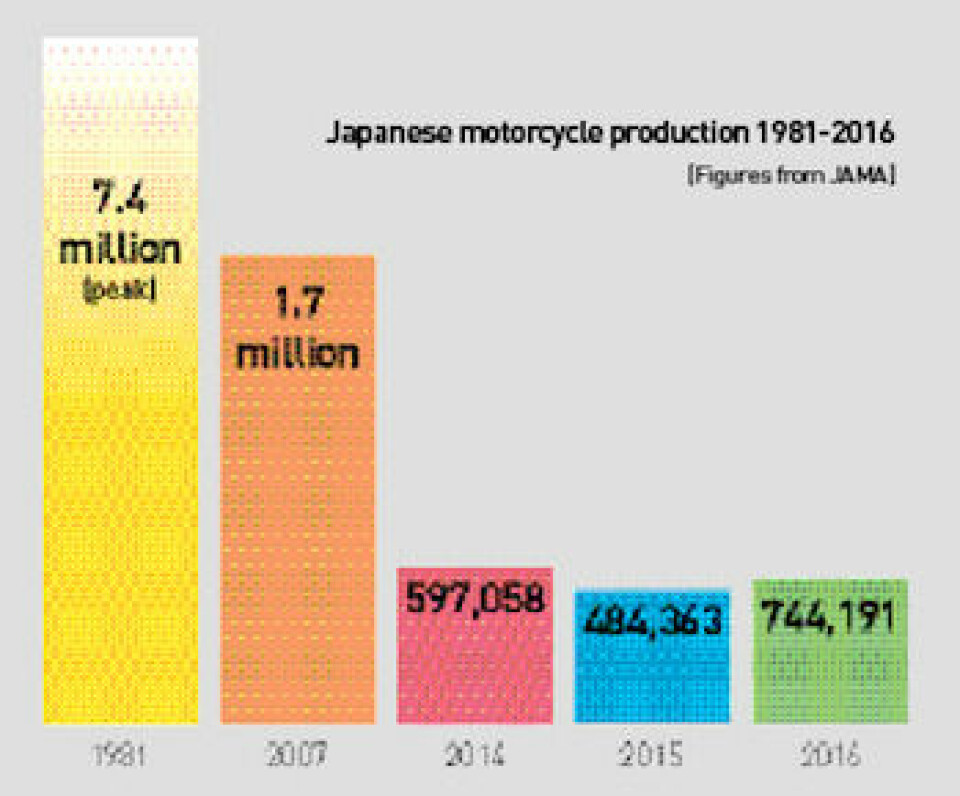
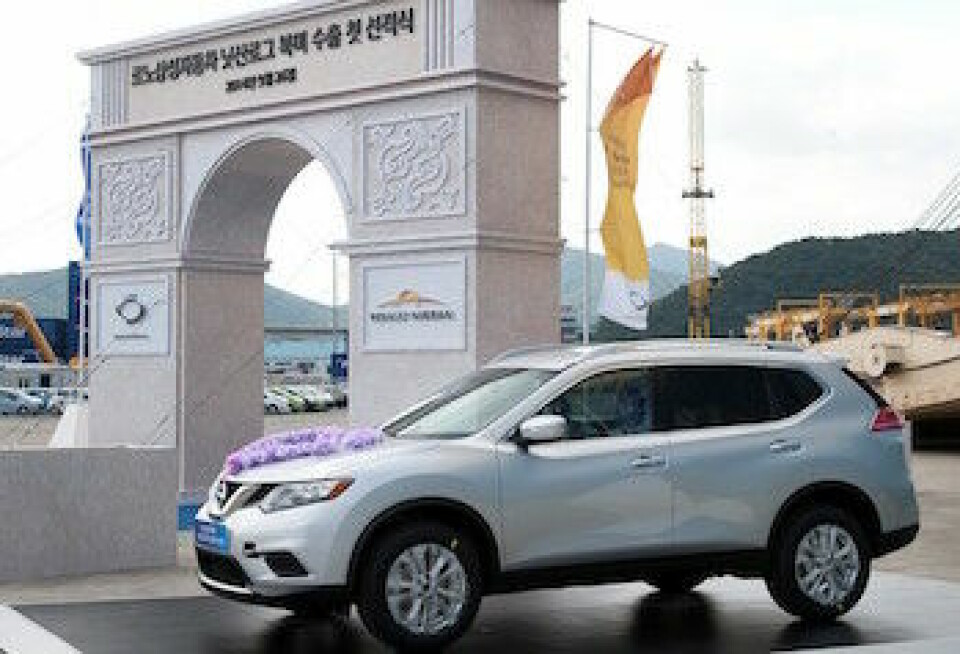